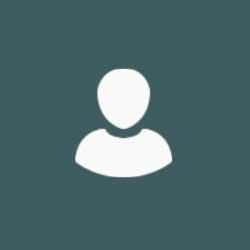
Dr Craig Pitcher
Academic and research departments
Publications
As we explore our solar system and other extraterrestrial bodies, the subsurface plays a vital role in allowing us to peer back into the history of a particular body, looking for life or signs that it may have been habitable. This can be achieved by using a form of drill or penetrator, although traditional technologies require large masses to produce an overhead force (OHF) that pushes the drill into the subsurface. Dual reciprocating drilling (DRD) is a new biologically inspired technology based on the wood wasp ovipositor. It consists of two reciprocating backward-facing teethed halves that generate a drilling force that reduces the required overhead penetration force and mass requirements. The Surrey Space Centre (SSC) has overseen the design, development, and testing of a proof-of-concept model with funding from European Space Agency. The system is now evolving to include a drive mechanism within the drill head and bays for scientific instrumentation.
The Powdered Sample Dosing and Distribution System (PSDDS) of the ExoMars rover will be required to handle and contain samples of Mars regolith for long periods of time. Cementation of the regolith, caused by water and salts in the soil, results in clumpy material and a duricrust layer forming on the surface. It is therefore possible that material residing in the sampling system may cement, and could potentially hinder its operation. There has yet to be an investigation into the formation of duricrusts under simulated Martian conditions, or how this may affect the performance of sample handling mechanisms. Therefore experiments have been performed to create a duricrust and to explore the cementation of Mars analogues, before performing a series of tests on a qualification model of the PSDDS under simulated Martian conditions.It was possible to create a consolidated crust of cemented material several millimetres deep, with the material below remaining powder-like. It was seen that due to the very low permeability of the Montmorillonite component material, diffusion of water through the material was quickly blocked, resulting in a sample with an inhomogeneous water content. Additionally, samples with a water mass content of 10% or higher would cement into a single solid piece. Finally, tests with the PSDDS revealed that samples with a water mass content of just 5% created small clumps with significant internal cohesion, blocking the sample funnels and preventing transportation of the material. These experiments have highlighted that the cementation of regolith in Martian conditions must be taken into consideration in the design of sample handling instruments.
© 2015 COSPAR. The dual-reciprocating drill (DRD) is a biologically-inspired concept which has shown promise in planetary environments, requiring a lower overhead force than traditional rotary drilling techniques. By using two reciprocating backwards-facing teethed halves to grip the surrounding substrate, it generates a traction force that reduces the required overhead penetration force. Research into DRD has focused on the effects of operational and substrate parameters on performance compared to static penetration, with minimal study of the geometrical parameters which define the drill head. This paper presents the exploration of the effects of drill head design on drilling depth and power consumption. Sixteen variations of the original design were tested in planetary regolith simulants up to depths of 800. mm. The experiments showed relationships between final depth, total drill radius and cone shape, though the teeth design had a negligible effect on performance. These results can be used alongside the previous research to optimise the future design and operation of the DRD. Drill stem bending was seen to cause an increase in drilling speed and depth, leading to the exploration of the mechanics of diagonal drilling. This resulted in the proposal of a fully-integrated system prototype that incorporates both reciprocating and lateral motion mechanisms.
There is evidence that water-ice exists on a number of bodies in the solar system. As ice deposits may contain biomarkers that indicate the presence of life, or can be used as a consumable resource for future missions, confirming these observations with in-situ measurements is of great interest. Missions aiming to do this must consider how the presence of water-ice in regolith affects both the regolith’s properties and the performance of the instruments that interact with it. The properties of icy lunar and Martian regolith simulants in preparation for currently planned missions are examined in this chapter. These results can be used in future instrumentation testing and missions designed to explore other icy bodies in the solar system. The testing of icy lunar regolith simulants is summarised, before focusing on experiments demonstrating the change in properties of frozen NU-LHT-2M, a simulant of the highlands regolith found at the lunar poles, as water is added. Further tests showed a critical point of 5 ± 1% water mass content where the penetration resistance significantly increases. The addition of water to Martian regolith simulants was also examined, with the presence of salts resulting in the formation of cemented crusts under simulated Martian conditions. Additional tests with the ExoMars PSDDS demonstrated how increased internal cohesion caused by the water resulted in the failure of the instrument.
