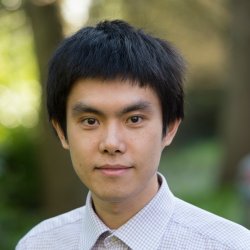
Dr Feng Gao
About
Biography
Feng Gao is research fellow in the Rolls-Royce UTC in thermo-fluid systems at the University of Surrey. Prior to his appointment in the University, he received his PhD degree in the Laboratoire de Mécanique des Fluides et d'Acoustique (LMFA), Ecole Centrale de Lyon, France. His research interest focuses on large-eddy simulation of complex flows in turbomachinery.
My qualifications
Publications
This paper addresses limitations of widely used Reynolds-averaged turbulence models (RANS) for prediction of gas turbine internal air systems. Results from direct numerical simulation (DNS), wall-resolved large-eddy simulation (LES), wall-modelled large-eddy simulation (WMLES), and RANS for benchmark test cases are compared. For rotor-stator disc cavity flows results for mean velocities, velocity fluctuations, rotor torque and laminar-turbulent transition are considered and compared with published data. For cavities between co-rotating discs attention is focused on buoyancy-driven convection in the centrifugal force field. It is concluded that WMLES is suitable for application in engine conditions, offering better accuracy than RANS in some critical applications. This confirms recently published results for turbine rim sealing and is further illustrated by application to convection in a sealed cavity at higher Rayleigh number than is practical with DNS or wall-resolved LES. The results show that the approximate near-wall treatment gives reasonable results for complex flows and extend previous studies to higher speed rig conditions where Eckert number effects become significant.
A systematic study of sealing performance for a chute style turbine rim seal using URANS methods is reported. This extends previous studies from a configuration without external flow in the main annulus to cases with a circumferentially uniform axial flow and vane generated swirling annulus flow (but without rotor blades). The study includes variation of the mean seal-to-rotor velocity ratio, main annulus-to-rotor velocity ratio, and seal clearance. The effects on the unsteady flow structures and the degree of main annulus flow ingestion into the rim seal cavity are examined. Sealing effectiveness is quantified by modeling a passive scalar, and the timescales for the convergence of this solution are considered. It has been found that intrinsic flow unsteadiness occurs in most cases, with the presence of vanes and external flow modifying, the associated flow structures and frequencies. Some sensitivities to the annulus flow conditions are identified. The circumferential pressure asymmetry generated by the vanes has a clear influence on the flow structure but does not lead to higher ingestion rates than the other conditions studied.
Closure models started from Chou’s work have been developed for more than 70 years, aiming at providing analytical tools to describe turbulent flows in the spectral space. In this study, a preliminary attempt is presented to introduce a closure model in the physical space, using the velocity structure functions as key parameters. The present closure model appears to qualitatively reproduce the asymptotic scaling behaviors at small and large scales, despite some inappropriate behaviors such as oscillations. Therefore, further improvements of the present model are expected to provide appropriate descriptions of turbulent flows in the physical space.
This paper presents a numerical investigation of buoyancy-driven flow in a closed rapidly rotating disc cavity. Pseudo two-dimensional models are considered, with periodic boundary conditions on a thin axial domain. An incompressible model, in which density variation is considered with the Boussinesq approximation, is evaluated through comparisons with a full compressible model. Effects of property (viscosity) variation and dependency on buoyancy parameter (ß∆T) and rotational Reynolds number for a given Rayleigh number, are investigated with the full compressible model. The mean centrifugal and radial Coriolis forces are analysed. Heat transfer predictions from the Boussinesq and compressible models agree to within 10%, for ß∆T ≤ 0.2.
An improved domain‐decoupled compact scheme for first and second spatial derivatives is proposed for domain‐decomposition‐based parallel computational fluid dynamics. The method improves the accuracy of previously developed decoupled schemes and preserves the accuracy and bandwidth properties of fully coupled compact schemes, even for a very large degree of parallelism, and enables the Navier‐Stokes equations to be solved independently on each processor. The scheme is analysed using Fourier analysis and error analysis, and tested on one‐dimensional wave‐packet propagation, a two‐dimensional vortex convection problem, and in the direct numerical simulation of the three‐dimensional Taylor‐Green vortex problem and turbulent channel flow. Our results demonstrate the scheme's effectiveness in performing direct numerical simulation of turbulence in terms of accuracy and scalability.
