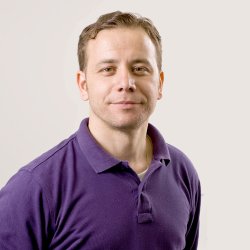
Dario Amirante
Publications
Flow and heat transfer in an aero-engine compressor disk cavity with radial inflow has been studied using computational fluid dynamics (CFD), large eddy simulation (LES), and coupled fluid/ solid modeling. Standalone CFD investigations were conducted using a set of popular turbulence models along with 0.2 deg axisymmetric and a 22.5 deg discrete sector CFD models. The overall agreement between the CFD predictions is good, and solutions are comparable to an established integral method solution in the major part of the cavity. The LES simulation demonstrates that flow unsteadiness in the cavity due to the unstable thermal stratification is largely suppressed by the radial inflow. Steady flow CFD modeling using the axisymmetric sector model and the Spalart-Allmaras turbulence model was coupled with a finite element (FE) thermal model of the rotating cavity. Good agreement was obtained between the coupled solution and rig test data in terms of metal temperature. Analysis confirms that using a small radial bleed flow in compressor cavities is effective in reducing thermal response times for the compressor disks and that this could be applied in management of compressor blade clearance.
Large and flexible wind turbine blades may be susceptible to severe blade deformations coupled with dynamic stall. To advance prediction capability for this problem a general deforming mesh computational fluid dynamics (CFD) method has been developed for calculating flows with moving or deforming boundaries using an elastic spring analogy. The method has been evaluated against experimental data for flow around a pitching NACA0012 airfoil in the deep dynamic stall regime where flow is highly separated, and compared with other authors0 CFD simulations for pitching airfoil. The effects of varying the reduced frequency are also investigated. During the upstroke the present results are in generally good agreement with experiment and other CFD studies. During the downstroke some differences with experiment and other CFD models are apparent. This may be due to the sensitivity of the separated flow to modelling assumptions and experimental conditions. Overall, the degree of agreement between CFD and experiment is considered encouraging.
Accurate prediction of metal temperatures, blade tip and seal clearances in high pressure compressor and turbine air systems leads to dramatic improvements in overall aero-engine efficiency and component life. Fast transients during an engine flight profile may introduce large changes in geometry between adjacent rotor and stator components. The changing dynamics in a few critical seals and interfaces can change the dynamics of the entire engine, compromising efficiency, integrity and long service life. In this paper we present results of a coupled aero-thermo-mechanical transient simulation of a high pressure turbine assembly throughout an engine flight cycle. The fluid and solid model geometry is approximated as 2D axisymmetric. The problem, formulated as a four field coupled multiphysics system of equations, is simplified using a quasi-steady state assumption: the transient thermal solid problem is coupled to a sequence of steady fluid problems and static structural problems. The predicted results compare well with the experimental measurements over the entire fluid-solid interface. We show improvement in transient predictions isolating the effects of the solid domain deformation. The remaining transient error is linked to temporal uncertainties in the fluid model inlet boundary conditions which were taken as a spatial average of the main annulus flow conditions.
The paper presents a multi-disciplinary approach for aero-thermal and heat transfer analysis for internal flows. The versatility and potential benefit offered by the approach is described through the application to a realistic low pressure turbine assembly. The computational method is based on a run time code-coupling architecture that allows mixed models and simulations to be integrated together for the prediction of the sub-system aero-thermal performance. In this specific application the model is consisting of two rotor blades, the embedded vanes, the inter-stage cavity and the solid parts. The geometry represents a real engine situation. The key element of the approach is the use of a fully modular coupling strategy that aims to combine (1) flexibility for design needs, (2) variable level of modelling for better accuracy and (3) in memory code coupling for preserving computational efficiency in large system and sub-system simulations. For this particular example Reynolds Averaged Navier-Stokes (RANS) equations are solved for the fluid regions and thermal coupling is enforced with the metal (conjugate heat transfer). Fluid-fluid interfaces use mixing planes between the rotating parts while overlapping regions are exploited to link the cavity flow to the main annulus flow as well as in the cavity itself for mapping of the metal parts and leakages. Metal temperatures predicted by the simulation are compared to those retrieved from a thermal model of the engine, and the results are discussed with reference to the underlying flow physics.
