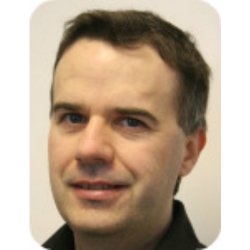
Dr Christopher Turner
About
Biography
Dr Turner is research active in the fields of business analytics, digital manufacturing, circular economy, industry 4.0 and human centric industry 5.0 automation solutions. Dr Turner is also a fellow of the cross-University People-centred AI Institute with his research focussing on Industry 5.0 Human Centred Manufacturing. Dr Turner has published over 100 papers (including 59 journal papers) in peer reviewed international journals and conferences and has received over 5600 citations (as recorded by Google Scholar) with a H index of 30 (i10: 54). With his involvement in the successful completion of several UK research council funded projects (with subjects ranging from business process optimisation to the simulation of product-service systems), Dr Turner is experienced in the management of commercially focused applied projects. He has been engaged in the AUTONOM project (Integrated through-life support for high-value systems) working with industry partners, such as Network Rail, in the area of automated intelligent maintenance systems. He has also been involved in a Knowledge Transfer Project (KTP) with the company Basemap. This KTP had the aim of developing a holistic logistics management routing software tool combining scheduling and routing with critical vehicle and environmental performance factors relevant to the electric commercial vehicle market. He is also a member of the IEEE task force on process mining.
Areas of specialism
Previous roles
ResearchResearch interests
Dr Turner is research active in the following areas:-
- Business Analytics
- Data Mining
- Machine Learning
- Digital Manufacturing
- Discrete Event Simulation
- Virtual and Mixed Reality for Data Visualisation
- Distributed and Sustainable Manufacturing
- Industry 4.0 & 5.0
-
Research interests
Dr Turner is research active in the following areas:-
- Business Analytics
- Data Mining
- Machine Learning
- Digital Manufacturing
- Discrete Event Simulation
- Virtual and Mixed Reality for Data Visualisation
- Distributed and Sustainable Manufacturing
- Industry 4.0 & 5.0
Teaching
I lecture on the MSc module Operations Management and Digital Services, part of the Operations and Supply Chain in the Digital Era and Entrepreneurship MSc programmes.
Publications
The e-waste management market is a major business opportunity with a projection to grow to USD 137.60 bn by 2029 being a key motivator to undertake research in this area. A formal, methodical, organised sector is essential to ensure the best possible collection of e-waste as well as its proper disposal or recycling. While the UN SDG Goal No. 12 aims for responsible production and consumption, businesses are still looking into ways to guarantee that e-waste collection, recycling, or disposal is not an expensive endeavour. This implies that a variety of activities throughout the supply chain would be involved, not only in the collection, disposal, and recycling of e-waste, but also in the establishment of a system for its management. This paper builds on the novel Present-Unique-Repeatable-Environmentally-friendly (PURE) framework underlying the introduction of makerspaces and Centre for Refurbishment and Recycling of Electrical and Electronic Waste (CReW) & addresses quantitatively how the network flow should be to achieve sustainable development goals of minimising cost and emissions. Also generates employment opportunities while tackling health concerns for those residing within the proximity of landfills. Therefore it ensures a leaner process that can be adopted horizontally across industries while also coining electronic reverse logistics into e-waste’s forward logistics as a formal supply chain design
The rapid advancement of Large Language Models (LLMs) has resulted in interest in their potential applications within manufacturing systems, particularly in the context of Industry 5.0. However, determining when to implement LLMs versus other Natural Language Processing (NLP) techniques, ontologies or knowledge graphs, remains an open question. This paper offers decision-making guidance for selecting the most suitable technique in various industrial contexts, emphasizing human–robot collaboration and resilience in manufacturing. We examine the origins and unique strengths of LLMs, ontologies, and knowledge graphs, assessing their effectiveness across different industrial scenarios based on the number of domains or disciplines required to bring a product from design to manufacture. Through this comparative framework, we explore specific use cases where LLMs could enhance robotics for human–robot collaboration, while underscoring the continued relevance of ontologies and knowledge graphs in low-dependency or resource-constrained sectors. Additionally, we address the practical challenges of deploying these technologies, such as computational cost and interpretability, providing a roadmap for manufacturers to navigate the evolving landscape of Language based AI tools in Industry 5.0. Our findings offer a foundation for informed decision-making, helping industry professionals optimize the use of Language Based models for sustainable, resilient, and human-centric manufacturing. We also propose a Large Knowledge Language Model architecture that offers the potential for transparency and configuration based on complexity of task and computing resources available. •We explore various Natural Language technologies to enhance human–robot interaction.•We explore Language Models, Ontologies and Knowledge Graphs for various sectors.•Various manufacturing sectors have different levels of dependency on other sectors.•Sectors with high dependency have the most to benefit from Large Language Models.•We provide a framework on when and which technology to choose for various contexts. [Display omitted]
Human-robot collaboration (HRC) is at the heart of intelligent automation and is essential for increasing efficiencies in industrial systems by combining the strength, dexterity and precision of robots with the intelligence and adaptation skills of humans. HRC is enabled by Human-Robot Interaction (HRI) in which humans and robots co-work on a task communicating and physically interacting with each other. However, the principles of HRI are neither well understood nor well established and detailed investigation is difficult because real-life experimentation involving human and industrial robot interactions carry the risk of detrimental encounters. This paper presents an opportunity to investigate and assess human-robot interactions for collaboration efficacy and safety within a realistic Virtual Reality (VR) environment A simple maintenance activity involving the assembly of two blocks was designed with two scenarios: manual assembly; robot assisted assembly.
The field of Explainable Artificial Intelligence (XAI) is a relatively new approach to AI, with the aim to provide black box algorithms with human intelligible narrative functionality. It is most often in end-of-life considerations of the asset lifecycle that sustainability issues are encountered. Modern maintenance practice requires a holistic understanding of lifecycle and options for sustainable asset treatments. human in the loop solutions offer a way to leverage both machine and human skill sets to provide the next level of automaton solutions for industrial maintenance activities. This paper presents a framework for human in the loop Intelligent and Sustainable Maintenance. In bridging the gap between machines and humans XAI leverages the best of both worlds to provide a new level of agility to cyber assisted maintenance activities and full lifecycle consideration of assets; a notion that is necessary throughout the organization in the achievement of sustainability goals set by governments around the world in the achievement of a net zero carbon emission economy.
This paper demonstrates a design and evaluation approach for delivering real world efficacy of an explainable artificial intelligence (XAI) model. The first of its kind, it leverages three distinct but complimentary frameworks to support a user-centric and context-sensitive, post-hoc explanation for fraud detection. Using the principles of scenario-based design, it amalgamates two independent real-world sources to establish a realistic card fraud prediction scenario. The SAGE (Settings, Audience, Goals and Ethics) framework is then used to identify key context-sensitive criteria for model selection and refinement. The application of SAGE reveals gaps in the current XAI model design and provides opportunities for further model development. The paper then employs a functionally-grounded evaluation method to assess its effectiveness. The resulting explanation represents real-world requirements more accurately than established models.
As we progress towards Industry 5.0, technological advancements are converging; this movement is realised by the increasing collaboration between humans and intelligent digital platforms and further enabled by the interactive visualisation modes provided by Metaverse technology. This research examines the practical applications and limitations of Metaverse technology providing insights into the transformative possibilities it offers for the manufacturing sector. Specifically, the research was guided by the core objective to trace the evolution of Metaverse technology within manufacturing. This study provides a comprehensive and state-of-the-art analysis of the adoption and impact of Metaverse technologies in the manufacturing sector. While previous research has explored aspects of Industry 4.0 and digital transformation, this study specifically focuses on human-centric manufacturing (human-in-the-loop) applications of Metaverse technology, including augmented reality, virtual reality, digital twins, and cyber-physical robotic systems. Findings from the systematic literature review indicate that Metaverse technologies, primarily augmented reality and virtual reality, have evolved into powerful tools in manufacturing. They are widely adopted across sectors in the industry, transforming processes such as product design, quality control, and maintenance. Augmented reality and virtual reality offer intuitive ways to visualise data and interact with digital twins, bridging the gap between physical and virtual realms in manufacturing. A roadmap and scenarios for the introduction of Metaverse technology in manufacturing are provided with suggested adoption timespans. Furthermore, the systematic literature review identified barriers hindering the wider adoption of Metaverse technology in manufacturing.
