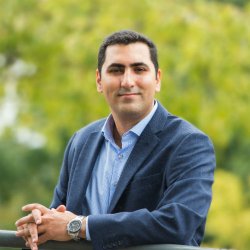
Dr Iman Mohagheghian
About
Biography
Dr Iman Mohagheghian is Associate Professor (Reader) in Mechanics of Materials at the University of Surrey. Dr Mohagheghian’s core expertise is around designing, manufacturing, modelling and testing the performance of novel lightweight materials/structures with lightweighting achieved through hybridisation of materials and through introducing multiple functionalities. Dr Mohagheghian is currently leading the Multi-functional, Adaptive and Sustainable Structures (MASS) lab conducting research projects spanning across TRL levels with funding from EPSRC, Innovate UK and industry.
Dr Mohagheghian received his PhD from the University of Cambridge in 2013. He worked in the micro-mechanics lab in the field of impact mechanics. His PhD, was on the application of polymers and polymer nano-composites as lightweight impact energy absorbing materials. Prior to joining Surrey, Dr Mohagheghian was a research associate in the Department of Mechanical Engineering at Imperial College London.
Areas of specialism
University roles and responsibilities
- Undergraduate programme leader for Mechanical Engineering
- Academic lead for mechanical testing facility
- Academic senior colleague role
My qualifications
Previous roles
ResearchResearch interests
- Adaptive, multifunctional structures
- Lightweight materials for energy absorption
- Metamaterials
- Multi-material additive manufacturing
- AI-informed mechanical and material design
- Sustainable materials
Research interests
- Adaptive, multifunctional structures
- Lightweight materials for energy absorption
- Metamaterials
- Multi-material additive manufacturing
- AI-informed mechanical and material design
- Sustainable materials
Supervision
Postgraduate research supervision
Mr Silas Purja (2023-present)
Mr Oswaldo A. Pellejer (2023-present)
Mr James Smith (2021-present)
Mr Henry Yu (2020-present)
Mr Zhong Li (2019-present)
Mr Parham Mostofizadeh (2019-present)
Mr Dimitrios Charaklias (2019-present)
Mr Chirnjeev Nagi (2017-present)
Dr Abhishek Dixit (2017-2020)
Dr Ignacio Carranza Guisado (2017-2019)
Dr Ghilane Bragagnolo (2017-2019)
Dr Jie Zhou (2014-2017)
Dr Cihan Kaboglu (2014-2017)
Dr Long Yu (2014-2016)
Dr Yi Wang (2014-2016)
Teaching
- ENG2088 (FHEQ Level 5): Solid Mechanics II: Stress Analysis
- ENG2087 (FHEQ Level 5): Design Project: Design, Make & Evaluate
- ENG2093 (FHEQ Level 5): Strain gauge lab
- ENG3206 (FHEQ Level 6): Materials Selection in Mechanical Design
- ENGD028 (FHEQ Level 8): Composite Materials Technology
Sustainable development goals
My research interests are related to the following:
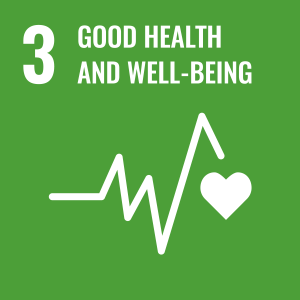
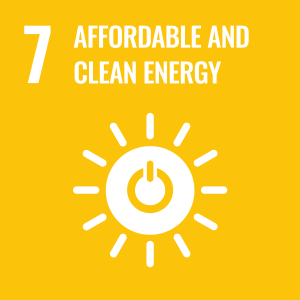
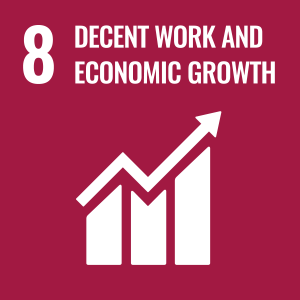
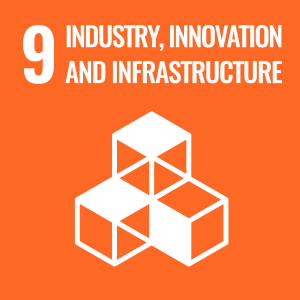
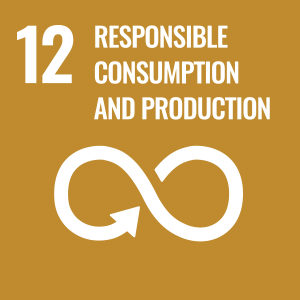
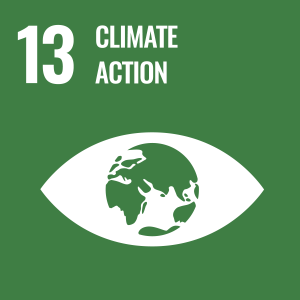
Publications
In constant pursuit of lightweight, efficient, and resilient structures, the focus to Multi-Functional Structure (MSF) has increasing grown over the past decade. The MFSs combine load-bearing capacity with other functionalities such as thermal/electrical conductivity or insulation, electromagnetic shielding, energy storage, self-healing, stiffness modulation, or any combination of them. In constant pursuit of lightweight, efficient, and resilient structures, attention to Multi-Functional Structure (MSF) has increasing grown over the last decade. The MFSs often combine load-bearing capacity with other functionalities such as thermal/electrical conductivity or insulation, electromagnetic shielding, energy storage, self-healing, stiffness modulation, or any combination of them. Often constituted of hybrid materials, MFSs employ stimuli-responsive materials, allowing them to adapt to external factors like heat, pressure, electrical current, magnetic or electrical fields, moisture, pH levels, or light. Amongst various methods, thermal softening in thermoplastics is one of the most desirable de-stiffening methods because of its reversibility, scalability, and applicability in many of current multi-layered structures without compromising structural performance. However, the reliance on delivering thermal energy introduces challenges such as prolonged activation times and high-power requirements, limiting its application in scenarios requiring rapid de-stiffening, such as impact protection. This paper systematically investigates the parameters influencing the response time of de-stiffening, focusing on characteristics such as the size of the heating element and the volume, as well as the thermal properties of the material to be heated. We employed three types of heating elements embedded in multi-layered structures, namely wires, structured metallic meshes, and random metallic meshes (refer to Figure 1). Our findings demonstrate that achieving a very fast heating rate (45°C·s-1) is feasible using random metallic meshes under 4.8 V excitation. Figure 1: Embedding various types of heating element in multi-layered structures.
