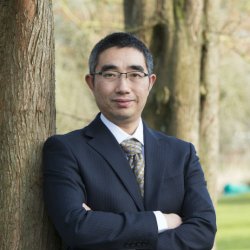
Dr Guohong Tian
About
Biography
Dr G Tian joined the University of Surrey in June 2015. Prior to this, he was a Lecturer at Sir Joseph Swan Centre for Energy Research, Newcastle University from 2010 to 2015, after serving Birmingham University as a Research Fellow from 2008.He has many years of experience in internal combustion engine research. He has collaborated with a number of industrial partners including Jaguar Land Rover, Cummins, BP, Shell, JCB, Continental and Avid.
University roles and responsibilities
- Departmental rep of Faculty International Relations Committee and Mobility Committee
- Departmental coordinator of Headstart and Summer School
- Year two tutor
ResearchResearch interests
- Alternative fuels for Internal Combustion engines
- Engine spray and combustion diagnostics
- Advanced engine combustion technologies
- Novel engines technologies including free piston engine, con-rod-less engine and scroll engine
- Engine waste heat recovery by organic Rankine cycle
- Desalination
I am developing a state-of-the-art engine test bench with an FTIR based emission analyser. The test bench will be capable of conducting any up to 180kW heavy or light duty engine research in the area of alternative fuel, advanced combustion technology, waste heat recovery system or after-treatment system development. The bench can also be used as a platform for engine sub-systems research and development.
A high speed imaging system for spray and combustion research is under development, together with a supercritical injection test rig. For more information please get in touch.
Research projects
KTP project with William Medcalf LimitedThis project aims to use modern engine development technologies to improve vintage Bentley engine performance without losing the original taste of the drivability.
ADVICE-ADvancing user acceptance of general purpose hybridized VehiclesThis project is funded by Improved Cost and Efficiency. Our aim in this H2020 project is to understand and optimise the thermal energy management of an hybrid vehicle IC engine
Research interests
- Alternative fuels for Internal Combustion engines
- Engine spray and combustion diagnostics
- Advanced engine combustion technologies
- Novel engines technologies including free piston engine, con-rod-less engine and scroll engine
- Engine waste heat recovery by organic Rankine cycle
- Desalination
I am developing a state-of-the-art engine test bench with an FTIR based emission analyser. The test bench will be capable of conducting any up to 180kW heavy or light duty engine research in the area of alternative fuel, advanced combustion technology, waste heat recovery system or after-treatment system development. The bench can also be used as a platform for engine sub-systems research and development.
A high speed imaging system for spray and combustion research is under development, together with a supercritical injection test rig. For more information please get in touch.
Research projects
This project aims to use modern engine development technologies to improve vintage Bentley engine performance without losing the original taste of the drivability.
This project is funded by Improved Cost and Efficiency. Our aim in this H2020 project is to understand and optimise the thermal energy management of an hybrid vehicle IC engine
Supervision
Postgraduate research supervision
- Mr Ioannis Kalargaris, project topic: Pyrolysis oils in commercial scale IC engines
- Mr Simon Emhardt, project topic: Development of Scroll Expander
Teaching
- ENG1062 Fluid Mechanics & Thermodynamics
- ENG2119 Powertrain design & Chassis Engineering
- ENG2087 Design Project
I am interested in taking promising graduate research students in the area of vehicle powertrain system. If you need support in applying for a scholarship for a PhD studentship, including CSC scholarship, please get in touch.
Sustainable development goals
My research interests are related to the following:
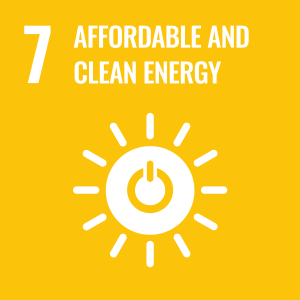
Publications
Multi-point ignition and non-equilibrium plasma ignition technologies were both certified to enhance the ignition and combustion processes of ammonia (NH3). High-frequency Nanosecond Surface dielectric barrier discharge (nSDBD) ignition is a promising strategy to carry out both multi-point ignition and non-equilibrium plasma ignition with high energy supply. However, there is little research on how equivalence ratio, initial pressure, and initial temperature affect NH3/air mixtures ignited by nSDBD in Constant Volume Chamber (CVC). This study experimentally-investigated the plasma assisted NH3/air ignition with a high-frequency nSDBD device in a CVC. The effects of equivalence ratio, initial pressure, and initial temperature on this plasma assisted NH3/air ignition strategy were evaluated by discharge performance, flame morphology, and combustion parameters. Results showed that initial pressure strongly influenced the total supplied energy to nSDBD, with a bell-shaped tendency as the initial pressure increased. Near-stoichiometric mixtures exhibited the fastest flame kernel development, the highest pressure rise, and the greatest heat release. Lower initial pressure and higher initial temperature generally promoted flame kernel growth but delayed pressure rise and heat release, though extremely low pressure prevented ignition. [Display omitted] •Nanosecond-scale high-frequency nSDBD was applied to ignite NH3/air mixtures.•Effects of equivalence ratio, initial pressure, and initial temperature on NH3 ignition.•Near stoichiometric equivalence ratios achieved optimal combustion.•Increasing initial temperature promoted NH3 ignition and combustion.
This research paper presents a CFD analysis of small scale ORC scroll expanders using variable and constant wall thicknesses by providing back-to-back aerodynamic performance comparisons. The evaluation of the three-dimensional and transient CFD results shows that the shorter scroll profile length of the variable wall thickness design (VWD) generated lower average radial and axial gas forces. In addition, higher pressure gradients in between individual working chambers contributed to a higher peak of the tangential gas moment despite higher transient gas force and tangential gas moment variations. Moreover, the pressure trace analysis reveals that the expansion process was finished at a crank angle of 816° in VWD, compared to 996° in the constant wall thickness design (CWD). The studies of the static pressure distributions along the surface of the fixed scroll of the two geometries indicate that static pressure drops through local radial clearances were higher in VWD. However, a higher number of static pressure drops occurred in CWD. The expansion process of CWD was driven by lower pressure gradients resulting in a complete dissipation of the large-scale vortices in the expansion chambers of CWD at the crank angle of 672°, in contrast to 600° in the expansion chambers of VWD.
When coupling the Free Piston Engine (FPE) to the Permanent Magnet Linear Synchronous Machine (PMLSM) to produce electrical energy, its intrinsic multi-directional and non-linear dynamics have been typically described in a simplified mono-directional and linear fashion when considering a system-level modelling approach. This paper presents a detailed, multi-directional, multi-domain model of the FPE and PMLSM. The model was implemented in an opposed-piston free-piston engine configuration and validated against experimental data captured from a prototype with identical parameters. The simulation results indicate a strong correlation to the experimental data, which captured the dominant dynamics of the FPE and proved the satisfactory accuracy and performance of the model. This study considers the characteristic multi-directional nature and non-linearity of the machine dynamics and its interactions with multi-physical domains such as electrical, mechanical, and pneumatic.
Review A Comprehensive Review of the Free Piston Engine Generator and Its Control Patrick Brosnan 1, Guohong Tian 1, * , Umberto Montanaro 1, and Sam Cockerill 2 1 School of Mechanical Engineering Sciences, University of Surrey, Surrey GU2 7XH, UK 2 Libertine FPE Ltd., Sheffield S9 1DA, UK * Correspondence: g.tian@surrey.ac.uk; Tel.: +44-1483-300-800 Received: 2 February 2023 Accepted: 10 March 2023 Published: 23 March 2023 Abstract: The Free Piston Engine (FPE) is a unique machine with a higher thermal efficiency than its counterpart, the Conventional Reciprocating Piston Engine (CPE). The unique piston motion of the FPE is not constrained kinematically like the CPE with its connecting crankshaft and rotational inertial masses. Moreover, when directly coupled to the Linear Electric Machine (LEM) to harness electric energy production, the Free Piston Engine Generator’s (FPEG) characteristic motion, now being dynamically constrained, permits an extensive range of piston trajectory profiles to be exploited during operation. In addition, exploring varied piston trajectories during the development stages may be vital in reducing in-cylinder combustion emissions through strategies such as Low-Temperature Combustion (LTC) and Homogeneous Charge Compression Ignition (HCCI). This review paper will focus on the key motivations and drivers for continued FPEG development. It will also highlight and review its distinct advantages and challenges in being a viable solution as a future zero-carbon engine technology. Finally, FPE fundamentals, alongside its rich history, will be introduced, clearly presenting how academia and industry have described and controlled its intrinsic non-linear dynamics.
•The motivations for continued FPE and LEM development are established•A non-linear and multi-domain model of the PMLSM is presented•Incorporation of the PMLSM in an FPEG multi-domain model is demonstrated•Model validation with data captured from an experimental FPEG is conducted•Simulation results indicate the model captures the dominant dynamics of the PMLSM The Free Piston Engine (FPE) can be considered a viable and promising option in future low-carbon technology development. When coupled to the Linear Electric Machine (LEM) to produce electrical energy, its characteristic non-linear dynamics typically have been described as linear when considering a systems-level modelling approach. This paper presents a multi-domain model of a Permanent Magnet Linear Synchronous Machine (PMLSM) for Free Piston Engine Generators (FPEG) and offers a detailed non-linear mathematical description of the machine dynamics. The model was implemented in a free-piston expander system and validated against experimental data from a test rig that has identical parameters. The simulation results indicate a strong correlation to the experimental data, which captured the dominant dynamics of the PMLSM and prove the satisfactory accuracy and performance of the model, together with a similar voltage and current output trace, indicating a cyclic energy output error of approximately 10 %. This paper aims to extend the current knowledge and literature within FPEG PMLSM design by considering the inherent non-linearity and multi-directional nature of the system dynamics and its interactions with multi-physical domains.
Chemical recycling is an attractive way to address the explosive growth of plastic waste and disposal problems. Pyrolysis is a chemical recycling process that can convert plastics into high quality oil, which can then be utilised in internal combustion engines for power and heat generation. The aim of the present work is to evaluate the potential of using oils that have been derived from the pyrolysis of plastics at di erent temperatures in diesel engines. The produced oils were analysed and found to have similar properties to diesel fuel. The plastic pyrolysis oils were then tested in a four-cylinder direct injection diesel engine, and their combustion, performance and emission characteristics analysed and compared to mineral diesel. The engine was found to perform better on the pyrolysis oils at higher loads. The pyrolysis temperature had a signi cant e ect, as the oil produced at a lower temperature presented higher brake thermal e ciency and shorter ignition delay period at all loads. This oil also produced lower NOX, UHC, CO and CO2 emissions than the oil produced at a higher temperature, although diesel emissions were lower.
With the increasing pressure of fossil fuel consumption and pollutions from vehicles powered by internal combustion engines, much attention has been attracted for hybrid and electric vehicles. With this background, an increasing demand for compact and high power density engines is being developed for the purpose of hybrid vehicles. In this paper, the design of a novel opposed rotary piston engine was investigated. In comparison with conventional reciprocating engines, this design has no crank connecting rods and intake/exhaust valves, and the operation cycle takes 360° crank angle to complete but similar to a four stroke cycle. 3D and 1D simulations were conducted to analyse the in-cylinder flow and evaluate the engine performance. The simulation results indicated the air velocity was very high at the end of intake stroke due to the lack of intake valves. The opposed rotary piston engine had a higher fraction of constant volumetric combustion that yielded to less heat loss, which contributed to a higher power output per combustion cycle than a reciprocating engine at low engine speed. The estimated minimum brake specific fuel consumption and maximum power density were 240 g/(kW·h) and approximately 80 kW/L, respectively.
© 2014 The Authors. Published by Elsevier Ltd.As an alternative to conventional engines, free-piston engine generator (FPEG) is a promising power generation system due to its simplicity and high thermal efficiency. One crucial technical challenge in the FPEG operation is the initial process of overcoming the compression force to achieve a certain speed which allows a stable and continuous operation, i.e. starting process. This paper proposes a novel method to start the engine by mechanical resonance. A closed-loop control model was developed and implemented in a prototype FPEG which was driven by a linear machine with a constant driving force. Both numerical and experimental investigation was carried out. The results show that once the linear motor force have overcome the initial friction force, both the in-cylinder peak pressure and the amplitude of the piston motion would increase gradually by resonance and quickly achieve the target for ignition. With a fixed motor force of 110N, within 0.8 second, the maximum in-cylinder pressure can achieve 12 bars, the compression ratio can reach 9:1, and the engine is ready for ignition. The results demonstrated that it is feasible to start the FPEG by mechanical resonance in a constant motor force in the direction of the natural bouncing motion.
Evaluation of driving behaviour is helpful for policy development, and for designing infrastructure and an intelligent safety system for a car. This study focused on a quantitative evaluation method of driving behaviour based on the shared-electrical car. The data were obtained from the OBD interface via CAN bus and transferred to a server by 4G network. Eleven types of NDS data were selected as the indexes for driving behaviour evaluation. Kullback-Leibler divergence was calculated to confirm the minimum data quantity and ensure the effectiveness of the analysis. The distribution of the main driving behaviour parameters was compared and the change trend of the parameters was analysed in conjunction with car speed to identify the threshold for recognition of aberrant driving behaviour. The weights of indexes were confirmed by combining the analytic hierarchy process and entropy weight method. The scoring rule was confirmed according to the distribution of the indexes. A score-based evaluation method was proposed and verified by the driving behaviour data collected from randomly chosen drivers.
This paper investigated the effects of hydrogen addition to gasoline surrogates fuel-air mixture on the premixed spherical flame laminar combustion characteristics. The experiments were carried out by high speed Schlieren photography on a constant-volume combustion vessel. Combining with nonlinear fitting technique, the variation of flame propagation speed, laminar burning velocity, Markstein length, flame thickness, thermal expansion coefficient and mass burning flux were studied at various equivalence ratios (0.8–1.4) and hydrogen mixing ratios (0%–50%). The results suggested that the nonlinear fitting method had a better agreement with the experimental data in this paper and the flame propagation was strongly effected by stretch at low equivalence ratios. The stretched propagation speed increased with the increase of hydrogen fraction at the same equivalence ratio. For a given hydrogen fraction, Markstein length decreased with the increase of equivalence ratio; flame propagation speed and laminar burning velocity first increased and then decreased with the increase of equivalence ratio while the peaks of the burning velocity shifted toward the richer side with the increase of hydrogen fraction.
Diesel particulate matter (PM) has brought about huge environmental problems. The diameter of diesel PM is smaller than 1 mu m that could be easily inhaled into the respiratory system. The PM diameter is smaller if turbocharger and common rail are used. Restrict exhaust emission legislations were carried out to decrease diesel PM emissions both in mass and number level. The formation mechanism of diesel PM is complex, and the cylinder combustion conditions have a huge effect on PM physico-chemical properties. In this chapter, the detailed analysis of diesel PM physico-chemical properties is made such as particulate ingredients, diameter and mass distributions, microstructures and oxidation behaviours. Diesel PM mainly contains soot, soluble organic fraction and ash whose percentages change with PM formation conditions such as engine load and speed, engine type and fuel type. Diameter distributions of diesel PM show a peak value around 100 nm that is caused by nucleation mode, while the mass distributions present double peaks around 40 and 300 nm, where the nucleation and accumulation mode particulates dominate, respectively. And, the researches of microstructures and oxidation behaviour make the foundation of decreasing PM emission and optimizing PM after-treatment device.