This paper presents WMLES simulations of a chute type turbine rim seal. Configurations with an axisymmetric annulus flow and with nozzle guide vanes fitted (but without rotor blades) are considered. The passive scalar concentration solution and WMLES are validated against available data in the literature for uniform convection and a rotor-stator cavity flow. The WMLES approach is shown to be effective, giving significant improvements over an eddy viscosity turbulence model, in prediction of rim seal effectiveness compared to research rig measurements. WMLES requires considerably less computational time than wall-resolved LES, and has the potential for extension to engine conditions. All WMLES solutions show rotating inertial waves in the chute seal. Good agreement between WMLES and measurements for sealing effectiveness in the configuration without vanes is found. For cases with vanes fitted the WMLES simulation shows less ingestion than the measurements, and possible reasons are discussed.
This paper describes Large-Eddy Simulations (LES) of the flow in a rotating cavity with narrow inter-disc spacing and a radial inflow introduced from the shroud. Simulations have been conducted using a compressible, unstructured, finite-volume solver, and testing different subgrid scale models. These include the standard Smagorinsky model with Van Driest damping function near the wall, the WALE model and the implicit LES procedure. Reynolds averaged Navier-Stokes (RANS) results, based on the Spalart-Allmaras and SST k − ω models, are also presented. LES solutions reveal a turbulent source region, a laminar oscillating core with almost zero axial and radial velocity and turbulent Ekman type boundary layers along the discs. Validations are carried out against the experimental data available from the study of Firouzian et al. [1]. It is shown that the tangential velocity and the pressure drop across the cavity are very well predicted by both RANS and LES, although significant differences are observed in the velocity profiles within the boundary layers.
This paper presents wall-modeled large-eddy simulations (WMLES) simulations of a chute type turbine rim seal. Configurations with an axisymmetric annulus flow and with nozzle guide vanes fitted (but without rotor blades) are considered. The passive scalar concentration solution and WMLES are validated against available data in the literature for uniform convection and a rotor-stator cavity flow. The WMLES approach is shown to be effective, giving significant improvements over an eddy viscosity turbulence model, in prediction of rim seal effectiveness compared to research rig measurements. WMLES requires considerably less computational time than wall-resolved LES, and has the potential for extension to engine conditions. All WMLES solutions show rotating inertial waves in the chute seal. Good agreement between WMLES and measurements for sealing effectiveness in the configuration without vanes is found. For cases with vanes fitted the WMLES simulation shows less ingestion than the measurements, and possible reasons are discussed.
Unsteady flow phenomena unrelated to the main gas-path blading have been identified in a number of turbine rim seal investigations. This unsteadiness has significant influence on the sealing effectiveness predicted by the conventional steady RANS (Reynolds-averaged Navier–Stokes) method, thus it is important for turbine stage design and optimisation. This paper presents CFD (computational fluid dynamics) modelling of a chute type rim seal that has been previously experimentally investigated. The study focuses on inherent large-scale unsteadiness rather than that imposed by vanes and blades or external flow. A large-eddy simulation (LES) solver is validated for a pipe flow test case and then applied to the chute rim seal rotor/stator cavity. LES, RANS and unsteady RANS (URANS) models all showed reasonable agreement with steady measurements within the disc cavity, but only the LES shows unsteadiness at a similar distinct peak frequency to that found in the experiment, at 23 times the rotational frequency. The boundary layer profile within the chute rim seal clearance has been scrutinised, which may explain the improvement of LES over RANS predictions for the pressure drop across the seal. LES results show a clockwise mean flow vortex. A more detailed sketch of the rim sealing flow unsteady flow structures is established with the help of the LES results. However, there are some significant differences between unsteadiness predicted and the measurements, and possible causes of these are discussed.
The paper describes a Large Eddy Simulation (LES) conducted for a non adiabatic rotating cavity with a radial inflow introduced from the shroud. The dimensionless mass flow rate of the radial inflow is Cw = 3500 and the rotational Reynolds number, based on the cavity outer radius, is equal to Reθ = 1.2 x 10⁶. The time averaged local Nusselt number on the heated wall is compared with the experimental data available from the literature, and with those derived from the solution of two Unsteady Reynolds Averaged Navier-Stokes (URANS) eddy viscosity models, namely the Spalart-Allmaras and the k - ω SST model. It is shown that the Nusselt number is under-predicted in the lower part of the disc and over-predicted in the outer region by both URANS models, whereas the LES provides a much better agreement with the measurements. The behaviour results primarily from a different flow structure in the source region, which, in the LES, is found to be considerably more extended and show localized buoyancy phenomena that the URANS models investigated do not capture.