Brexit has been a game-changer for Britain, and its key partners. Strategic shifts as well as historic relations have impacted the UK’s relationship with France in a number of unexpected ways. This article explores some of the key historical events that have caused both agreement and strife between the two states, looking at the bilateral treaties established to deepen cooperation on security and defence, specifically the Lancaster House agreements, and considers the series of intriguing accords and conventions that have arisen from the mid-1980s, as well as the logistical challenges of the shared border and juxtaposed border controls of Britain and France. Post-Brexit diplomatic forums in which Britain and France are joined by Germany are then explored, before assessing Britain’s attempts to forge its new role in relation to long-standing commitments to France and an evolving relationship with the EU.
While the move towards Industry 4.0 has motivated a re-evaluation of how a manufacturing organization should operate in light of the availability of a new generation of digital production equipment, the new emphasis is on human worker inclusion to provide decision making activities or physical actions (at decision nodes) within an otherwise automated process flow; termed by some authors as Industry 5.0 and seen as related to the earlier Japanese Society 5.0 concept (seeking to address wider social and environmental problems with the latest developments in digital system, artificial Intelligence and automation solutions). As motivated by the EU the Industry 5.0 paradigm can be seen as a movement to address infrastructural resilience, employee and environmental concerns in industrial settings. This is coupled with a greater awareness of environmental issues, especially those related to Carbon output at production and throughout manufactured products lifecycle. This paper proposes the concept of dynamic Life Cycle Assessment (LCA), enabled by the functionality possible with intelligent products. A particular focus of this paper is that of human in the loop assisted decision making for end-of-life disassembly of products and the role intelligent products can perform in achieving sustainable reuse of components and materials. It is concluded by this research that intelligent products must provide auditable data to support the achievement of net zero carbon and circular economy goals. The role of the human in moving towards net zero production, through the increased understanding and arbitration powers over information and decisions, is paramount; this opportunity is further enabled through the use of intelligent products.
New trends in Knowledge-Based Engineering (KBE) highlight the need for decoupling the automation aspect from the knowledge management side of KBE. In this direction, some authors argue that KBE is capable of effectively capturing, retaining and reusing engineering knowledge. However, there are some limitations associated with some aspects of KBE that present a barrier to deliver the knowledge sourcing process requested by industry. To overcome some of these limitations this research proposes a new methodology for efficient knowledge capture and effective management of the complete knowledge life cycle. The methodology proposed in this research is validated through the development and implementation of a case study involving the optimisation of wing design concepts at an Aerospace manufacturer. The results obtained proved the extended KBE capability for fast and effective knowledge sourcing. This evidence was provided by the experts working in the development of the case study through the implementation of structured quantitative and qualitative analyses.
Purpose The purpose of this paper is to explore the role that computer vision can play within new industrial paradigms such as Industry 4.0 and in particular to support production line improvements to achieve flexible manufacturing. As Industry 4.0 requires "big data", it is accepted that computer vision could be one of the tools for its capture and efficient analysis. RGB-D data gathered from real-time machine vision systems such as Kinect (R) can be processed using computer vision techniques. Design/methodology/approach This research exploits RGB-D cameras such as Kinect (R) to investigate the feasibility of using computer vision techniques to track the progress of a manual assembly task on a production line. Several techniques to track the progress of a manual assembly task are presented. The use of CAD model files to track the manufacturing tasks is also outlined. Findings This research has found that RGB-D cameras can be suitable for object recognition within an industrial environment if a number of constraints are considered or different devices/techniques combined. Furthermore, through the use of a HMM inspired state-based workflow, the algorithm presented in this paper is computationally tractable. Originality/value Processing of data from robust and cheap real-time machine vision systems could bring increased understanding of production line features. In addition, new techniques that enable the progress tracking of manual assembly sequences may be defined through the further analysis of such visual data. The approaches explored within this paper make a contribution to the utilisation of visual information "big data" sets for more efficient and automated production.
This paper explores the use of Discrete Event Simulation (DES) for decision making in real time based on the potential for data streamed from production line sensors. Technological innovations for data collection and an increasingly competitive global market have led to an increase in the application of Discrete Event Simulation by manufacturing companies in recent years. Scenario analysis and optimisation methods are often applied to these simulation models to improve objectives such as cost, profit and throughput. The literature review has identified key research gaps as: The lack of example cases where multi-objective optimisation methods have been applied to simulation models; The need for a framework to visualise the relationship between inputs and outputs of simulation models. A framework is presented to enable the optimisation DES simulation models and optimise multiple objectives simultaneously using design of experiments and meta-models to create a Pareto front of solutions. The results show the resource allocation meta-model provides acceptable prediction accuracy whilst the lead time meta-model was not able to provide accurate prediction. Regression trees have been proposed to assist stakeholders with understanding the relationships between input and output variables. The framework uses regression and classification trees with overlaid values for multiple objectives and random forests to improve prediction accuracy for new points. A real-life test case involving a turbine assembly process is presented to illustrate the use and validity of the framework. The generated regression tree expressed a general trend by demonstrating relationships between input variables and two conflicting objectives. Random forests were implemented for creating higher accuracy predictions and they produced a mean square error of ~0.066 on the training data and ~0.081 on test data.
Purpose – The purpose of this paper is to identify measure and prioritise the perceived importance of supply chain issues within the automotive industry related to information flow during product development (PD). Design/methodology/approach – This study analyses empirical data captured from semi-structure interviews with 15 multinational companies operating in the automotive sector. Data collected are analysed using a standard methodology identified from the literature. The individual issues captured are classified against 14 clusters that represent the core and the fundamental supply chain issues of information flow. Findings – This study showed that half of the issues captured are related to the inadequate information systems used. The cluster that had the majority of individual issues is related to suppliers that are not directly connected with their customers through an enterprise system. However it was identified that two fundamental clusters justify the decision of not being directly connected. Implementing and maintaining multiple enterprise systems can be a big overhead for multinational companies working with a high number of customers. Originality/value – Although several studies have proved the benefits that can be obtained through supply chain collaboration, there are relatively little empirical studies that seek to explore the understanding of supply chain issues in regards to information flow especially during PD. By identifying, measuring and prioritising the importance of supply chain issues this study provides researchers and practitioners guidance in developing better tools and defining more efficient processes.
The aim of this work is to capture current practices in the use of computational optimisation in UK engineering companies and identify the current challenges and future needs of the companies. To achieve this aim, a survey was conducted from June 2013 to August 2013 with 17 experts and practitioners from power, aerospace and automotive Original Equipment Manufacturers (OEMs), steel manufacturing sector, small- and medium-sized design, manufacturing and consultancy companies, and optimisation software vendors. By focusing on practitioners in industry, this work complements current surveys in optimisation that have mainly focused on published literature. This survey was carried out using a questionnaire administered through face-to-face interviews lasting around 2 h with each participant. The questionnaire covered 5 main topics: (i) state of optimisation in industry, (ii) optimisation problems, (iii) modelling techniques, (iv) optimisation techniques, and (v) challenges faced and future research areas. This survey identified the following challenges that the participant companies are facing in solving optimisation problems: large number of objectives and variables, availability of computing resources, data management and data mining for optimisation workflow, over-constrained problems, too many algorithms with limited help in selection, and cultural issues including training and mindset. The key areas for future research suggested by the participant companies are as follows: handling large number of variables, objectives and constraints particularly when solution robustness is important, reducing the number of iterations and evaluations, helping the users in algorithm selection and business case for optimisation, sharing data between different disciplines for multi-disciplinary optimisation, and supporting the users in model development and post-processing through design space visualisation and data mining.
