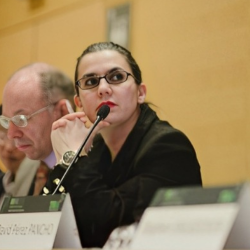
Dr Ahu Ece Hartavi Karci
About
Biography
Reader Hartavi Karci is in the Center of the Automotive Engineering. Her current research interests are connected to autonomous vehicle trajectory planners and controllers, advanced driver assistance systems, electric/hybrid electric vehicles technology, modeling, and control methodology, active magnetic bearings, and their applications.
With over 75 articles, 3 patents, and 3 book chapters, Reader Ahu Ece Hartavi Karcı has made significant contributions to the automotive industry through comprehensive publications and innovations. She has achieved world-class success in the field of electric vehicles and has won more than 8 prestigious awards, including the Mercedes Benz AMG Powertrain Award.
In recognition of her contributions to interdisciplinary sustainability research, Reader Ahu Ece has been awarded the title of Sustainability Fellow by the University of Surrey's Sustainability Institute.
Reader Ahu Ece Hartavi Karcı has been involved in more than 17 national and international EU projects, serving as a Scientific and Technical Coordinator, as well as a manager and advisory board member. She has played a key role in these projects, establishing partnerships with over 15 EU countries and taking her work to the international level.
Reader Ahu Ece Hartavi Karcı continues to hold the position of Head of the Centre for Automotive Engineering.
University roles and responsibilities
- Reader, Head of the Centre for Automotive Engineering
Previous roles
Affiliations and memberships
AWARDS
- The Institution of Mechanical Engineers Formula Student UK 2019 Global Winner Award (among 117 international teams.)
- The Mercedes-AMG HPP Best High Voltage Powertrain Implementation Number 1 Award in 2019.
- The Santander Most Improved Car Number 1 Award in 2019.
- Team Mekar Connected and Automated Vehicle, Fifth-place at Individual Performance in Grand Cooperative Driving Challenge that aims to accelerate Intelligent Transportation System Implementation in Europe, Netherlands, 2011.
- Team Mekar, Seventh-placed at Platoon Performance in Grand Cooperative Driving Challenge 2011, Netherlands, 2011.
- Technology Awards in Product Category for the Ford Transit Hybrid Vehicle Development Project-II, 2009.
- European Business Awards for the Environment in Turkey award for the Ford Transit Hybrid Vehicle Development Project-I, 2008.
- Winner of the ANOK Cup of the National Fuel-cell Race Car Competition, in 2007.
News
In the media
ResearchResearch interests
- Electric and hybrid vehicle technology, modeling, design, and control
- Connected autonomous vehicles
- Intelligent ground vehicles
- Software safety
- Electrical machines
- Active magnetic bearing systems and applications
Research projects
Scientific and Technical Coordinator & PI: 37 partners from 13 countries including 5 leading EU Truck Manufacturers 2nd biggest EU funding in the Destination. (1 January 2023-30 June 2026)(Total budget €19 000 000): An Horizon Europe project aims at advancing and demonstrating high-efficiency zero emission Heavy Duty Vehicle (HDV) powertrains for long-haul that will provide a range of 800 km without re-fueling/charging and cover at least 500 km average daily operation (6+ months) in real conditions. It is built on three 3 main areas, which are: i) Standardized well-designed, cost-effective modular and scalable multi-powertrain components; ii) Fast Fueling & Grid-friendly charging solutions; and iii) Digital Twin & AI-based management tools. The ultimate goal is to develop well-designed modular building blocks with a TRL7/8 based on business model innovations used for 3 types of zero HDVs {battery, fuel cell, range extender}. Dr. Hartavi is the Scientific and Technical Coordinator, and she built the consortium with the technical identification of content and successfully received the funding with the highest score among competitors (14/15).
PI & Technical Coordinator: 11 partners from 6 countries including 2 leading EU Automotive manufacturers(Completed Successfully )(1 June 2017-31 October 2020)(Total budget € 7 995 988,75): A Horizon 2020 project to develop:i)Systematic identification of critical road scenarios for the currently available Automated Driving (AD) systems;ii) Controllers and sensor fusion systems capable of dealing with complex, uncertain and variable road scenarios for enhanced road safety;iii) Development and demonstration of intuitive HMIs for the safe management of the transition between fully automated driving mode and human driving taking into account user acceptance and gender-specific aspects;iv) Development and demonstration of new tools for the cost- and time-effective assessment of vehicle and driver behaviour in mixed-traffic scenarios; v) Evaluation of Level3Automated functions (Grant agreement ID: 723324). Dr. Hartavi was the Technical Coordinator of the consortium and she led the efforts in establishing the consortium the consortium and successfully obtained the funding.
PI: 16 partners from 9 countries (1 June 2023 - 1 June 2026)(Total budget € 7 995 988,75): A Horizon Europe project aims to overcome the barriers regarding the assessment of the battery system's safety, performance, reliability, and lifetime by developing and validating a fast-track testing platform able to deliver a strategy based on Design of Experiments and robust testing results, combining multi-scale and multi-physics virtual and physical testing. This will enable an accelerated battery design that is more reliable, safer and long-lasting.
PI: 16 partners from 10 countries (Total budget € 7 995 988,75) (1 December 2019- 31 May 2023): A Horizon 2020 project aims to increase the safety of AD level transitions by 85 % compared to traditional, non-adaptive HMIs, and achieve acceptability of 95%. Field demonstrations will be performed using the full range from light to larger passenger vehicles and freight vehicles/trucks (L, M, and N class).Eventually, the HADRIAN demonstrators and effectiveness metrics will be translated into guidelines and recommendations for OEMs world-wide for human-systems integration of safe, acceptable and trustworthy AD technologies and functionalities.
PI: 15 partners from 9 countries, including 2 leading EU commercial vehicle manufacturers-van type(Completed Successfully )(January 2019- September 2022)(Total budget € 7 995 988,75): A Horizon 2020 project aims to develop components and systems for a range of commercial battery electric vehicles (cBEVs), and extensions to passenger vehicles and busses. Essential enabling elements in the project are EM for both in-wheel and e-axle systems, a novel suspension for in-wheel systems, time-sensitive networking, advanced controls, affordable and efficient processes, and scalability and transferability of innovations.