This paper presents WMLES simulations of a chute type turbine rim seal. Configurations with an axisymmetric annulus flow and with nozzle guide vanes fitted (but without rotor blades) are considered. The passive scalar concentration solution and WMLES are validated against available data in the literature for uniform convection and a rotor-stator cavity flow. The WMLES approach is shown to be effective, giving significant improvements over an eddy viscosity turbulence model, in prediction of rim seal effectiveness compared to research rig measurements. WMLES requires considerably less computational time than wall-resolved LES, and has the potential for extension to engine conditions. All WMLES solutions show rotating inertial waves in the chute seal. Good agreement between WMLES and measurements for sealing effectiveness in the configuration without vanes is found. For cases with vanes fitted the WMLES simulation shows less ingestion than the measurements, and possible reasons are discussed.
The generation of turbulent inflow conditions in large-eddy simulation (LES) is a key ingredient for general applications of LES in both academic turbulent flows and industrial designs with complicated engineering flows. This is because accurate predictions of the fluid behaviour are strongly dependent on the inflow conditions, particularly in turbulent flows at high turbulent Reynolds numbers. This paper aims at improving the vortex method (VM) of Sergent that demands long adaptive distances (12 times the half channel height, for a channel flow at Reτ = 395) to achieve high quality turbulence, and evaluating the equilibrium of the flow field obtained in terms of both the equilibrium of the mean flow and that of the turbulence (inter-scale turbulent energy transfer). The mean flow equilibrium is checked with classic criteria such as the friction velocity. In order to assess the equilibrium of turbulence, we propose using the velocity-derivative skewness, because it associates with the balance of energy transfer between large- and small-scale fluid motions. Numerical tests with the optimised set of model parameters reveal that the IVM is very efficient, in terms of adaptive distance, in generating high-quality synthetic turbulent fluctuations over a moderate distance: 6h for channel flow and 21δ for flat-plate boundary layer, with h and δ being respectively the half channel height and the nominal boundary layer thickness.
This paper presents buoyancy-induced flow for a sealed rotating cavity with rotational Rayleigh number Ra in the range 10⁷ to 10⁹. DNS for an incompressible model with the Boussinesq approximation is compared with LES for a compressible gas flow model. The compressible solver's solutions show the shroud Nusselt number scales with Ra0.286, in close agreement with the corrected experimental correlation and the Ra2/7 scaling for gravitational heat convection between horizontal plates, but differs from the N u ∝ Ra1/3 scaling given by the incompressible solver. The shroud thermal boundary layer thickness, based on the root mean square of the temperature fluctuation, can be estimated with λ* = 0:5N u-1 Velocities scale approximately with Ωa√β∆T. Disc laminar Ekman layer behaviour is confirmed up to Ra = 109. An Ekman layer scrubbing effect, associated with the viscous energy dissipation, is considered to be mainly responsible for the difference in N u between the two solvers at Ra = 109, in spite of rather small Eckert number. The analysis of the turbulent kinetic energy budget shows a dominant constant buoyancy production in the core. The use of the incompressible formulation for the considered problem is restricted by the applicable range of the Boussinesq approximation characterised by the buoyancy parameter β∆T and neglect of viscous heating and compressibility effects characterised by the Eckert number Ec = Ω2r2m =(Cp∆T).
This paper presents wall-modeled large-eddy simulations (WMLES) simulations of a chute type turbine rim seal. Configurations with an axisymmetric annulus flow and with nozzle guide vanes fitted (but without rotor blades) are considered. The passive scalar concentration solution and WMLES are validated against available data in the literature for uniform convection and a rotor-stator cavity flow. The WMLES approach is shown to be effective, giving significant improvements over an eddy viscosity turbulence model, in prediction of rim seal effectiveness compared to research rig measurements. WMLES requires considerably less computational time than wall-resolved LES, and has the potential for extension to engine conditions. All WMLES solutions show rotating inertial waves in the chute seal. Good agreement between WMLES and measurements for sealing effectiveness in the configuration without vanes is found. For cases with vanes fitted the WMLES simulation shows less ingestion than the measurements, and possible reasons are discussed.