Popularisations of hybrid vehicles and range extender electric vehicles promote the development of high power density and small scale internal combustion engines. Opposed rotary piston (ORP)engines characteri s ed by compact designs, few moving parts and high power density are an ideal power source for the above mentioned vehicles. Due to the short cyclic period of the ORP engine, hydrogen fuel was applied to decrease the combustion duration This paper investigate d the in cylinder combustion and emission s characteristics of the hydrogen fuelled ORP engine using 3D numerical simulation method at various engine speeds and full load conditions. In cylinder pressure evolutions, heat release rates, nitrogen monoxide (NO) formations, and power density were analysed to evaluate the engine performance The results indicated that volumetric efficiency of this ORP engine was higher than 88.3 for all the given scenarios , being benefited from large area of intake ports . Peak in cylinder pressure decreased significantly with engine speed s which was mainly resulted fr om low fuel mass burn fraction before top dead centre (TDC) for high engine speed conditions. As long as the combustion chambers passed TDC, combustion flame propagated from the bowls into the gaps between end faces of adjacent pistons rapidly. In the exhaust stroke,free discharge process of this ORP engine last ed longer duration than reciprocating engines, which would lead to more energy loss es . NO was mainly formed after TDC, with the accumulated NO mass being in the range of 0. 0 7 mg ~ 5 mg per cycle per cylinder in the engine speed range of 1000~5000 r/min . Maximum power density and NO emission s factor of this engine fuelled with hydrogen was approximately 69.2 kW·L 1 and 10.60 g·(kW·h) 1 , Indicated thermal efficiency dropped from 36.2 to 26.5% when the engine speed increased from 1000 to 5000 r/min
This investigation addresses the potential for heat recovery from Multi Stage Flash (MSF) desalination plant hot distillate water to power an Organic Rankine Cycle (ORC), comparing R134a and R245fa refrigerants as the working fluid. Using design characteristics of an existing ORC unit, the model was first validated against its measured output. The distillate hot water from MSF stages is utilised to provide heat to the ORC and performance is investigated for both working fluids and for the number of MSF stages for heat recovery. For the specific MSF plant investigated, the net produced ORC power is found the highest with extraction up to MSF powering stage 8, generating 359. kW when R245fa is used and 307. kW when R134a is used. Both refrigerants exhibit an increase of power output and decrease of energy efficiency as heat is recovered from more MSF stages. The influence of variation of the evaporator and cooling temperature on ORC performance is demonstrated to be significant for both refrigerants, with R245fa performing better in this specific application. © 2014 Elsevier Ltd.
Opposed rotary piston (ORP) engines can deliver high power density and have few moving parts, being suitable for the power sources of hybrid electric vehicles, range extended electric vehicles, and unmanned aerial vehicles. Hydrogen as a promising alternative fuel is free of carbon emissions during combustion. Hydrogen direct injection avoids the significant power losses of port injection scenarios resulting from the low hydrogen energy density by volume. This paper firstly investigated the ORP engine performance using a 3D numerical simulation method over various hydrogen direct injection strategies (start of hydrogen injection and injection durations). Hydrogen diffusions in combustion chambers, combustion characteristics, engine performance, nitrogen oxides (NOx) emissions, and knock tendency were researched over various hydrogen injection strategies. Hydrogen was unevenly distributed in the combustion chambers for high equivalence ratio scenarios, leading to low combustion efficiency; additionally, the unburned hydrogen was mainly in the cylinder bowls and bottoms. Combustion durations were the shortest within the equivalence ratio range of 0.577–0.865, being approximately 18° crank angle (CA). The maximum in-cylinder pressure was higher than 8.0 MPa over the equivalence ratio of 0.961; and the corresponding heat release rates were higher than 45 J·(°CA)−1. The indicated thermal efficiency was higher than 38%, and it was increased generally by dropping equivalence ratios, with the maximum efficiency being approximately 42.5%. NOx emission factors, approximately 35 g (kW h)−1, reached the maximum value under the equivalence ratio of 0.673 conditions. Knock tendency was decreased continuously by lowering equivalence ratios. This research made a foundation of improving the engine fuel economy and mitigating NOx emissions for hydrogen direct injection ORP engines. •Hydrogen direct injection applied to ORP engines maintains high power density.•Hydrogen injection strategy affects mixture formation and combustion characteristics.•High ER cases had low combustion efficiency due to uneven hydrogen distributions.•Thermal efficiency was increased by low ER due to less heat loss by cylinder walls.•Cylinder bowls were the man regions having high NOx concentration for all the cases.
Backfire of hydrogen-fuelled internal combustion engines limits the hydrogen fuel applications and drops the power output. Opposed rotary piston (ORP) engines are characterized by high power density, smooth operations, and few moving parts. However, the intake structures of ORP engines tend to deliver high possibility of backfire under hydrogen utilization conditions due to more residual exhaust. This paper proposed an effective approach of eliminating backfire for a hydrogen fuelled ORP engine, and it did not generate any penalty of power output theoretically. The effectiveness of this method was demonstrated using a 3D numerical simulation method. The results indicated that the average in-cylinder temperature started to increase at the start of the intake process if without any backfire control strategies; however, it decreased continuously if backfire control was applied. The mass flow rates of the intake fluid were at a low level without backfire control, but it increased sharply if backfire control was adopted. Backfire in this investigation was caused by the pre-ignition of mixture in cylinders. The temperature in intake pipes reached up to 1000 K over backfire scenarios, and heat of reaction was higher than 3 W. Hydrogen mass fractions at the bottom of intake pipes were low at the start of intake process due to the backfire; meantime, slight backflow also happened in the intake process due to the pre-ignition of cylinders mixture. The fluid velocity was higher than 100 m/s at the beginning of intake process if backfire was controlled.
Opposed rotary piston engines are characterized by high power density, which makes them as an ideal power source for hybrid vehicles and range extended electric vehicles. Hydrogen applications can fully exhibit the merits of opposed rotary piston engines, and achieve zero carbon dioxide emissions; however, the applications seriously worsen the nitrogen oxides emissions. In this investigation, lean-burn was adopted to achieve low nitrogen oxides emissions using a three dimensional numerical simulation approach. The results indicated that engine speed of 3000 r/min presented the highest in-cylinder pressure during combustion among the given scenarios, and the pressure over 3000 r/min depended more on the equivalence ratio than that of 1000 r/min and 2000 r/min. Heat release rates were very sensitive to low equivalence ratio. Combustion duration over the equivalence ratio of 0.8 was the shortest among 1000 r/min cases; however, it decreased with equivalence ratio for 2000 r/min and 3000 r/min. Heat loss rates through cylinder walls increased significantly with engine speed, meanwhile they were more dependent on the equivalence ratio over higher engine speed. Maximum nitrogen monoxide formation rates over 3000 r/min occurred slightly earlier than those of 1000 r/min and 2000 r/min. Equivalence ratio of 0.8 showed the highest indicated thermal efficiency over corresponding engine speed, and nitrogen dioxide emission factors were quite low over the equivalence ratio of 0.7 for the given engine speed. [Display omitted] •Start of hydrogen combustion was retarded with the increase of equivalence ratio.•3000 RPM presented the highest in-cylinder temperature and combustion efficiency.•Indicated thermal efficiency had the highest value over the equivalence ratio of 0.8.•Heat loss through cylinder walls depended on the engine speed and equivalence ratio.•NO emission factor was much low over the equivalence ratio of 0.7.
© 2014 Elsevier Ltd. All rights reserved. This paper focuses on the numerical modelling of a spark ignited free-piston engine generator and the model validation with test results. Detailed sub-models for both starting process and steady operation were derived. The compression and expansion processes were not regarded as ideal gas isentropic processes; both heat transfer and air leakage were taken into consideration. The simulation results show good agreement with the prototype test data for both the starting process and steady operation. During the starting process, the difference of the in-cylinder gas pressure can be controlled within 1 bar for every running cycle. For the steady operation process, the difference was less than 5% and the areas enclosed on the pressure-volume diagram were similar, indicating that the power produced by the engine and the engine efficiency could be predicted by this model. Based on this model, the starting process with different starting motor forces and the combustion process with various throttle openings were simulated. The engine performance during stable operation at 100% engine load was predicted, and the efficiency of the prototype was estimated to be 31.5% at power output of 4 kW.
The differences between modern diesel and gasoline engine configurations are now becoming smaller and smaller, and in fact will be even smaller in the near future. They will all use moderately high compression ratios and complex direct injection strategies. The HCCI combustion mode is likely to lead to the merging of gasoline and diesel engine technologies to handle the challenges they are facing, offering a number of opportunities for the development of the fuels, engine control and after-treatment. The authors' recent experimental research into the HCCI combustion quality of gasoline and diesel blend fuels has referred to the new combustion technology as 'Dieseline'. It is found that this kind of fuel blend provides some unexpected benefits to the expansion of the operating window and reduction of hydrocarbon emissions in HCCI engines, and these benefits include extended low misfire limit, increased engine stability, reduced peak cylinder pressures and reduced emissions within the whole HCCI operating window. It was shown that the lean limit of lambda can almost reach up to 2.0 when the engine is operated with moderate compression ratios. It is shown that the combustion of the blended fuel offers promise to the desired ignition quality, which reduces the dependence of HCCI on EGR trapping or intake heating for a wide range of CR. The HCCI operating region for the unheated NVO can be significantly extended into lower IMEP values and the audible knocking is restrained to the highest values of air fuel ratio at high load boundary for the highest mixture temperatures. Copyright ©2009 SAE International.
Conventional diesel fuelled Partially-Premixed Compression Ignition (PPCI) engines have been investigated by many researchers previously. However, the ease of ignition and difficulty of vaporization of diesel fuel make it imperfect for PPCI combustion. In this study, Dieseline (blending of diesel and gasoline) was looked into as the Partially-Premixed Compression Ignition fuel for its combination of two fuel properties, ignition-delay-increasing characteristics and higher volatility, which make it more suitable for PPCI combustion compared to neat diesel. A series of tests were carried out on a Euro IV light-duty common-rail diesel engine, and different engine modes, from low speed/load to middle speed/load were all tested, under which fuel blend ratios, EGR rates, injection timings and quantities were varied. The emissions, fuel consumption and combustion stability of this dieseline-fuelled PPCI combustion were all investigated. The results showed that dieseline had great advantages as a PPCI combustion fuel in terms of emission reduction. This was particularly significant at high-speed engine mode. It was also found that with a blend of 50% gasoline in diesel, the particle numbers total concentration could be reduced by 90% while low NOx level and high brake fuel conversion efficiency (around 30%) were maintained at all the loads tested. © 2011 SAE International.
Opposed rotary piston (ORP) engines have high power density and compact designs which meet the requirements of power sources of hybrid vehicles. Hydrogen applications to ORP engines can effectively decrease greenhouse gas emissions; however, hydrogen combustion in ORP engines around stoichiometric ratio generated large quantities of nitrogen oxides (NO x), especially for low engine speed conditions. Lean-burn as an effective method to decrease NO x emissions was adopted in this research. A 3D numerical simulation method was used to explore the effect of equivalence ratio (≤1) on combustion and NO x emission characteristics of this ORP engine fuelled with hydrogen. The results indicated that peak in-cylinder pressure increased with equivalence ratio for 1000 revolutions per minute (RPM); however, the value over the equivalence ratio of 0.9 was the maximum among 2000 RPM scenarios. The effect of equivalence ratio on heat release rates was greatly dependent on the engine speeds. Start of combustion over 1000 RPM engine speed was advanced with the increase of equivalence ratio; and it was the earliest over the equivalence ratio of 0.9 at 2000 RPM conditions. During the exhaust stroke, in-cylinder pressure of free discharge was much higher than atmosphere pressure, which significantly increased the pumping losses of exhaust stroke. Accumulated NO x emissions over the equivalence ratio of 0.9 reached the maximum value for given engine speeds; and the NO x emissions were almost zero for severe lean-burn (
Requirements of recycling low temperature waste heat energy from internal combustion engines drive the developments of excellent performance expanders with high compactness which significantly affects the applications of waste heat recovery systems to on-road vehicles. In the present study, an opposed rotary piston expander was proposed for the practical utilisations on a small-scale Organic Rankine Cycle (ORC) system, aiming at recycling the waste heat energy from internal combustion engines of on-road vehicles. The opposed rotary piston expander had a cyclic period of 180° crank angle (CA), four intake ports and two discharge ports. In order to investigate the expander performance, 3D numerical simulations were conducted under various scenarios whose boundary conditions were among the frequently reported thermodynamic states in ORC systems; additionally, these scenarios were around the design operation point of the expander. Intake and discharge characteristics, in-cylinder pressure evolutions, in-cylinder fluid flow, and P-V diagrams were analysed; further, volumetric efficiency, power output and adiabatic efficiency were calculated using the simulation results, and were compared to various types of expanders. Each two opposed cylinders had the same evolutions of cylinder volume, fluid mass, in-cylinder pressure, and temperature during operation. Maximum fluid flow rate in the intake process increased with intake pressure and rotation speed; in addition, the in-cylinder pressure reached the maximum value in a short time after the intake ports opened. However, high rotation speed also led to a drop of in-cylinder pressure (expansion process), volumetric efficiency, and adiabatic efficiency compared to low speed condition.
Plenty of diesel particulate matter (PM) is emitted into the atmosphere in the forms of raw PM and partially oxidized PM. Comprehensive investigations of PM oxidation behavior and kinetics contribute to lower PM emission and optimize the PM capture device design. In this paper, diesel PM oxidation behavior was investigated using different temperature control programs, and then the oxidation kinetics was analyzed using the Arrhenius equation. The nanostructure, Fourier transform infrared spectroscopy, and Raman characteristics were adopted to further clarify PM oxidation kinetics. The results indicated that PM oxidation showed multistage reactions, and the reaction rate decreased rapidly in the isothermal process, with the activation energy increasing. Heat transfer limitation significantly decreased the activation energy and also affected the subsequent reactions. In the narrow temperature range (523-537 degrees C), the activation energies of partially oxidized and aging PM were smaller than the values of the initial oxidation stage. The oxidation transformation phase had a huge potential of evolving into heat transfer limitation. The activation energies of partially oxidized and aging PM were smaller than the value of raw PM at the end of oxidation, which was caused by the catalytic reaction of metal ash. The diesel PM nanostructure changed from the onion-like to the core-shell-like structures after partial oxidation.
Diesel particulate matter (PM) was collected at different tailpipe positions where the sampling temperature was different. The PM samples were pre-treated in air at high temperature until 40% mass loss. Then, the partially oxidized PM samples were aged in air for 40 days, and the physicochemical properties of partially oxidized PM before and after aging in air were tested. The results showed that the oxidation activity of partially oxidized PM was appreciably restored by aging in air. The morphology, diameter distribution of primary particles and nanostructures of partially oxidized PM changed slightly after aging in air. The amorphous carbon adsorbing on PM surface were faintly observed through high resolution transmission electron microscope (HRTEM) images. The adsorption of oxygen-containing functional groups (carbonyl and hydroxy) and organic compounds were evidenced through Fourier transform infrared spectroscopy (FTIR) and Raman parameter AD3/AG. The crystallite size calculated using Raman parameter decreased slightly after aging in air.
In this paper, a hybrid combustion mode in four-stroke gasoline direct injection engines was studied. Switching cam profiles and injection strategies simultaneously was adopted to obtain a rapid and smooth switch between SI mode and HCCI mode. Based on the continuous pressure traces and corresponding emissions, HCCI steady operation, HCCI transient process (combustion phase adjustment, SI-HCCI, HCCI-SI, HCCI cold start) were studied. In HCCI mode, HCCI combustion phase can be adjusted rapidly by changing the split injection ratio. The HCCI control strategies had been demonstrated in a Chery GDI2.0 engine. The HCCI engine simulation results show that, oxygen and active radicals are stored due to negative valve overlap and split fuel injection under learn burn condition. This reduces the HCCI sensitivity on inlet boundary conditions, such as intake charge and intake temperature. The engine can be run from 1500rpm to 4000rpm in HCCI mode without spark ignition. The COV of IMEP within and among cylinders are less than 2%. NOx emission is from 0.1 to 2 g/kW.h before TWC. The lowest BSFC is 240g/kW.h at 2000r/min. © 2008 SAE International.