Regulatory and technological changes have recently transformed the digital footprint of credit card transactions, providing at least ten times the amount of data available for fraud detection practices that were previously available for analysis. This newly enhanced dataset challenges the scalability of traditional rule-based fraud detection methods and creates an opportunity for wider adoption of artificial intelligence (AI) techniques. However, the opacity of AI models, combined with the high stakes involved in the finance industry, means practitioners have been slow to adapt. In response, this paper argues for more researchers to engage with investigations into the use of Explainable Artificial Intelligence (XAI) techniques for credit card fraud detection. Firstly, it sheds light on recent regulatory changes which are pivotal in driving the adoption of new machine learning (ML) techniques. Secondly, it examines the operating environment for credit card transactions, an understanding of which is crucial for the ability to operationalise solutions. Finally, it proposes a research agenda comprised of four key areas of investigation for XAI, arguing that further work would contribute towards a step-change in fraud detection practices.
Scholars often recommend incorporating context into the design of an ex-plainable artificial intelligence (XAI) model in order to deliver the successful integration of an explainable agent into a real-world operating environment. However, few in the field of XAI have expanded upon the meaning of context, or provided clarification as to what they consider its constituent parts. This paper answers that question by providing a thematic review of the extant literature , revealing an interaction between the contextual elements of Setting, Audience, Goals and Ethics (SAGE). This paper therefore proposes SAGE as a conceptual framework that enables researchers to build audience-centric and context-sensitive XAI, thereby strengthening the prospects for successful adoption of an XAI solution.
Discrete - Event Simulation (DES) is commonly used for the simulation of manufacturing systems. In many practical cases, DES practitioners ha ve to make simplifications or to use the software in an unconventional or convoluted fashion to meet their needs. Petri nets enable the development of transparent models which allow increased flexibility and control for designers. Furthermore, Petri nets t ake advantage of a solid mathematical ground and constitute a simple language. However, Petri nets lack the software capabilities to realise their full potential. This study investigates the suitability and relevance of Discrete - Event Simulation (DES) soft ware for Petri net modelling in the context of manufacturing systems. A framework is developed for the modelling of different classes of Petri nets on DES. Analytical models of asynchronous flow lines are developed. Initial results show that the analytical models are without closed - form solution and the explosion of the state space is observed, justifying the use of computational methods and simulation for the analysis of manufacturing systems. This study shows that the gain in flexibility provided by Petri nets provides a new insight into the effects of stochasticity on setup and failure times in manufacturing systems.
Discrete Event Simulation (DES) can help speed up the layout design process. It offers further benefits when combined with Virtual Reality (VR). The latest technology, Immersive Virtual Reality (IVR), immerses users in virtual prototypes of their manufacturing plants to-be, potentially helping decision-making. This work seeks to evaluate the impact of visual fidelity, which refers to the degree to which objects in VR conforms to the real world, using an IVR visualisation of the DES model of an actual shop floor. User studies are performed using scenarios populated with low- and high-fidelity models. Study participant carried out four tasks representative of layout decision-making. Limitations of existing IVR technology was found to cause motion sickness. The results indicate with the particular group of naïve modellers used that there is no significant difference in benefits between low and high fidelity, suggesting that low fidelity VR models may be more cost-effective for this group.
Purpose - The purpose of this paper is to present a comparison of a number of business process mining tools currently available in the UK market. An outline of the practice of business process mining is given, along with an analysis of the main techniques developed by academia and commercial entities. This paper also acts as a primer for the acceptance and further use of process mining in industry, suggesting future directions for this practice. Design/methodology/approach - Secondary research has been completed to establish the main commercial business process mining tool vendors for the market. A literature survey has also been undertaken into the latest theoretical techniques being developed in the field of business process mining. Findings - The authors have identified a number of existing commercially available business process mining tools and have listed their capabilities within a comparative analysis table. All commercially available business process mining tools included in this paper are capable of process comparison and at least 40 per cent of the tools claim to deal with noise in process data. Originality/value - The contribution of this paper is to provide a state-of-the-art review of a number of commercial business process mining tools available within the UK. This paper also presents a summary of the latest research being undertaken in academia in this subject area and future directions for the practice of business process mining.
The changing nature of manufacturing, in recent years, is evident in industries willingness to adopt network connected intelligent machines in their factory development plans. While advances in sensors and sensor fusion techniques have been significant in recent years, the possibilities brought by Internet of Things create new challenges in the scale of data and its analysis. The development of audit trail style practice for the collection of data and the provision of comprehensive framework for its processing, analysis and use should be an important goal in addressing the new data analytics challenges for maintenance created by internet connected devices. This paper proposes that further research should be conducted into audit trail collection of maintenance data and the provision of a comprehensive framework for its processing analysis and use. The concept of ‘Human in the loop’ is also reinforced with the use of audit trails, allowing streamlined access to decision making and providing the ability to mine decisions.
The increasing demand for a sustainable, reliable and secure supply chain for food products has led to the application of digital technologies such as blockchain to improve operational effectiveness. The purpose of this paper is to investigate the integration barriers of Blockchain Technology (BCT) within Circular Food Supply Chains (CFSCs) towards firm’s operational effectiveness through a multi-methodological process. Initially the integration barriers are identified through a review of literature and these risks are categorised, using evidence obtained by survey questionnaire completed by experts in the integrated research arena. A further quantified prioritisation of these barriers is made by utilizing a Fuzzy Delphi approach, validated by expert practitioners drawn from the food production and supply organizations. Finally, through semi-structured interviews with Blockchain and FSC experts, an examination of how the integration barriers affect operational effectiveness may be mitigated is provided. This paper concludes that the identified barriers to blockchain integration have real impact on the operational effectiveness of the firm that can only be clarified through industry wide standardised processes.
This paper outlines a vision for Internet connected production complementary to the Cloud Manufacturing paradigm, reviewing current research and putting forward a generic outline of this form of manufacture. This paper describes the conceptual positioning and practical implementation of the latest developments in manufacturing practice such as Redistributed manufacturing, Cloud manufacturing and the technologies promoted by Industry 4.0 and Industrial Internet agendas. In the illustration of the outline of web enabled production a case study is presented based on automotive manufacture. Existing and future needs for customized production and the manufacturing flexibility required are examined. Future directions for manufacturing, enabled by web based connectivity are then examined, concluding that the need for humans to remain ‘in the loop’ while automation develops is an essential ingredient of all future manufacturing scenarios.
The rise in EVs popularity, combined with reducing emissions and cutting costs, encouraged delivery companies to integrate them in their fleets. The fleet heterogeneity brings new challenges to the Capacitated Vehicle Routing Problem (CVRP). Driving range and different vehicles' capacity constraints must be considered. A cluster-first, route-second heuristic approach is proposed to maximise the number of parcels delivered. Clustering is achieved with two algorithms: a capacitated k-median algorithm that groups parcel drop-offs based on customer location and parcel weight; and a hierarchical constrained minimum weight matching clustering algorithm which considers EVs' range. This reduces the solution space in a meaningful way for the routing. The routing heuristic introduces a novel Monte-Carlo Tree Search enriched with a custom objective function, rollout policy and a tree pruning technique. Moreover, EVs are preferred overother vehicles when assigning parcels to vehicles. A Tabu Search step further optimises the solution. This two-step procedure allows problems with thousands of customers and hundreds of vehicles to be solved accomodating customised vehicle constraints. The solution quality is similar to other CVRP implementations when applied to classic VRP test-instances; and its quality is superior in real-world scenarios when constraints for EVs must be used.
In recent years a step change has been seen in the rate of adoption of Industry 4.0 technologies by manufacturers and industrial organizations alike. This paper discusses the current state of the art in the adoption of industry 4.0 technologies within the construction industry. Increasing complexity in onsite construction projects coupled with the need for higher productivity is leading to increased interest in the potential use of industry 4.0 technologies. This paper discusses the relevance of the following key industry 4.0 technologies to construction: data analytics and artificial intelligence; robotics and automation; buildings information management; sensors and wearables; digital twin and industrial connectivity. Industrial connectivity is a key aspect as it ensures that all Industry 4.0 technologies are interconnected allowing the full benefits to be realized. This paper also presents a research agenda for the adoption of Industry 4.0 technologies within the construction sector; a three-phase use of intelligent assets from the point of manufacture up to after build and a four staged R&D process for the implementation of smart wearables in a digital enhanced construction site.