As the complexity of multi-physics simulations increases, there is a need for efficient flow of information between components. Discrete 'coupler' codes can abstract away this process, improving solver interoperability. One such multi-physics problem is modelling the high pressure compressor of turbofan engines, where instances of rotor/stator CFD simulations are coupled. Configuring couplers and allocating resources correctly can be challenging for such problems due to the sliding interfaces between codes. In this research, we present CPX, a mini-coupler designed to model the performance behaviour of a production coupler framework at Rolls-Royce plc., used for coupling rotor/stator simulations. CPX, the first mini-coupler framework of its kind, is combined with a CFD mini-app to predict the run-time and scaling behaviour of large scale coupled CFD simulations. We demonstrate high qualitative and quantitative predictive accuracy with a less than 17 % mean error. A performance model is developed to predict the 'optimum' configuration of resources, and is tested to show the high accuracy of these predictions. The model is also used to project the 'optimum' configuration for a 6 Billion cell test case, a problem size representative of current leading-edge production workloads, on a 100,000 core cluster and a 400 GPU cluster. Further testing reveals that the 'optimum' configuration is unstable if not set up correctly, and therefore a trade-off needs to be made with a marginally less-than-optimal setup to ensure stability. The work illustrates the significant utility of CPX to carry out such rapid design space and run-time setup exploration studies to obtain the best performance from production CFD coupled simulations.
We present the large-scale, computational fluid dynamics (CFD) simulation of a full gas-turbine engine compressor, demonstrating capability towards overcoming current limitations for virtual certification of aero-engine design. The simulation is carried out through a performance portable code-base on multi-core/many-core HPC clusters with a CFD-to-CFD coupled execution, combining an industrial CFD solver linked using custom coupler software. The application innovates in its design for performance portability through the OP2 domain specific library for the CFD components, allowing the automatic generation of highly optimized platform-specific parallelizations for both multi-core (CPU) and many-core (GPU) clusters from a single high-level source. The code is used for the simulation of a 4.58B node, full-annulus 10-row production-grade test compressor (DLR's Rig250), using a coupled sliding-plane setup on the ARCHER2 and Cirrus supercomputers at EPCC. The OP2 generated multiple parallelizations, together with optimized coupler configurations on heterogeneous/hybrid settings achieve, for the first time, execution of 1 revolution in less than 6 hours on 512 nodes of ARCHER2 (65k cores), with a parallel scaling efficiency of over 80% compared to a 107 node run. Results indicate a speed up of the CFD suite by an order of a magnitude (approximate to 30x) relative to current production capability. Benchmarking and performance modelling project a time-to-solution of less than 5 hours on a cluster of 488xNVIDIA V100 GPUs, about 3x-4x speedup over CPU clusters. The work demonstrates a step-change towards achieving virtual certification of aircraft engines with the requisite fidelity and tractable time-to-solution that was previously out of reach under production settings.
The paper presents a multidisciplinary approach for aero-thermal and heat transfer analysis for internal flows. The versatility and potential benefit offered by the approach are described through the application to a realistic low pressure turbine assembly. The computational method is based on a run time code-coupling architecture that allows mixed models and simulations to be integrated together for the prediction of the subsystem aero-thermal performance. In this specific application, the model is consisting of two rotor blades, the embedded vanes, the interstage cavity, and the solid parts. The geometry represents a real engine situation. The key element of the approach is the use of a fully modular coupling strategy that aims to combine (1) flexibility for design needs, (2) variable level of modeling for better accuracy, and (3) in memory code coupling for preserving computational efficiency in large system and subsystem simulations. For this particular example, Reynolds averaged Navier-Stokes (RANS) equations are solved for the fluid regions and thermal coupling is enforced with the metal (conjugate heat transfer, CHT). Fluid-fluid interfaces use mixing planes between the rotating parts while overlapping regions are exploited to link the cavity flow to the main annulus flow as well as in the cavity itself for mapping of the metal parts and leakages. Metal temperatures predicted by the simulation are compared to those retrieved from a thermal model of the engine, and the results are discussed with reference to the underlying flow physics.