The proposed study aims to evaluate the feasibility of a range extender scroll engine by means of an analytical heat release rate analysis. This novel engine technology is comprising an upstream compressor and a downstream scroll expander which is mechanically connected and drives the compressor. Hence, the compression and expansion processes of the air-fuel mixture are decoupled which enables the possibility to apply higher expansion than compression ratios resulting in a scroll engine combustion process being similar to the Miller or Aktinson cycle. The scroll engine performance in terms of power output and thermal efficiency was accordingly evaluated for two compression ratios of 8.2:1 and 10.1:1 and six corresponding expansion ratios in the range of 8.2:1 to 17.8:1. It has been proven that high compression ratios are beneficial for the power output as more fuel can be introduced into the expander part. At a constant compression ratio, the power output increased for a rising expansion ratio but at the expense of a reduced power density. The evaluation revealed a peak value of 44.48kW at a compression ratio of 10.1:1 and an expansion ratio of 17.8:1. A more thorough expansion process due to the implementation of a Miller/Aktinson cycle resulted in a significantly increasing thermal efficiency for a rising ratio of expansion to compression ratio reaching a peak value
Diesel particulate matter (PM) samples were collected at different tailpipe positions where sampling temperature differed greatly. All the samples were pre-heated in air at high temperature until 40% mass was burnt out. Physicochemical properties of diesel PM both before and after partial oxidation were analyzed, and to further figure out the reasons of oxidation activity changes in the oxidation process. The results showed that ignition temperature of PM whose sampling temperature was higher than 208 °C differed greatly from PM sampled below that temperature. After partial oxidation, sample 3 presented the hugest oxidation activity decreasing with burn out temperature increasing by 14.7 °C. Primary particle size distribution shifted to smaller diameter direction after partial oxidation, and particle stacking degree decreased evidently. Nanostructures of diesel PM transferred from onion like structures with randomly arranged crystallite to core-shell like structures with void inner cores. Oxygen-containing functional groups (carbonyl and hydroxy) decreased evidently after PM partial oxidation that was obtained from Fourier transform infrared spectroscopy (FTIR) spectra, it was consistent with the results of Raman parameter ID3/IG.
High power density of opposed rotary piston (ORP) engines provides a possibility for the applications to hybrid vehicles. Under real driving conditions, internal combustion engines as the power sources of hybrid vehicles run under part load conditions in majorities of operation time. Hydrogen applications in internal combustion engines will promote zero-carbon travel, contributing to alleviating global warming. In this investigation, 3D numerical simulations were conducted to explore the performance of an ORP engine fuelled with hydrogen under part load and various ignition timing conditions. The results indicated that peak in-cylinder pressure and corresponding crank angle (CA) changed slightly within the early ignition range of −20.85º CA~ −14.23º CA; peak in-cylinder pressure was decreased significantly by late ignition. Heat release rates were more sensitive to late ignition than early ignition. Start of combustion, combustion phase, and combustion durations presented minor impacts by early ignition and engine loads. Ignition timing of −20.85º CA~ −11.06º CA showed limited impacts on indicated mean effective pressure and indicated power over individual intake manifold pressure. Indicated thermal efficiency was around 40% for the ignition timing of −20.85º CA~ −11.06º CA over the intake manifold pressure of 0.8 bar; indicated thermal efficiency drop caused by ignition timing of −8.33º CA was higher than 7% compared with optimal conditions. Heat loss by cylinder walls in proportions of fuel energy was lower than 25%, 20%, 18% for the intake manifold pressure of 0.4 bar, 0.6 bar, 0.8 bar respectively. Energy loss by the exhaust was higher than 41% for all the scenarios, with the maximum value being approximately 57%. Nitrogen oxides (NOx) emission factors were higher than 11 g (kW h)−1, and they were increased significantly by early ignition. [Display omitted] •Spark plugs layout led to special combustion characteristics and engine performance.•In-cylinder pressure evolutions were dependent less on early ignition timing.•Combustion durations presented the smallest value over ignition timing of −11.06º CA.•Exhaust energy accounted for higher than 41% of the total fuel chemical energy.•NOx were higher than 11 g (kW h)−1, being increased greatly by early ignition.
Understanding the physicochemical properties of aged soot particles is crucial for enhancing diesel particulate filter (DPF) regeneration strategies. This study examines the physicochemical properties of such soot subjected to both non-catalytic and CeO2-catalytic aging, utilizing a fixed bed test bench where soot samples are aerobically aged at 300–500 °C for 30–90 min before being cooled to ambient temperature under anaerobic conditions. The results indicate that sequential aging at 300–400 °C has minimal impact on soot oxidation activity, with a slight reduction in ignition temperature compared to nascent soot. Concurrently, there is a notable decrease in soot agglomeration, resulting in reduced macropore sizes ranging from 100 nm to 210 nm. The effects of non-catalytic and catalytic aging on soot oxidation activity diverge significantly at 500 °C. The crystallite arrangement in the soot particles takes precedence over oxidation activity, despite the formation of numerous pores post aging above 400 °C. Graphitization in non-catalytically aged soot increases, whereas it decreases following catalytic sequential aging. Post sequential aging at temperatures ranging from 300 to 500 °C, a noticeable shift occurs in soot particles, characterized by the depletion of C=O functional groups and concurrent emergence of C-O functional groups. Moreover, the presence of catalysts during this aging process markedly enhances the reduction of C=O functional groups.
Automotive polymer electrolyte membrane fuel cell systems are attracting much attention, driven by the requirements of low automotive exhaust emissions and energy consumption. A polymer electrolyte membrane fuel cell system provides opportunities for the developments in different types of air compressors. This paper proposed an opposed rotary piston compressor, which had the merits of more compact structures, less movement components, and a high pressure ratio, meeting the requirements of polymer electrolyte membrane fuel cell systems. Preliminary performance evaluations of the opposed rotary piston compressor were conducted under various scenarios. This will make a foundation for optimizations of outlet pipe layouts of the compressor. A three-dimensional numerical simulation approach was used; further, in-cylinder pressure evolutions, fluid mass flow rates, and P–V diagrams were analyzed. It indicated that the cyclic period of the opposed rotary piston compressor was half of reciprocating piston compressors. The specific mass flow rate of the compressor is in the range of 0.094–0.113 kg·(s·L)−1 for the given scenarios. Outlet ports 1 and 2 dominated the mass flow in the discharge process under scenarios 1, 3, and 4. In-cylinder pressure profiles show multipeaks for all of these scenarios. In-cylinder pressure increased rapidly in the compression process and part of the discharge process, which led to high energy consumption and low adiabatic efficiency. The maximum adiabatic efficiency is approximately 43.96% among the given scenarios.
•Starting strategies of free-piston engine generator by linear electric machine is investigated.•A novel method to start the engine by mechanical resonance is proposed.•A detailed comparison of the implementation of open-loop and close-loop strategies.•A detailed discussion of how the motor force can influence the starting process and the following combustion process. Two general methods to start the engine are investigated by the linear electric machine operating as a linear motor and identified one for a specific FPEG prototype configuration. Based on that, a novel method to start the engine by mechanical resonance is proposed. Both simulation and test results are presented, and the numerical model is successfully validated. The results show that with a fixed motor force of 110N, within 0.5s, the maximum in-cylinder pressure could reach 13bar, indicating that the engine is ready for ignition. Further investigation on the engine performance with the closed-loop control strategy is carried out. The results demonstrate that it is feasible to start the FPEG with mechanical resonance with a closed-loop controlled electric linear machine that applies a proper constant motor force in the direction of the natural bouncing motion. With different starting motor force, the top dead centre (TDC) value for both cylinder is different during the first few running cycles, but the difference reduces and tends to be zero during the stable resonance state. There is not any significant difference observed on the engine frequency and piston profile during combustion process.
The increase in worldwide greenhouse gas emissions and costs for fossil fuels are forcing fuel suppliers and engine manufacturers to consider more sustainable alternatives for powering internal combustion engines. One very promising equivalent to mineral diesel fuel is hydrotreated vegetable oil (HVO) as it is highly paraffinic and offers similar combustion characteristics. This fuel offer the potential of not requiring further engine hardware modification together with correspondingly lower exhaust gas emissions and better fuel consumption than mineral diesel. In this paper the spray and combustion characteristics of HVO and its blends are investigated and compared with mineral diesel (European standard). Evidence of the reported reductions in NOx emissions has proven contradictory with some researchers reporting large reductions, whilst others measured no differences. This paper reports the results from comparison of three different experimental tests methods using diesel/HVO binary fuel blends. The macroscopic spray characteristics have been investigated and quantified using a constant volume spray vessel. Engine performance and exhaust emissions have also been characterised using a HD diesel engine in its original configuration (mineral diesel fuel-ready) and then in a recalibrated configuration optimised for HVO fuel. The results show that the engine injection control and also the fuel quality can influence the formation of NOx and particulate matter significantly. In-particular a potential pilot injection proved highly influential upon whether NOx emissions were reduced or not. When optimising the fuel injection, a reduction in NOx emissions of up to 18% or reductions of PN of up to 42–66% were achieved with simultaneous savings in fuel consumption of 4.3%.
The hybrid combustion mode is an ideal operation strategy for a gasoline homogeneous charge compression ignition (HCCI) engine. A stable and smooth spark ignition (SI)/HCCI switch has been an issue in the research on multimode combustion. In this paper, the switch process has two key issues; the cam profile and throttle opening. With the developed two-stage cam system, the valve phase strategy can be switched within one engine cycle, from the normal cam profile for the SI mode to a negative valve overlap (NVO) profile for the HCCI mode, or vice versa. For a smoother and more stable switch, the throttle change was separated from the cam profile switch, which was called the stepped switch. The effect of throttle opening on HCCI combustion was studied, and the results showed that the concept of the stepped switch was reliable. With gasoline direct injection (GDI) the combustion mode switches from both SI and HCCI sides were smooth, rapid, and robust, without any abnormal combustion such as knocking and misfiring.
A wide literature has demonstrated that internal combustion engines are the main responsible for the emission of fine particles in urban areas. Within this scope, ultrafine particles within diesel exhausted gas have been widely proven to exert a significantly harmful impact on human health and environment. This scenario has led the research community to turn the attention from particle mass to diameter and surface area. In this paper, non-thermal plasma (NTP) technology was applied to a heavy duty diesel engine. Chemical reactions of diesel particles in plasma zone were analyzed. Additionally, variation in diesel particles’ number and surface area distributions, engendered by above reactions, were thoroughly investigated. The results showed that diesel exhausted particles experienced oxidation, aggregation, and crush because of enhanced plasma transports and active species in plasma zone. NTP presents excellent reduction effectiveness of diesel particles covering different sizes. Being more than 50%, the most considerable surface area concentration drop was found in correspondence of 1800 RPM. Differently, the lowest drop of surface area concentration was seen at 1200 RPM. As a result of the NTP actions, surface area concentration distributions were almost the same for diameters being larger than 0.5 μm at different engine modes, except at 900 RPM. This research made a foundation of dropping particle emissions and evaluating the effectiveness of NTP dropping particle harms to human health. [Display omitted] •Particle number concentration decreased significantly regardless of particle sizes.•Breakup, oxidation, accumulation of diesel particles happened in plasma zone.•SA concentration of accumulation mode particles was huger than nucleation mode.
To solve the problems of easy leakage and weak thermal conductivity of single-phase change material, in this experiment, cobalt/nitrogen-doped ZIF-67 derived carbon (CoN-ZIF-C x ) was constructed as the carrier material, and paraffin was used as the phase change core material to construct thermally enhanced shaped composite phase change materials (P 0.6 @CoN-ZIF-C x ). The composite PCMs were characterized using scanning electron microscopy, isothermal nitrogen adsorption–desorption, X-ray diffraction, and Fourier infrared spectroscopy, and their performance was evaluated using transient planar heat source techniques, differential scanning calorimetry, and thermal cycling tests. The results indicated that the impurities of the acid-washed porous carbon material were reduced and the loading of the paraffin was 60%, and the prepared P 0.6 @CoN-ZIF-C x had an excellent thermal performance. Among them, P 0.6 @CoN-ZIF-C3 has the melting and crystallization enthalpy of 71.03 J g −1 and 68.81 J g −1 . The thermal conductivity is 0.4127 W m −1 K −1 , a 46.19% thermal conductivity improvement compared with pure paraffin. It still has favourable thermal storage capacity after 50 cycles without paraffin leakage during the phase transition. The cobalt/nitrogen-doped ZIF-67 derived carbon (CoN-ZIF-C x ) was constructed as the carrier material, and paraffin was used as the phase change core material to construct thermally enhanced shaped composite phase change materials.
Dual-injection strategies in spark-ignition engines allow the in-cylinder blending of two different fuels at any blend ratio, when simultaneously combining port fuel injection (PFI) and direct-injection (DI). Either fuel can be used as the main fuel, depending on the engine demand and the fuel availability. This paper presents the preliminary investigation of such a flexible, bi-fuel concept using a single cylinder spark-ignition research engine. Gasoline has been used as the PFI fuel, while various mass fractions of gasoline, ethanol and 2,5-dimethylfuran (DMF) have been used in DI. The control of the excess air ratio during the in-cylinder mixing of two different fuels was realized using the cross-over theory of the carbon monoxide and oxygen emissions concentrations. The dual-injection results showed how the volumetric air flow rate, total input energy and indicated mean effective pressure (IMEP) increases with deceasing PFI mass fraction, regardless of the DI fuel. The indicated efficiency increases when using any ethanol fraction in DI and results in higher combustion and fuel conversion efficiencies compared to gasoline. Increasing the DMF mass fraction in DI reduces the combustion duration more significantly than with increased fractions of ethanol or gasoline in DI. The hydrocarbon (HC), oxides of nitrogen (NOx) and carbon dioxide (CO2) emissions mostly reduce when using any gasoline or ethanol fraction in DI. When using DMF, the HC emissions reduce, but the NOx and CO2 emissions increase. © 2011.
Energy saving and emission reduction of engines were taken seriously, especially for vehicular diesel engines. Exhaust heat recovery based on organic Rankine cycle (ORC) system has been considered as an effective approach for improving engine fuel economy. This article presents the investigation of water or air cooling method for an ORC exhaust heat recovery system on a heavy duty truck through simulations. The models of the truck engine and the ORC system were developed in GT-suite, and the integration system model was developed in the Simulink environment. The validity of the models was verified experimentally. The performance of the vehicular engine with ORC system using water or air cooling method was comparatively analyzed. The simulation results indicated that water cooling method is more suitable for the vehicular ORC system than air cooling method. The relation between benefit and penalty of the ORC system and cooling system was discussed. The operating condition of the cooling system was confirmed having significant effects on the combined system performance, especially the fan speed. The performance improvement of the engine with the use of ORC system was further evaluated under different engine operating conditions and ambient temperatures. Lower ambient temperature had positive impacts on the engine fuel economy. The mass flow rate of exhaust gas for heat recovery should be regulated for better performance under high ambient temperature.