PI: 19 partners from 8 countries including 3 leading EU Automotive manufacturers (Completed Successfully )(1 October 2017-30 November 2020)(Total budget € 9 077 497,50): A H2020 European research project aims to develop a comprehensive framework for the design, development and testing of Advanced e-Powertrains and EV line-ups, to reduce development efforts by 40% while improving efficiency of the e-drivetrain by 20% and increase safety by a factor of 10 using advanced model-based testing methods and tools; as well as scalable and easy to parameterize real-time models. Dr. Hartavi also contributed to the consortium build up by introducing Ford to the consortium due to her strong relationship with the company.
CoPI: 8 partners from 7 counties (1 December 2020-30 November 2023)(Total budget € 7 995 988,75): A Horizon 2020 project aims to design a fleet of multi-passenger and multi-purpose commercial vans. With enhanced safety features, these vehicles are fitted with sensing, scanning, and night vision to enhance autonomous capabilities. They also feature a robust battery pack based on hybrid cells. The vans have an on-board charger and a standardized low-cost charging system. By advancing the development of such technology, the project is driving the market towards safe and affordable EVs.
CoPI: 13 partners from 8 countries including 2 leading EU commercial vehicle manufacturers (1 January 2023- December 2025)(Total budget € 7 995 988,75): A Horizon 2020 project aims the feasibility of a family of highly efficient power electronics components and systems, and including integrated traction inverters, on-board chargers, DC/DC converters, and electric drives for auxiliaries and actuators. The proposed solutions will be assessed on test rigs and on 2 differently sized BEVs.
CoPI: 11 partners from 7 countries including 2 leading EU commercial vehicle manufacturers (1 November 2022-31 October 2025)(Total budget € 7 995 988,75): A Horizon Europe project aims developing energy-efficient, cost-effective, modular, compact and integrated wide band gap (WBG) power electronics for next-generation battery electric vehicles. The project outputs will include: i) a scalable and modular family of WBG-based traction inverters with significantly improved specific cooling performance for 400 - 1200 V applications; ii) bi-directional OBC and DC/DC converters with the use of GaN; and iii) integrated, fault-tolerant and cost-effective GaN-based power electronics for HV ancillaries and chassis actuators.
CoPI: 10 partners from 5 countries (1 January 2023-31 December 2025)(Total budget € 7 995 988,75): A Horizon Europe project to develop novel solutions to push the boundaries of electric machine technology for automotive traction, through: i) innovative direct and active cooling designs; ii) virtual sensing functionalities for the high-fidelity real-time estimation of the operating condition of the machine; iii) enhanced machine control, bringing reduced design and operating conservativeness enabled by ii); iv) electric gearing to provide enhanced operational flexibility and energy efficiency; v) digital twin based optimisation, embedding systematic consideration of Life Cycle Analysis and Life Cycle Costing aspects since the early design stages; and vi) adoption of recycled permanent magnets and circularity solutions.
CoPI:10 partners from 7 countries (Completed successfully)(1 January 2019-30 June 2022)(Total budget € 9 077 497,50): A Horizon2020 project aims to develop new components for in-wheel powertrains: i) Efficient, scalable, reliable, low-cost and production-ready in-wheel motors suitable for a wide range of torque and power levels; and ii) Compact centralised drive for in-wheel motor axles, based on SiC technology, targeting superior levels of functional integration and failsafe operation – so called, eWD2. EVC1000 includes the demonstration of long-distance daily trips of up to 1000 km with no more than 90 min. additional travel time due to charging.
CoPI : 5 partners from 4 countries (Completed successfully) (1 December 2018-30 November 2021)(Total budget € 9 077 497,50): A Horizon 2020 project addresses the optimization and large-scale manufacturing of low and medium voltage electric powertrain solutions, with focus on high efficiency, compact packaging and low cost. 3 main applications are targeted: Small-to-medium segment electric cars; Hybrid electric cars with a low voltage add-on electric propulsion system; The lightweight urban mobility sector, e.g. electric quadricycles.The TELL powertrains will be demonstrated on two EV platforms.
CoPI: 21 partners from 7 countries (Completed successfully) (1 November 2017-28 February 2021)(Total budget € 9 484 981,06):A Horizon 2020 project with the primary idea of STEVE is to implement and test a human-centric approach to electro-Mobility-as-a-Service, according to the “Move2Me” vision of the consortium. To provide low-cost and financially sustainable EL V solutions and “gamified” services, to enhance users’ awareness, engagement and vehicle energy efficiency. A core item of STEVE is a low-cost electric quadricycle that integrates high-technology contents with respect to the current competitors, and will be pilot-tested, together with many other EL-Vs, during extensive demonstration phases in the 4 cities.
CoPI: 24 partners from 8 countries (Completed successfully)(1 April 2017-30 September 2020)(Total budget € 11 717 524,04):A Horizon 2020 project aims at increasing the number of HEVs up to 10% of all vehicles registered in the mid-term range. It was focused on a market segment called “premium class”, which covers medium, upper medium and luxury class vehicles up to SUVs. ADVICE aimed for a reduction of emissions on WLTP of 20% and a 25% increase in electric driving range for P-HEVs at a maximum cost of 5% for HEV (15% for P-HEV) with respect to the best-in-class non-hybrid diesel vehicles. (Grant agreement ID: 724095).
Between 2015 and 2018, Dr. Hartavi secured ~€ 1.235.115 from several other research collaborations, such as Marie-Curie and McLaren, among others. Prior to joining Surrey, she achieved €60M in funding with a consortium of partners, coordinated by Anadolu-Isuzu Bus Manufacturer.
9 partners from 7 countries (1 January 2020-31 December 2024 (Total budget 644 000,00): Grant agreement ID: 872907. Cars have four corners, the area where the wheels are mounted. A vehicle’s ride comfort and handling capabilities are mainly determined by its suspension system, which keeps the car’s wheels in contact with the road. The same applies to future self-driving cars. The EU-funded OWHEEL project will produce recommendations for improving ride dynamics and passenger comfort through innovative wheel-corner designs for automated vehicles. The project will draw on collaborative research and training between universities and industrial organisations from the EU, Japan, and South Africa. It will also include relevant networking, dissemination, and exploitation actions.