Microfluidics is a relatively new and profitable domain. Constant development of new technologies and a growing demand for more versatile products are the cause of increasing domain complexity in this area. A review of existing research in the microfluidic devices domain has highlighted a lack of customer and service-orientation in their design. The developed guidelines detailed in this paper present a proposal for a general process for the design of microfluidics. The solution attempts to tackle the issue of sub-section interactions and brings the domain one step towards an 'experience economy' by incorporating service-considerations into the design process. Step by step instructions for the guidelines usage are given. The validation of the guidelines has been conducted with microfluidic designers, and the results prove that the guidelines are applicable.
Current OEM (Original Equipment Manufacturer) facilities tend to be highly integrated and are often situated on one site. While providing scale of production such centralisation may create barriers to the achievement of fully flexible, adaptable, and reconfigurable factories. The advent of Industry 4.0 opens up opportunities to address these barriers by decentralising information and decision-making in manufacturing systems through CPS (Cyber Physical Systems) use. This research presents a qualitative study that investigates the possibility of distributing information and decision-making logic into ‘smart workpieces’ which can actively participate in assembly operations. To validate the concept, a use-case demonstrator, corresponding to the assembly of a ‘flat-pack’ table, was explored. Assembly parts in the demonstrator, were equipped with computation, networking, and interaction capabilities. Ten participants were invited to evaluate the smart assembly method and compare its results to the traditional assembly method. The results showed that in its current configuration the smart assembly was slower. However, it made the assembly process more flexible, adaptable and reconfigurable.
Purpose This paper reports on the experimentation of an integrated manufacturing and building model to improve energy efficiency. Traditionally, manufacturing and building-facilities engineers work independently, with their own performance objectives, methods and software support. However, with progresses in resource reduction, advances have become more challenging. Further opportunities for energy efficiency require an expansion of scope across the functional boundaries of facility, utility and manufacturing assets. Design/methodology/approach The design of methods that provide guidance on factory modelling is inductive. The literature review outlines techniques for the simulation of energy efficiency in manufacturing, utility and facility assets. It demonstrates that detailed guidance for modelling across these domains is sparse. Therefore, five experiments are undertaken in an integrated manufacturing, utility and facility simulation software IES < VE > . These evaluate the impact of time-step granularity on the modelling of a paint shop process. Findings Experimentation demonstrates that time-step granularity can have a significant impact on simulation model results quality. Linear deterioration in results can be assumed from time intervals of 10 minutes and beyond. Therefore, an appropriate logging interval, and time-step granularity should be chosen during the data composition process. Time-step granularity is vital factor in the modelling process, impacting the quality of simulation results produced. Practical implications This work supports progress towards sustainable factories by understanding the impact of time-step granularity on data composition, modelling, and on the quality of simulation results. Better understanding of this granularity factor will guide engineers to use an appropriate level of data and understand the impact of the choices they are making. Originality/value This paper reports on the use of simulation modelling tool that links manufacturing, utilities and facilities domains, enabling their joint analysis to reduce factory resource consumption. Currently, there are few available tools to link these areas together; hence, there is little or no understanding of how such combined factory analysis should be conducted to assess and reduce factory resource consumption.
•The paper focuses on the matching of digital technologies to maintenance practice in the automotive sector.•A framework for IOT enabled circular maintenance practice and treatment of automotive parts is proposed.•The framework proposed is capable of processing data from vehicle based sensors.•An Auto-circular simulator concept is outlined, providing visualisation and analytics toolbox capabilities.•A case study focused on a hydrogen car power unit is included, with a supporting ontology. The adoption of the Circular Economy paradigm by industry leads to increased responsibility of manufacturing to ensure a holistic awareness of the environmental impact of its operations. In mitigating negative effects in the environment, current maintenance practice must be considered for its potential contribution to a more sustainable lifecycle for the manufacturing operation, its products and related services. Focusing on the matching of digital technologies to maintenance practice in the automotive sector, this paper outlines a framework for organisations pursuing the integration of environmentally aware solutions in their production systems. This research sets out an agenda and framework for digital maintenance practice within the Circular Economy and the utilisation of Industry 4.0 technologies for this purpose.
Composite laminate manual lay-up operations and component quality inspections involve a variety of complex operations and instructions requiring highly-skilled operators, which can result in time-consuming and cost-inefficient processes. This research attempts to check the compatibility of Virtual Fabric Placement (VFP) and Microsoft Kinect to aid laminators and composite production. This research has investigated the feasibility of using this tracking technology to support the virtual prototyping of manual composite lay-up. It is concluded that, at the current stage of development, Kinect and VFP can be successfully used for virtual prototyping of large scale geometries while encountering only negligible tracking error with respect to mould size.
High value manufacturing systems still require ergonomically intensive manual activities. Examples include the aerospace industry where the fitting of pipes and wiring into confined spaces in aircraft wings is still a manual operation. In these environments, workers are subjected to ergonomically awkward forces and postures for long periods of time. This leads to musculoskeletal injuries that severely limit the output of a shopfloor leading to loss of productivity. The use of tools such as wearable sensors could provide a way to track the ergonomics of workers in real time. However, an information processing architecture is required in order to ensure that data is processed in real time and in a manner that meaningful action points are retrieved for use by workers. In this work, based on the Adaptive Control of Thought—Rational (ACT-R) cognitive framework, we propose a Cognitive Architecture for Wearable Sensors (CAWES); a wearable sensor system and cognitive architecture that is capable of taking data streams from multiple wearable sensors on a worker’s body and fusing them to enable digitisation, tracking and analysis of human ergonomics in real time on a shopfloor. Furthermore, through tactile feedback, the architecture is able to inform workers in real time when ergonomics rules are broken. The architecture is validated through the use of an aerospace case study undertaken in laboratory conditions. The results from the validation are encouraging and in the future, further tests will be performed in an actual working environment.
Process mining techniques are able to extract knowledge from event logs commonly available in today’s information systems. These techniques provide new means to discover, monitor, and improve processes in a variety of application domains. There are two main drivers for the growing interest in process mining. On the one hand, more and more events are being recorded, thus, providing detailed information about the history of processes. On the other hand, there is a need to improve and support business processes in competitive and rapidly changing environments. This manifesto is created by the IEEE Task Force on Process Mining and aims to promote the topic of process mining. Moreover, by defining a set of guiding principles and listing important challenges, this manifesto hopes to serve as a guide for software developers, scientists, consultants, business managers, and end-users. The goal is to increase the maturity of process mining as a new tool to improve the (re)design, control, and support of operational business processes.
Fibre steering is involved in the development of non-conventional variable stiffness laminates (VSL) with curvilinear paths as well as in the lay-up of conventional laminates with complex shapes. Manufacturability is generally overlooked in design and, as a result, industrial applications do not take advantage of the potential of composite materials. This work develops a design for manufacturing (DFM) tool for the introduction in design of the manufacturing requirements and limitations derived from the fibre placement technology. This tool enables the automatic generation of continuous fibre paths for manufacturing. Results from its application to a plate with a central hole and an aircraft structure – a windshield front fairing – are presented, showing good correlation of resulting manufacturable paths to initial fibre trajectories. The effect of manufacturing constraints is assessed to elucidate the extent to which the structurally optimal design can be reached while conforming to existing manufacturing specifications.
The accessibility of legal documents to the different actors of the judicial system needs to be ensured for the implementation of a strong international rule of law. The gap of such accessibility is being addressed by the Jus Mundi multilingual search-engine for International Law. The data updated on this platform is qualified by skilled lawyers. However, the interconnection of references within such documents, is a key feature for lawyers since, a major part of the legal research is analysing such citations to support their arguments. The process of interconnecting such references can prove to be expensive as well as time-consuming, if completed manually. Hence, the purpose of this research is to automatically extract such legal citations within international law, using Natural Language Processing (NLP), enabling the interconnectivity of documents on Jus Mundi. This study also discusses and addresses research gaps within this subject, especially in the domain specific to International Law. The method followed to achieve the automation is building an adaptable model through Regular-Expression based annotation language named JAPE (Java Annotation Patterns Engine). This set of automatically extracted links are then to be integrated with the search engine, having direct implication in the enablement of smoother navigation, making the law more accessible. This research also contributes to the state of the art bringing closer the eventual use of NLP in applications used to interact with International Law documents.