•Analysis of combustion status under different speeds, torques and oil temperatures.•Study on the spectrum characteristic analysis of block vibration.•Time-frequency characteristics of block vibration at different combustion status.•Correlation analysis between WPD result and combustion status. The correlation between the combustion status and block vibration was studied at different engine speed, torque and oil temperature conditions. The frequency components lower than 8 kHz had a similar change trend with the peak value of combustion pressure at different speed conditions. The frequency components from 8 kHz to 25 kHz increased with engine speed and these frequency components were mainly affected by the inertia force. The spectrum energy of frequency components increased with engine torque due to the increase of combustion pressure. The maximum spectrum energy of frequency components below 20 kHz didn’t show a particular trend due to the opposite effects caused by combustion pressure and oil damping at different oil temperatures. The frequency components higher than 20 kHz increased with the increase of oil temperature, which meant the frequency components were more sensitive to the oil damping.
•Backfire origins of hydrogen fuelled engines are comprehensively reviewed.•Backfire control technologies of hydrogen engines are detailed discussed.•Correlations between various backfire origins are analyzed.•Different backfire control technologies are recommended adopting jointly. Hydrogen fuel applications in internal combustion engines have attracted increasing attention due to zero carbon emission and excellent combustion characteristics in terms of thermal efficiency. Internal combustion engines fuelled with hydrogen are demonstrated to have higher brake thermal efficiency than other fossil fuel cases. However, abnormal combustion such as backfire in port hydrogen injection engines limits the improvement of internal combustion engine performance resulting from low ignition energy and high flame propagation velocity of hydrogen fuel. Volumetric efficiency drops significantly if backfire occurs; moreover, it brings about damages to the intake systems and fuel injection systems. Backfire is induced by high temperature residual exhaust gas, hot spots, and abnormal discharge of spark plugs; all the factors causing pre-ignition of hydrogen-air mixture promote the backfire occurrences. This paper reviews the factors tending to induce backfire, such as improper intake valve timing and fuel injection timing, and high fuel-air equivalence ratios; additionally, the corresponding backfire control strategies are analyzed with advantages and disadvantages being discussed. The factors leading to backfire are mainly caused by large amounts of residual exhaust gas, extremely slow combustion, and improper hydrogen distributions around intake valve seats. Backfire control strategies have specific application conditions to ensure their effectiveness, beyond which they will generate negative impacts on backfire control effectiveness. Power loss is nearly inevitable for naturally aspirated engines when backfire control strategies are adopted. Multiple control strategies are recommended to ease the engine performance drop caused by backfire control; meantime, multi-objective optimizations are suggested to achieve the optimal global performance.
•Heat generation of Lithium ion batteries and consequences of thermal instability.•Capability of heat pipes in maintaining thermal stability of Li-ion cells.•Gaps in heat pipe based battery thermal management.•Current status, challenges and future direction of heat pipe based battery thermal management. Heat pipes are currently attracting increasing interest in thermal management of Electric vehicle (EV) and Hybrid electric vehicle (HEV) battery packs due to its superconductive capability, robustness, low maintenance and longevity. With the focus of battery thermal management directed towards both convective and conductive cooling, a significant number of research, both experimental and numerical investigations have been performed during the past decade. However, heat pipe based battery thermal management systems (HP-BTMS) are yet to be commercialized due to lack of understanding their limitations during rapid heat fluctuations and adverse environmental conditions, performance under multiple heat loads, failure criteria in the context of battery thermal management and lack of simple and versatile thermal models to accurately predict the battery thermal performance at module and pack level. This comprehensive review highlights the different heat generation mechanisms of Li-ion batteries and their resulting consequences, followed by the operating principles of heat pipes along with background and shortcomings related to heat pipe based battery thermal management, for the mere purpose of further development of this promising thermal management system. Different heat pipe based thermal management systems developed during the last decade along with their modelling approaches, including the methods adopted for enhancing heat transfer are critically analysed. Heat pipes have demonstrated to be an effective approach in maintaining optimum cell surface temperature, however, several areas require attention if this system is to be commercialized. Niche types of heat pipes such as pulsating heat pipes, loop heat pipe, mini/micro heat pipe have also been reviewed and their advantages, disadvantages, and challenges in the context of BTMS are discussed. Finally, the current status, challenges and prospects of the future direction in HP-BTMS are highlighted.
Scroll expander has demonstrated high efficiency at low power range. In this paper, a generic model of a scroll expander has been developed. It can calculate the ideal expander parameters to give the optimal efficiency and prevent under- or over-expansion at any given operating conditions or fluids. The dynamic model was validated by predicting the ideal volumetric expansion ratio with ideal expansion ratio of 4.03 at 0.7 MPa pressure, and showed agreement with experimental data. The results suggested that the rate of scroll increase K in the geometric model has little effect on volumetric expansion ratio or ideal scroll length of the expander, but when expansion ratio is kept constant, lower K value results in lower leakage losses. Crown Copyright (C) 2015 Published by Elsevier Ltd.
Polypropylene is the most common type of plastic found in municipal solid waste. The production of polypropylene is expected to increase due to the widespread utilization in daily life, resulting in even higher amounts of polypropylene waste. Sending this plastic to landfill not only exacerbates environmental problems, but also results in energy loss due to the elevated energy content of polypropylene. Pyrolysis is a process that can effectively convert polypropylene waste into fuel, which can then be used to generate power and heat. In the present study, the ect of the pyrolysis temperature on the pyrolysis of polypropylene was investigated, and the oils produced at 700oC (PP700) and 900oC (PP900) were used to fuel a four cylinder diesel engine. The engine's combustion, performance and emission characteristics were analysed and compared to diesel operation. The results showed that both PP700 and PP900 enabled stable engine operation, with PP900 performing slightly better in terms of efficiency and emissions. However, PP700 and PP900 were found to have longer ignition delay periods, longer combustion periods, lower brake thermal efficiencies, higher NOX, UHC and CO emissions, and lower CO2 emissions in comparison to diesel operation. Nonetheless, the addition of a small quantity of diesel improved the overall performance of the oil blends, resulting in comparable results to diesel in the case of PP900.
For spark ignition (SI) engines, the optimum spark timing is crucial for maximum efficiency. However, as the spark timing is advanced, so the propensity to knock increases, thus compromising efficiency. One method to suppress knock is to use high octane fuel additives. However, the blend ratio of these additives cannot be varied on demand. Therefore, with the advent of aggressive downsizing, new knock mitigation techniques are required. Fortuitously, there are two well-known lower alcohols which exhibit attractive knock mitigation properties: ethanol and methanol. Both not only have high octane ratings, but also result in greater charge-cooling than with gasoline. In the current work, the authors have exploited these attractive properties with the dual-injection, or the dual-fuel concept (gasoline in PFI and fuel additive in DI) using pure ethanol and methanol. The single cylinder engine results at 1500 rpm (λ=1) show benefits to indicated efficiency and emissions (HC, CO and CO2) at almost every load (4.5 bar to 8.5 bar IMEP) compared to GDI. This is because the spark timing can be significantly advanced despite the use of relatively low blends (≤50%, by volume), which lowers the combustion duration and improves the conversion of fuel energy into useful work. Overall, these results reinforce the potential of the dual-injection concept to provide a platform for aggressive downsizing, whilst contributing to a renewable energy economy. Copyright © 2012 SAE International.
Particulate matter (PM) emitted by internal combustion engines has brought about serious environmental problems. Investigations of the PM oxidation behaviors and kinetics make the foundations of decreasing PM emission and working out the regeneration problems of PM capture devices. In this paper, the oxidation kinetics and microstructure evolutions of diesel PM in the oxidation process were researched. The results showed that thermogravimetric analysis (TGA) temperature history had a limited influence on the tendency of the oxidation kinetics. The volatilization of the organic compounds dominated the mass loss without any heat release at the initial stage of PM oxidation. The abnormal phenomenon (negative apparent activation energy) was observed in the oxidation process when the oxidation temperature was in the range of 200 °C–340 °C, which was ubiquitous during PM oxidation. However, the abnormal phenomenon disappeared if the PM sample was pre-treated to remove the volatile organic compounds (VOC), with the result that the phenomenon was caused by the VOC. The hydrogen bonding complex was formed in that temperature range, where the energy of the hydrogen bonding complex was lower than the value of the reactants, which caused the negative apparent activation energy. The apparent activation energy increased gradually when the temperature was higher than 340 °C.
Opposed rotary piston (ORP) engines have advantages of high power density, few moving parts, and smooth operations, which makes ORP engines as potential power sources for hybrid vehicles and range extended electric vehicles. Ignition timing significantly affects the performance of spark ignition engines including fuel economy and emission factors. In this paper, the effect of ignition timing on the engine performance was investigated using a three-dimensional numerical simulation method. The results indicated that crank angle corresponding to the peak in-cylinder pressure over the ignition timing of −8.2° crank angle (CA) was advanced compared with other cases having earlier ignition timing; however, the crank angle of peak heat release rates were retarded. Start of combustion was delayed by retarding the ignition timing and increasing engine speed; combustion duration over the ignition timing of −18.9° CA ~ −11.1° CA changed slightly for individual engine speed. Indicated specific fuel consumption (ISFC), being hardly dependent on the ignition timing, was less than 74 g/(kW·h) over the ignition timing of −17.3° CA ~ −11.1° CA, where indicated thermal efficiency was approximately 41%, 39% and 35% for 1000 RPM, 3000 RPM and 5000 RPM respectively. When ignition timing was later than −11.1° CA, ISFC and indicated thermal efficiency were deteriorated seriously. Nitrogen oxides (NOx) emission factors increased with engine speed over early ignition timing; however, they were inverse for late ignition cases. Higher engine speed and retarded ignition timing led to higher percentage of exhaust energy in fuel chemical energy.
Plastic waste is an ideal source of energy due to its high heating value and abundance. It can be converted into oil through the pyrolysis process and utilised in internal combustion engines to produce power and heat. In the present work, plastic pyrolysis oil is manufactured via a fast pyrolysis process using a feedstock consisting of different types of plastic. The oil was analysed and it was found that its properties are similar to diesel fuel. The plastic pyrolysis oil was tested on a four-cylinder direct injection diesel engine running at various blends of plastic pyrolysis oil and diesel fuel from 0% to 100% at different engine loads from 25% to 100%. The engine combustion characteristics, performance and exhaust emissions were analysed and compared with diesel fuel operation. The results showed that the engine is able to run on plastic pyrolysis oil at high loads presenting similar performance to diesel while at lower loads the longer ignition delay period causes stability issues. The brake thermal efficiency for plastic pyrolysis oil at full load was slightly lower than diesel, but NOX emissions were considerably higher. The results suggested that the plastic pyrolysis oil is a promising alternative fuel for certain engine application at certain operation conditions.
Opposed rotary piston (ORP) engines are characterized by high power density, compact designs, and smooth operations which meet the requirements of the power source for hybrid vehicles. Hydrogen fuel applications will fully present ORP engines' advantages due to the short cyclic period. Internal combustion engines mainly operate under part load conditions over real world driving, the performance of hydrogen ORP engines over part load needs to be addressed in order to promote the applications to hybrid vehicles. In this paper, combustion and nitrogen oxides emission of this ORP engine under part load and stoichiometric conditions were investigated using a 3D numerical simulation approach. The results indicated that peak in-cylinder pressure during combustion was significantly dependent on the intake manifold pressure, and the corresponding crank angle (CA) was almost kept the same for 1000 RPM and 3000 RPM. Heat release rates for hydrogen combustion presented double-peak under high intake manifold pressure scenarios. Combustion durations over 1000 RPM increased with intake manifold pressure; however, they changed slightly for 3000 RPM. Nitrogen oxides (NOx) emission concentration increased with intake manifold pressure for 3000 RPM and 5000 RPM; however, intake manifold pressure of 0.6 bar presented the highest value for 1000 RPM. Indicated thermal efficiency was higher than 30% for 1000 RPM and 3000 RPM; and the minimum value was approximately 21% over 5000 RPM and 0.4 bar. (C) 2021 Elsevier Ltd. All rights reserved.
Compact and high power density internal combustion engines are attracting much attention for the applications to hybrid vehicles, aiming at decreasing fuel consumption and exhaust emissions. A novel opposed rotary piston engine, whose cyclic period is 360° crank angle, is designed as the power of hybrid vehicles. Intake process of the internal combustion engines significantly affects brake thermal efficiency and rated power. In this paper, 3D simulation of a opposed rotary piston engine is conducted over different engine speeds of 3000 and 5000 RPM, in order to analyze the intake characteristics and pumping loss in the intake stroke. The results indicate that the in-cylinder pressure distributions change significantly in the intake process, which results from the variations of cylinder volume and fresh air flow rates. The minimum in-cylinder pressure is approximately 0.3 and 0.2 bar for 3000 and 5000 RPM, respectively, with the combustion chamber volume being ~0.04 L correspondingly. The maximum velocity of the fresh air in the intake process is higher than 150 m/s. Intake ports 2 and 3 dominate the mass flow of the combustion chambers, in addition, the contribution of mass flow from intake port 1 decreases with the engine speed. The pumping loss in the intake process increases from 1.35 to 4.39 kW when the engine speed increases from 3000 to 5000 RPM.
Hydrogen internal combustion engines are attracting increasing attention because of no carbon dioxide (CO2) emission and high thermal efficiency for hydrogen combustion. Opposed rotary piston (ORP) engines have simple structures, small size and mass, contributing to the performance improvement of hybrid electric vehicles (HEVs) and range extended electric vehicles (RE-EVs). Compression ratios as an important factor affecting engine performance should be considered in the process of engine designs and optimizations. In this paper, in-cylinder combustion characteristics of a small-scale ORP engine were investigated using a numerical simulation method over different compression ratios (8.90, 9.66, and 10.55). Compression ratio adjustment of the ORP engine may be achieved by the movement patterns of the two shafts. The results indicated that maximum in-cylinder pressure was increased from approximately 3.5 MPa–5.0 MPa when the compression ratios were increased from 8.90 to 10.55. The crank angle (CA) of the maximum in-cylinder pressure was slightly retarded by increasing compression ratios. The hydrogen combustion rates were almost the same before top dead centre (TDC) for the three cases. The combustion durations were dropped from approximately 38.7 °CA to 28.3 °CA when the compression ratios were increased from 8.90 to 10.55; however, the combustion phase of the compression ratio of 9.66 was the earliest among the three cases. The proportions of energy loss by cylinder walls were almost the same under different compression ratios, being approximately 10%; additionally, the indicated thermal efficiency was increased from approximately 34%–39% by changing compression ratios from 8.90 to 10.55. The nitrogen oxides (NOx) emission factors of the ORP engine were almost linearly increased by increasing compression ratios, with the values being higher than 17.2 g/kWh for all the three cases. NOx distributions in combustion chambers around 50 °CA after TDC agreed well with those of in-cylinder temperature and hydrogen residuals.
Catalytic converters mitigate carbon monoxide, hydrocarbon, nitrogen oxides and particulate matter emissions from internal combustion engines, and allow meeting the increasingly stringent emission regulations. However, catalytic converters experience light-off issues during cold start and warm up. This paper reviews the literature on the thermal management of catalysts, which aims to significantly reduce the light-off time and emission concentrations through appropriate heating methods. In particular, methods based on the control of engine parameters are easily implementable, as they do not require extra heating devices. They present good performance in terms of catalyst light-off time reduction, but bring high fuel penalties, caused by the heat loss and unburnt fuel. Other thermal management methods, such as those based on burners, reformers and electrically heated catalysts, involve the installation of additional devices, but allow flexibility in the location and intensity of the heat injection, which can effectively reduce the heat loss in the tailpipe. Heat storage materials decrease catalyst light-off time, emission concentrations and fuel consumption, but they are not effective if the engine remains switched off for long periods of time. The main recommendation of this survey is that integrated and more advanced thermal management control strategies should be developed to reduce light-off time without significant energy penalty.