Improving the efficiency of a subsurface sample acquisition process provides operational benefits such as reduced bit wear and power consumption, and may increase the sample fidelity by minimising alterations caused by the drilling operation to the surrounding substrate. This could be achieved by acquiring multiple samples during a single drilling procedure. Although some recent planetary drills have incorporated a hybrid cored and cuttings sampling technique, there are currently no systems that have been designed to obtain and separately store multiple comparable samples. The Internal Actuation Mechanism, developed as part of the latest generation of the Dual-Reciprocating Drill, will incorporate a rotating shutter mechanism capable of acquiring up to four samples. In the first demonstration of the fully-integrated prototype using layers of differently-coloured sand, the shutter mechanism was shown to be able to take multiple samples in a single drilling operation. These experiments also confirmed the observations of numerical simulations, which showed that the drill’s teethed design results in regolith from the surface layer being dragged down with the descending drill and collected by the sampling system. By optimising the geometrical design to increase sample value and refining the shutter mechanism to improve reliability, a multi-sample acquisition system for planetary subsurface exploration could become a viable technology. •The IAM is a fully-integrated DRD prototype with an integrated sampling mechanism.•A rotating shutter system allows samples to be collected in separate compartments.•Numerical simulations explored the drill behaviour and tool-soil interactions.•IAM drilling and multi-sampling in one operation were successfully demonstrated.•Surface regolith is dragged down by the drill head geometry as it descends.
The dual-reciprocating drill (DRD) is a biologically-inspired low-mass alternative to traditional drilling techniques, using backwards-facing teethed halves to grip the surrounding substrate, generating a traction force that reduces the required overhead penetration force. Previous experiments using a proof-of-concept test bench have provided evidence as to the significant role of sideways movements and lateral forces in improving drilling performance. The system is also progressing to a first system prototype concept, in which an actuation mechanism is integrated within the drill heads. To experimentally determine the effect of lateral motions, a new internal actuation mechanism was developed to allow the inclusion of controlled sideways movements, resulting in the creation of the circular and diagonal burrowing motions. This paper presents an investigation into the performance of the reciprocation and burrowing motions by testing them in a planetary regolith simulant. Analysis of force sensor measurements has shown a relationship between the penetration and traction forces and the internal friction of the mechanism and depth achieved. These tests have also experimentally demonstrated the benefit of lateral motions in drilling performance, with both the burrowing mechanisms and drilling tests performed at an angle able to penetrate further than traditional vertical reciprocation, leading to the proposition of new burrowing and diagonal drilling mechanics. From this, a new fully integrated system prototype can be developed which incorporates lateral motions that can optimise the drilling performance.
The dual-reciprocating drill (DRD) is a low-mass alternative to traditional drilling techniques biologically inspired by the wood wasp ovipositor, which is used to drill into wood in order to lay its eggs. The DRD reciprocates two halves lined with backwards-facing teeth, enabling it to generate traction forces that reduce the required overhead penetration force. While previous research has focused on experimental testing of the drill's operational and design parameters, numerical simulation techniques are being developed to allow the rapid testing of multiple designs, complementing and informing experimental testing campaigns. The latest DRD design iteration integrated a novel internal actuation mechanism and demonstrated the benefits of adding controlled lateral movements. This paper presents an exploration of how bit morphology affects drilling performance and a preliminary study of discrete element method (DEM) simulations for modelling DRD interactions in regolith. These have shown how regolith grain size and microscopic behaviour significantly affects the performance of different drill designs, and demonstrated how customisable drills can exploit the properties of various substrates. Two system prototypes are also being developed for the DRD's third generation, each utilising novel actuation and sampling mechanisms. A final drill design will then be deployed from a planetary rover and perform the first DRD drilling and sampling operation.
As icy regolith is believed to exist in the subsurface of permanently shadowed areas near the lunar south pole, there is a growing interest in obtaining samples from these polar regions. To qualify for spaceflight, sampling instruments must demonstrate their ability to operate in the expected environment. However, there is currently no quantitative data detailing the extent and distribution of ice in polar regolith. While work has been done to determine the effects of water ice content in simulants such as JSC-1A, to date there has been no investigation into the properties of icy simulants of the regolith believed to be found at lunar polar regions. A series of experiments has therefore been conducted to determine the properties of icy NU-LHT-2M lunar highland simulant, an approximation of lunar polar regolith, at varying degrees of saturation. A number of procedures for preparing the simulant were tested, with the aim of defining a standardised technique for the creation of icy simulants with controlled water contents. Saturation of the highland simulant was found to occur at a water mass content between 13% and 17%, while cone penetration tests demonstrated that a significant increase in penetration resistance occurs at 5 ± 1%. Uniaxial compression tests showed an increase in regolith strength with water mass and density, which slows down as the saturation level is reached. The results presented here demonstrate the first characterisation of the properties of icy lunar polar regolith simulants, which can be expanded upon to further the understanding of its properties for use in future instrumentation testing.