This paper reviews the area of combined discrete event simulation (DES) and virtual reality (VR) use within in- dustry. While establishing a state of the art for progress in this area, this paper makes the case for VR DES as the vehicle of choice for complex data analysis through interactive simulation models, highlighting both its advantages and current limitations. This pa- per reviews active research topics such as VR and DES real-time integration, communication protocols, system design considera- tions, model validation, and applications of VR and DES. While summarizing future research directions for this technology combi- nation, the case is made for smart factory adoption of VR DES as a new platform for scenario testing and decision making. It is put that in order for VR DES to fully meet the visualization require- ments of both Industry 4.0 and Industrial Internet visions of digital manufacturing, further research is required in the areas of lower latency image processing, DES delivery as a service, gesture recog- nition for VR DES interaction, and linkage of DES to real-time data streams and Big Data sets.
The purpose of this paper is to demonstrate a system architecture for integrating product lifecycle management (PLM) systems with cross supply chain maintenance information to support root cause analysis. By integrating product data from PLM systems with warranty claims, vehicle diagnostics and technical publications, engineers were able to improve the root cause analysis and close the information gaps. Data collection was achieved via in-depth semi-structured interviews and workshops with experts from the automotive sector. Unified Modelling Language (UML) diagrams were used to design the system architecture proposed. A user scenario is also presented to demonstrate the functionality of the system.
Innovation outsourcing is a phenomenon that is gaining increasing interest amongst both practitioners and academics alike. Despite this there does not exist a comprehensive study which identifies the status of knowledge within this domain. This study aims to fill this gap. The extant literature is reviewed and analysed to define a baseline of existing research and to guide further research. This review aims to address the questions of what is innovation outsourcing, the significance of innovation outsourcing and the key issues associated with innovation outsourcing.
Remanufacturing is a viable option to extend the useful life of an end-of-use product or its parts, ensuring sustainable competitive advantages under the current global economic climate. Challenges typical to remanufacturing still persist, despite its many benefits. According to the European Remanufacturing Network, a key challenge is the lack of accurate, timely and consistent product knowledge as highlighted in a 2015 survey of 188 European remanufacturers. With more data being produced by electric and hybrid vehicles, this adds to the information complexity challenge already experienced in remanufacturing. Therefore, it is difficult to implement real-time and accurate remanufacturing for the shop floor; there are no papers that focus on this within an electric and hybrid vehicle environment. To address this problem, this paper attempts to: (1) identify the required parameters/variables needed for fuel cell remanufacturing by means of interviews; (2) rank the variables by Pareto analysis; (3) develop a casual loop diagram for the identified parameters/variables to visualise their impact on remanufacturing; and (4) model a simple stock and flow diagram to simulate and understand data and information-driven schemes in remanufacturing.
This research examines the opportunities provided by advances in digital manufacturing technologies for the provision of products designed to meet the needs of an individual consumer. The ability to co-create products with customers could enable mass personalisation to become a popular and fast-growing mode of production. Additive manufacturing, in both 3D and 4D printing forms, opens up new opportunities for circular economy-compliant production of such highly personalised products. Industry 4.0 has been seen by many as an agenda for the utilisation of interconnected digital technologies in industry, with a particular focus on manufacturing. Industry 5.0 seeks to address challenges that have grown in importance since the inception of Industry 4.0, such as the efficient inclusion of human worker skills in tandem with automation solutions, to address highly complex manufacturing scenarios while mitigating many of the environmental issues inherent with current manufacturing practices, while using circular economy principles. In examining the production of smart fabrics, this paper puts forward a framework for circular production of additively manufactured personalised products, co-designed with inputs from consumers.
This paper seeks to examine the area of circular economy, providing an overview of the development of data driven circular approaches in manufacturing, particularly Industry 4.0, from the point of view of Reuse, Remanufacturing, Redistribution and Recycle. This paper also aims to develop a working framework for future circular economy research. The Design, methodological approach of this paper focuses on a comprehensive review of literature covering over 51 research papers. These papers are analysed using pie charts and bar charts to understand current trends in circular economy and circular economy related research and future research directions in the field. Findings show that research on circular economy has been steady and gradual with 2014 and 2015 having the most papers on the subject with 43% of the papers from engineering related research. Research which links circular strategies and their application within Industry 4.0 to digital technologies is still a very new area of research and, as such, is an area for further studies. Although papers on Circular Economy and Circular Economy Approaches exists, however, there are no papers that offer an overview of the development of circular approaches within manufacturing. The contribution of this paper is to provide a summary of current trends in circular economy research in manufacturing, within focus on Industry 4.0. A review of this development has been provided in the form of illustrative charts and graphs that identifies these trends. From this a framework for future circular economy research as it relates to manufacturing was developed.
National railways are typically large and complex systems. Their network infrastructure usually includes extended track sections, bridges, stations and other supporting assets. In recent years, railways have also become a data-rich environment. Railway infrastructure assets have a very long life, but inherently degrade. Interventions are necessary but they can cause lateness, damage and hazards. Every day, thousands of discrete maintenance jobs are scheduled according to time and urgency. Service disruption has a direct economic impact. Planning for maintenance can be complex, expensive and uncertain. Autonomous scheduling of maintenance jobs is essential. The design strategy of a novel in- tegrated system for automatic job scheduling is presented; from concept formulation to the ex- amination of the data to information transitional level interface, and at the decision making level. The underlying architecture con fi gures high-level fusion of technical and business drivers; scheduling optimized intervention plans that factor-in cost impact and added value. A proof of concept demonstrator was developed to validate the system principle and to test algorithm functionality. It employs a dashboard for visualization of the system response and to present key information. Real track incident and inspection datasets were analyzed to raise de- gradation alarms that initiate the automatic scheduling of maintenance tasks. Optimum sche- duling was realized through data analytics and job sequencing heuristic and genetic algorithms, taking into account speci fi c cost & value inputs from comprehensive task cost modelling. Formal face validation was conducted with railway infrastructure specialists and stakeholders. The de- monstrator structure was found fi t for purpose with logical component relationships, o ff ering further scope for research and commercial exploitation
A considerable proportion of current point-of-care devices do not offer a wide enough set of capabilities if they are to function in any telehealth system. There is a need for intermediate devices that lie between healthcare devices and service networks. The development of an application is suggested that allows for a smartphone to take the role of an intermediate device. This research seeks to identify the telehealth service requirements for long-term condition management using a product-service system approach. The use of product-service system has proven to be a suitable methodology for the design and development of telehealth smartphone applications.
The modern manufacturing industry, especially in developed economies, is pushing towards automation of skill-intensive manual manufacturing operations to remain globally competitive. However, automation of such operations is not trivial because it is difficult to replace a highly skilled human with an equivalent machine. Therefore, it is necessary to capture and extract human skills from skill-intensive manufacturing operations in order to enable the process of automating such operations. To achieve this goal, the first step is to capture, digitise and segment the human-workpiece interactions during a simplified manual manufacturing operation in preparation for skill extraction. This paper presents one such attempt using a gaming interface device (Microsoft Kinect™) to simultaneously capture human actions and the resulting workpiece motions non-obtrusively in three dimensions in real-time. The captured human-workpiece interaction data is automatically segmented into human action states, represented as therbligs and workpiece states, using which the subsequent skill extraction can be performed. The use of therbligs also enables this work to be used for human motion analysis for effective and ergonomic design of assembly workstations.
Automation boosts competitiveness of manufacturing companies and is pervasive in modern industry. However, skilled manual labour is still used in a variety of complex tasks and is currently irreplaceable. A solution may lie in understanding the interactions between a human worker and the workpiece during a manufacturing task and digitising these interactions to potentially enable automation of the task. In this paper, a method to observe, record and digitise human-workpiece interactions using the Microsoft Kinectim is described. A manual threaded-fit assembly of a two-component pen housing is chosen. Essential information about the manual assembly is extracted from the recorded interaction data. The developed mechanism being markerless and unobtrusive is helpful in recording human-workpiece interactions in a factory without affecting normal operations.