This paper presents wall-modeled large-eddy simulations (WMLES) of a chute-type turbine rim seal. Configurations with an axisymmetric annulus flow and with nozzle guide vanes fitted (but without rotor blades) are considered. The passive scalar concentration solution and WMLES are validated against available data in the literature for uniform convection and a rotor-stator cavity flow. The WMLES approach is shown to be effective, giving significant improvements over an eddy viscosity turbulence model, in prediction of rim seal effectiveness compared to research rig measurements. WMLES requires considerably less computational tune than wall-resolved LES, and has the potential for extension to engine conditions. All WMLES solutions show rotating inertial waves in the chute seal. Good agreement between WMLES and measurements for sealing effectiveness in the configuration without vanes is found. For cases with vanes fitted, the WMLES simulation shows less ingestion than the measurements, and possible reasons are discussed.
This paper describes a coupling framework for parallel execution of different solvers for multi-physics and multi-domain simulations with an arbitrary number of adjacent zones connected by different physical or overlapping interfaces. The coupling architecture is based on the execution of several instances of the same coupling code and relies on the use of smart edges (i.e., separate processes) dedicated to managing the exchange of information between two adjacent regions. The collection of solvers and coupling sessions forms a flexible and modular system, where the data exchange is handled by independent servers that are dedicated to a single interface connecting two solvers’ sessions. Accuracy and performance of the strategy is considered for turbomachinery applications involving Conjugate Heat Transfer (CHT) analysis and Sliding Plane (SP) interfaces.
The paper describes a Large Eddy Simulation (LES) conducted for a non adiabatic rotating cavity with a radial inflow introduced from the shroud. The dimensionless mass flow rate of the radial inflow is Cw = 3500 and the rotational Reynolds number, based on the cavity outer radius, is equal to Req =1:2 x 106. The time averaged local Nusselt number on the heated wall is compared with the experimental data available from the literature, and with those derived from the solution of two Unsteady Reynolds Averaged Navier-Stokes (URANS) eddy viscosity models, namely the Spalart-Allmaras and the k-w SST model. It is shown that the Nusselt number is underpredicted in the lower part of the disc and over-predicted in the outer region by both URANS models, whereas the LES provides a much better agreement with the measurements. The behaviour results primarily from a different flow structure in the source region, which, in the LES, is found to be considerably more extended and show localized buoyancy phenomena that the URANS models investigated do not capture.
Hot gas ingestion in a chute seal configuration has been numerically and experimentally investigated. First, the NGVs were included to generate a swirled annulus flow. This staged approach to rig configuration is used to understand the relative contribution of rotation and NGVs induced pressure asymmetries in turbine rim sealing flow ingestion. Computations were performed with a URANS model and a novel LES code including near wall boundary layer modelling, the wall-modelled LES (WMLES). The experimental data was obtained in the Oxford Rotor Facility (ORF). The main focus of this study was the mean cavity flow aerodynamics and the sealing performance of the chute seal under a range of operating conditions. These are studied through measurements of pressure and gas concentration within the rotor-stator disc cavity and the rim seal which are compared to CFD predictions. In addition, experimental and CFD assessments of concentration-based sealing effectiveness in the gas path for the vaned configuration are presented. Measurements were taken at a representative rotor leading edge axial position to focus on the radial diffusion and interaction between the purge flow and annulus flow. Overall the WMLES code better captured the interaction between main annulus and turbine cavity flow positioning it as a powerful tool with potential to be implemented in the design and verification process.
Reynolds-Averaged Navier-Stokes (RANS) computations have been conducted to investigate the flow and heat trans-fer between two co-rotating discs with an axial throughflow of cooling air and a radial bleed introduced from the shroud. The computational fluid dynamics (CFD) models have been cou-pled with a thermal model of the test rig, and the predicted metal temperature compared with the thermocouple data. CFD solutions are shown to vary from a buoyancy driven regime to a forced convection regime, depending on the radial inflow rate prescribed at the shroud. At a high radial inflow rate, the computations show an excellent agreement with the measured temperatures through a transient rig condition. At a low radial inflow rate, the cavity flow is destabilized by the thermal stratification. Good qualitative agreement with the measurements is shown, although a significant over-prediction of disc temperatures is observed. This is associated with under prediction of the penetration of the axial throughflow into the cavity. The mismatch could be the result of strong sensitivity to the prescribed inlet conditions, in addition to possible shortcomings in the turbulence modeling.