Rotating fluids are well-known to be susceptible to waves. This has received much attention from the geophysics, oceanographic and atmospheric research communities. Inertial waves, which are driven by restoring forces, for example the Coriolis force, have been detected in the research fields mentioned above. This paper investigates inertial waves in turbine rim seal flows in turbomachinery. These are associated with the large-scale unsteady ow structures having distinct frequencies, unrelated to the main annulus blading, identified in many experimental and numerical studies. These unsteady flow structures have been shown in some cases to reduce sealing effectiveness and are difficult to predict with conventional steady Reynolds-averaged Navier-Stokes (RANS) approaches. Improved understanding of the underlying ow mechanisms and how these could be controlled is needed to improve the efficiency and stability of gas turbines. This study presents large-eddy simulations for three rim seal configurations { chute, axial and radial rim seals { representative of those used in gas turbines. Evidence of inertial waves is shown in the axial and chute seals, with characteristic wave frequencies limited within the threshold for inertial waves given by classic linear theory (i.e. jf=frelj 2), and instantaneous flow fields showing helical characteristics. The radial seal, which limits the radial fluid motion with the seal geometry, restricts the Coriolis force and suppresses the inertial wave.
This paper presents large-eddy and direct numerical simulations of buoyancy-driven convection in sealed and open rapidly rotating cavities for Rayleigh numbers in the range 107-109, and axial throughflow Reynolds numbers 2000 and 5600. Viscous heating due to the Ekman layer scrubbing effect, which has previously been found responsible for the difference in sealed cavity shroud Nusselt number predictions between a compressible N-S solver and an incompressible counterpart using the Boussinesq approximation, is discussed and scaled up to engine conditions. For the open cavity with an axial throughflow, laminar Ekman layer behaviour of the mean flow statistics is confirmed up to the highest condition in this paper. The Buoyancy number Bo is found useful to indicate the influence of an axial throughflow. For the conditions studied the mean velocities are subject to Ra, while the velocity fluctuations are affected by Bo. A correlation, Nu0 = 0:169(Ra0)0:318, obtained with both the sealed and open cavity shroud heat transfer solutions, agrees with that for free gravitational convection between horizontal plates within 16% for the range of Ra0 considered.
This paper presents a systematic study of flow and heat transfer mechanisms in a compressor disc cavity with an axial throughflow under centrifugal buoyancy-driven convection, comparing with previously published experimental data. Wall-modelled large-eddy simulations are conducted for six operating conditions, covering a range of rotational Reynolds number (3.2 × 105 – 2.2 × 106), buoyancy parameter (0.11 – 0.26) and Rossby number (0.4 – 0.8). Numerical accuracy and computational efficiency of the simulations are considered. Wall heat transfer predictions are compared with measured data with a good level of agreement. A constant rothalpy core occurs at high Eckert number, appearing to reduce the driving buoyancy force. The flow in the cavity is turbulent with unsteady laminar Ekman layers observed on both discs except in the bore flow affected region on the downstream disc cob. The shroud heat transfer Nusselt number-Rayleigh number scaling agrees with that of natural convection under gravity for high Rayleigh numbers. Disc heat transfer is dominated by conduction across unsteady Ekman layers, except on the downstream disc cob. The disc bore heat transfer is close to a pipe flow forced convection correlation. The unsteady flow structure is investigated showing strong unsteadiness in the cavity that extends into the axial throughflow.
While turbine rim sealing flows are an important aspect of turbomachinery design, affecting turbine aerodynamic performance and turbine disc temperatures, the present understanding and predictive capability for such flows is limited. The aim of the present study is to clarify the flow physics involved in rim sealing flows and to provide high quality experimental data for use in evaluation of CFD models. The seal considered is similar to a chute seal previously investigated by other workers, and the study focuses on the inherent unsteadiness of rim seal flows, rather than unsteadiness imposed by the rotating blades. Unsteady pressure measurements from radially and circumferentially distributed transducers are presented for flow in a rotor-stator disc cavity and the rim seal without imposed external flow. The test matrix covered ranges in rotational Reynolds number, Re∅, and non-dimensional flow rate, , of 2.2 –3.0x106 and 0 – 3.5x103 respectively. Distinct frequencies are identified in the cavity flow and detailed analysis of the pressure data associates these with large scale flow structures rotating about the axis. This confirms the occurrence of such structures as predicted in previously published CFD studies and provides new data for detailed assessment of CFD models.