This paper presents a novel method for dynamic alignment control using infrared light depth imagery to enable automated wheel loading operation for the trim and final automotive assembly line. A key requirement for automated wheel loading is to track the motion of the wheel hub and simultaneously identify the spatial positions and angular orientations of its alignment features in real-time on a moving vehicle body. This requirement is met in this work, where low-cost infrared depth-imaging devices like Microsoft Kinect (TM) and Asus Xtion (TM), vastly popular in the gaming industry, are used to track a moving wheel hub and recognise alignment features on both the wheel hub and the wheel in real time in a laboratory environment. Accurate control instructions are then computed to instruct the automation system to rotate the wheel to achieve precise alignment with the wheel hub and load the wheel at the right time. Experimental results demonstrate that the reproducibility error in alignment control satisfies the assembly tolerance of 2mm for the wheel loading operation, and thus the proposed method can be applied to automate wheel assembly on the trim and final automotive assembly line. The novelty of this work lies in its use of depth imaging for dynamic alignment control, which provides real-time spatial data in all 3 axes simultaneously as against the popularly reported RGB imaging techniques that are computationally more demanding, sensitive to ambient lighting and require the use of additional force sensors to obtain depth axis control data. This paper demonstrates the concept of a light-controlled factory where depth imaging using infrared light and depth image analysis is used to enable intelligent control in automation. (C) 2014 The Authrs. Published by Elsevier B.V.
Manufacturers are facing increased pressure from external forces. This has led to companies competing for shorter development cycles in order to gain market share. Product lifecycle management (PLM), particularly within complex industries such as the aeronautical industry, is a business activity which may leverage stakeholders to achieve business objectives. PLM implementations however are not meeting timescales and budget expectations, therefore the need to improve efficiency and effectiveness in PLM implementations is required and the use of lean principles to do so is a potential way forward. This paper explores the use of lean principles to improve the efficiency and effectiveness of product lifecycle management (PLM) solutions. A lean PLM deployment methodology has been developed as part of this research, based on surveys of current lean PLM practice and the potential for further gains by holistic use of lean principles is outlined. From the research featured in this paper it has been found that the application of lean principles and subsequently its methods and tools, support the improvement of efficiency and effectiveness within PLM implementations.
Planning and scheduling activities within the rail industry have benefited from developments in computer-based simulation and modelling techniques over the last 25 years. Increasingly, the use of computational intelligence in such tasks is featuring more heavily in research publications. This paper examines a number of common rail-based planning and scheduling activities and how they benefit from five broad technology approaches. Summary tables of papers are provided relating to rail planning and scheduling activities and to the use of expert and decision systems in the rail industry.
Purpose - The techniques that help organisations implement leading edge cost and quality practices in manufacturing operations management are typically disparate and generic in nature. There is a need to identify integrated practices at the right level of granularity, based on a clear definition of the existing operations practices. This paper proposes a novel framework for achieving and maintaining good cost and quality operations management practice within a manufacturing environment. Design/methodology/approach - The framework uses a new approach for identifying the profile of current activities and better practice activities for the roles of team leaders, cell leaders and operations managers within a manufacturing company. Findings - The paper proposes a recommended set of context-specific activities for these roles. These recommended activities are utilised to develop a cascade of deployable recommendations. Originality/value - The framework is illustrated within a manufacturing environment producing complex product ranges. The implementation of the framework enables improved operational efficiency and effectiveness. It also enables the benefits of improved operational standardisation and consistency.
This paper explores the need for new visualisation modes to better enable interaction with increasingly complex and sophisticated Discrete Event Simulation (DES) models. In this research an initial framework for interactive and immersive DES models is put forward along with an extended framework, which takes account of the potential of streaming data from production line/shop floor sensor networks. The initial framework is illustrated by a test case involving the modelling of a maintenance and repair facility. A visualisation metaphor is provided as an illustration of an extended framework, and its potential operation as an interactive visualisation component within a Digital Twin for manufacturing.
The purpose of this review is to provide an analysis and comparison of publications identified in the area of information flow in supply chain management. Although review articles have extensively analysed supply chain management during the manufacturing phase of the product lifecycle, product development and service phases seems to be largely separated. Therefore a total of 132 journal articles were systematically selected and analysed. In order to enable a methodological approach, a framework is proposed to classify the publications based on the product lifecycle phase and the type of the publication. Each phase of the product lifecycle is discussed in detail and research gaps are identified. Finally cross-phase research gaps are identified to provide guidelines for future research.
Mitigation of cost pressures is an ever present factor in every commercial organisation's corporate strategy. This is especially true for automotive manufacturers. This paper explores the development of a partner selection and inventory reduction process for use within the automotive industry. The research featured in this paper carried out an assessment of the inventory holding of a large automotive manufacturer. This research identifies suppliers with the capability to provide maintenance, repair and operations (MRO) inventory reduction services under the technical constraints of a large automotive manufacturing facility, and then operates a trial of their inventory reduction process against the sponsor company's inventory. The study establishes a process for managing the identification of commodity groups to investigate, and the transfer of parts data and analytical findings between the parties. Validation is provided through the analysis of results recorded during the implementation in the context of the sponsor company.
The aim of process mining is to identify and extract process patterns from data logs to reconstruct an overall process flowchart. As business processes become more and more complex there is a need for managers to understand the processes they already have in place. To undertake such a task manually would be extremely time consuming so the practice of process mining attempts to automatically reconstruct the correct representation of a process based on a set of process execution traces. This paper outlines an alternative approach to business process mining utilising a Genetic Programming (GP) technique coupled with a graph based representation. The graph based representation allows greater flexibility in the analysis of process flowchart structure and offers the possibility of mining complex business processes from incomplete or problematic event logs. A number of event logs have been mined by the GP technique featured in this paper and the results of the experimentation point towards the potential of this novel process mining approach.
Business processes have been discussed for more than a decade now. However, there are not as of yet comprehensive and substantial benefits that can justify the hype around the concept. This paper contrasts and summarises the main findings of literature research and a targeted survey conducted within the service industry in order to investigate the current state of research and practice regarding key aspects of business processes. The survey involved the participation of 25 respondents working in service industry sectors such as finance, public sector and consultancy. The paper demonstrates that although theoretical developments are dealing with sophisticated issues around business processes, the service industry is reluctant to adopt a similar perspective and still uses simple and manual techniques in dealing with business processes. The main reason is that the service industry is not convinced that a business process approach could bring significant tangible and measurable benefits. This is due to the fact that there is no comprehensive and systematic solution proposed in terms of a fully functional business process software suite. The requirements for an integrated business process management tool include some of the paper's findings. (C) 2008 Elsevier B.V. All rights reserved.
The changing nature of manufacturing, in recent years, is evident in industry's willingness to adopt network-connected intelligent machines in their factory development plans. A number of joint corporate/government initiatives also describe and encourage the adoption of Artificial Intelligence (AI) in the operation and management of production lines. Machine learning will have a significant role to play in the delivery of automated and intelligently supported maintenance decision-making systems. While e-maintenance practice provides aframework for internet-connected operation of maintenance practice the advent of IoT has changed the scale of internetworking and new architectures and tools are needed. While advances in sensors and sensor fusion techniques have been significant in recent years, the possibilities brought by IoT create new challenges in the scale of data and its analysis. The development of audit trail style practice for the collection of data and the provision of acomprehensive framework for its processing, analysis and use should be avaluable contribution in addressing the new data analytics challenges for maintenance created by internet connected devices. This paper proposes that further research should be conducted into audit trail collection of maintenance data, allowing future systems to enable 'Human in the loop' interactions.
Since it first appeared in literature in the early nineties, the Circular Economy (CE) has grown in significance amongst academic, policymaking, and industry groups. The latest developments in the CE field have included the interrogation of CE as a paradigm, and its relationship with sustainability and other concepts, including iterative definitions. Research has also identified a significant opportunity to apply circular approaches to our rapidly changing industrial system, including manufacturing processes and Industry 4.0 (I4.0) which, with data, is enabling the latest advances in digital technologies (DT). Research which fuses these two areas has not been extensively explored. This is the first paper to provide a synergistic and integrative CE-DT framework which offers directions for policymakers and guidance for future research through a review of the integrated fields of CE and I4.0. To achieve this, a Systematic Literature Review (SLR; n = 174) of the empirical literature related to digital technologies, I4.0, and circular approaches is conducted. The SLR is based on peer-reviewed articles published between 2000 and early 2018. This paper also summarizes the current trends in CE research related to manufacturing. The findings confirm that while CE research has been on the increase, research on digital technologies to enable a CE is still relatively untouched. While the “interdisciplinarity” of CE research is well-known, the findings reveal that a substantial percentage is engineering-focused. The paper concludes by proposing a synergistic and integrative CE-DT framework for future research developed from the gaps in the current research landscape.