In this paper, the macroscopic spray characteristics of four next-generation biofuels, namely, hydrotreated vegetable oil (HVO), Palm oil methyl ester (PME), Soybean oil methyl ester (SME) and used cooking oil methyl ester (UCOME) were investigated in detail using a constant volume spray vessel, and benchmarked against reference mineral diesel (B0). During experiments, fuels were heated to 80 °C to achieve an engine-like environment before being injected at various compression ignition engine relevant operating conditions. The fuel spray tip penetration, spray cone angle and spray area were investigated analysing images obtained using a direct photography technique. Furthermore, a modified spray model was proposed to extend its scope to include alternative fuels by considering fuel density as part of the spray model. The results show that HVO with the lowest density of all fuels achieves the shortest penetration distance and the highest cone angle, resulting in a more distributed fuel-air mixture. All fuels have very similar spray areas for the same injection conditions, but the specific spray area per injected mass is highest for HVO followed by the three methyl esters. It was concluded that the fuel liquid viscosity was a significant factor on the observed air-fuel mixing process. The spray characteristics were compared with our engine test results and can be used to explain observed engine behaviour when fuelled with biofuels.
Global concerns over atmospheric carbon dioxide (CO 2) levels and the security of fossil fuel supply have led to the development of biofuels; a potentially carbon-neutral and renewable fuel strategy. One new gasoline-alternative biofuel candidate is 2,5-dimethylfuran (DMF). In this paper, the potential of DMF is examined in a direct-injection spark-ignition (DISI) engine. Focus is given to the combustion performance and emissions sensitivity around the optimum spark timing, especially at 10 crank angle degrees retard (SR10). Such spark retard strategies are commonly used to reduce catalyst light-off times, albeit at the cost of reduced engine performance and increased CO 2. The results for DMF are compared to gasoline, ethanol, butanol and methanol so that its sensitivity can be positioned relatively. The overall order of spark sensitivity at the highest load (8.5 bar IMEP) was: gasoline > butanol > DMF > ethanol > methanol. The four biofuels widen the spark window due to improved anti-knock qualities and sometimes increased charge-cooling. This allows the increase of CO 2 to be better minimized than with gasoline. Furthermore, DMF is the only biofuel to produce high exhaust gas temperatures, similar to gasoline and helpful for fast catalyst light-off, whilst maintaining high combustion stabilities. This demonstrates the potentially favorable characteristics of DMF to become an effective cold-start fuel. © 2012 Elsevier Ltd. All rights reserved.
This paper presents a case study of a live combined heat and power (CHP) system at the author's university campus. The system comprises a 1 MWe gas engine which is operating continuously to provide electricity, as well as a heat recovery system that recovers heat from both engine jacket water and exhaust gas to provide heat to the campus. The analysis shows that the electricity generation is stable during the year but the heat recovered fluctuates considerably at different time of the year due to the different heat demand. This results in an inefficient use of the available energy. Exergy analysis is conducted for a better understanding of the components performance of the system. An absorption chiller is finally proposed to make a better utilization of the energy and the pay-back time for the chiller is found to be approximately 22 months which is economically viable.
The scroll-type expander can be the promising candidate for micro-scale (
The built-in volume ratio of variable wall thickness scroll expanders can be increased without increasing the number of scroll turns and the expander size in contrast to constant wall thickness expanders. CFD models for these novel scroll-type designs are presented in this research paper. The validation, verification and the findings have proven consistency with the theory of small scale ORC scroll expanders. The performance analysis indicates that the optimum performance point was reached at a pressure ratio of 3.5. The decrease of radial clearance from 200μm to 75μm had a significant effect on the isentropic efficiency and the specific power output, with the isentropic efficiency significantly increasing from 31.9% up to 53.9%. Based on the second-law analysis, it is found that exergy of 336.5W (75μm) and 864.2W (200μm) were destroyed during the expansion processes. Furthermore, characteristic pressure imbalances were observed in the expansion chambers. The studies also reveal that the large-scale vortices, generated during the suction process, were completely dissipated in the expansion chambers at a crank angle of 600°. Analysis of the pressure-volume diagram shows that variable wall thickness scroll expanders with built-in volume ratios above 4.5 could fully expand the working fluid to the defined outlet pressure.
Scroll expanders are currently attracting interest for integration in small scale organic Rankine cycle (ORC) waste heat recovery applications and have been subject to significant research over the last two decades. The most common geometrical design uses a scroll profile generated by the involute of a circle with a constant wall thickness. A major disadvantage of this approach is that the increase of the geometric expansion ratio is constrained, since it is accompanied with a large increase in the scroll profile length and is associated with a decreased efficiency. In this paper, the published literature related to scroll expander geometry is reviewed. Investigations regarding the influence of varying scroll geometrical parameters on the performance of scroll expanders with a constant wall thickness are first examined. The use of variable wall thicknesses and their effects on the performance are then considered. Finally, the impact of scroll expander geometries using unconventional scroll profiles and scroll tip shape variations on the performance is discussed and summarised. The major conclusion to be drawn from this review is that scroll expanders with variable wall thickness scrolls should be further designed and developed. It is possible to increase the geometric expansion ratio without increasing the length of the scroll profiles. CFD simulations are a promising tool to illustrate and understand the non-uniform and asymmetric inner flow and temperature fields. The related benefits could lead to scroll devices with variable wall thickness not only improving the performance of organic Rankine cycle (ORC) systems but also opening a broad new field of applications such as refrigeration cycles and other power cycles where a high pressure ratio is preferred.
Transcritical carbon dioxide waste heat recovery systems and the construction of scroll expanders have recently been hot topics. The flank clearance, located between the orbiting and fixed scroll, has a vital impact on the scroll expander performance. This paper estimates the effect of the flank clearance on the expander’s thermodynamic performance (first-law efficiency) based on computational fluid dynamics (CFD) simulations. The manufacturing cost of different flank clearances is also considered to enhance the feasibility of the machinery design. The computational cost for different flank clearance cases is significantly reduced with a surrogate-assisted multi-objective optimisation algorithm (SAMOA), which also supports modelling the trade-off relationship between manufacturing cost and machinery efficiency. The results indicated that an increasing flank clearance negatively affects the first-law thermal efficiency. The efficiency decreased from 87.41% to 44.83% moving from 20 to 200 μm flank clearances. The SAMOA successfully reduced the computational cost of the dynamic mesh CFD model from 90 h to 15 s with 0.6% discrepancy. The final Pareto solutions presented a clear trade-off relationship between the first-law efficiency and manufacturing cost and promised a diversity of optimum solutions. The “knee points” for the relationship were 25, 55, and 127 μm, which provided flexible clearance choices based on the importance of either machinery efficiency or manufacturing cost.
This paper presents the investigation of engine optimisation when plastic pyrolysis oil (PPO) is used as the primary fuel of a direct injection diesel engine. Our previous investigation revealed that PPO is a promising fuel however the results suggested that control parameters should be optimised in order to obtain a better engine performance. In the present work, the injection timing was advanced, and fuel additives were utilised to overcome the issues experienced in the previous work. In addition, spray characteristics of PPO were investigated in comparison with diesel to provide in-depth understanding of the engine behaviour. The experimental results on advanced injection timing (AIT) showed a reduced brake thermal efficiency and increased carbon monoxide, unburned hydrocarbons and nitrogen oxides emissions in comparison to standard injection timing. On the other hand, the addition of fuel additive resulted in a higher engine efficiency and lower exhaust emissions. Finally, the spray tests revealed that the spray tip penetration for PPO is faster than diesel. The results suggested that AIT is not a preferable option while fuel additive is a promising solution for long-term use of PPO in diesel engines.
It is well known that direct-injection (DI) is a technology enabler for stratified combustion in spark-ignition (SI) engines. At full-load or wide-open throttle (WOT), partial charge stratification can suppress knock, enabling greater spark advance and increased torque. Such split-injection or double-pulse injection strategies are employed when using gasoline in DI (GDI). However, as the use of biofuels is set to increase, is this mode still beneficial? In the current study, the authors attempt to answer this question using two gasoline-alternative biofuels: firstly, ethanol; the widely used gasoline-alternative biofuel and secondly, 2,5-dimethylfuran (DMF); the new biofuel candidate. These results have been benchmarked against gasoline in a single-cylinder, spray-guided DISI research engine at WOT (λ=1 and 1500rpm). Firstly, single-pulse start of injection (SOI) timing sweeps were conducted with each fuel to find the highest volumetric efficiency and IMEP. The resulting optimum SOI timing for gasoline was then used as the first injection (SOI1) with each fuel in the split-injection tests. In this instance, second SOI timing (SOI2) sweeps were made using two split-ratios (SOI1:SOI2 = 1:1 and 2:1). For the single-pulse SOI timing sweeps, the change in IMEP when using ethanol is symmetrical either side of the maximum. However, when using gasoline and DMF, the behavior is asymmetrical, with maximums later and earlier than with ethanol, respectively. For split-injection, the maximum IMEP increases when fuelled with the biofuels, whilst maintaining acceptable engine stability. This increase, however, is much more dependent on SOI2 timing than with gasoline, due to the deterioration of in-cylinder mixing and slower combustion. Copyright © 2012 SAE International.
In this research, a one-way fluid-thermal-solid numerical coupling model of a scroll expander for a waste heat recovery system was developed and used to investigate the deformation of the scroll pair. The pressure and thermal loads were firstly calculated by a CFD model, and the surface pressure and body temperature distributions of the scroll members were used as boundary conditions in the FEM model to obtain the deformation distributions of the scroll parts. Three time instants that may have significant adverse impacts on the maximum forces were selected to determine the most critical time for the occurrence of the maximum deformation of the scroll wraps. The results showed that the deformations induced by inertial force only occurred at the orbiting scroll tail, whereas the deformations in other regions negligible. At the time instants of t/T equaled to 13/15 and 1, the deformations induced by pressure loads had the opposite direction compared to that of the thermal loads and thus the two deformations canceled each other out and the coupling deformations decreased. The deformations induced by pressure loads were less significant than the thermal loads, therefore the coupling deformation was dominated by the thermal loads. The results also confirmed that the critical time at t/T equaled to 7/20 for the occurrence of the largest deformation resulted from the maximum axial forces that were exerted on the fixed scroll.
Recent developments in the field of renewable energy have led to a renewed interest in low-grade heat (< 500 K). The low-grade heat is widely wasted by the lack of efficient heat recovery technologies. It is also limited by the system size, which defines as the micro to small-scale (< 50 kW). Although ORC based unit has been implemented in this field, the CO2 based waste heat recovery units can be more capable in the size construction. The performance of the expander plays a vital role in the system's efficiency. Thus, the current paper provides thermodynamic and CFD analysis of a scroll expander regarding a micro-scale T-CO2 recovery system (< 10 kW) with a 400 K low-grade heat source. In the current CFD model, all the fluid domains were constructed by structural mesh. It also successfully integrated with the thermodynamic table to simulate two-phase T-CO2. This model can be the first scroll expander model for T-CO2 power system and gap the bridge of utilising the scroll machinery in this field. The CFD methodology was successfully validated by the new-built testing platform and previous data. The energy performance of T-CO2 and ORC (R123) based scroll expanders are compared by isentropic and exergy efficiency. The results showed that isentropic and exergy efficiencies of T-CO2 were 7% and 14% higher than the R123. It also identified higher irreversibilities of T-CO2 by the exergy of the working fluids. The pressure and temperature distributions identified the over-expansion and reversed flow characteristics, and the pressure imbalance of the initial expansion chambers denoted the reversed flow.
•Performance of a heavy-duty truck fitted with an on-board ORC system was evaluated.•Effects of condensers with same volume on the system performance were discussed.•Suitable working fluid of on-board ORC exhaust heat recovery system was selected.•Effects of cargo mass on performance of the truck with ORC system were discussed.•Benefit and penalty of the truck integration with ORC system were analyzed. Exhaust thermal energy conversion based on ORC system has been considered as an effective method for improving engine fuel economy. In this paper, the performance of a heavy-duty truck fitted with an on-board ORC exhaust heat recovery system was evaluated through simulations. The models of the truck/engine and the ORC/cooling system were developed in GT-suite and validated experimentally. A coupling model was developed in the Simulink environment. The performance of the engine ORC system using R123 and R245fa was evaluated individually. The performance of the vehicular system with different condensers which have the same volume was also evaluated. The effects of the increased backpressure and weight caused by ORC system on performance of the truck engine were discussed. The benefit and penalty of the on-board system under different engine speed, truck speed and cargo mass conditions were also analyzed. The simulation results indicated that the cargo mass, engine speed, truck speed had significant effects on performance of the truck engine with ORC system. The truck engine had a profit of 3.07kW at the speed of 95km/h under full cargo load condition. While an additional engine power consumption of 0.67kW was required at the truck speed of 30km/h due to the increased weight of the ORC system.
A catalyst is usually coated on Diesel particulate filter (DPF) for assisted regeneration. In this paper, the oxidation activity and pore structure evolutions of soot under the effect of CeO2 are explored. CeO2 effectively increases the oxidation activity of soot and reduces the initial activation energy; in the meantime, the addition of CeO2 changes the soot oxidation mode. Pure soot particles tend to produce the porous structure in the oxidation process. Mesopores promote the diffusion of oxygen, and macropores contribute to reduce the agglomeration of soot particles. Additionally, CeO2 provides the active oxygen for soot oxidation and promotes the multi-point oxidation at the beginning of soot oxidation. With the oxidation proceeding, catalysis causes the collapsion of soot microspatial structures, in the meantime, the macropores caused by the catalytic oxidation are filled by CeO2. It results in the tight contact between soot and catalyst, further promoting the formation of the available active oxygen for soot oxidation. This paper is meaningful to analyze the oxidation mechanism of soot under catalysis, which lays a foundation for improving the regeneration efficiency of DPF and reducing the particle emission. [Display omitted] •Thermogravimetric analysis (TGA) of soot oxidation activity under catalysis.•Pore structure and volume analysis of soot under catalysis.•Analysis of pore and sample surface area.•Differences in oxidation modes of soot under catalysis.
The impetus of the internal combustion engine developments is the reductions of the fuel consumptions and exhaust emissions. Thermal management is an efficient method to decrease the exhaust emissions and enhance fuel economy. In order to further optimize the thermal management of internal combustion engines, a detailed analysis of the energy flow in each component of internal combustion engines is indispensable. In this paper, the test bench of a heavy duty diesel engine was established to obtain the target parameters. The energy distributions in each component of the diesel engine, including compressor, intercooler, shaft power, turbine, coolant and exhaust, were calculated using tested parameters. The lubricating oil consumption was also taken into consideration. In addition, the potential influences of different turbochargers on the total thermal efficiency were analyzed. The results showed that the thermal efficiency of the diesel engine was more than 38% when the engine operated at 50%–100% engine load and 1000 rpm–1700 rpm conditions. The energy loss by coolant was more than 50% of the total fuel energy consumption in the low power output conditions. However, it was lower than 30% in high power output conditions, and the thermal loss was more than 150 kW around rated power conditions. The maximum proportion of the energy being consumed by turbine was ∼10% of the fuel energy; additionally, the exhaust energy distributions changed significantly after the turbine expansion. 1%–3% of the fuel energy was recycled by the turbocharger, then, flowed into the cylinders. The energy loss through the intercooler accounted for ∼6% of the fuel energy. Significant reductions of exhaust emissions and fuel consumptions can be achieved by optimizing the coolant and lubricating oil thermal conditions. Turbochargers presented a huge effect on exhaust temperature distributions at high power output conditions, and the total thermal efficiency changed significantly if all kinds of energy recovery approaches were applied.