This paper reports large-eddy simulations (LES) and unsteady Reynolds-averaged Navier-Stokes (URANS) calculations of a turbine rim seal configuration previously investigated experimentally. The configuration does not include any vanes, blades or external flows, but investigates inherent unsteady flow features and limitations of CFD modelling identified in engine representative studies. Compared to RANS and URANS CFD models, a sector LES model showed closer agreement with mean pressure measurements. LES models also showed agreement with measured pressure frequency spectra, but discrepancies were found between the LES and experiment in the speed and the circumferential lobe number of the unsteady flow structures. Sensitivity of predictions to modelling assumptions and differences with experimental data are investigated through CFD calculations considering sector size, interaction between the rim cavity and the inner cavity, outer annulus boundary conditions, and the coolant mass flow. Significant sensitivity to external flow conditions, which could contribute to differences with measurements, is shown, although some discrepancies remain. Further detailed analysis of the CFD solutions is given illustrating the complex flow physics. Possible improvement of a steady RANS model using a priori analysis of LES was investigated, but showed a rather small improvement in mean pressure prediction.
Unsteady flow phenomena unrelated to the main gas-path blading have been identified in a number of turbine rim seal investigations. This unsteadiness has significant influence on the sealing effectiveness predicted by the conventional steady RANS (Reynolds-averaged Navier–Stokes) method, thus it is important for turbine stage design and optimisation. This paper presents CFD (computational fluid dynamics) modelling of a chute type rim seal that has been previously experimentally investigated. The study focuses on inherent large-scale unsteadiness rather than that imposed by vanes and blades or external flow. A large-eddy simulation (LES) solver is validated for a pipe flow test case and then applied to the chute rim seal rotor/stator cavity. LES, RANS and unsteady RANS (URANS) models all showed reasonable agreement with steady measurements within the disc cavity, but only the LES shows unsteadiness at a similar distinct peak frequency to that found in the experiment, at 23 times the rotational frequency. The boundary layer profile within the chute rim seal clearance has been scrutinised, which may explain the improvement of LES over RANS predictions for the pressure drop across the seal. LES results show a clockwise mean flow vortex. A more detailed sketch of the rim sealing flow unsteady flow structures is established with the help of the LES results. However, there are some significant differences between unsteadiness predicted and the measurements, and possible causes of these are discussed.
This paper presents a review of research on turbine rim sealing with emphasis placed on the underlying flow physics and modelling capability. Rim seal flows play a crucial role in controlling engine disc temperatures but represent a loss from the main engine power cycle and are associated with spoiling losses in the turbine. Elementary models that rely on empirical validation and are currently used in design do not account for some of the known flow mechanisms, and prediction of sealing performance with computational fluid dynamics (CFD) has proved challenging. CFD and experimental studies have indicated important unsteady flow effects that explain some of the differences identified in comparing predicted and measure sealing effectiveness. This review reveals some consistency of investigations across a range of configurations, with inertial waves in the rotating flow apparently interacting with other flow mechanisms which include vane, blade and seal flow interactions, disc pumping and cavity flows, shear layer and other instabilities, and turbulent mixing.
This paper presents large-eddy and direct numerical simulations of buoyancy-driven convection in sealed and open rapidly rotating cavities for Rayleigh numbers in the range 107–109, and axial throughflow Reynolds numbers 2000 and 5600. Viscous heating due to the Ekman layer scrubbing effect, which has previously been found responsible for the difference in sealed cavity shroud Nusselt number predictions between a compressible N-S solver and an incompressible counterpart using the Boussinesq approximation, is discussed and scaled up to engine conditions. For the open cavity with an axial throughflow, laminar Ekman layer behaviour of the mean flow statistics is confirmed up to the highest condition in this paper. The Buoyancy number Bo is found useful to indicate the influence of an axial throughflow. For the conditions studied the mean velocities are subject to Ra, while the velocity fluctuations are affected by Bo. A correlation, Nu' = 0.169(Ra')0.318, obtained with both the sealed and open cavity shroud heat transfer solutions, agrees with that for free gravitational convection between horizontal plates within 16% for the range of Ra' considered.