The practice of optimising business processes has, until recently, been undertaken mainly as a manual task. This paper provides insight s into a n automated business process optimisation framework by using web services for the development of re - configurable business processes. The research presented here extends the framework of Vergidis (2008) by introducing web services as a mechanism for facilitating business process interactions, identifying enhancements to support business processes and undertaking three case studies to evaluate the proposed enhancements. The featured case studies demonstrate that an increase in the amount of available web services gives rise to improvements in the business processes generated. This research highlights an increase in the efficiency of the algorithm and the quality of the business proc ess designs that result from the enhancements . Future research directio ns are proposed for the further improvement of the framework
The use of curvilinear fibre paths to develop variable stiffness laminates is now recognised as a promising technique offering great potential for performance improvements over conventional straight fibre' laminates. Its manufacture is feasible by fibre placement technologies, such as automated fibre placement. However, these technologies present a set of limitations that need to be included in the design to guarantee the manufacturability and quality of the composite laminates. Although this approach experiences an increasing interest from the specialised literature, most of the works completed overlook the manufacturing reality and, as a result, variable stiffness laminates are not used in industry. This work aims to provide a review of the State-of-the-Art on design for manufacture of variable stiffness in order to highlight the current gaps and research needs. As a conclusion, tools for analysis of the effect of manufacturing defects, manufacturing optimisation of gaps/overlaps or cycle time and the systematic integration of manufacturing constraints in design, are the main challenges that will be faced in the future to be able to exploit the potential of this advanced tailoring technique.
first_pagesettingsOrder Article Reprints Open AccessArticle Manufacturing in the Age of Human-Centric and Sustainable Industry 5.0: Application to Holonic, Flexible, Reconfigurable and Smart Manufacturing Systems by Chris Turner 1,*ORCID andJohn Oyekan 2 1 Surrey Business School, University of Surrey, Guildford GU2 7XH, UK 2 Real Time and Distributed Systems Group, Department of Computer Science, University of York, Heslington, York YO10 5GH, UK * Author to whom correspondence should be addressed. Sustainability 2023, 15(13), 10169; https://doi.org/10.3390/su151310169 Received: 11 May 2023 / Revised: 20 June 2023 / Accepted: 23 June 2023 / Published: 27 June 2023 Download Browse Figures Versions Notes Abstract This paper provides a classification of manufacturing types in terms of new technological tools provided in the Industry 5.0 framework. The manufacturing types agile, holonic, flexible and reconfigurable benefit from and are potentially changed by Industry 4.0 technologies and the human-centric focus of Industry 5.0. Furthermore, the use of Lifecycle Analysis (LCA) provides a holistic method for estimating the true value of emissions emitted during the carrying out of manufacturing decisions. As a result, LCA may be used as a central guiding framework, in addition to the use of Circular Economy metrics, for decisions in manufacturing whose results could be presented to humans as part of a scenario-generation system using visualisations within a Digital Twin environment. This enables a decision maker to make informed decisions regarding current and future production needs. Regardless of the size of production facility, this integrated approach is perhaps the most significant gap in research identified by this survey of manufacturing types and systems when viewed through the lens of Industry 5.0. This paper makes the contribution of providing an assessment of the major manufacturing types in the context of Industry 5.0, highlighting the gaps in the current research and providing a sustainable and human-centric agenda supported by LCA use with modern production methodologies.
This paper explores the notion of the modular building construction site as an applied instance of redistributed manufacturing; in so doing, this research seeks to reduce the environmental footprint of building sites, treating them as small digitally connected subunits. In seeking to provide a whole lifecycle appreciation of a construction project, it is noted that the presence of a framework to provide guidance on the consideration of Internet of Things (IoT) data streams and connected construction objects is currently lacking. This paper proposes use of embedded IoT enabled sensing technology within all stages of a modular building lifecycle. An expanded four-phase model of intelligent assets use in construction is proposed along with an outline of the required data flows between the stages of a given building’s entire lifecycle that need to be facilitated for a BIM (Buildings Information Modelling) representation to begin to describe a building project as a sustainable asset within the circular economy. This paper also describes the use of concrete as a modular sensing structure; proposing that health monitoring of the material in situ along with the recoding of environmental factors over time could help to extend the longevity of such structures.
Industry 4.0 derived technologies have the potential to enable a new wave of digital manufacturing solutions for semi and fully automated production. In addition, this paradigm encompasses the use of communication technologies to transmit data to processing stations as well as the utilization of cloud based computational resources for data mining. Despite the rise in automation, future manufacturing systems will initially still require humans in the loop to provide supervisory level mediation for even the most autonomous production scenarios. Through a structured review, this paper details a number of key technologies that are most likely to shape this future and describes a range of scenarios for their use in delivering human mediated automated and autonomous production. This paper argues that in all cases of future manufacturing management it is key that the human has oversight of critical information flows and remains an active participant in the delivery of the next generation of production systems.
Recent introduction of low-cost 3D sensing and affordable immersive virtual reality have lowered the barriers for creating and maintaining 3D virtual worlds. In this paper, we propose a way to combine these technologies with discrete-event simulation to improve the use of simulation in decision making in manufacturing. This work will describe how feedback is possible from real world systems directly into a simulation model to guide smart behaviors. Technologies included in the research include feedback from RGBD images of shop floor motion and human interaction within full immersive virtual reality that includes the latest headset technologies.
Purpose - The purpose of this paper is to propose a methodology for rapidly and reliably capturing, representing and analysing process systems to facilitate the potential for operations performance improvement within a complex product design and manufacturing facility operating in a high-performance business environment. Design/methodology/approach - This paper demonstrates the proposed methodology within an electro-mechanical design and manufacturing environment producing complex non-standard products for a global market. The technique has national and international application for a wide spectrum of design and manufacturing facilities. Findings - The authors also demonstrate the effectiveness of the proposed methodology in capturing, representing and analysing processes to assess the feasibility of and identify the issues involved in realising further performance improvements in an existing complex product, high variety, design and manufacturing facility. Practical implications - Through the enhanced level of understanding of business processes and knowledge intensive operations, the design and manufacturing facilities managers can now realise the next level of performance enhancement by fully exploiting the potential of performance improvement initiatives. Since the proposed methodology creates an environment in which risks inherent in new techniques are controlled, the facilities managers can also gain competitive advantage by becoming the early adopters of radical performance enhancement approaches. Originality/value - Most major and many smaller manufacturing companies have adopted the popular performance improvement initiatives. These companies are now striving to achieve the next level of performance enhancement at the system or enterprise level and require a better understanding of their business processes and knowledge intensive operations. This understanding needs to be achieved rapidly, cost effectively and in a readily communicable and quantifiable form to allow analysis and ongoing re-analysis within the volatile industrial environment. The proposed methodology achieves this through the identification, communication, understanding and analysis of the internal and external interactions and dependencies of the facility.
This paper aims to ascertain the optimum values for two fitness function parameters within a process mining genetic algorithm; the o parameter, which reduces the likelihood of process models with extra behaviour being selected and the parameter, which restricts the selection of models containing duplicate tasks. The experiments conducted in this research also include the use of a decaying rate for the mutation operator in order to promote greater accuracy in the mined process models. The paper concludes that the optimum setting of the fitness function parameters will in fact vary depending on the constructs found in each process model. This paper finds that a higher value for one of the fitness function parameters allows for simple process constructs to be mined with greater accuracy. The use of a decaying rate of mutation is also found to be beneficial in the correct mining of simple processe.