This study harnesses advanced Bayesian optimisation techniques for the intricate design of structures, poised for application as compliant flooring unit cells, as shown to reduce fall injuries in older people[1]. Inspired by the foundational research detailed in studies[2][3], our exploration delves into a design space encompassing eight key variables, contributing to a broad spectrum of geometric variations. In constitutive modelling of unit cells, we adopt the Neo-Hookean model for its effectiveness in mirroring rubber-like materials' intrinsic properties. A key element of our approach involves acknowledging and addressing uncertainty, emanating from variations in material properties and geometric imperfections. The study rigorously explores the behaviour of these structures under 2D loading conditions , examining various ratios of compression and shear forces. Employing the Bayesian optimisation algorithm, the design iteratively progresses towards an optimal configuration, driven by a comprehensive set of objective functions, which are formulated to achieve an balance between structural stiffness, critical buckling load, and the energy absorption. The effectiveness of the obtained designs is validated by mechanical testing of specimens, manufactured utilizing rubber casting and 3D printing. This study highlights the efficacy of Bayesian optimization in design, particularly under diverse loading conditions and in the presence of uncertainty. It provides valuable insights into the method's ability to improve the resilience and adaptability of structures, representing a notable advancement in the field.
This study investigates the performance of a multi-layered variable stiffness structure with an embedded metallic mesh as a heating source. A combined experimental and numerical approach was employed to assess the heating efficiency, temperature distribution, and stiffness modulation. The embedded metallic mesh, with seamless junctions and an 11% fill factor, achieved uniform temperature distribution, heating rate of 6.4 °C/sec and induced a 30% reduction in stiffness at an applied current of 5 A. However, localised overheating led to matrix damage in the form of thermal hotspots. To mitigate this, a modulated current input was introduced using a 50% duty cycle square pulse at frequencies ranging from 1 Hz to 10 Hz. This modulation successfully reduced peak hotspot temperatures by 30%, prevented matrix degradation, and improved initial system response time while maintaining the desired temperature profile. Furthermore, numerical simulations were conducted to evaluate the impact of various metallic mesh topologies, each maintaining a constant fill factor. The results indicate that topology plays a significant role in heating efficiency, particularly at lower current densities. These findings offer critical insights into the design of advanced variable stiffness materials with large stiffness variation and fast response dynamics.
Composite foam sandwich structures are considered high performance materials, however skin-core debonding and core failure are often a weak link in the structure. This is a follow on from the paper presented at Adhesion 19 which presented the results from plain composite sandwich panels for a range of foams, showing that the coarser cell foams introduce a thicker hybrid resin layer at the foam-composite interface leading to enhanced panel performance. This paper presents results from a study with a single foam looking at the effect of through-thickness reinforcement of the panels. The position of the through-thickness ribs was investigated by undertaking quasi-static three-point bend tests on the panels. Typical panel failure was due to shear in the foam extending to crack growth along the foam-skin interface. The best performance was found when the through thickness reinforcement was placed on either side of the central loading roller, thus constraining the spread of the damage. Effort was made to develop reliable FE models for the configurations considered thus providing a method of predicting the performance of other panel designs. The experimental data, which included load-displacement responses, failure mechanisms and full- field strain from digital image correlation, was used to assess the validity of the FE models developed. It was found that by using appropriate failure models for foam and skin the need for complex interface modelling was not necessary.
Lattice structures offer excellent stiffness to weight ratios and show promising potentials in decreasing the weight of structures. This has significant implications in reducing carbon footprint, especially in the automotive and aerospace sectors. In this paper, the aim is to enhance the efficiency of lattice structures further by embedding multiple functionalities into one structure. To reach this goal, a multi-material lattice structure was designed and manufactured using a Polyjet 3D printer capable of printing different polymers in a single print. By fabricating a lattice whose different struts were built from distinctive materials, it was possible to induce a continuous varying stiffness in the structure through temperature elevations. A compressive stiffness drop of more than 95% could be observed in the lattice with a 27-degree increase in temperature. The observations demonstrate the potential of using the proposed method in designing programmable lightweight structures which can be a leap forward in achieving more efficient and multi-purpose structures.
The Arthritis patients and aging population has challenged society to develop safer, independent living environments. Falls, associated injuries, and delays in fall treatment are major causes of morbidity and death in older adults. Therefore, fall detection systems are fundamental to reducing fall risks and building safer environments. Designing fall detection systems is an emerging field of research. The development of the system relies on a sensing mechanism, processing unit, and communication to alert the emergency facilities. Each module is crucial in providing a cost-effective, accurate, reliable, and robust solution. Technological advancements in fall detection systems, particularly wearable and non-wearable devices, offer promising solutions. Wearable systems are prevalent due to their cost-effectiveness and ease of installation, but they canbe unreliable if not worn consistently. Non-wearable systems, including smart flooring, provide continuous monitoring but are expensive and complex to maintain. This article reviews the development and deployment of fall detection technologies, examining their practical limitations and emphasizing floor-based detection systems as a viable solution for fostering independent living among older adults.
With growing demands for cleaner and more sustainable energy, there has been rapid development in the wind energy industry. This trend has led to an increase in the size of wind turbines, which could cause drawbacks such as increased stresses, more complex control systems, and more costly manufacturing and transportation. Due to their high aerodynamic efficiency, light weight, and structural simplicity, morphing structures have become of great interest in the renewable energy industry. Morphing structures are structural systems capable of shifting their geometric form across two or more stable configurations to achieve targeted engineering functionalities. Despite having many advantageous characteristics, there is a significant challenge with designing morphing structures; that is, the structure must be compliant to demand low actuation force, while being stiff for load-carrying purposes. One approach to addressing this issue is using composite materials with anisotropic properties or bistable/multistable behavior. Through an extensive review of the recent literature, this study aims to provide insights into the underlying structural concepts and mechanical properties of morphing structural materials and their viability and sustainability for wind turbine blade applications.