This paper presents wall-modeled large-eddy simulations (WMLES) of a chute-type turbine rim seal. Configurations with an axisymmetric annulus flow and with nozzle guide vanes fitted (but without rotor blades) are considered. The passive scalar concentration solution and WMLES are validated against available data in the literature for uniform convection and a rotor-stator cavity flow. The WMLES approach is shown to be effective, giving significant improvements over an eddy viscosity turbulence model, in prediction of rim seal effectiveness compared to research rig measurements. WMLES requires considerably less computational tune than wall-resolved LES, and has the potential for extension to engine conditions. All WMLES solutions show rotating inertial waves in the chute seal. Good agreement between WMLES and measurements for sealing effectiveness in the configuration without vanes is found. For cases with vanes fitted, the WMLES simulation shows less ingestion than the measurements, and possible reasons are discussed.
Hot gas ingestion in a chute seal configuration has been numerically and experimentally investigated. First, the NGVs were included to generate a swirled annulus flow. This staged approach to rig configuration is used to understand the relative contribution of rotation and NGVs induced pressure asymmetries in turbine rim sealing flow ingestion. Computations were performed with a URANS model and a novel LES code including near wall boundary layer modelling, the wall-modelled LES (WMLES). The experimental data was obtained in the Oxford Rotor Facility (ORF). The main focus of this study was the mean cavity flow aerodynamics and the sealing performance of the chute seal under a range of operating conditions. These are studied through measurements of pressure and gas concentration within the rotor-stator disc cavity and the rim seal which are compared to CFD predictions. In addition, experimental and CFD assessments of concentration-based sealing effectiveness in the gas path for the vaned configuration are presented. Measurements were taken at a representative rotor leading edge axial position to focus on the radial diffusion and interaction between the purge flow and annulus flow. Overall the WMLES code better captured the interaction between main annulus and turbine cavity flow positioning it as a powerful tool with potential to be implemented in the design and verification process.
Large-eddy simulation (LES) is compared with experiment and Reynolds-averaged Navier-Stokes (RANS), and LES is shown to be superior to RANS in reproducing corner separation in the LMFA-NACA65 linear compressor cascade, in terms of surface limiting streamlines, blade pressure coefficient, total pressure losses and blade suction side boundary layer profiles. However, LES is too expensive to conduct an influencing parameter study of the corner separation. RANS approach, despite over-predicting the corner separation, gives reasonable descriptions of the corner separated flow, and is thus selected to conduct a parametric study in this paper. Two kinds of influencing parameters on corner separation, numerical and physical parameters, are analyzed and discussed: second order spatial scheme is necessary for a RANS simulation; incidence angle and inflow boundary layer thickness are found to show the most significant influences on the corner separation among the parameters studied; unsteady RANS with the imposed inflow unsteadiness (inflow angle varying sinusoidally with fluctuating amplitude of 0.92°) does not show any non-linear effect on the corner separation.
This paper presents CFD (computational fluid dynamics) modelling of a chute type rim seal that has been previously experimentally investigated. The study focuses on inherent large-scale unsteadiness rather than that imposed by vanes and blades or external flow. A large-eddy simulation (LES) solver is validated for a pipe flow test case and then applied to the chute rim seal rotor/stator cavity. LES, Reynolds-averaged Navier-Stokes (RANS) and unsteady RANS (URANS) models all showed reasonable agreement with steady measurements within the disc cavity, but only the LES shows unsteadiness at a similar distinct peak frequency to that found in the experiment, at 23 times the rotational frequency. However, there are some significant differences between unsteadiness predicted and the measurements, and possible causes of these are discussed.
Additional publications
F Gao, Advanced numerical simulation of corner separation in a linear compressor cascade. PhD thesis. Ecole Centrale de Lyon. 2014