Research interests
- Electric and hybrid vehicle technology, modeling, design, and control
- Connected autonomous vehicles
- Intelligent ground vehicles
- Software safety
- Electrical machines
- Active magnetic bearing systems and applications
Research projects
Scientific and Technical Coordinator & PI: 37 partners from 13 countries including 5 leading EU Truck Manufacturers 2nd biggest EU funding in the Destination. (1 January 2023-30 June 2026)(Total budget €19 000 000): An Horizon Europe project aims at advancing and demonstrating high-efficiency zero emission Heavy Duty Vehicle (HDV) powertrains for long-haul that will provide a range of 800 km without re-fueling/charging and cover at least 500 km average daily operation (6+ months) in real conditions. It is built on three 3 main areas, which are: i) Standardized well-designed, cost-effective modular and scalable multi-powertrain components; ii) Fast Fueling & Grid-friendly charging solutions; and iii) Digital Twin & AI-based management tools. The ultimate goal is to develop well-designed modular building blocks with a TRL7/8 based on business model innovations used for 3 types of zero HDVs {battery, fuel cell, range extender}. Dr. Hartavi is the Scientific and Technical Coordinator, and she built the consortium with the technical identification of content and successfully received the funding with the highest score among competitors (14/15).
PI & Technical Coordinator: 11 partners from 6 countries including 2 leading EU Automotive manufacturers(Completed Successfully )(1 June 2017-31 October 2020)(Total budget € 7 995 988,75): A Horizon 2020 project to develop:i)Systematic identification of critical road scenarios for the currently available Automated Driving (AD) systems;ii) Controllers and sensor fusion systems capable of dealing with complex, uncertain and variable road scenarios for enhanced road safety;iii) Development and demonstration of intuitive HMIs for the safe management of the transition between fully automated driving mode and human driving taking into account user acceptance and gender-specific aspects;iv) Development and demonstration of new tools for the cost- and time-effective assessment of vehicle and driver behaviour in mixed-traffic scenarios; v) Evaluation of Level3Automated functions (Grant agreement ID: 723324). Dr. Hartavi was the Technical Coordinator of the consortium and she led the efforts in establishing the consortium the consortium and successfully obtained the funding.
PI: 16 partners from 9 countries (1 June 2023 - 1 June 2026)(Total budget € 7 995 988,75): A Horizon Europe project aims to overcome the barriers regarding the assessment of the battery system's safety, performance, reliability, and lifetime by developing and validating a fast-track testing platform able to deliver a strategy based on Design of Experiments and robust testing results, combining multi-scale and multi-physics virtual and physical testing. This will enable an accelerated battery design that is more reliable, safer and long-lasting.
PI: 16 partners from 10 countries (Total budget € 7 995 988,75) (1 December 2019- 31 May 2023): A Horizon 2020 project aims to increase the safety of AD level transitions by 85 % compared to traditional, non-adaptive HMIs, and achieve acceptability of 95%. Field demonstrations will be performed using the full range from light to larger passenger vehicles and freight vehicles/trucks (L, M, and N class).Eventually, the HADRIAN demonstrators and effectiveness metrics will be translated into guidelines and recommendations for OEMs world-wide for human-systems integration of safe, acceptable and trustworthy AD technologies and functionalities.
PI: 15 partners from 9 countries, including 2 leading EU commercial vehicle manufacturers-van type(Completed Successfully )(January 2019- September 2022)(Total budget € 7 995 988,75): A Horizon 2020 project aims to develop components and systems for a range of commercial battery electric vehicles (cBEVs), and extensions to passenger vehicles and busses. Essential enabling elements in the project are EM for both in-wheel and e-axle systems, a novel suspension for in-wheel systems, time-sensitive networking, advanced controls, affordable and efficient processes, and scalability and transferability of innovations.
PI: 19 partners from 8 countries including 3 leading EU Automotive manufacturers (Completed Successfully )(1 October 2017-30 November 2020)(Total budget € 9 077 497,50): A H2020 European research project aims to develop a comprehensive framework for the design, development and testing of Advanced e-Powertrains and EV line-ups, to reduce development efforts by 40% while improving efficiency of the e-drivetrain by 20% and increase safety by a factor of 10 using advanced model-based testing methods and tools; as well as scalable and easy to parameterize real-time models. Dr. Hartavi also contributed to the consortium build up by introducing Ford to the consortium due to her strong relationship with the company.
CoPI: 8 partners from 7 counties (1 December 2020-30 November 2023)(Total budget € 7 995 988,75): A Horizon 2020 project aims to design a fleet of multi-passenger and multi-purpose commercial vans. With enhanced safety features, these vehicles are fitted with sensing, scanning, and night vision to enhance autonomous capabilities. They also feature a robust battery pack based on hybrid cells. The vans have an on-board charger and a standardized low-cost charging system. By advancing the development of such technology, the project is driving the market towards safe and affordable EVs.
CoPI: 13 partners from 8 countries including 2 leading EU commercial vehicle manufacturers (1 January 2023- December 2025)(Total budget € 7 995 988,75): A Horizon 2020 project aims the feasibility of a family of highly efficient power electronics components and systems, and including integrated traction inverters, on-board chargers, DC/DC converters, and electric drives for auxiliaries and actuators. The proposed solutions will be assessed on test rigs and on 2 differently sized BEVs.
CoPI: 11 partners from 7 countries including 2 leading EU commercial vehicle manufacturers (1 November 2022-31 October 2025)(Total budget € 7 995 988,75): A Horizon Europe project aims developing energy-efficient, cost-effective, modular, compact and integrated wide band gap (WBG) power electronics for next-generation battery electric vehicles. The project outputs will include: i) a scalable and modular family of WBG-based traction inverters with significantly improved specific cooling performance for 400 - 1200 V applications; ii) bi-directional OBC and DC/DC converters with the use of GaN; and iii) integrated, fault-tolerant and cost-effective GaN-based power electronics for HV ancillaries and chassis actuators.