Traditional auxetic honeycombs often exhibit reduced energy absorption capabilities due to global instability arising from shear band formation, significantly limiting their practical applications. To address this limitation, this study presents the Auxetic Arc-Curved Honeycomb with a novel Bioinspired Layering Gradient (BLG-AACH). The innovative gradient design of the BLG-AACH is inspired by the dense exterior and sparse interior characteristics of biological tissues across multiple scales, utilizing fractal self-similar structure to achieve this biological trait. The BLG-AACH facilitates induced deformation in the intermediate layers, thereby preventing overall global buckling and significantly enhancing energy absorption properties. The compressive behavior of the BLG-AACH was investigated through both experimental testing and finite element modeling. The results demonstrate that the BLG-AACH structure maintains a stable concave folding deformation mode and exhibits multi-level energy absorption capabilities. Its specific energy absorption and total energy absorption are 5.81 and 10.74 times greater than those of the homogeneous AACH, respectively, outperforming other layered configurations. Moreover, the BLG-AACH is highly programmable, enabling the adjustment of mechanical properties such as initial stiffness, plateau stress, and specific energy absorption by varying parameters like cell angle and cell wall thickness. Additionally, Genetic Programming-Symbolic Regression (GP-SR) was innovatively employed to derive a compact and scalable formula for calculating the specific energy absorption of the BLG-AACH, achieving an impressive R2 value of 0.99. These findings provide a novel paradigm for enhancing the energy absorption performance and its calculation in auxetic honeycombs.
Kirigami, the Japanese art of paper cutting, can be used to generate complex 3D shapes from 2D sheets. Kirigami structures can also be highly stretchable and accommodate extremely large strains from common materials, such as aluminium, which allow relatively small strains at failure. The high stretchability of Kirigami makes it an ideal method for energy dissipation applications. This study investigates the mechanics and energy-dissipating behaviour of Kirigami made from metallic materials. A comprehensive analysis is conducted using a combination of reduced-order analytical modelling, finite element analysis, and experimental validation. The analytical model is used to produce a design methodology for energy-dissipating devices based on metallic ribbon Kirigami and is then applied as a case study to the design of a novel fall arrest system. The results of this study will enable the design of efficient, and highly customisable energy-dissipating systems based on metallic Kirigami.
Transparent thermal heaters based on metallic networks have gained considerable attention in the last few years as a result of their superior response time, low sheet resistance and low cost of manufacturing. To increase the mechanical stability and reliability of the thermal heater, it is desirable to embed the metallic network in some form of matrix. Embedding the network however, changes the nature of thermal conduction making both in-plane and out-of-plane thermal conduction important for ensuring reliability and uniform thermal distribution. The performance of embedded thermal heaters is also significantly influenced by the geometry of metallic network, both in terms of optical transparency and thermal performance. In this paper, we have developed a coupled electro-thermal model and an electromagnetic model to investigate the properties of an embedded metallic mesh in a polymer matrix. IR thermal imaging and UV spectrophotometer have been used to quantify thermal transport and transparency in the system and to verify the performance of FE models. A systematic study is then performed to assess the role of network topology both on in-plane and out-of-plane thermal distribution and optical performance. According to numerical analysis, a structure-property relationship has been established which could provide desirable network configurations to optimize performance.
Here, electro-thermal response of thin film heaters is investigated for a wide range of periodic metallic mesh topologies. The aim of this study is to systematically investigate the effect of topology, in particular node connectivity, on the response of these networks. First, the allowable design space is defined by developing analytical expressions for geometrical dependencies of each topology and for permissible range of parameters. Subsequently, closed-formed analytical expressions are developed to calculate the resistance of each network considering junction area compensation. Finally, transient coupled electro-thermal finite element modelling is performed for a wide range of topologies using automated CAD model generation, meshing, analysis, and post processing. The closed-form analytical expressions of resistance can quickly and accurately predict the resistance of the networks of various topologies. Incorporation of junction area compensation in particular, improves the accuracy of models considerably. The network topology has a significant impact on resistance, demonstrating up to three times higher resistance for some topologies over the range investigated when compared on the same fill factor basis. This higher resistance results in faster response time when the current density is fixed. For the same power input however, the response time is much more similar yet has a considerable spatial temperature variation can be observed. The new insights obtained in this study will help designing faster and more energy efficient thin film heaters with a wide range of applications in electronics displays, wearable technologies, energy systems, optics and photonics and multifunctional devices.
Multi-material additive manufacturing has emerged as a promising avenue for the creation of innovative metamaterials including multi-material lattices with unique characteristics. This paper presents the examination of the impacts of varying loading rate and temperature on the mechanical properties of such lattice structures. The primary objective is to enhance understanding of how manipulating materials' configurations within multi-material lattices (by employing materials with different strain rate and temperature sensitivities) affects overall mechanical characteristics. The multi-material design was found to provide a broader and more tunable range of properties, e.g. peak stress increase of over 80% with changing strain rate from 10⁻⁴ to 10⁻² s⁻¹ in comparison to a 30% increase for the single material design and a 96% drop in peak stress, compared to an 84% decrease for the single-material design when temperature changing from 27°C to 50°C. Results indicate that through multi-material design, post-elastic deformation can be finely tuned for specific application requirements, whether necessitating high stiffness or high energy absorption. Moreover, it is observed that the global strain rate sensitivity of the multi-material lattice is influenced not only by the intrinsic sensitivity of constituent materials but also by changes in local stress and strain distribution as the rate increases.