Two laboratory test series were performed with the aim of ensuring the proper functionality of the key sampling mechanisms installed aboard the Mars rover ExoMars, currently scheduled for launch in 2020 by the European Space Agency ESA. In order to facilitate the chemical analysis of the Martian ground accessible to the ExoMars drill, the retrieved drill cores must first be milled. This task is performed by a crushing station (CS), which delivers the milled product to a dosing device (PSDDS). From there the material is distributed further to the various analysis instruments mounted on the rover. The first test series was performed with a mock-up of crushing station and dosing device under simulated Martian pressure and temperature conditions. As a worst-case scenario, crushing of frozen soil mixtures was performed and the milling products were collected in the dosing station before being further distributed. In the second test series, granular analogue materials equivalent to the milled products obtained in previous tests were stored for periods of several days in the input funnel of the dosing device. The set-up included a regulation valve through which water vapour was streamed into the vacuum chamber to create a water vapour-saturated atmosphere. The purpose of this series of tests was to investigate if the presence of water can cause cementation of the samples, and how this subsequently affects the operation of the crushing and distribution devices. Our results indicate that the milling device works very well with the current design both for loose and for hard block-like materials, e.g., chunks of frozen soil. It was also found that milled material, when subjected to a water-saturated atmosphere, does not experience any cementation.
The International Space Exploration Coordination Group (ISECG) identifies one of the first exploration steps as in situ investigations of moon or asteroids. Europe is developing payload concepts for drilling and sample analysis, a contribution to a 250kg rover as well as for sample return. To achieve these missions, ESA depends on international partnerships. Such important missions will be seldom, expensive and the drill/sample site selected will be based on observations from orbit not calibrated with ground truth data. Many of the international science communitys objectives can be met at lower cost, or the chances of mission success improved and the quality of the science increased by making use of an innovative, low mass, mobile robotic payload following the Lunar Exploration Analysis Group (LEAG) recommendations. The LUnar Volatiles Mobile Instrumentation (LUVMI) provides a smart, low mass, innovative, modular mobile payload comprising surface and subsurface sensing with an in-situ sampling technology capable of depth-resolved extraction of volatiles, combined with a volatiles analyser (mass spectrometer) capable of identifying the chemical composition of the most important volatiles. This will allow LUVMI to: traverse the lunar surface prospecting for volatiles; sample subsurface up to a depth of 10 cm (with a goal of 20 cm); extract water and other loosely bound volatiles; identify the chemical species extracted; access and sample permanently shadowed regions (PSR). These payload characteristics of LUVMI will permit to maximize sample transfer efficiency and minimize sample handling as well its attendant mass requirements and risk of sample alterations. By building on national, EC and ESA funded research and developments, this project will develop to TRL6 instruments that together form a smart modular mobile payload that could be flight ready in 2020. The LUVMI sampling instrument will be tested in a highly representative environment including thermal, vacuum and regolith simulant and the integrated payload demonstrated in a representative environment.
The International Space Exploration Coordination Group (ISECG) identifies one of the first exploration steps as in situ investigations of the Moon or asteroids. Europe is developing payload concepts for drilling and sample analysis, a contribution to a 250kg rover as well as for sample return. To achieve these missions, ESA depends on international partnerships. Such missions will be seldom, expensive and the drill/sample site selected will be based on observations from orbit not calibrated with ground truth data. Many of the international science community’s objectives can be met at lower cost, or the chances of mission success improved and the quality of the science increased by making use of an innovative, low mass, mobile robotic payload following the LEAG recommendations. As a main objective LUVMI is designed specifically for operations at the South Pole of the Moon with a payload accommodated by a novel lightweight mobile platform (rover) with a range of several kilometers. Over the 2 years duration of the project, the scientific instruments payload will be developed and validated up to TRL 6. LUVMI targets being ready for flight in 2020 on an ESA mission partially supported by private funding.