CoPI: 10 partners from 5 countries (1 January 2023-31 December 2025)(Total budget € 7 995 988,75): A Horizon Europe project to develop novel solutions to push the boundaries of electric machine technology for automotive traction, through: i) innovative direct and active cooling designs; ii) virtual sensing functionalities for the high-fidelity real-time estimation of the operating condition of the machine; iii) enhanced machine control, bringing reduced design and operating conservativeness enabled by ii); iv) electric gearing to provide enhanced operational flexibility and energy efficiency; v) digital twin based optimisation, embedding systematic consideration of Life Cycle Analysis and Life Cycle Costing aspects since the early design stages; and vi) adoption of recycled permanent magnets and circularity solutions.
CoPI:10 partners from 7 countries (Completed successfully)(1 January 2019-30 June 2022)(Total budget € 9 077 497,50): A Horizon2020 project aims to develop new components for in-wheel powertrains: i) Efficient, scalable, reliable, low-cost and production-ready in-wheel motors suitable for a wide range of torque and power levels; and ii) Compact centralised drive for in-wheel motor axles, based on SiC technology, targeting superior levels of functional integration and failsafe operation – so called, eWD2. EVC1000 includes the demonstration of long-distance daily trips of up to 1000 km with no more than 90 min. additional travel time due to charging.
CoPI : 5 partners from 4 countries (Completed successfully) (1 December 2018-30 November 2021)(Total budget € 9 077 497,50): A Horizon 2020 project addresses the optimization and large-scale manufacturing of low and medium voltage electric powertrain solutions, with focus on high efficiency, compact packaging and low cost. 3 main applications are targeted: Small-to-medium segment electric cars; Hybrid electric cars with a low voltage add-on electric propulsion system; The lightweight urban mobility sector, e.g. electric quadricycles.The TELL powertrains will be demonstrated on two EV platforms.
CoPI: 21 partners from 7 countries (Completed successfully) (1 November 2017-28 February 2021)(Total budget € 9 484 981,06):A Horizon 2020 project with the primary idea of STEVE is to implement and test a human-centric approach to electro-Mobility-as-a-Service, according to the “Move2Me” vision of the consortium. To provide low-cost and financially sustainable EL V solutions and “gamified” services, to enhance users’ awareness, engagement and vehicle energy efficiency. A core item of STEVE is a low-cost electric quadricycle that integrates high-technology contents with respect to the current competitors, and will be pilot-tested, together with many other EL-Vs, during extensive demonstration phases in the 4 cities.
CoPI: 24 partners from 8 countries (Completed successfully)(1 April 2017-30 September 2020)(Total budget € 11 717 524,04):A Horizon 2020 project aims at increasing the number of HEVs up to 10% of all vehicles registered in the mid-term range. It was focused on a market segment called “premium class”, which covers medium, upper medium and luxury class vehicles up to SUVs. ADVICE aimed for a reduction of emissions on WLTP of 20% and a 25% increase in electric driving range for P-HEVs at a maximum cost of 5% for HEV (15% for P-HEV) with respect to the best-in-class non-hybrid diesel vehicles. (Grant agreement ID: 724095).
Between 2015 and 2018, Dr. Hartavi secured ~€ 1.235.115 from several other research collaborations, such as Marie-Curie and McLaren, among others. Prior to joining Surrey, she achieved €60M in funding with a consortium of partners, coordinated by Anadolu-Isuzu Bus Manufacturer.
9 partners from 7 countries (1 January 2020-31 December 2024 (Total budget 644 000,00): Grant agreement ID: 872907. Cars have four corners, the area where the wheels are mounted. A vehicle’s ride comfort and handling capabilities are mainly determined by its suspension system, which keeps the car’s wheels in contact with the road. The same applies to future self-driving cars. The EU-funded OWHEEL project will produce recommendations for improving ride dynamics and passenger comfort through innovative wheel-corner designs for automated vehicles. The project will draw on collaborative research and training between universities and industrial organisations from the EU, Japan, and South Africa. It will also include relevant networking, dissemination, and exploitation actions.
Teaching
Teaching experience at the University of Surrey
During the 2.8 years spent at the University of Surrey more than 123 timetabled teaching hours/year have been devoted to teaching.
- Formula Student Electric (FSe) Project: Dr. Hartavi has been the coordinator of the FSe project since 2016. Dr. Hartavi shifted the project from an internal combustion engine race car into an electric race car to ensure that MES students are learning up-to-date content to gain foundational knowledge in the field of advanced vehicle engineering. With that transformation, the Formula Student Electric project also integrated well into the Automotive Engineering program. Under Dr. Hartavi’s supervision, the University has achieved its first entries to this competition, competing with a Class 1 electric vehicle in 2016, and in both classes (Class 1 and Class 2 Cars) in 2017. The team SURTES was one of the two teams that succeeded in passing the electrical scrutineering in 2017. Moreover, Dr. Hartavi has been the line manager of four Industrial Placement students relating to the FSe activity until now.
- Level M Multi-Disciplinary Design Project (ENG M001): Dr. Hartavi has renewed the content of the module with the Industrial Professor to extend the skills of the students into the areas such as mechatronics and computing. Dr. Hartavi has supervised 2 groups per academic year.
- Level 3 Group Design Project (ENG3162): Dr. Hartavi has contributed as supervisor of two design teams of the Formula Student Electric project which was formerly known as the Formula Student project.
- Level 1 Electronic Instrumentation 1 (ENG1068): Dr. Hartavi has been the module leader and the lecturer of the second part of the module since 2017. Dr. Hartavi has renewed the content of the module according to the education needs of today’s (tomorrow’s) MES students.
- Dr. Hartavi supervised / co-supervised 3 PhD students, 2 MSc students, and 14 MEng/BEng students, while supervising several visiting researchers from Turkey, India, and Italy since her last promotion.
Teaching experience at the Previous Universities
During the previous years, intensive courses were taught at the undergraduate and postgraduate levels.