The majority of natural organisms interact with their environments with a degree of mechanical adaptability that allows them to carry out a variety of tasks and adapt to changing circumstances. Human-made structures, however, lack this versatility and are normally designed to fulfill a certain load-carrying requirement. This causes limitations in performance, efficiency, and safety. The aim of this article is to present rapid de-stiffening in the response of conventional structures, without compromising the load-bearing capacity. This has been achieved by developing an active interface using an interconnected nanostructured metallic network. A very fast heating rate with an average of approximate to 45 degrees C s-1 under 4.8 V excitation while retaining transparency of 67% is demonstrated. The embedded metallic network in a thermoplastic matrix has been deployed as an active interface, in a conventional transparent multilayered structure. Upon activation, it provides a rapid (i.e., 2 s after activation) mechanical de-stiffening capability. The results from finite element modeling have been found to be in good agreements with those from experiments. The rapid reversible stiffness tuning demonstrated here can be implemented in variety of multilayered structures with a wide range of applications in robotics, morphing and deployable structures, active damping, and active impact safety systems. Herein, a transparent active interface is presented, which is manufactured using a template-based technique and is capable of very fast heating rates (approximate to 45 degrees C s-1 under 4.8 V excitation). The proposed interface can be utilized in many conventional multilayer structures and have great potentials for improving impact safety in pedestrian crashing or in human-robot interaction by fast de-stiffening of structures.image (c) 2024 WILEY-VCH GmbH
In this paper, surface conductive heating was utilized to actively control the stiffness of lattice metamaterials manufactured employing multi-material 3D printing. To create an electrical surface conduction, additively manufactured samples in single and dual material configurations were dip coated in a solution of carbon black in water. Electro-thermo-mechanical tests conducted successfully demonstrated that the low-cost conductive coating can be used to actively alter the stiffness of the structure through surface joule heating. The process was found to result in repeatable and reproduceable stiffness tuning. Stiffness reductions of 56% and 94% were demonstrated for single and dual material configurations under the same electrical loading. The proposed methodology can be implemented to actively control the properties of polymeric lattice materials/structures where the change in the composition of polymers (introduce bulk electrical conductivity) is difficult and can have a wide range of applications in soft robotics, shape-changing, and deployable structures.
Stir casting and powder metallurgy are the mainstream technologies for manufacturing particle-reinforced aluminum matrix composites. However, particle agglomeration and extensive interfacial reaction in stir casting, as well as residual porosity in powder metallurgy, make it challenging to obtain the due performance. In this study, a semi-solid metal direct writing process based on mixed powder remelting was proposed to manufacture SiCp/Al composites. The mixed powder consisting of AlSi10Mg alloy powder, pure Al powder, and SiCp is heated to a temperature slightly exceeding the melting point of the alloy powder and then sheared to produce a paste-like semi-solid aluminum slurry with suspended SiCp. The microstructures of SiCp/Al composites were experimentally investigated and modeled, demonstrating the uniformity of SiCp and the designability of microstructural characteristics (i.e., the volume fraction and shape factor of the solid phases). The SiCp-matrix interface was also characterized to illustrate the reliable interfacial bonding due to the relatively low processing temperature. Compared with the mentioned processes, this novel approach shows superiorities in particle dispersion and interfacial reaction control.
Bird strike on aircraft remains a serious threat to flight safety. Experimental investigations employing real birds are associated with high cost and low reproducibility. Therefore, physical substitute materials are often used instead of real birds. This study investigates the soft impact loading on aluminium and laminated glass targets from ballistic gelatine and rubber projectiles. The two targets simulate strike on the aircrafts' fuselage and windshield respectively. The full field out of plane displacements of the targets were recorded for velocities 110 to 170 m s−1 using digital image correlation during gas gun experiments. A simulation model based on Smoothed Particle Hydrodynamics was developed and validated against the experimental data from all four projectile-target material combinations. It was shown that for the same momentum, a rubber projectile exerts a higher pressure on a target as compared to gelatine, even though the out of plane displacements and in-plane strains are similar. This led to fractures in the impacted laminated glass when rubber was used. The study offers new experimental data as well as efficient design modelling tools to mitigate damage imposed during bird strike. The models provide a way towards enabling the optimisation of real, large scale aircraft structures and components.
Recent advancements in the field of multi-material 3D printing have opened up new opportunities for the production of intricate structures capable of displaying distinct behaviours. The primary objective of this study is to develop adaptive multi-material lattice structures with customizable properties through thermal activation. This objective was accomplished by applying a conductive coating onto the surface of polymeric-based multi-material lattices. Subsequently, the structure was subjected to Joule heating, achieved by passing an electric current through it. To evaluate the electro-thermo-mechanical properties of these lattices, electrical and mechanical loads were simultaneously applied while monitoring the surface temperature. The findings indicate that by applying a 12V potential to the coated multi-material samples at room temperature, a significant average reduction of over 70% in the elastic modulus of the samples was observed, demonstrating the considerable potential inherent in this approach.
In this paper, firstly the quasi-static bending performance of chemically strengthened alumina silicate glass plates is investigated for different glass thicknesses: 2.2, 4.0 and 6.0 mm. The flexural strength is measured using coaxial double ring experiments. The 3D Digital Image Correlation (DIC) technique is employed to measure the strain at failure. The failure probability is then assessed using the Weibull statistical distribution. Secondly, the performance of the laminated glass windows made of these chemically strengthened glass plates is evaluated quasi-statically under concentrated and distributed loadings. The effects of polymer interlayer thickness, glass and polymer type and multi-layering the polymer interlayer on the structural performance are investigated. The type and thickness of the polymer interlayer, as well as the type of loading are found to influence the fracture sequence in the glass plates and consequently the post fracture safety of the structure. The response of laminated glass specimens is then assessed under low velocity soft impacts, for velocities up to 3.3 m s−1, using a drop tower facility. Laminated glass with a polyvinyl butyral (PVB) interlayer shows the greatest improvement in terms of peak force and absorbed energy.