Purpose - This paper seeks to examine the area of business process mining, providing an overview of state-of-the-art techniques. An outline of the main problems experienced in the practice of process mining is given along with reference to work that addresses the most challenging issues experienced in this field. This paper also aims to examine the application of soft computing techniques to process-mining problems. Design/methodology/approach - This paper is based on a comprehensive review of literature covering more than 50 research papers. These papers are analysed to identify current trends and future research directions in the field. Findings - Process-mining techniques are now becoming available as graphical interface-driven software tools, where flow diagram representations of processes may be manipulated as part of the mining task. A significant number of papers employ mining heuristics to aid in the task of process discovery. Soft computing algorithms are increasingly being investigated to aid the accuracy and speed of mining algorithms. Many papers exist that address common mining problems such as noise and mining loops. However, problems such as duplicate tasks, mining perspectives and delta analysis require further research. Originality/value - The contribution of this paper is to provide a summary of the current trends in process-mining practice and point out future research directions. A review of the work in this new and expanding area has been provided in the form of illustrative graphs and tables that identify the trends in this area. This is the most comprehensive and up-to-date review of business process-mining literature.
There is a growing recognition in industry and research that in order to realise their sustainability ambitions and leverage new enabling technologies, organisations have to innovate not only products or services but the entire business model. This is also the case within the emerging context of re-distributed manufacturing (RdM), where there is an organisational need to configure viable future RdM business models based on data-driven experimentation. We reviewed the literature and synthesised a conceptual framework for sustainable re-distributed manufacturing business models, based on data-driven decision making. In a next step, we will review both system dynamics and agent-based models to identify variables and interrelations between the variables that will help us to model sustainable RdM business models necessary to implement and test the framework within industry.
This paper experiments with the use of feedback loops in a genetic business process mining algorithm. The use of genetic algorithms for process mining is explained along with a description of the research background to process mining. Of particular interest in this paper is the crossover operator. Experiments are described where problems encountered in mining processes are fed back into the crossover operator and used in the selection of crossover points. Both roulette wheel and tournament methods are used in the process of selecting crossover points. The paper concludes that the use of such problem feedback loops can be beneficial in the mining of simple business processes. However the paper makes clear that feedback loops are best employed as part of an 'intelligent' mining technique.
There is an increasing need to eliminate wasted time and money during factory layout design and subsequent construction. It is presently difficult for engineers to foresee if a certain layout is optimal for work and material flows. By exploiting modelling, simulation and visualisation techniques, this paper presents a tool concept called immersive WITNESS that combines the modelling strengths of Discrete Event Simulation (DES) with the 3D visualisation strengths of recent 3D low cost gaming technology to enable decision makers make informed design choices for future factories layouts. The tool enables engineers to receive immediate feedback on their design choices. Our results show that this tool has the potential to reduce rework as well as the associated costs of making physical prototypes. (C) 2015 The Authors. Published by Elsevier B.V.
This paper proposes an approach for the optimisation of web business processes using multi-objective evolutionary computing. Business process optimisation is considered as the problem of constructing feasible business process designs with optimum attribute values such as duration and cost. This optimisation framework involves the application of a series of Evolutionary Multi-objective Optimisation Algorithms (EMOAs) in an attempt to generate a series of diverse optimised business process designs for given requirements. The optimisation framework is tested to validate the framework's capability in capturing, composing and optimising business process designs constituted of web services. The results from the web business process optimisation scenario, featured in this paper, demonstrate that the framework can identify business process designs with optimised attribute values.
The theme of Redistributed Manufacturing (RdM) has gained in interest over recent years. While much research has taken place into the effects of RdM on current manufacturing models very few people have proposed new business models for this concept. The RdM studio is a new approach to business model development that will allow future users to dynamically incorporate data and experiment with new redistributed manufacturing scenarios. An RdM System Dynamics (SD) model is illustrated (as a potential constituent model of the RdM studio) with a case study called ShoeLab that explores RdM scenario generation through parameter sets utilising the SD modelling method. This research provides a valuable platform on which future models and scenarios may be derived.
Increasing market saturation has led companies to try and identify those customers at highest risk of churning. The practice of customer churn prediction addresses this need. This paper details a novel approach and framework for customer churn prediction utilising a Neural Network (NN) approach. The methodology for customer churn prediction describes a predictive approach for the identification of customers who are most likely to churn in the future. This is a departure from current research into customer churn which tries to predict which customers are most likely to instantaneously churn. A real life case study from industry is presented here to illustrate this approach in practice. Future research will include the enhancement of this approach for more accurate modelling of collective systems.
The catchment area along a bus route is key in predicting bus journeys. In particular, the aggregated number of households within the catchment area are used in the prediction model. The model uses other factors, such as head-way, day-of-week and others. The focus of this study was to classify types of catchment areas and analyse the impact of varying their sizes on the quality of predicting the number of bus passengers. Machine Learning techniques: Random Forest, Neural Networks and C5.0 Decision Trees, were compared regarding solution quality of predictions. The study discusses the sensitivity of catchment area size variations. Bus routes in the county Surrey in the United Kingdom were used to test the quality of the methods. The findings show that the quality of predicting bus journeys depends on the size of the catchment area.
This paper proposes a framework for the facilitation of organisational capability for outsourcing innovation, enabling firms to take advantage of its many benefits (e.g., reduced costs, increased flexibility, access to better expertise and increased business focus), whilst mitigating its risks. In this framework a generic holistic model is developed to aid firms to successfully outsource innovation. The model is realised in two stages using a qualitative theory-building research design. The initial stage develops a preliminary model which is subsequently validated and refined during the second stage. The propositions which form the preliminary model are deductively explored to identify whether they also exist in a second data set. A semi-structured interview survey is executed with the aid of a rich picture survey instrument to gather data for this purpose. The model developed by this study describes innovation outsourcing as an open system of interrelated activities that takes established company strategy (in terms of people, organisational structures, environment, and technology), and transforms it into improved firm performance through innovation. The model achieves this through a three-stage process which enables the alignment of capability to outsourced innovation activity, and makes actual performance outcomes, rather than expected benefits, the focus of innovation outsourcing aims.
This paper presents the current state of microfluidic design from a practitioner's perspective. The capture of microfluidic design practice was facilitated through a combination of industry survey and expert interviews, allowing the authors to draw out models for microfluidic design. Exploration of the current practice of microfluidic design showed that formal design methodologies were not in use. This research has also found that sub-section interactions have been addressed in an inadequate fashion by current design practices. The work presented in this paper outlines the scope for further research in the development of a formal design methodology for microfluidics.
The emergence of new technologies such as the Internet of Things, big data, and advanced robotics, together with risks such as climate change, rising labour costs, and a fluctuating economy, are challenging the current UK manufacturing model. In this paper, business models for re-distributed manufacture (RdM) are developed using anIDEF (Icam DEFinition for Function Modelling) description to serve as a guide for the implementation of the RdM concept in the consumer goods industry. This paper explores the viability of a re-distributed business model for manufacturers employing new manufacturing technologies such as additive manufacturing or three-dimensional (3D) printing, as part of a sustainable and circular production and consumption system. An As-Is value chain model is presented alongside the proposed new business model for a sustainable re-distributed manufacturing system. Both are illustrated via a case study drawn from the shoe manufacturing industry. The case study shows that there is a need for robust facilities in close proximity to the customer. These facilities are store fronts which can also manufacture, remanufacture, and provide services. The reduction in transportation and increase in customer involvement throughout the process are the main benefits that would accrue if a re-distributed model is implemented in the given industry.
In this paper we introduce a research agenda to guide the development of the next generation of Discrete Event Simulation (DES) systems. Interfaces to digital twins are projected to go beyond physical representations to become blueprints for the actual “objects” and an active dashboard for their control. The role and importance of real-time interactive animations presented in an Extended Reality (XR) format will be explored. The need for using game engines, particularly their physics engines and AI within interactive simulated Extended Reality is expanded on. Importing and scanning real-world environments is assumed to become more efficient when using AR. Exporting to VR and AR is recommended to be a default feature. A technology framework for the next generation simulators is presented along with a proposed set of implementation guidelines. The need for more human centric technology approaches, nascent in Industry 4.0, are now central to the emerging Industry 5.0 paradigm; an agenda that is discussed in this research as part of a human in the loop future, supported by DES. The potential role of Explainable Artificial Intelligence is also explored along with an audit trail approach to provide a justification of complex and automated decision-making systems with relation to DES. A technology framework is proposed, which brings the above together and can serve as a guide for the next generation of holistic simulators for manufacturing.
Additional publications
Utilizing Industry 4.0 on the Construction Site: Challenges and opportunities