- Brushless Servomotors and Their Applications, Science Eng. and Technology Institute (PhD), Power System Harmonics, Science Eng. and Technology Institute (PhD), Electrical Machines I & II, Electrical Engineering Department (BSc), Electronic Devices and Circuits, Electrical Engineering Department (BSc), Power Electronics, Electrical Engineering Department (BSc), Digital Design-I, Electrical Engineering Department (BSc), Fundamentals of Energy Conversion, Electrical Engineering Department (BSc), Fundamentals of Electrical Engineering, Electrical and Mechanical Engineering Department (BSc), and Physics II: Electromagnetic Field, Electrical Engineering Department (BSc)
Moreover, she built experimental rigs, prepared laboratory manuals, and supervised experiments for:
- Electrical Machines Laboratory-I & II Electrical Machines and Drives Department (BSc),
- Power Electronics Laboratory, Electrical Machines and Drives Department (BSc).
She was one of the main contributors to the development of the laboratories and the modules for the Electrical and
Electronics Engineering Degree, including design of modules and re-organization of the syllabus. She was also the
Faculty Advisor for the teams designing fuel cell and supercapacitor-powered electric race cars. Moreover, she was the
Faculty Erasmus Coordinator, and Internship Commission Member of the EEE department.
Sustainable development goals
My research interests are related to the following:
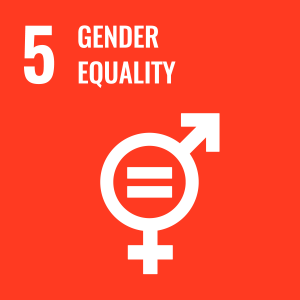
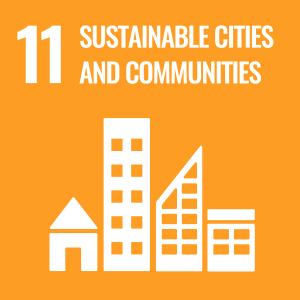
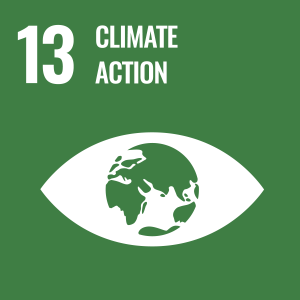
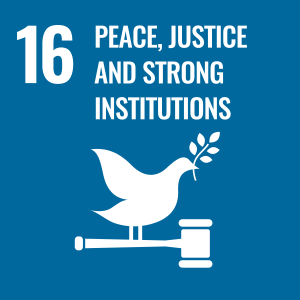
Publications
Research and Scholarly Activity
1) Bernardis M. D., Rini G., Bottiglione F., Hartavi A. E., Sorniotti A., On nonlinear model predictive direct yaw moment control for trailer sway mitigation, Vehicle System Dynamics, 61:2, 445-471, 2023.
2) Rini G., Bernardis M., D., Francesco Bottiglione, Hartavi A., E, Sorniotti A, On The Comparıson Of Centralızed And Multı-Layer Archıtectures For Nonlınear Model Predıctıve Torque-Vectorıng And Tractıon Control, International Journal of Automotive Technology, 2023.
3) Shao, L., Hartavi A.E., Tavernini D., Sorniotti A., Design and optimization of energy-efficient PM-assisted synchronous reluctance machines for electric vehicles. IET Electr. Power Appl. 1– 14, 2023.
4) Armengaud, E., Brandstätter, B., Biček, M., Buh, J., Hartavi A.E. et al., Towards Brand-Independent Architectures, Components and Systems for Next Generation Electrified Vehicles Optimised for the Infrastructure, SAE Int. J. Adv. & Curr. Prac. in Mobility 4(5):1906-1922, 2022.
5) Shah Alias Sangani, A., Harman, C., Kinav, E., Göl, M. Hartavi A.E., "Commercial Viability Assessment and Planning of Safety-Critical Embedded SW of Electrified Road Vehicles," SAE Int. J. Adv. & Curr. Prac. in Mobility 4(1):86-97, 2022.
6) K. M. So, P. Gruber, D. Tavernini, Hartavi A. E., A. Sorniotti and T. Motaln, On the Optimal Speed Profile for Electric Vehicles, in IEEE Access, vol. 8, pp. 78504-78518, 2020.
7) L. Shao, Hartavi A.E , D. Tavernini, A. Sorniotti and M. Cheng, Design Approaches and Control Strategies for Energy-Efficient Electric Machines for Electric Vehicles—A Review, IEEE Access, vol. 8, pp. 116900-116913, 2020.
8) Tavernini D., Vacca F., Metzler M., Savitsky D., Ivanov V., Hartavi A.E., Gruber P., Dhaens M., Sorniotti A.,An Explicit Nonlinear Model Predictive ABS Controller for Electro-Hydraulic Braking Systems, IEEE Transactions on Industrial Electronics, vol. 67, no. 5, pp. 3990-4001, May 2020.
9) Asef P., Bargallo R., A.E. Hartavi, Niknejad P., M.R. Barzegaran, Lapthorn A.C., Correlation of Solar Power Prediction Considering The Nominal Operating Cell Temperature Under Partial Shading Effect, Measurement, Volume 147, 2019.
10) Gao J., Tian G., Sorniotti A., Hartavi A.E., Di Palo R., Review of thermal management of catalytic converters to decrease engine emissions during cold start and warm up, Applied Thermal Engineering, Vol 147, pp 177-187, 2019.
11) Vacca, F., De Pinto, S., Hartavi Karci, A.E., Gruber, P., Viotto, F., Cavallino, C., Rossi, J.; Sorniotti, A. On the Energy Efficiency of Dual Clutch Transmissions and Automated Manual Transmissions, Energies, 10, 1562, 2017.
12) Ahu Ece Hartavi, İsmail Meriç Can Uygan and Levent Güvenç, A Hybrid Electric Vehicle Hardware-in-the-Loop Simulator as a Development Platform For Energy Management Algorithms, International Journal of Vehicle Design Vol. 71, No. 1-4, pp 410-429.2016.
13) Kahraman K., Hartavi A. E., Guvenc L., et al. Cooperative Adaptive Cruise Control Implementation of Team Mekar at the Grand Cooperative Driving Challenge, IEEE Transactions on Intelligent Transportation Systems, Vol:13, 3, 2012.