2,5-dimethylfuran (DMF) is currently regarded as a potential alternative fuel to gasoline due to the development of new production technology. In this paper, the spray characteristics of DMF and its blends with gasoline were studied from a high pressure direct injection gasoline injector using the shadowgraph and Phase Doppler Particle Analyzer (PDPA) techniques, This includes the spray penetration, droplet velocity and size distribution of the various mixtures. In parallel commercial gasoline and ethanol were measured in order to compare the characteristics of DMF. A total of 52 points were measured along the spray so that the experimental results could be used for subsequent numerical modeling. In summary, the experimental results showed that DMF and its blends have similar spray properties to gasoline, compared to ethanol. The droplet size of DMF is generally smaller than ethanol and decreases faster with the increase of injection pressure. The mean velocity of DMF spray droplets is similar to gasoline and higher than ethanol. Ultimately, the spray characteristics of DMF are better suited to the gasoline engine technology than its counterpart, ethanol. © 2010 SAE International.
This paper presents a theoretical calculation and a preliminary design of a thermal storage system (TSS) for a heavy duty diesel engine, in order to re-utilise the wasted heat from the engine when in operation and reduce the warm-up time, thus reducing the engine emissions and improve the performance. The thermal storage mainly comprises of a heat exchanger filled with phase change material. A group of candidate materials were evaluated and NaOH H2O was selected for the particular application, as its phase change temperature is suitable and latent heat is relatively high. The storage was preliminarily designed considering the size of the engine and the quantity of heat requested, and the improvement of the engine was evaluated. The theoretical calculation suggested that nearly 40% improvement in warm-up time could be achieved with the TSS.
Homogeneous Charge Compression Ignition (HCCI) has challenges of ignition control. In this paper, HCCI ignition timing and combustion rate were controlled by two-stage direct injection (TSDI) strategies on a four-stroke gasoline HCCI engine. TSDI strategy was proposed to solve the two major problems of HCCI application-ignition control and load extension. Both simulation and experiments were carried out on a gasoline HCCI engine with negative valve overlap (NVO). An engine model with detailed chemical kinetics was established to study the gas exchange process and the direct injection strategy in the gasoline HCCI engine with TSDI and NVO. Simulation results were compared with experiments and good agreement was achieved. The simulated and experimental results provided a detailed insight into the processes governing ignition in the HCCI engine. Using TSDI, the fuel concentration, temperature as well as chemical species can be controlled. The effects of different injection parameters, such as split injection ratio and start-of-injection (SOI) timing, were studied. The experimental results indicate that, two-stage direct injection is a practical technology to control the ignition timing and combustion rate effectively in four-stroke gasoline HCCI engines. Both the high load and low load limits of HCCI operation were extended.
In this paper, a multimode combustion system was developed in a gasoline direct injection engine. A two-stage fuel-injection strategy, including flexible injection timings and flexible fuel quantity, is adopted as a main means to form desired mixture in the cylinder. The combustion system can realize five combustion modes. The homogeneous charge spark ignition (HCSI) mode was used at high load to achieve high-power output density; stratified charge spark ignition (SCSI) was adopted at intermediate load to get optimum fuel economy; stratified charge compression ignition (SCCI) was introduced at transient operation between SI and CI mode. Homogeneous charge compression ignition (HCCI) was utilized at part load to obtain ultralow emissions. Reformed charge compression ignition (RCCI) was imposed at low load to extend the HCCI operation range. In SI mode, the stratified concentration is formed by introducing a second fuel injection in the compression stroke. This kind of stratified mixture has a faster heat release than the homogeneous mixture and is primarily optimized to reduce the fuel consumption. In CI mode, the cam phase configurations are switched from positive valve overlap to negative valve overlap (NVO). The test results reveal that the CI combustion is featured with a high gradient pressure after ignition and has advantages in high thermal efficiency and low NOx emissions over SI combustion at part load.
© 2014 The Authors. Published by Elsevier Ltd.The paper presents an attempt to enhance unit performance of an existing 1274 m3/h Multi Stage Flash (MSF) desalination plant through sensible heat recovery from hot distillate water at the MSF stages to warm up the make-up seawater using internal heat exchange. The extraction of the distillate from stages could increase water production by 2% and reduces steam consumption by 5%. In addition, a reduction of seawater feed flow which also results in a drop of pump power consumption were observed. Environmentally, the modification could decrease CO2 emissions by 2300 tonnes annually.
In an Organic Rankine cycle (ORC) system, the working fluid pump plays an important role in the system performance. This paper focused on the operating characteristics of a multistage centrifugal pump at various speed and condensation conditions. The experimental investigation was carried out to assess the influence of the performance of the pump by the ORC system with special attention to actual net power output, thermal efficiency as well as back work ratio (BWR). The results showed that an increase in the pump speed led to an increase in the mass flow rate and expand in the operating range of the outlet pressure. The mass flow rate decreased nonlinearly with the increase of the outlet pressure from 0.22 to 2.41 MPa; the electric power consumption changed between 151.54 and 2409.34 W and the mechanical efficiency of the pump changed from 7.90% to 61.88% when the pump speed varied from 1160 to 2900 RPM. Furthermore, at lower pump specific speed the ORC system achieved higher thermal efficiency, which suggested that an ultra-low specific speed pump was a promising candidate for an ORC system. The results also suggested that the effects of condensation conditions on the pump performance decreased with the pump speed increasing and BWR was relatively sensitive to the condensation conditions, especially at low pump speed.
This paper presents the long-term effects of plastic pyrolysis oil (PPO) in a diesel engine when it is used as a primary fuel. Our previous investigation indicated that PPO is a promising fuel; however, the results suggested that the addition of diesel is necessary in order to obtain acceptable engine performance. In the present work, a blend of 75% PPO and 25% diesel was utilized in the engine for the longevity test. The engine failed after 36 hours on PPO blend when a piston was cracked. The engine's combustion, performance and emissions characteristics were monitored throughout the longevity test revealing that the engine performance deteriorated dramatically the last hours of operation. Moreover, the analysis of the exhaust temperatures during the failure moment suggested that the underpinning reason for the cracked piston was the injector failure. After the failure, the engine was opened and the engine's parts were investigated showing excessive wear. The lubricant oil was analysed and confirmed the increased wear due to the elevated contamination. Finally, the deposits from the piston heads were collected and analysed revealing that incomplete combustion was taking place. (C) 2017 The Authors. Published by Elsevier Ltd. Peer-review under responsibility of the scientific committee of the 9th International Conference on Applied Energy.
A thermal management system for lithium-ion batteries is an essential requirement for electric vehicle operation due to the large amount of heat generated by these cylindrical batteries during fast charging/discharging. Previously, researchers have focused mostly on pouch and prismatic cells with heat pipes arranged in the horizontal direction. The current study introduces a novel vertically-oriented heat-pipe-based hybrid cooling battery thermal management system (BTMS) that numerically evaluates the thermal performance of the cylindrical batteries and the flow pattern within the cooling channel at C rates as high as 8C. The model was experimentally validated using five round heat pipes in a vertical orientation utilizing the effect of gravity to assist condensate flow through the heat pipe. The heat pipes were arranged in a staggered pattern to improve the overall heat transfer performance by means of forced convective cooling. This design allowed for maximizing the heat transfer process despite the lack of contact between the cylindrical-shaped batteries and round-shaped heat pipes. During this study, the temperatures of the evaporator end and the condenser end of the heat pipes and battery surfaces were monitored, and the thermal performances of the system were determined at varying inlet cooling liquid temperatures (15, 20, 25 °C) and high rates of 4C and 8C. Representatively, the proposed hybrid BTMS could maintain a maximum battery surface temperature of around 64 °C and a temperature difference between cells under 2.5 °C when the inlet velocity was 0.33 L/min and the cooling liquid temperature was 25 °C. The high temperatures reached the fourth and fifth heat pipes because they are part of the backflow design and are affected by backflow temperature. Nevertheless, the current design shows that the proposed system can maintain battery surface temperatures well within 5 °C.
Hydrogen energy is considered to be the most potential “ultimate energy source” due to its high combustion calorific value, cleanliness, and pollution-free characteristics. Furthermore, the production of hydrogen via the electrolysis of water has the advantages of simplicity, high efficiency, environmentally safe, and high-purity hydrogen. However, it is also associated with issues such as high-power consumption for the reaction and limited large-scale application of noble metal catalysts. Metal–organic frameworks (MOFs) are porous composite materials composed of metal ions and organic functional groups through orderly coordination with large specific surface areas and large porosity. Herein, we focus on the research status of MOFs and their transition metal derivatives for electrocatalytic water splitting to produce hydrogen and briefly describe the reaction mechanism and evaluation parameters of the electrocatalytic hydrogen evolution and oxygen evolution reactions. Furthermore, the relationship between the catalytic behavior and catalytic activity of different MOF-based catalysts and their morphology, elemental composition, and synthetic strategy is analyzed and discussed. The reasons for the excellent activity and poor stability of the original MOF materials for the electrolysis of water reaction are shown through analysis, and using various means to improve the catalytic activity by changing the electronic structure, active sites, and charge transfer rate, MOF-based catalysts were obtained. Finally, we present perspectives on the future development of MOFs for the electrocatalytic decomposition of water.
This book aspires to be a comprehensive summary of current biofuels issues and thereby contribute to the understanding of this important topic. Readers will find themes including biofuels development efforts, their implications for the food industry, current and future biofuels crops, the successful Brazilian ethanol program, insights of the first, second, third and fourth biofuel generations, advanced biofuel production techniques, related waste treatment, emissions and environmental impacts, water consumption, produced allergens and toxins. Additionally, the biofuel policy discussion is expected to be continuing in the foreseeable future and the reading of the biofuels features dealt with in this book, are recommended for anyone interested in understanding this diverse and developing theme.
In the present study, a micro-scale solar organic Rankine cycle power generation system was developed. The system comprises of a solar collection system based on compound cylindrical Fresnel lens concentrator and an organic Rankine cycle power generation system integrated with a scroll expander. YD320 and R245fa were used as the heat transfer fluid and the working fluid, respectively. The effects of the evaporation pressure, the degree of superheat, and the mass flow rate of the working fluid were analyzed to evaluate the solar collection efficiency, the electric power output, the thermal efficiency and exergy efficiency of the system. The results illustrate that both the increasing evaporation pressure and decreasing superheat degree have positive impacts on solar collection efficiency. The electric power increases as the evaporation pressure increases, while the thermal efficiency and the exergy efficiency decrease. However, the system overall efficiency decreases slowly due to the increase of solar collection efficiency. The electric power increases with the increment of the working fluid mass flow rate. The increasing mass flow rate has no visible impact on the thermal and exergy efficiencies of organic Rankine cycle subsystem, whereas a slightly increase of the thermal and exergy efficiencies of the integrated system. The electric power decreases with the increase of the superheat degree, whereas the thermal and the exergy efficiencies of the system increase. The system works more suitably with a higher degree of superheat for the small mass flow rate condition.
[Display omitted] •Opposed rotary piston engines deliver high power density.•Hydrogen direct injection applications to this novel engine are explored.•In-cylinder combustion and thermal efficiency are insensitive to early ignition.•Start of hydrogen injection avoiding the piston end faces is helpful for combustion.•Late hydrogen injection contributes to restraining the nitric oxides formations. Opposed rotary piston (ORP) engines as a new type of internal combustion engines are free of connecting-rod mechanisms, have small engine size and mass. ORP engines have the abilities of delivering high power density. Hydrogen fuel applications in internal combustion engines contribute to nearly zero carbon emissions in the combustion processes. In this paper, the effect of hydrogen direct injection strategies and ignition timing on hydrogen diffusion, in-cylinder combustion, energy distributions, and nitric oxide (NOx) emissions are investigated using a numerical simulation method regarding this novel internal combustion engine. The results showed that hydrogen was the most unevenly distributed in the combustion chambers for the start of injection (SoI) of −68.2° crank angle (CA) after top dead centre (aTDC) among the three hydrogen injection strategies; meantime, it presented the lowest combustion efficiency, being smaller than 98.5%. The peak in-cylinder pressure ranged from 40 bar to 83 bar for the given scenarios. The combustion durations were in the range of 20 °CA ~ 30 °CA for the ignition timing of −20.85 °CA aTDC ~ −11.06 °CA aTDC. The indicated thermal efficiency was higher than 38% over early ignition cases; the energy losses in total fuel energy by cylinder walls were lower than 15%. NOx emissions factors were lower than 36 g/kWh, and they were reduced by the retarded hydrogen injection. The engine performance and NOx emissions under early hydrogen injection scenarios are less sensitive to late ignition; additionally, the crank angle corresponding to the optimal efficiency was almost the same under different hydrogen injection strategies.
The effect of ozone on the combustion performance of methane-air mixture was studied with a constant volume combustion bomb test bench under different initial pressures and equivalence ratios. The laminar combustion characteristic parameters were obtained according to the flame propagation images. The comparison of the laminar combustion characteristic parameters showed that the O-atom decomposed from ozone can promote the reaction activity of the mixture. Based on the Markstein length, it can be concluded that ozone can increase the flame instability of the mixture, also the flame thickness decreased with ozone addition due to the acceleration of chemical reaction. Both the laminar flame speed and laminar burning velocity increased with ozone addition, and the maximum relative increment of the parameters all appeared at the equivalence ratio of 0.6, which showed the ozone had a more notable enhancement effect for lean methane-air mixture. It was feasible to enhance the combustion performance for natural gas engine using lean burn combustion in principle. •Study the laminar combustion characteristic of ozonized methane/air mixture under lifted initial pressure.•Laminar combustion performance was improved due to the increase of active species with ozone addition.•Ozone addition reduced the flame thickness and increased the flame instability.•Ozone had a higher enhancement effect for the lean methane/air mixture.
Currently, bioethanol leads the automotive fuel market as the main substitute for gasoline in spark-ignition engines. However, worldwide interest has been triggered in the potential of 2,5-dimethylfuran, known as DMF, since the discovery of improved production methods. Although the energy content of DMF is comparable to that of gasoline, little is known about its combustion characteristics and emissions. Therefore, this work examines the effect of DMF in a single cylinder direct-injection spark-ignition engine. The results are compared to ethanol and gasoline using the optimized spark timings for gasoline and the respective fuel. In summary, DMF produces competitive combustion and emissions qualities to gasoline, which, in some cases surpass ethanol. The two biofuels have a higher burning rate and lower initial combustion duration than gasoline. They also produce greater combustion efficiency, which helps to lower hydrocarbon and carbon monoxide emissions. These initial results highlight how DMF, which was originally only considered as an octane improver, has the potential to become a competitive renewable gasoline alternative. © 2010 Elsevier Ltd. All rights reserved.
© 2015 Elsevier Ltd.This paper presents an experimental investigation of the starting process of a prototype free piston engine generator (FPEG). Experimental test results show that during the motoring stage, the peak in-cylinder pressure and compression ratio increase in a non-linear manner and trend to reach a stable state after a number of cycles. The motoring force is suggested to be within a reasonable range. With a fixed starting force of 125. N, the in-cylinder air fuel mixture was successfully ignited at the fourth cycle with a compression ratio of over 9:1. The peak in-cylinder pressure for the first combustion cycle reached over 40. bar. The piston ran at high and relatively constant speed at the middle portion of the stroke. The peak piston velocity increases significantly to around 4.0. m/s. Cycle-to-cycle variation of the piston movement was significant and the engine misfired frequently. During the misfire cycles, the peak piston velocity decreased to nearly 2.5. m/s; and the piston dynamics were similar to the motoring process. Based on these, discussion on misfire and further stable running control, as well as the linear electric machine mode switch were presented.