The correlation between K + -Na+ diffusion coefficient and mechanical properties of chemically tempered and hybrid tempered (chemically tempered subsequent to thermally tempered) aluminosilicate glass are investigated. Firstly, the potassium ion concentration profiles are experimentally measured and the diffusion coefficient is calculated according to the Boltzmann-Matano approach. Secondly, the flexure strength and Weibull modulus are determined using a combined experimental (coaxial double ring) and finite element analysis method. The results indicate that the flexural strength decreases with the diffusion coefficient of the air side for both types of glass samples while there is no significant relationship between diffusion coefficient and Weibull modulus. Diffusion coefficient on air side shows a higher value than that of the tin side. With the same diffusion coefficient, the flexural strength of chemically tempered glasses are found to be higher than that for hybrid tempered glasses. The effect of diffusion coefficient on modulus of rupture (MOR) for hybrid tempered glass is more remarkable. These results would be useful in designing the strength of glass and guiding the strengthening process by chemical or hybrid tempering.
The effect of residual stress on the fracture of chemically strengthened thin aluminosilicate glass was investigated. The large deflection problem on the flexure of thin chemically strengthened glass was solved through finite element analysis. The relationship among compressive stress (CS), central tension (CT), and the modulus of rupture of chemically strengthened thin glass was also discussed. High CS and low CT improved the flexural strength of chemically strengthened glass. However, the effect of residual stress was more complex on Weibull modulus than on strength. The effect of residual stress on the fractography of chemically strengthened thin glass was analyzed. Transparent and opaque zones were observed on the fracture surface of chemically strengthened glass. The relative thickness of the opaque zone (dOpaque/d0), which is a constant in the same fracture zone, linearly decreased with increasing fracture zone. This result indicates that the stored elastic strain energy was released with the number of transverse cracks. These results provide useful information on the failure analysis of chemically strengthened thin glass.
Composite sandwich structures are well-suited for applications requiring high bending strength, flexural rigidity, crashworthiness, and light weight. However, skin-core debonding and core failure remain a barrier to optimal structural performance when polymeric foams are used as core materials. Suppressing or compartmentalising these failure modes can enhance the structural integrity of sandwich structures. In this paper, the flexural response of a sandwich structure was improved by adding carbon fibre-reinforced plastic in the form of through-thickness ribs during the manufacturing process. The effect of the position of the ribs was investigated using a quasi-static three-point bend test. A camera was used to capture failure events, while the digital image correlation technique provided the full-strain field at different stages of loading. Improved flexural performance was obtained when a reinforcement was placed on either side of the loading roller. With this configuration, skin-core debonding was restricted to a confined portion of the panel, resulting in a more localised and stable fracture process, which involved enhanced foam crushing and hardening. A simple FEA approach has been adopted in this paper and has proven to be an effective approach for capturing the details of the failure process, including the debonding in the composite foam structures, without the need for complex and computationally expensive interface modelling.
The effect of residual stress on subcritical crack growth in chemically strengthened aluminosilicate glass in air and water was firstly investigated using the double torsion (DT) technique. An experimental evaluation procedure was developed based on the DT method. The research demonstrates that high compressive stress (CS) and low central tension (CT) in chemically strengthened glass are beneficial in improving crack growth index and decreasing susceptibility to fatigue. Chemically strengthened glass with high CS and low CT exhibits a smaller proof-test ratio, which indicates better survival characteristics. The results are useful in designing the strength and optimizing the strengthening process by ion exchange to obtain a more robust glass with long service lifetime.
Ductile thermoplastics, for example Ultra High Molecular Weight Polyethylene (UHMWPE), are of interest for their impact energy absorbing capabilities. While the impact perforation mechanisms of metallic targets have been investigated in some detail, far less progress has been made towards understanding the impact resistance of ductile polymers. The aim of this investigation is to identify the relationship between the projectile tip geometry and impact energy absorption of semi-crystalline thermoplastics. The focus of the study is light-weight monolithic plates of extruded polymer impacted normally by rigid projectiles at velocities up to 100 ms−1. Three polymers will be considered: Low Density Polyethylene (LDPE), High Density Polyethylene (HDPE) and Ultra High Molecular Weight Polyethylene (UHMWPE). Polyethylene provides a convenient test material, as variations in microstructure provide a contrast in mechanical properties, without significant variations in density. Three distinct projectile nose shapes are considered: blunt, hemi-spherical and conical. For a conical tip, perforation occurs by ductile hole expansion. For this nose shape the high yield strength and strain rate sensitivity of HDPE offers an advantage over the other two polyethylenes. Perforation by blunt and hemi-spherical projectiles is more sensitive to deformation localisation. The high strain hardening of UHMWPE, which increases with strain rate, results in a significantly greater impact resistance than either HDPE or LDPE. The perforation mechanisms and energy absorption of these PE plates are contrasted with those of thin aluminium alloy targets that have the same total mass. UHMWPE outperforms these metallic targets for all three projectile nose shapes. Finally, the influence of target thickness on the impact perforation of LDPE is considered. All three nose shapes show a linear increase in perforation energy with target thickness.
Thermoplastic softening is one of the most desirable de-stiffening methods because of its reversibility, scalability, and applicability in many of current multi-layered structures without compromising structural performance. Despite the advantages, long activation times and high activation power requirements are generally considered as the main drawbacks for this method which can potentially limit its application in scenarios where fast de-stiffening is required. The aim of this study is to identify the key design requirements of heating element to minimise the de-stiffening response time using thermoplastic softening while maximising transparency. The focus of this study is on multilayer transparent structures, with low heating element content. A systematic investigation, including experimental and numerical investigation, is performed to study the effect of the fill factor and the heating element’s length scale on the response time of de-stiffening. Melting of the polymer and melting or electrical breakdown of the heating element are observed as practical limitations and are introduced as constraints to the design maps. The fill factor is found to have considerable influence on improving the response time, especially at low fill factors (i.e. below 10%). For the material combinations investigated here, the design maps show that heating elements with wire diameters up to 7 μm, at maximum transparency of 2% fill factor and up to 12 μm at 20% fill factor can achieve sub-second response times for temperature increase of 30⁰C. This new understanding will accelerate the technology readiness level of active structural control technology to be used in the future multi-functional and smart structures with a wide range of application in robotics, shape morphing, active damping, and active impact protection.
