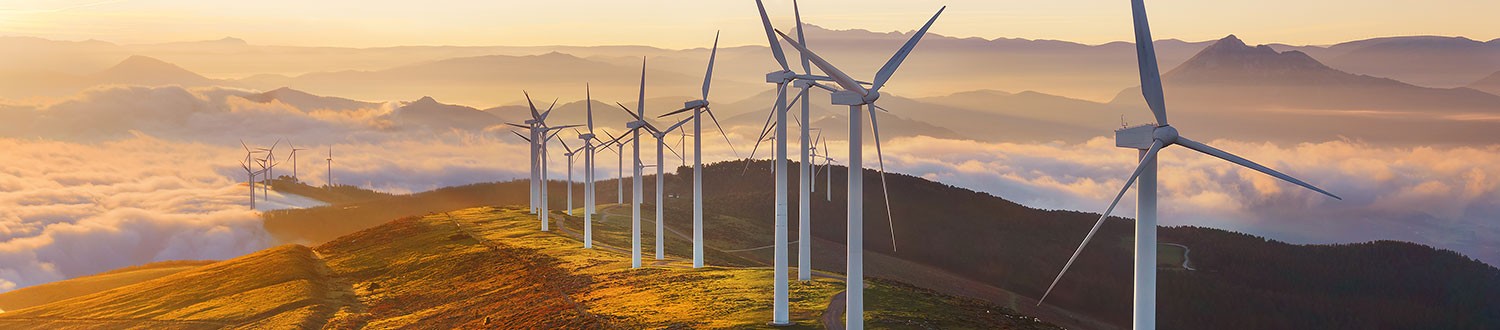
People
We are a friendly School of academic and research staff, tutors and administrators, with additional dedicated staff within the Faculty to support us.
Our staff and students
Find out more about our staff and students and get in contact.
We are a friendly School of academic and research staff, tutors and administrators, with additional dedicated staff within the Faculty to support us.
Find out more about our staff and students and get in contact.