Combustion-related characteristic parameters, such as the start of combustion (SoC) and the timing of the peak pressure increase rate (PIR), can be used as the feedback signals for the closed-loop control of combustion. A dynamic Finite Element Method (FEM) model was firstly developed to confirm the closely related time period between combustion pressure and vibration. On this basis, a fast processing method was developed to estimate the timings of SoC and the peak PIR in the closely related time period. This method was verified on a twelve-cylinder heavy-duty diesel engine at various engine speed and load. Results showed that the maximum deviation of the two parameters were within 2 °CA and 1.5 °CA, respectively, which suggested that the proposed method had an adequate accuracy.
© 2012 Elsevier Ltd.This detailed exergy analysis of a 3800 m3/h Multi-Stage Flash (MSF) desalination plant is based on the latest published thermodynamics properties of water and seawater. The parameters of the study were extracted from a validated model of MSF desalination using IPSEpro software. The results confirmed that the overall exergy efficiency of the unit is lower than would be desirable at only 5.8%. Exergy inputs were destroyed by 55%, 17%, 10%, 4.3%, and 14% respectively, in the heat recovery stages, brine heater, heat rejection stages, pumps and brine streams disposal. Moreover, the detail of the study showed that the lowest exergy destruction occurs in the first stage, increasing gradually in heat recovery stages and sharply in heat rejection stages. The study concludes that recovering the heat from the hot distillate water stages can improve unit exergy efficiency from its low 5.8% to a more economical 14%, with the hot water parameters suitable for powering other thermal systems such as absorption chiller and multi-effect desalination.
Under the stress of environmental pollutions and fossil fuel consumption caused by on-road transport, hybrid vehicles are attracting much attention. Opposed rotary piston (ORP) engines are a promising power source for hybrid vehicles, due to their compact designs and high power density. In this paper, combustion and emission characteristics of a turbocharged ORP engine fuelled with hydrogen were investigated to evaluate the overall performance of this engine. The results indicated that volumetric efficiency of this ORP engine was higher than 89.0% for all the given cases. Peak in-cylinder pressure was in the range of 51.0 ~ 69.0 bar; and 4000 RPM scenario had the maximum value, being benefitted from high intake temperature and pressure, and high volumetric efficiency. Combustion duration of this engine ranged 27 ~ 43° crank angle (CA), and combustion phase happened at 7.5 ~ 13°CA after top dead centre (TDC). Peak nitrogen monoxide (NO) formation rates were corresponding to 5 ~ 13°CA after TDC; accumulated NO decreased slightly after reaching the peak value for low engine speed conditions. Discharge pressure at the start of the exhaust stroke was higher than 6.0 bar, especially for 5000 RPM case whose value was approximately 11.0 bar. This ORP engine presented excellent torque characteristics, and the maximum indicated power density was approximately 104.0 kW·L−1 which was much higher than turbocharged four-stroke reciprocating engines fuelled with gasoline.
Homogeneous charge compression ignition (HCCI) has challenges in ignition timing control, combustion rate control, and operating range extension. In this paper, HCCI combustion was studied in a two-cylinder gasoline direct injection (GDI) engine with negative valve overlap (NVO). A two-stage gasoline direct injection strategy combined with negative valve overlap was used to control mixture formation and combustion. The gasoline engine could be operated in HCCI combustion mode at a speed range of 800-2 200 r/min and load, indicated mean effective pressure (IMEP) range of 0.1-0.53 MPa. The engine fuel consumption is below 240 g/(kW^sup -1^·h^sup -1^), and the NO^sub x^ emission is below 4 × 10^sup -5^ without soot emission. The effect of different injection strategies on HCCI combustion was studied. The experimental results indicated that the coefficient of variation of the engine cycle decreased by using NVO with two-stage direct injection; the ignition timing and combustion rate could be controlled; and the operational range of HCCI combustion could be extended.[PUBLICATION ABSTRACT]
© 2014 The Authors.Organic Rankine Cycle (ORC) based engine waste heat recovery (WHR) has been recognised as a promising technology as it can potentially improve the total engine efficiency significantly and has no noticeable effect on engine operation. In this paper, a model based investigation in this technology has been presented. A semi-dynamic model has been developed which consists of a detailed 1-D engine acoustic model, an ideal ORC thermodynamic model and a bridging model that couples the two sub-models and enables a dynamic data transfer between these two models, thus enables a semi-dynamic simulation. A parametric analysis has been carried out for working fluid selection that allows the best match of the engine working conditions. Water, R134a and R245fa were selected as working fluid candidates, and the simulation results suggest that despite water has the highest cycle efficiency, it is unsuitable to use it because as a wet fluid, water cannot be heated to superheated steam in most of the conditions. For the two organic refrigerants, R245fa is superior to R123a in terms of cycle efficiency. A cyclic simulation following a WHSC engine operation cycle suggests that the control of working fluid flow rate is necessary to maintain a high ORC cycle efficiency. A preliminary optimal control can achieve 8.1% fuel economy improvement throughout the whole cycle.
This paper presents a linearization of the dynamic equation for a free-piston engine generator (FPEG), and simplifies it to a one-degree forced vibration system with viscous damping. The analogy between a massspring damper and a FPEG system is expressed, and the solution to the vibration system is solved. The model was successfully validated with respect to experimental data obtained from a prototype. The simulated piston displacement during steady operation showed similar trends with the test results and the error of the displacement amplitude was controlled within 3%. The state-space equations and the transfer function of the system are obtain using the fast response numerical model. An example of model application in the real FEPG control system was provided. Compared to the previous numerical model with differential approaches, the solving time of the proposed fast response model can be significantly reduced. The simplicity and flexibility of the proposed model make it feasible to be implemented to several computing software, i.e. Matlab, AMESim, Labview, Dymola et al. It can be easily implemented to real-time Hardware-in-the-Loop (HIL) simulation model for the future piston dynamic control system development. In addition, since it reveals how an FPEG operates in a resonant principle, the model is useful for parameter selection in the FPEG design process. (C) 2015 Elsevier Ltd. All rights reserved.
To study the fuel atomization problem when raw vegetable oil is used as an alternative fuel of compression-ignition internal combustion engine, this paper investigated the differences in spray characteristics between raw sunflower oil and regular diesel under different experimental conditions using the Schlieren method. The focus of this study is the effects of fuel temperature and injection pressure on the spray penetration distance, the spray cone angle, and the air entrainment of fuels injected into the constant volume vessel. The results show that both the spray penetration distance and the spray cone angle of the sunflower oil increase with increasing the fuel injection pressure and fuel temperature, which are similar to those of regular diesel.
In conventional heat pipe based battery thermal management systems the thermal contact between the battery and the heat pipe is enhanced by means of heat conductive elements. These additional elements introduce multiple layers of thermal resistance and contribute to increased weight. This paper aims to address this issue by minimizing the contact thermal resistance and potentially reduce this additional weight. The proposed solution relies on capillary-driven evaporative cooling (CDEC), wherein a wick structure is directly integrated onto the battery's surface to enable direct cooling. To demonstrate this concept, an experimental study was conducted by affixing a Copper foam to an emulated battery block, and using ethanol and Novec 7000 as cooling media. The CDEC system's thermal performance was assessed under three heating conditions, and different operating conditions. The results indicated that the copper foam with higher pore density outperformed the other due to its greater wetting height. The maximum cell surface temperature was maintained around 40 °C for a continuous 50 W heat input. Furthermore, the thermal resistance of the system was lowered by a factor of 6 compared to an air-cooled system. The thermal resistance ranged from a minimum of 0.32 to a maximum of 1.5 K/W, which were comparatively low compared to some existing battery thermal management system designs. This paper introduces an innovative battery cooling concept, presents experimental evidence of its feasibility, and demonstrates its ability to effectively regulate battery temperature within acceptable limits even under high heat loads, while minimizing overall thermal resistance.
An integrated air conditioning/heat pump (AC/HP) system for electric vehicle (EV) was developed and the system heating performances under low temperature were quantitatively evaluated. The AC/HP system employed electric scroll compressor to achieve high compressor speed. The heat exchangers were derived from the original EV air conditioning system. A four-way reversing valve was used to switch the system working modes between AC and HP. Heating tests using R134a and R407C as refrigerants were conducted respectively in an environmental chamber. The cabin temperature, the compressor power and other variables were analyzed to evaluate the system heating capability and energy efficiency. Test results showed that the AC/HP system satisfied the EV cabin heating requirement at the ambient temperature -10 degrees C. It reduced the EV power consumption remarkably compared to the original PTC heater. But the system performance was greatly affected by the ambient temperature. Compared to R134a, the system heating capability and the compressor power of R407C were increased but the energy efficiency was reduced. Increasing the compressor speed could limitedly improve the heating capacity, especially at the decreased ambient temperature. But it would reduce the energy efficiency distinctly. Test results also implied that the system performance has the potential for improvement. (C) 2016 Elsevier Ltd. All rights reserved.
The studies of constant wall thickness scroll expander have pointed out that geometries with large built-in volume ratios are necessary to achieve high performances in small-sized organic Rankine cycle (ORC) units. The variable wall thickness expander design offers the opportunity of increasing the geometric expansion ratio with the number of scroll turns remaining unchanged to avoid sealing and lubricating issues. In this paper, unsteady and three-dimensional computational fluid dynamics (CFD) simulations of scroll expander using variable wall thicknesses were therefore carried out to investigate the effects of the geometry on the internal flow behaviour. The scroll expander was integrated into an ORC unit fed by R123. The dynamic mesh technology of ANSYS Fluent was applied to generate the deforming mesh in the expander working chambers. The aerodynamic performance analysis yielded how over-expansion phenomena occurred at low pressure ratio while under-expansion phenomena were existing at high pressure ratio which are consistent with the thermodynamic theory of scroll expander. The higher pressure ratio was also contributing to higher temperature drops during the expansion process. Moreover, the occurrence of flank leakages through the radial clearances and its effects on the flow field were pointed out further proving the thermodynamic theory of scroll expander.
In this paper, the microscopic spray characteristics of diesel, Rapeseed Methyl Ester (RME) and Gas-to-Liquid (GTL) fuel, were studied at different injection pressures and measuring positions using Phase Doppler Anemometry (PDA) technique and the velocity development and size distributions of the fuel droplets were analysed in order to understand spray atomisation process. The injection pressures ranged from 80MPa to 150MPa, and the measuring position varied from 20mm to 70mm downstream the nozzle. It was found that the data rate is quite low in the near nozzle region and at high injection pressure. Sauter Mean Diameter (SMD) of all fuels obviously decreases when the injection pressure increases from 80MPa to 120MPa; but the injection pressure has little promotion on the axial velocity of droplets. The SMD decreases with increasing axial distance from the nozzle from 40mm to 70mm downstream the nozzle for the given fuels at the injection pressure of 120MPa while relatively stable at 80MPa injection pressure. Moreover, the droplet velocity development of GTL and RME exhibits a similar tendency, compared with that of diesel at given injection pressure. GTL has the smallest SMD, compared with diesel and RME at the given test condition. For RME and diesel, SMD does not show obvious difference at 80MPa injection pressure. However, diesel obtained a smaller SMD when injection pressure was increased to 120MPa. Copyright © 2010 SAE International.
In this study, the particle emission characteristics of 10% alternative diesel fuel blends (Rapeseed Methyl Ester and Gas-to-Liquid) were investigated through the tests carried out on a light duty common-rail Euro 4 diesel engine. Under steady engine conditions, the study focused on particle number concentration and size distribution, to comply with the particle metrics of the European Emission Regulations (Regulation NO 715/2007, amended by 692/2008 and 595/2009). The non-volatile particle characteristics during the engine warming up were also investigated. They indicated that without any modification to the engine, adding selected alternative fuels, even at a low percentage, can result in a noticeable reduction of the total particle numbers; however, the number of nucleation mode particles can increase in certain cases. For all the fuels tested, the increase of engine load results in a general reduction of particle numbers and an increase of particle mean diameters while increasing EGR leads to increased total particle numbers, which are mainly in the nucleation mode. The engine particle emissions suffer much higher numbers of the nucleation mode non-volatiles during warming up than during normal operations. © 2010 SAE International.
Exploring the differences between soot non-catalytic and catalytic oxidation process is beneficial to enhance the catalyst performance and soot removal efficiency of catalytic diesel particulate filters. In this paper, the soot samples are pretreated under high temperature conditions at both non-catalytic and catalytic oxidation atmosphere to obtain target pretreated soot samples with different mass loss. Five typical oxidation stages are analyzed with corresponding soot mass loss rate of 15 %, 25 %, 50 %, 70 %, 85 %. The soot physicochemical properties including oxidation activity, porous structure, particle layer, nanostructure, graphitization and functional groups are explored; further, the correlations among these physicochemical properties are analyzed, and three levels of catalytic effect mechanism are proposed based on CeO2 catalyst. This paper helps in understanding the differences of the mechanisms between non-catalytic and catalytic oxidation of soot.
Interstage turbine combustion used for improving efficiency of gas turbine was a new type of combustion mode. Operating conditions and technical requirements for this type of combustor were different from those of traditional combustor. It was expected to achieve engineering application in both ground-based and aviation gas turbine in the near future. In this study, a number of modifications in a base design were applied and examined experimentally. The trapped-vortex combustion technology was adopted for flame stability under high velocity conditions, and the preheating-fuel injection technology was used to improve the atomization and evaporation performance of liquid fuel. The experimental results indicated that stable and efficient combustion with slight temperature-rise can be achieved under the high velocity conditions of combustor inlet. Under all experimental conditions, the excess air coefficients of ignition and lean blow-out were larger than 7 and 20, respectively; pollutant emission index of NOx and the maximum wall temperature were below 2.5 g/(kg fuel) and 1050 K, respectively. Moreover, the effects of fuel injection and overall configuration on the combustion characteristics were analyzed in detail. The number increase, area increase and depth increase of fuel injectors had different influences on the stability, combustion characteristic and temperature distribution. •The combustion mode of slight temperature-rise (200 K) was achieved.•Effect of fuel and air injection on stability characteristic was investigated.•Impact of overall configuration on combustion performance was analyzed.•The feasibility of scheme was determined.
Copyright © 2014 SAE International.The free-piston engine generator (FPEG) is a novel type of energy conversion device; it integrates a two stroke combustion engine and a linear electric machine into a single unit. As an alternative to conventional engines, the FPEG is a promising power generation system due to its simplicity and high thermal efficiency and has attracted considerable research interests recently. This paper presents the development for a spark-ignited free-piston engine generator prototype, and the design of major sub-systems is introduced. The electrical linear machine is operated as a motor to start the engine and switched to a generator after successful ignition. Ignition is one of the most crucial problems for the generating process, thus a unique control sub-system to generate ignition signals at the correct ignition timing based on the piston position was completed. Then experiments of the starting process were carried out with the prototype. The results indicate that with a fixed motor force of 110N, the maximum in-cylinder gas pressure can reach 12 bar and the compression ratio can reach 8:1. Moreover, the experiment results show a good agreement with the simulation prediction. According to the performance of the starting process, the development of the prototype is acceptable and further research on the generating process will be undertaken soon.