14) Uygan I. M.C, Hartavi A.E., Guvenc L., Sezer V., Acarman T, Propulsion System Design of a Hybrid Electric Vehicle, International Journal of Vehicle Design Vol. 52, No. 1-4, 2009.
15) Uygan I. M. C, Hartavi A. E., Guvenc L., Sezer V., Acarman T., Propulsion System Design of a Hybrid Electric Vehicle, International Journal of Vehicle DesignVol. 52, No. 1-4, 2009.
16) M. N. Sahinkaya and A. E. Hartavi, Variable Bias Current in Magnetic Bearings for Energy Optimization, IEEE Transactions on Magnetics, vol. 43, no. 3, pp. 1052-1060, March 2007.
17) Hartavi, A.E., Tuncay N. R., Sahinkaya M.N., Burrows C.R., Rotor-AMY Sisteminin Bulanık Denetleyici ile Kontrolü ve Denge Akımı En İyileştirilmesi, ITU, Vol 5, 3, 2006.
18) Hartavi A.E., Sahinkaya M. N, Tunçay R. N., Burrows C.R., Fuzzy Supervisory Control and Bias Current Optimization of Rotor Active Magnetic Bearing System, Journal of ITU , 2006.
19) Ozgurs Ustun, R. Nejat Tuncay, A. Kerem Dogueri, A. Ece Hartavi, An Integrated Approach for Linear Actuator Design, IFAC Proceedings Volumes, Volume 35, Issue 2, 2002, pp 37-42,2002.
Book Chapters
1) Hillbrand, B. , Innerwinkler P., Stettinger G., Hartavi, A.E., Rodoplu K., Demir A., Buyukakin T.,Sozen E., Aydemir E., Clement P., Zaya J., Sahimäki S., Tarkiainen M.,TrustVehicle Verification Procedure, Enhanced Trustworthiness and End User Acceptance of Conditionally Automated Vehicles in the Transition Period. Springer, 2021.
2) Hartavi, A.E., Kabbani T., Sarhadi P., Sangani A.S.A.,Zaya J., Maroun S., Saleh M., Shanmugam S.,Krishna A., Ou J., Sozen E., Aydemir E, Ahiad S., Reliable Sense-Plan-Act Approaches for TrustVehicles, Enhanced Trustworthiness and End User Acceptance of Conditionally Automated Vehicles in the Transition Period, Springer, 2021.
3) Schicker, L.M., Watzenig, D., Hartavi, A.E., Troglia, M., How Should TrustVehicles Behave? Trustworthiness, User Acceptance and Expectations. Enhanced Trustworthiness and End User Acceptance of Conditionally Automated Vehicles in the Transition Period. Springer, 2021.
4) Clement, P., Danzinger, H., Quinz, P., Hillbrand, B., Hartavi, A.E., Kasikci, K.Z., Assessment Concept for TrustVehicles, Trustworthiness and End User Acceptance of Conditionally Automated Vehicles in the Transition Period. Enhanced Trustworthiness and End User Acceptance of Conditionally Automated Vehicles in the Transition Period, Springer, 2021.
5) Innerwinkler P, Hartavi A.E.,Tarkiainen M.J., Troglia M., Kinav E., Ozan B., Aydemir E., Derse C., Stettinger G., Watzenig D., Sahimäki S., Druml N.,Nahler C., Metzner S., Gopi S., Clement P., Macher G., Zaya J.,Groppo R., Ahiad S., TrustVehicle – Improved Trustworthiness and Weather-Independence of Conditionally Automated Vehicles in Mixed Traffic Scenarios: Smart Systems for Clean, Safe and Shared Road Vehicles, Advanced Microsystems for Automotive Applications 2018.
6) Hartavi, A., Uygan I.M.C, Sezer, V., Güvenç, L., Acarman T.,Kilic V., Yildirim M., Electric Regenerative Power Assisted Brake Algorithm for a Front and Rear Wheel Drive Parallel Hybrid Electric Commercial Van, Advancements in Steering Systems, Braking Systems, and Advanced Chassis Control and Rollover Stability, Chapter 7, SAE International, ISBN: 978-0-7680-2092-2, October 2009.
7) Sezer, V., Uygan, I.M.C., Acarman T., Kilic V., Yildirim M., Hartavi, A., Güvenç, L., Chapter 7: Maximizing Overall Efficiency Strategy (MOES) for Power Split Control of a Parallel Hybrid Electric Vehicle, Simulation of Commercial Vehicles, Chapter 7, SAE International, ISBN: 978-0-7680-2094-6, October 2008.
White Papers
8) Hartavi A.E., Sangani A.S.A., Trustvehicle Catalogue of Critical Scenarios, Trustvehicle, Grant agreement ID: 723324, 2020.
9) Hartavi A.E., Alkan E., Sangani A.S.A., Catalogue of Assessment Criteria for Level 3 Autonomous Vehicles, Trustvehicle, Grant agreement ID: 723324, 2020.
Conference Papers
10) Gol M., Camci M.,Serbes D., Santuci E., Mörtl P., Ozan B., Hartavi A. E., Empowering SAE Level 4 Autonomous Trucks: The Decision-Making System, International Congress on Transportatıon Research, ICTR, Heraklion, Crete, 2023.
11) Kim. S, D.Serbes, T.Kabbani, Hartavi A.E. R. Egmond, Designing sounds to support visual Human Machine Interface for automated vehicles: A study for truck drivers, The Human Factors and Ergonomics Conference-Europe, Torino, Italy, 2022.
12) Mohamed Y., Gol M., Kabbani T., Ghazali M., Demir A., Sangani, Rodoplu K., Derse C., Hartavi A. E., Real-Time Implementable Intelligent Trajectory Controller Design for a Light Commercial Vehicle, Transport Research Arena Conference Lisbon, Portugal, 2022.
13) Kabbani T., Sarhadi P., Ghazali M., Gamagea C., Serbes D, Sozen E., Ozan B., Hartavi A. E., Model Validation of Articulated Heavy-Duty Vehicle via IPG for Tracking Controller Design, Transport Research Arena. Lisbon 2022.