A laminated glass typically consists of two layers of glass and one layer of polymer. It is utilised in many applications in which the glazing is exposed to external threats like impact or blast. In this paper, damage development of laminated glass plates by soft impact is investigated in both low and high velocity regimes. Low velocity impacts (up to 4 ms-1 ) were conducted using a drop tower. Soft impact was achieved by attaching a silicon rubber cylinder to a flat steel impactor, with a diameter larger than that of the rubber, which itself is backed by a 16.9 kg weight. Different velocities were obtained by dropping the weight from various heights. For high velocity impacts (up to 220 ms-1 ), a gas gun apparatus was used. The silicon rubber cylinder was fired, using a sabot, in a 25 mm diameter barrel. High speed photography was employed to monitor the deformation and damage development in the laminated glass samples. Laminated glasses with different types of polymer interlayer were tested. The results show a better impact resistance for laminated glass with a stiffer polymer interlayer at both low and high velocity regimes.
The high velocity impact resistance of fibre metal laminates (FMLs) based on combinations of three different aluminium alloys (6161-O, 6061-T6, 7075-T6) and a glass fibre reinforced epoxy resin have been investigated both experimentally and numerically. A series of perforation tests on multilayer configurations, ranging from a simple 2/1 lay-up to a seven ply 4/3 laminate. High velocity impact was conducted using a projectile gas-gun launcher, operating in the velocity range between 119 m/s and 252 m/s.[1] The impact response of fibre metal laminates samples was characterised by determining the energy required to perforate the panels. A stereoscopic Digital Image Correlation (DIC) method was adopted to measure full-field deformations and strain for FMLs which providing the full field strain history and 3D measurements up to sample perforation. The perforation resistance of the panels was predicted using the finite element analysis package Abaqus/Explicit. A vectorized user-defined material subroutine (VUMAT) was employed to define Hashin’s 3D rate-dependant damage criteria for the composite layers. The subroutine was implemented into the commercial finite element software ABAQUS/Explicit to simulate the deformation and failure of FMLs. Agreement between the predictions of the finite element models and the experimental data was good across the range of configurations. Ballistic limit of those FMLs was obtained from both the experimental tests and numerical approaches.
Debonding between the skins and the core in a sandwich structure is a critical failure mode in automotive applications; once debonding occurs, the load carrying capacity of a sandwich structure drastically decreases. In the present paper, the effect of using three core materials, with different cell characteristics, on the interfacial strength between the foam cores and a CFRP skin is investigated through mechanical testing and numerical modelling. A key finding is that foams with a coarse cellular structure favour a high resin uptake at the interface during the manufacturing process, which results in a stronger interfacial bonding between the foam and the CFRP. During Mode I loading, the thick resin layer at the interface postpones crack initiation and kinking in the core, whilst under Mode II, this resin layer delays the collapse in compression of foam cells under the crack tip. Thus, the importance of including this thick resin layer in the FE modelling was demonstrated. Finally, as the CZM was shown to be unable to predict the unstable crack propagation within the core, an alternative approach was suggested which has the significant benefit of not requiring experimental testing of the interface between the skin and the core.
This paper outlines preliminary work developing graphene modified thermoplastic inserts to be used for the toughening of CFRP. The paper outlines laminate manufacture, mechanical testing and fracture analysis of graphene modified CFRP.
Extrusion-based metal direct writing is a promising metal additive manufacturing technology due to its high efficiency and low cost. However, fabricating parts with high integrity and complex geometry remains challenging. The most critical factor is the unavailable of semi-solid slurries with uniform and nearly spherical solid particles, resulting in uncontrollable extrusion and printing. Currently, mixed powder remelting (MPR) is reported to preset the features of the solid phases, including volume fraction, morphology, and size distribution. Specifically, the semi-solid slurries of hypoeutectic AlSi alloys were obtained by preheating and shearing the mixed powder composed of eutectic AlSi alloy powder and pure aluminum powder. Their microstructural characteristics and rheological behavior were investigated, demonstrating the microstructure tailoring (controllable solid fraction and size distribution, high shape factor of about 0.9) and the reduced viscosity fluctuation by a factor of 7 compared with traditional processes. MPR shows unparalleled advantages for further engineering applications of metal direct writing.
Bird strike can cause serious risks to the safety of air travel. In this paper, the aim is to improve design by determining deformation and damage mechanisms of laminated glass windows when subjected to high velocity soft impacts. To achieve this, laboratory-scale impact experiments using bird substitute materials were performed in the velocity range of 100–180 m s−1. An important step forward is that high-speed 3D Digital Image Correlation (DIC) has effectively been employed to extract the full-field deformation and strain on the back surface of the specimens during impact. The finite element simulations were performed in Abaqus/explicit using Eulerian approach and were able to represent successfully the experiments. For the laminated glass structures investigated, the damage inflicted is strongly sensitive to the nose shape of the projectile and most deleterious is a flat-fronted projectile. Two threshold velocities for impact damage have been identified associated with firstly the front-facing and secondly the rear-facing glass layer breaking. The order of the glass layers significantly influences the impact performance. The findings from this research study have led to a deeper and better-quantified understanding of soft impact damage on laminated glass windows and can lead to more effective design of aircraft windshields.