© 2014 The Authors.In the present paper the combustion behaviour and soot generation of different neat vegetable oils on a direct injection optical diesel engine have been investigated using in-cylinder pressure based combustion analysis and high-speed two colour method. A singlecylinder optical diesel engine with an electronically controlled common-rail fuel injection system has been used for this study. Four different vegetable oils, Jatropha, Croton, Rapeseed and Sunflower oil, have been tested at 120 MPa injection pressure and fuel temperatures of 60 and 90 °C. All tests were performed at fixed injection timings and fixed engine speed at 1200 rev/min with pilot and main injection. The experimental results show that although all four bio-oils have very similar physiochemical properties, some differences in their combustion and soot generation behaviour have been observed. It was concluded that sunflower oil (SFO) had very good combustion properties at lower temperatures compared to other fuels. While croton oil (CO) did not have outstanding combustion behaviour at any conditions, the combustion of Jatropha oil (JO) was improved at higher fuel injection temperatures.
In recent decades, the carbon dioxide cycles, including supercritical carbon dioxide cycle, transcritical carbon dioxide Rankine cycle and refrigeration cycle, have been proven effective due to the high efficiency and compact structure, and received increasing interests. The performance of the expander in the power cycles, particularly in micro-scale applications, is one of the essential components that determine the cycle performance and still remains a significant challenge. This paper presents a critical overview of micro-scale (
Over the last few decades, the annual air pollutants from internal combustion engine (ICE) vehicles have dropped significantly, benefiting from the implementation of strict emission regulations and the development of vehicle technology. Nitrogen oxides (NOx) and particulate matter (PM) emissions from transport sectors contributed more than 32% and 12% of annual total emissions. Although hazardous exhaust emissions from ICE vehicles will be reduced after the bans on ICE vehicle sales in 2030, sustainable technology development of ICE vehicles is still necessary to meet the future challenges. After-treatment retrofitting technology and Inspection/Maintenance (I/M) are particularly important measures to deal with the deterioration of engines and after-treatment systems. [Display omitted] •Great success of drop ICE vehicle emissions has been achieved by the UK.•PM and NOx emissions are the main concerns of ICE vehicle emissions.•M/I and retrofit technology of after treatment will be the main measures.
Opposed rotary piston engines have the characteristics of high-power density and simple mechanisms. The applications of hydrogen fuel to internal combustion engines significantly are without carbon dioxide emission, alleviating the global warming. In this paper, hydrogen fuel was asymmetrically injected into combustion chambers to increase hydrogen penetration distance via; in the meantime, the engine performance and nitrogen monoxide (NO) emission with different ignition timing are explored by numerical simulation method. The symmetrical fuel injection scenario was provided as a baseline. In the scenarios of asymmetrical fuel injection, the engine had the best hydrogen injector position and ignition timing. Peak in-cylinder pressure Pmax reached 56.0 bar under ignition timing ti of −14.2° CA before top dead centre (bTDC) and hydrogen injector position (θ2) of 60.5°; in the meantime, heat loss rate HL and heat release rate Qr reached maximum values. Compared with the symmetric fuel injection engine, the peak NO emission of the asymmetric fuel injection engine was reduced by 15%. The proportions of energy loss by cylinder walls of asymmetric fuel injection engine were low and showed low dependency on ignition timing and hydrogen injector layout. Additionally, the asymmetric hydrogen injection structure makes hydrogen distribute evenly in the combustion chamber. [Display omitted] •Asymmetric hydrogen injection engine has best injector position and ignition timing.•The energy loss by cylinder walls of asymmetric hydrogen injection engine is lower.•Asymmetric hydrogen injection structure can reduce NOx emission of ORP engine.•Asymmetric hydrogen injection structure makes hydrogen distribute evenly.
In this paper, the relationship between the operation management and fuel consumption of a coach fleet was studied. The box diagram method was used to remove the abnormal data and improve the quality of sample data. Multiple stepwise regression analysis was used to confirm the major influencing factors for fuel consumption of the coach fleet. For the selected coach fleet company, the passenger quantity fluctuated periodically in the course of a year, and the time of the lowest passenger quantity appeared during the Chinese New Year. Fuel consumption per unit turnover ( ) increased with the increase of the rated engine power in general. Fuel consumption increased and decreased with the increase of carrying mileage and turnover. According to the fluctuation of passenger quantity, the number of operation vehicles was adjusted and part of the route was rearranged. The improvement measures increased the actual loading rate and reduced fuel consumption considerably, which verified the effectiveness of the measures.
For Homogeneous Charge Compression Ignition (HCCI) combustion, the auto-ignition process is very sensitive to in-cylinder conditions. This includes the change in in-cylinder temperature, the composition of chemical components and their concentrations. This sensitivity presents a major challenge for the accurate control of reliable and efficient HCCI combustion. This paper outlines our recent work: 1. a real-time control oriented gasoline-fueled HCCI combustion model and its implementation in Simulink with fixed step for the conversion into dSPACE Hardware-in-the-Loop (HIL) simulation purpose. 2. The development of model-based fast calibration for the best fuel efficiency and hydrocarbon emissions via evolutionary algorithm (EA). The model reported in this paper is able to run in real-time cycle-to-cycle under engine speeds below 4000rpm and with fixed simulation steps. This aims to achieve cycle-to-cycle performance calculation for Model based Predictive Control (MPC) and HIL simulation. With the aim of controlling the desired amount of trapped Exhaust Gas Recirculation (EGR) from the previous cycle, the phase of the Intake Valves Opening (IVO) and Exhaust Valves Closing (EVC) are designed to vary in this model. The model is able to anticipate the auto-ignition timing, MFB, combustion duration, in-cylinder pressure and hydrocarbon emissions etc. The validation has been conducted by comparing experimental data obtained from a Jaguar HCCI/SI V6 GDI engine at the University of Birmingham. This comparison shows good agreement between the simulation results and experimental data. Copyright © 2012 SAE International.
The detailed chemical kinetics was implemented into the 0D single-zone model, 1D engine cycle model and 3D CFD model respectively. Both simulation and experiment were carried out on a four-stroke gasoline HCCI engine with direct injection. The 0D model (HRG) was developed to study the isolating effect of HCCI parameters. The 1D engine cycle model with HRG was established to study the gas exchange process and the direct injection strategy in the gasoline HCCI engine with two-stage direct injection (TSDI) and negative valve overlap (NVO). The 3D model with HRG was constructed to study the ignition control mechanism in "two-zone HCCI" combustion via analysis the auto-ignition spots distribution in combustion chamber. "Two-zone HCCI" is defined in this paper as premixed ultra-lean compression ignition combining with premixed ultra-rich compression ignition. The three models were validated by experiments. The simulated results provided a detailed insight into the processes governing combustion and pollutant formation in the HCCI engine. TSDI fuel strategy and two-zone HCCI combustion are adopted to resolve the two stubborn problems of HCCI ignition timing control and high load extension. Copyright © 2006 SAE International.
Waste heat recovery from exhaust gas with organic Rankine cycle (ORC) systems is a promising method to improve the overall thermal efficiency of engines. The performance of a diesel engine integrated with an ORC system is evaluated in this paper. Simulation models of the diesel engine and the ORC system are developed in GT-suite separately, and a combined system model is developed in Simulink environment. The engine simulation results are validated experimentally. The steady performance evaluation of the engine with ORC system at different engine conditionsis presented, and the acceleration performance of the diesel engine with and without ORC is evaluated. The performance of the engine during the ORC expander start-stop process is also discussed. The steady performance simulation results indicate that, the net power output increment, the brake specific fuel consumption (BSFC) reduction and the thermal efficiency improvement of the engine with ORC system can be up to 4.13 kW, 3.61 g/(kW·h) and 0.66 %, respectively. The transient performance simulation results show that the ORC system has minimal effects on the acceleration performance of the engine.
In this study, the application of two closely coupled Diesel Particle Filters (DPFs), composed of an assistant DPF and a main standard honeycomb DPF, was investigated. A series of tests were carried out on a light-duty common-rail Euro 4 diesel engine and the emissions were measured and compared with those when a standard DOC+DPF system was used for the after-treatment. Replacing the DOC with an assisting DPF (ADPF) showed significant advantages in the reduction of particles, which had a direct impact in reducing the soot loading rate of the main DPF by up to 30%. Its oxidation characteristics not only showed equivalent exhaust-conversion efficiency, which concern the regulated gaseous emissions (CO and HC) under most engine conditions, but also continuously regenerated the soot it trapped. The impacts on the particle size and distributions were investigated, based on the new regulations on particle number limits; as well as the increased back pressure which is an unavoidable compromise. The overall performance of this DPF+DPF strategy showed great potential to be adopted in the future, Not only can this cope with tighter emissions regulations but it also has great cost benefits as main DPF's size and weight can be reduced. It also encourages more options for other cheaper materials as less soot is collected. Copyright © 2010 SAE International.
The detailed intake, spray, combustion and pollution formation processes of compression ignition engine with high-octane fuel are studied by coupling multi-dimensional computational fluid dynamic (CFD) code with detailed chemical kinetics. An extended hydrocarbon oxidation reaction mechanism used for high-octane fuel was constructed and a modeling strategy of 3D-CFD/chemistry coupling for engine simulation is introduced to meet the requirements of execution time acceptable to simulate the whole engine physicochemical process including intake, compression, spray and combustion process. The improved 3D CFD/chemistry model was validated using the experimental data from HCCI engine with direct injection. Then, the CFD/chemistry model has been employed to simulate the intake, spray, combustion and pollution formation process of gasoline direct injection HCCI engine with two-stage injection strategy. The models account for intake flow structure, spray atomization, droplet evaporation and gas phase chemistry in complex multi-dimensional geometries. The calculated results show that the periphery of fuel-rich zone formed by the second injection ignited first, then the fuel-rich zone ignited and worked as an initiation to ignite the surrounding lean mixture zone formed by the first injection. The two-zone HCCI leads to sequential combustion, this makes ignition timing and combustion rate controllable. In addition, HCCI load range can be extended. However, the periphery of fuel-rich zone leads to fierce burning, which results in slightly high NOx emissions. © 2006 Elsevier Ltd. All rights reserved.
Depletion of oil resources and increase in energy demand have driven the researchers to seek ways to convert the waste products into high quality oils that could replace fossil fuels. Plastic waste is in abundance and can be converted into high quality oil through the pyrolysis process. In this study, pyrolysis oils were produced from polyethylene (LDPE700), the most common used plastic, and ethylene-vinyl acetate (EVA900) at pyrolysis temperatures of 700oC and 900oC respectively. The oils were then tested in a four cylinder diesel engine, and the performance, combustion and emission characteristics were analysed in comparison with mineral diesel. It was found that the engine could operate on both oils without the addition of diesel. LDPE700 exhibited almost identical combustion characteristics and brake thermal e ciency to that of diesel operation, with lower NOX, CO and CO2 emissions but higher unburned hydrocarbons (UHC). On the contrary, EVA900 presented longer ignition delay period, lower e ciency (1.5–2%), higher NOX and UHC emissions and lower CO and CO2 in comparison to diesel. The addition of diesel to the EVA900 did not significantly improve the overall engine performance.
The movement of piston in free-piston expander-linear generator (FPE-LG) mainly depends on the dynamic force balance among four kinds of forces (air impetus, air resistance, electromagnetic resistance and frictional resistance). In this paper, the Newton's Second Law and the first law of thermodynamics are used to analyze the single-piston FPE-LG, the change of four kinds of forces and work produced by the four kinds of forces are analyzed. Nominal work-electricity conversion loss coefficient is proposed for the firs time to represent the energy loss. The experiment results show that the work produced by four forces from top dead center (TDC) to bottom dead center (BDC) are higher than those from BDC to TDC. The minimum proportion of air resistance energy consumption is also more than 50%, the proportion of electromagnetic resistance energy consumption is less than 20%, and the proportion of frictional resistance energy consumption is more than 20%. Therefore, the total nominal work-electricity conversion loss can be effectively reduced by increasing intake time or intake pressure. •Newton's Second Law is used to analyze the change of forces.•The first law of thermodynamics is used to analyze work produced by different forces.•Increasing intake time or intake pressure in a certain range can reduce energy loss.
This paper presents both experimental and numerical studies to investigate the impact of ozone concentration on a methane/air mixture combustion process. The experiments were conducted in a constant-volume combustion bomb at elevated initial pressures. Combustion pressure history, combustion duration, and burning rate were obtained at different air/fuel ratios, initial pressures, and ozone mixing ratios. The results suggested that ozone addition promoted combustion by increasing peak pressure and peak burning rate and decreasing combustion duration. Chemical kinetic calculation was carried out to assist in the understanding of how ozone enhanced the combustion process. The calculation results revealed that the dominant production and consumption reactions were enhanced by ozone addition. The promotion effect of ozone on the combustion process was mainly caused by the O atom decomposed from ozone. With ozone addition, the concentration of O, H, OH, and HO₂ increased more obviously in the early stage of the combustion process, and ozone mainly played an important role at the beginning of the mixture oxidation.
Multi-mode combustion is an ideal combustion strategy to utilize HCCI for internal combustion engines. It combines HCCI combustion mode for low-middle load and traditional SI mode for high load and high speed. By changing the cam profiles from normal overlap for SI mode to the negative valve overlap (NVO) for HCCI mode, as well as the adjustment of direct injection strategy, the combustion mode transition between SI and HCCI was realized in one engine cycle. By two-step cam switch, the throttle action is separated from the cam action, which ensures the stabilization of mode transition. For validating the feasibility of the stepped switch, the influence of throttle position on HCCI combustion was carefully studied. Based on the research, the combustion mode switch was realized in one engine cycle; the whole switch process including throttle action was realized in 10 cycles. The entire process was smooth, rapid and reliable without any abnormal combustion such as knocking and misfiring. Copyright © 2007 SAE International.
Ethanol has long been regarded as the optimal gasoline-alternative biofuel for spark-ignition (SI) engines. It is used widely in Latin and North America and is increasingly accepted as an attractive option across Europe. Nevertheless, its low energy density requires a high rate of manufacture; in areas which are deficient of arable land, such rates might prove problematic. Therefore, fuels with higher calorific values, such as butanol or 2,5-dimethylfuran (DMF) deserve consideration; a similar yield to ethanol, in theory, would require much less land. This report addresses the suitability of DMF, to meet the needs as a biofuel substitute for gasoline in SI engines, using ethanol as the biofuel benchmark. Specific attention is given to the sensitivity of DMF to various engine control parameters: combustion phasing (ignition timing), injection timing, relative air-fuel ratio and valve timing (intake and exhaust). Focus is given to the window for optimization; the parameter range which sustains optimal IMEP (within 2%) but provides the largest reduction of emissions (HC or NOx). The test results using a single cylinder SI research engine at 1500rpm show how DMF is less sensitive to key engine parameters, compared to gasoline. This allows a wider window for emissions optimization because the IMEP remains optimal across a greater parameter range. Copyright © 2012 SAE International.
2,5-Dimethylfuran, known as DMF, is a promising second-generation biofuel candidate. The potential of 2,5-dimethylfuran as an additive in iso-octane (used as gasoline fuel substitute in this study) was studied. Using outwardly spherical flame method and high speed schlieren photography, laminar burning characteristics of 2,5-dimethylfuran/iso-octane (20%/80% vol., designated as D20)/air mixtures were experimentally investigated. Laminar flame speeds and Markstein lengths of D20-air mixtures were empirically organized as a function of initial pressures and temperatures. Onset of cellular structures at the flame front was observed at relatively higher initial pressures due to the combined effect of diffusional-thermal and hydrodynamic instabilities. Laminar flame speeds of D20-air mixtures are higher than those of iso-octane-air mixtures when the equivalence ratio is greater than 1.2. © 2012 Elsevier Ltd. All rights reserved.