14) Ghazali M., Gupta I., Ben Abdallah M., Clarke J., Hartavi A. E., Performance Comparison of Three Rival AI-Powered Intelligent Trajectory Tracking Controllers for an Autonomous Delivery Van, Accepted for Transport Research Arena. Lisbon 2022.
15) Ghazali M., Chaghazardi Z., Daryabari S, Harman C., Vukotic M, Miljavec D, Hartavi A,E., Quantitative Analysis of the Effect of Operating Temperature on Energy Performance of an Electric Heavy Commercial Vehicle, Transport Research Arena. Lisbon 2022.
17) A. Kanak, S. Ergün, A. Serdar Atalay, S. Persi and A. E. Hartavi, A Review and Strategic Approach for the Transition towards Third-Wave Trustworthy and Explainable AI in Connected, Cooperative and Automated Mobility, 27th Asia Pacific Conference on Communications, Jeju Island, Korea, Republic of, 2022.
18) Kim, S., Kabbani, T., Serbes, D., Happee, R., Hartavi, A.E, & van Egmond, R., A new approach to sound design in automated vehicles. In Proceedings of the Human Factors and Ergonomics Society Europe, pp. 149-159, 2022.
19) İnal T. T., Yalçın B., Çetin G., Abdallah M. B., Ghazali M., Cansever G., Hartavi A.E., Energy Benefit Analysis of Independent Torque Variation in Fully Electric Off-Road Tracked Vehicles, 10th International Automotive Technologies Congress, OTEKON 2020.
20) Hartavi, A.E., Gol M., Electrified Auxiliary System Demand Control Of A Hybrid Electric Refuse Truck, 10th International Automotive Technologies Congress, OTEKON, 2020.
21) Kabbani T, Sarhadi P., Sozen E., Ozan B, Kinav E., Hartavi A.E., Fully Automated Reverse-Parking System for a Level 3 Autonomous Heavy-Duty Vehicle, Virtual ITS European Congress, 9-10 November 2020.
22) Kaşıkcı K., Hartavi A. E.,Sorniotti A., Evaluatıon Of Automatıon Inıtıated Drıvıng Control Authorıty Transıtıon Tıme In Level 3 Automated Vehıcles, OTEKON’18, 2018.
23) Giannakou P., Hartavi A. E., Energy Harvesting Estimation of a Piezoelectric-Charging Structural Supercapacitor, Hybrid and Fuel Cell Electric Vehicle Congress, 2017.
24) Hartavi A.E, Akyuz B., Gol M., A Comparative Study of Different Electric Drive Systems and Their Effects on Drive Cycle Performance of an Electric City Bus, EVS’28, 2015.
25) Gol M., Inal T., Hartavi, A.E., An Effective Tool for Evaluating the Impact of E-Powertrain on Energy Consumption and Performance, OTEKON’14, 2014.
26) Uygan I. M. C, Hartavi A. E., Yildirim M., Guvenc L.,Development and Use of Hybrid Electric Vehicle Hardware-in-The-Loop Simulator for Power Management Controller Design and Testing, OTEKON’14, 2014.
27) Gol M., Hartavi, A.E., Akyuz B., Impact Assessment of Electric City Bus Parameters on Driving Range over Various Drive Cycles, International Conference on Automotive Technologies, ICAT, 2014.
28) Karabastık E., Akgün E., Savtur M., Hartavi A. E., Gelişen Teknoloji ve Karayolu Güvenliği, 4. Karayolu Trafik Güvenliği Sempozyumu ve Sergisi, Ankara, Turkey, May 8-10, 2013.
29) Gol M., Abdal S., Ceylan H., Hartavi A. E., Asfalttaki Zekâ, 4. Karayolu Trafik Güvenliği Sempozyumu ve Sergisi, May 8-10, 2013, Ankara, Turkey, 2013.
30) Demir M., Gezer I., Tarı O., Hartavi A. E., Karayolu Güvenliği Politikaları ve Stratejileri: Türkiye ve AB Karşılaştırması, 4. Karayolu Trafik Güvenliği Sempozyumu, May 8-10, Ankara, Turkey, 2013.
31) Boltürk S. T., Yıldırım G. Ö., Balata A., Hartavi A. E., İleri Sürücü Destek Sistemleri, 4. Karayolu Trafik Güvenliği Sempozyumu ve Sergisi, May 8-10, Ankara, Turkey, 2013
32) Hartavi A.E., Uygan I.M.C., Turan M. C., Karaahmetoğlu R., Senturk M., Tas O. S., Kahraman K., Güvenc L, Guvenc B.A, Ozguner U., Altug E., Efendioglu B., Design and Control Basics of a Cooperative Vehicle, Otomotiv Teknolojileri Kongresi (OTEKON’12), June 4-5, Bursa, Turkey, 2012.
33) Turan M. C., Hartavi A.E., Altug E., Development of Rule Based Upper Level Control Algorithm for an Intelligent Vehicle in Automated Highway System, 2012 IEEE International Conference on Vehicular Electronics and Safety (ICVES’12), Istanbul, Turkey. July 24-27, 2012,
34) Hartavi A.E., Turan M. C., Gol M., Tarı O., Pre-Competition Determination of Performance Effective Parameters for a Fuel Cell Electric Race Vehicle, International Workshop on Challanges and Opportunities for Green and Smart Vehicles, July 24, 2012.
35) M. C. Turan, A. E. Hartavi and E. Altuğ, Development of a Rule Based Upper Level Control Algorithm For a Co-Operative Vehicle in Automated Highway System, IEEE International Conference on Vehicular Electronics and Safety, ICVES, 2012.
36) Hartavi A.E., Uygan I.M.C., Güvenc L, Bypass Based Rapid Control Prototyping of Hybrid Brake Control System, Otomotiv Teknolojileri Kongresi (OTEKON’10), June 7-8, Bursa, Turkey, 2010.
37) Altındemir E., Hartavi A.E., Güvenc L, Göktan A., Yıldırım M., Development of an Auxiliary Pressurized Hybrid Brake System for a Parallel Hybrid Electric Commercial Van, SAE ,Commercial Vehicle Engineering Congress and Exhibition (SAE COMVEC 2009), Rosemont, Illinois, USA, 2009.