This study investigates the influence of the interlayer materials on the low velocity impact performance of laminated glass. By varying the impact velocity, with a drop-weight, the effect of impact energy levels (3, 5, 10 and 15 J) has been explored on the impact resistance of laminated glass and the failure mechanisms have been assessed. The four interlayer materials investigated were: SGP-Ionoplast as employed in Sentry Glas (R) Plus, TPU-Thermoplastic polyurethane, PVB-Polyvinyl butyral and a TPU/SGP/TPU hybrid interlayer. The drop weight method has been employed to obtain the energy dissipation, loading and deformation of the laminated glass. The low velocity impact results indicate that both the type of the interlayer materials and the impact energy have great influence on the impact performance of the laminated glass. The laminated glass with TPU and PVB interlayer exhibited better impact resistance than the laminated glass with SGP and TPU/SGP/TPU hybrid interlayer, when impacted at energies of 3 and 5J (corresponding to impact velocities of 1.71 and 2.21 ms(-1) respectively). However, the laminated glass with SGP and TPU/SGP/TPU hybrid interlayers has better load carrying capacity and better anti-deformation property than the TPU and PVB interlayers at the higher impact energies of 10 and 15J (impact velocities of 3.13 and 3.83 ms(-1) respectively). The results are thought to be attributed to the differences in the viscoelastic properties of the interlayer materials with strain rates.
This paper investigates the influence of the interlayer material on the low velocity impact performance of laminated glass. The effect of temperature (50°C, 23°C, 0°C and -30°C) has been explored to observe damage mechanisms and the associated impact resistant properties of the laminated glass. The four interlayer materials investigated were: SGP–Ionoplast as employed in Sentry Glas® Plus, TPU- Thermo-plastic polyurethane, PVB-Polyvinyl butyral and a TPU/SGP/TPU hybrid interlayer. The impact resistance was measured in terms of load peak, absorbed energy, ultimate deformation and crack patterns. The low velocity impact results indicated that both the type of the interlayer materials and testing temperature have great influence on the impact resistant properties of the laminated glass. The laminated glass with SGP interlayer exhibited best impact resistant properties amongst the four structures at room temperature. However, as the temperature was varied, the TPU/SGP/TPU hybrid interlayer performed the best over the entire range of temperatures tested, which can better ensure the safety of the occupants in the vehicle. This is because the elastic and viscous properties of the interlayer materials greatly changes with the temperature caused by the different glass transition temperatures of the interlayer materials.
The elastic-plastic deformation in raw and ion-exchanged aluminosilicate glass is investigated by loading rate dependent nanoindentation. The nanohardness and Young's modulus of the raw and ion-exchanged glasses at different loading rate (100–20,000 μN.s−1) are explored up to a maximum load of 9000 μN. The nanoindentations are scanned with AFM to observe the morphology of the indents. The results show that Young's modulus of the aluminosilicate glass increases after ion exchange and that the nanohardness of the raw and ion-exchanged aluminosilicate glass increases linearly with the loading rate, when plotted on a double logarithmic axes. However, the nanohardness of the raw glass is more sensitive to the variation of loading rate. The compressive stress on the ion-exchanged glass can inhibit plastic deformation. These results are explained in terms of shear stress underneath the indenter and the number of the flow lines in the nanoindentations. These findings are useful for better understanding the dynamic contact-induced damage growth mechanisms of ion-exchanged glass.
Polymeric foams are extensively used as the core materials in sandwich structures and the core material is typically bonded between relatively thin fibre-composite skins. Such sandwich structures are widely used in the aerospace, marine and wind-energy industries. In the present work, various sandwich structures have been manufactured using glass-fibre-reinforced polymer (GFRP) skins with three layers of poly(vinyl chloride) foam to form the core, with the densities of the foam layers ranging from 60 to 100 kg/m3. This study has investigated the effects on the quasi-static flexural and high-velocity impact properties of the sandwich structures of: (a) the density of the polymeric-foam core used and (b) grading the density of the foam core through its thickness. The digital image correlation technique has been employed to quantitatively measure the values of the deformation, strain and onset of damage. Under quasi-static three-point and four-point bend flexural loading, the use of a low-density layer in a graded-density configuration reduced the likelihood of failure of the sandwich structure by a sudden force drop, when compared with the core configuration using a uniform (i.e. homogenous) density layer. The high-velocity impact tests were performed on the sandwich structures using a gas-gun facility with a compliant, high-density polyethylene projectile. From these impact experiments, the graded-density foam core with the relatively low-density layer located immediately behind the front (i.e. impacted) GFRP skin was found to absorb more impact energy and possess an increased penetration resistance than a homogeneous core structure.
This study describes a novel and versatile method of incorporating graphene nano-platelets (GNP) into compos-ite laminates to investigate its effect on mode I and mode II interlaminar fracture toughness (ILFT). Non-woventhermoplastic veil interleaves have been modified by spray deposition with a GNP dispersion to give either a con-tinuous or strip-patterned distribution. The coated interleaves were used to modify the interlaminar region ofcarbonfibre reinforced polymer (CFRP) laminates. The fracture surfaces were characterised by scanning electronand optical microscopy.The continuous GNP distribution in mode I prevented the formation of carbonfibre bridging, resulting in similarinitiation and propagation values. In mode II, the increased thickness of the interlaminar region, coupled with theuneven fracture surface showed the highest increase in the mode II ILFT for the continuous GNP distribution. Thestrip-patterned GNP distribution showed reduced carbonfibre bridging compared to the baseline CFRP and ther-moplastic interleave laminates. This may be due to small scalefibre bridging between the deposited GNP-stripswhich also lead to peaks and troughs in the load-displacement response. In mode II, it is suggested that the de-posited GNP-strips were sufficiently tough to re-direct the propagating crack from the modified interlaminar re-gion to the adjacent ply.
Two polymeric foams have been characterised to develop a simple calibration process for extracting the parameters which are required by the material model available in the commercial FE package Abaqus. Indentation tests with DIC were conducted to study the validity of the proposed method.