This paper describes the development of a mesh deformation method used for aero-thermo-mechanical coupling of turbo-engine components. The method is based on the nonlinear solution of an elastic medium analogy, solved using finite element discretisation and modified to let the boundary nodes be free to slide over the deflected surfaces. This sliding technique relies on a B-spline reconstruction of the moving boundary and increases the robustness of the method in situations where the boundary deflection field presents significant gradients or large relative motion between two distinct boundaries. The performance of the method is illustrated with the application to an interstage cavity of a turbine assembly, subjected to the deformations computed by a coupled thermo-mechanical analysis of the engine component.
The optimization of heat transfer between fluid and metal plays a crucial role in gas turbine design. An accurate prediction of temperature for each metal component can help to minimize the coolant flow requirement, with a direct reduction of the corresponding loss in the thermodynamic cycle. Traditionally, in industry fluid and solid simulations are conducted separately. The prediction of metal stresses and temperatures, generally based on finite element analysis, requires the definition of a thermal model whose reliability is largely dependent on the validity of the boundary conditions prescribed on the solid surface. These boundary conditions are obtained from empirical correlations expressing local conditions as a function of working parameters of the entire system, with validation being supplied by engine testing. However, recent studies have demonstrated the benefits of employing coupling techniques, whereby computational fluid dynamics (CFD) is used to predict the heat flux from the air to the metal, and this is coupled to the thermal analysis predicting metal temperatures. This paper describes an extension of this coupling process, accounting for the thermo-mechanical distortion of the metal through the engine cycle. Two distinct codes, a finite element analysis (FEA) solver for thermo-mechanical analysis and a finite volume solver for CFD, are iteratively coupled to produce temperatures and deformations of the solid part through an engine cycle. At each time step, the CFD mesh is automatically adapted to the FEA prediction of the metal position using efficient spring analogy methods, ensuring the continuity of the coupled process. As an example of this methodology, the cavity flow in a turbine stator well is investigated. In this test case, there is a strong link between the thermo-mechanical distortion, governing the labyrinth seal clearance, and the amount of flow through the stator well, which determines the resulting heat transfer in the stator well. This feedback loop can only be resolved by including the thermo-mechanical distortion within the coupling process
This paper presents CFD (computational fluid dynamics) modelling of a chute type rim seal that has been previously experimentally investigated. The study focuses on inherent large-scale unsteadiness rather than that imposed by vanes and blades or external flow. A large-eddy simulation (LES) solver is validated for a pipe flow test case and then applied to the chute rim seal rotor/stator cavity. LES, Reynolds-averaged Navier-Stokes (RANS) and unsteady RANS (URANS) models all showed reasonable agreement with steady measurements within the disc cavity, but only the LES shows unsteadiness at a similar distinct peak frequency to that found in the experiment, at 23 times the rotational frequency. However, there are some significant differences between unsteadiness predicted and the measurements, and possible causes of these are discussed.
Flow and heat transfer in axial compressor disc cavities involve strong interaction of axial throughflow at the disc bores with centrifugal buoyant flow in the cavities. This paper presents large eddy simulation (LES) of flow and heat transfer in rotating cavities with a heated shroud and a relatively weak axial cooling throughflow. The conditions considered for a single cavity configuration correspond to Rossby numbers Ro=0.2 and 0.3, rotational Reynolds numbers Re Ω =3.2×10 5 and 7.7×10 5 , and buoyancy parameters βΔT=0.24 and 0.26. Reasonable agreement of the results with shroud heat transfer measurements was confirmed for the Ro=0.2 condition for which test data were available. A dual cavity configuration for Ro=0.3 and Re Ω =3.2×10 5 is also modelled. The simulations show that, at low Ro conditions, flow reversals occur along the length of the bore flow path, upstream and downstream of the rotating cavities. With the dual cavity strong, unsteady interactions between the flows in the two cavities occur. These flow interactions result in less stable flow structures, higher air temperatures within the cavities and lower shroud and disc heat transfer compared to the single cavity case. FFT analysis reveals a complex phase-locking mechanism between flows in the two cavities.