38) Sezer V., Biliroğlu A., Demirci M., Uçarol H., Kural E., Özsu E., Kilic V., Koçkan I., Yildirim M., Hartavi A.E., Uyagn I.M.C., Acarman T., Guvenc L., Design and Implementation of a Series-Parallel Light Commercial Hybrid Electric Vehicle,EVS24, 2009.
39) Uygan I.M.C., Hartavi A.E., Güvenc L, Powertrain Design for Hybrid Electric Vehicles, 4. Otomotiv Teknolojileri Kongresi (OTEKON’08), Bursa, Turkey, June 1-4, 2008.
40) Hartavi, A., Uygan I.M.C, Sezer, V., Güvenç, L., Acarman T.,Kilic V., Yildirim M., Electric Regenerative Power Assisted Brake Algorithm for a Front and Rear Wheel Drive Parallel Hybrid Electric Commercial Van, SAE Technical Paper 2008-01-2606, 2008.
41) Sezer, V., Uygan, I.M.C.,Acarman T.,Kilic V.,Yildirim M., Hartavi, A., Güvenç, L., Maximizing Overall Efficiency Strategy (MOES) for Power Split Control of a Parallel Hybrid Electric Vehicle, SAE Technical Paper 2008-01-2682, 2008.
42) Hartavi A.E., Uygan I.M.C., Sezer V., Acarman T. , Güvenc L, Goktan A.G., Development of an Electric Power Assisted Brake Algorithm for Electrically Driven Land Vehicles, 9th International Symposium on Advanced Vehicle Control, (AVEC’08), October 6-9, Japan, 2008.
43) Uygan I.M.C., Hartavi A.E., Güvenc L., Acarman T., Kılıç V., Özelgin İ., Yildirim M., Sezer V., FOHEV II - The Ford Otosan Hybrid Electric Research Prototype Vehicle, International Conference on Automotive Technologies, (ICAT’08) , November 13-14, 2008, Turkey.
44) Uygan I. M. C, Sezer V., Guvenc L, Goktan A.,Acarman T., Hartavi A. E., Kılıç V., Yildirim M., Electronic and Safety Structural Design of a Hybrid Electric Vehicle, Electronic and Safety Structural Design of a Hybrid Electric Vehicle, ICVES08, Columbus, USA, 2008.
45) Uygan I. M. C, Hartavi A. E., Sezer V., Guvenc L, Goktan A., Energy Recuperation in Electrically Driven Road Vehicles through Regenerative Braking, AVEC08, Kobe, Japan, 2008.
46) Uygan I. M. C, Hartavi A. E., Sezer V., Guvenc L, Acarman T., Kiliç V, Yildirim M., Regenerative Braking Algorithm for Energy Efficiency Enhancement of a Front and Rear Wheel Drive Parallel Hybrid Electric Commercial Van, COMVEC08, 2008.
47) Hartavi A.E. Uygan I.M.C., Sezer V., Acarman T. , Güvenc L., Kiliç V, Yildirim M., Signal interfacing for hybrid electric vehicular electronics and an implementation study, IEEE International Conference on Vehicular Electronics and Safety, Columbus, OH, USA, pp. 151-156, 2008.
48) Hartavi A.E., Uygan I.M.C., Sezer V., Acarman T. , Güvenc L., Development of Hybrid Braking Algorithm for Electric/Hybrid Electric Vehicles, The 3rd AUTOCOM International Workshop on Hybrid Electric Vehicle Modeling and Control, June 12, 2007.
49) Hartavi A.E. , Sahinkaya M. N, Tunçay R. N., Variable Current Control of A Five Axis Magnetically Levitated Turbomolecular Pump, International Conference on Electric Machines and Drives, (ICEM'06 ), Chania, Greece, September 2-5, 2006.
50) Hartavi A.E., R. N. Tuncay and M. N. Sahinkaya, The Effect of Current Control Strategies on Power Consumption of a Magnetically Levitated Turbomolecular Pump, CES/IEEE 5th International Power Electronics and Motion Control Conference, Shanghai, China, pp. 1-5, 2006.
51) Hartavi A.E., R. N. Tuncay and M. N. Sahinkaya, Burrow C. R., Bias Current Optimisation and Fuzzy Controllers for Magnetic Bearings in Turbo Molecular Pumps, Ninth International Symposium on Magnetic Bearings, August 3-6, 2004, Lexington, Kentucky, USA, 2004.
52) Hartavi A.E., O. Ustun and R. N. Tuncay, A comparative approach on PD and fuzzy control of AMB using RCP, IEEE International Electric Machines and Drives Conference, IEMDC'03., Madison, WI, USA, 2003, pp. 1507-1510 vol.3, 2003.
53) Üstün Ö,. Tunçay R.N. , Dogueri A.K. , Hartavi A.E., An Integrated Approach To Design of Linear Actuators, Mechatronics 2002 Conference, 9-11, Berkeley, USA, December 2002.
54) Hartavi A.E., O. Ustun, R. N. Tuncay and F. Gurleyen, The design, simulation and experimental study of active magnetic bearing, IEMDC 2001. IEEE International Electric Machines and Drives Conference, Cambridge, MA, USA, pp. 492-495, 2001.
55) Hartavi A.E., Üstün Ö., Tunçay R.N., Modelling and Control Aspects of Active Magnetic Bearing, European Conference on Power Electronics and Applications (EPE’01), Graz, Austria, 27-29 August 2001.
56) Hartavi A.E., Üstün Ö., Tunçay R.N., Dynamic Simulation of Attractive Type Suspension Systems, International Aegean Conference of Electrical Machines and Power Electronics (ACEMP’01), Kuşadası, Turkey, 26-29 June 2001.
57) Hartavi A.E., Üstün Ö., Tunçay R.N., Gürleyen F., The Design Simulation and Experimental Study of an Active Magnetic Bearing, International Electric Machines and Drives Conference (IEMDC'01), Cambridge, USA, 2001.
58) Hartavi A.E., Ö. Üstün, R.N.Tunçay, Design and Simulation of DC type Active Magnetic Bearing System, Elektrik, Elektronik ve Bilgisayar Mühendisliği Sempozyumu (ELECO 2000), Bursa, Turkey ( in Turkish), 2000.