Perforation resistance is an important design consideration for thin-walled metallic structures. However, the perforation energy of thin metallic plates is known to be sensitive to the nose shape of the indenter. This poses a challenge for predictive modelling, both analytical and numerical, as the material deformation and state of stress at the onset of failure can vary significantly from one indenter geometry to the next. Effective design requires an understanding of the key modelling parameters, and their influence on the predicted perforation response, across the widest range of possible indenter geometries. This paper aims to investigate systematically the indenter nose shape sensitivity of the quasi-static perforation of a 1 mm thick plate of aluminium alloy 6082-T4, and the modelling of the conditions at failure. The nose shape of the indenter is gradually changed from flat (i.e. blunt) to hemi-spherical either by (i) introducing a chamfer at the edge of the indenter or (ii) by changing the indenter frontal nose radius. This allows a wide range of states of deformation at the onset of failure to be spanned. The problem is investigated by both analytical and numerical methods. The results of both modelling techniques are compared with quasi-static perforation experiments, and the conditions necessary to achieve good agreement are obtained. Careful consideration of (i) material anisotropy, (ii) indenter-plate friction and (iii) boundary compliance is necessary for accurate prediction of the perforation energy. A Lode angle-dependent model for the onset of failure in the metal is found to be essential for predicting the perforation response for a range of indenter chamfer radii.
The choice of the materials used for the core and skin of a sandwich structure plays an extremely important role in the skin-core interfacial behaviour. In this paper, three PMI foams are used as core material and the effect of foam type in the skin-core interfacial response is examined.
Polymeric foams are used extensively as the core of sandwich structures in automotive and aerospace industries. Normally, several experiments are necessary to obtain the required properties to model the response of crushable foams using finite element analysis (FEA). Hence, this research aims to develop a simple and reliable calibration process for extracting the physical parameters which are required by the material model available in the commercial FE package Abaqus. To do this, a set of experimental tests, including uniaxial compression, uniaxial tension and shear punch tests, is proposed. All the experimental tests were also simulated, and generally, good correlations between experiments and numerical models were obtained. The validity of the overall approach was finally demonstrated using an indentation test in which the foam was subjected to a more complex mixed mode loading. During these indentation tests, digital image correlation was used to observe full-field strain distribution in the foam under the indenter. Good agreement between the experimental results and the numerical predictions was found for load–displacement response, failure mode and strain distribution.
Multiscale Topology Optimisation (MTO), by definition, operates over multiple length scales to achieve an optimised structural solution. Consequentially MTO can be computationally very expensive. Machine learning provides the opportunity to accelerate the process utilising surrogate models that approximate the behaviour of the system, allowing for faster evaluation and optimisation. This is particularly advantageous in scenarios where direct simulations at all scales are impractical or prohibitively time-consuming. In this study we demonstrate the effectiveness of a convolutional neural network (CNN) to map topologies of 2D micro-architectures to their corresponding stiffness property matrices. We utilise the topological dataset presented by Jiang et al [1] and generate the stiffness properties using 2D homogenisation [2] for micro-architectures made of a combination of printable polymeric materials (i.e. from a multi-material 3D printer such as an Object 260). We present a successful mapping, achieving results of R 2 greater than 99% and a mean average error of 0.012. Additionally, we examine the transferability of the initial learning of the above trained network. The trained mapping was used on the same topological dataset but with a different material combination. R 2 reduced to 34% and mean average error rose to 0.436. Mappings trained on one material combination will therefore be valid for only a small section of the total design space. To further explore the transferability of CNN, two architectures are proposed and evaluated. One network architecture employs transfer learning and the other incorporates branched connections which account for different printable material combinations. These models are assessed in terms of both the reduction in the computational cost, by leveraging the already trained CNN, and accuracy.
Advances in multi-material additive manufacturing have opened unprecedented new opportunities for the design and manufacture of lightweight multifunctional structures. The ability to create complex topologies, at a relatively fine resolution, in addition to controlling the material composition on a voxel basis have significantly expanded the design space. To explore this large design space efficiently, accurate and cost-effective modeling tools are essential. In this paper, mechanics-based models for predicting the elastic properties of multi-material 2D and 3D lattice structures are developed or extended. The outcomes are compared with the predictions obtained from finite element models and experimental data. The results reveal that the adapted analytical models demonstrate good accuracy in predicting the elastic modulus of multi-material lattices for relative densities up to approximately 25% while have considerably less computational cost compared to finite element using solid elements (providing the most accurate results in comparison with experiment). Careful consideration of the accuracy of the predictions is necessary for the use of these models for lattices with high relative density values. Besides, several homogenization-based models were studied to investigate their applicability to multi-material lattice structures when the assumption of scale-separation is considered valid. The capability of these models in predicting the whole elasticity tensor and the potential of multi-material lattices in manipulating the anisotropy are demonstrated. Finally, the introduced prediction frameworks are compared in order to provide an overview of their respective advantages and disadvantages in the case of multi-material lattice structures.
Recent research has established that polymer–metal laminates are able to provide enhanced impact perforation resistance compared to monolithic metallic plates of the same mass. A number of mechanisms have been proposed to explain this benefit, including the dissipation of energy within the polymer itself, and the polymer deformation enhancing dissipation within the metallic layer. This understanding of the layer interactions and synergies informs the optimisation of the laminate. However, the effect of the nose shape geometry of the projectile on perforation resistance of a particular laminate configuration has not been established. An optimal laminate configuration for one projectile may be sub-optimal for another. This investigation aims to clarify this nose shape sensitivity for both the quasi-static and impact perforation resistance of light-weight polymer–metal laminates. Bi-layer plates are investigated, with a polyethylene layer positioned on either the impacted or distal face of a thin aluminium alloy substrate. Three contrasting nose shapes are considered: blunt, hemi-spherical and conical. These have been shown to induce distinctly different deformation and fracture modes when impacting monolithic metallic targets. For all projectile nose shapes, placing a polyethylene layer on the impacted (rather than distal) face of the bi-layer plate results in an increase in perforation resistance compared to the bare substrate, by promoting plastic deformation in the metal backing. However, the effectiveness of the polymer in enhancing perforation resistance is sensitive to both the thickness of the polymer layer and the nose shape of the projectile. For a thin polyethylene layer placed on the impacted face, the perforation resistance is greatest for the blunt projectile, followed by the hemi-spherical and conical nose geometries. As the thickness of the polymer facing layer approaches the projectile radius, there is a convergence in both failure mode and perforation energy for all three nose shapes. Bi-layer targets can outperform monolithic metallic targets on an equal mass basis, though this is sensitive to the type of polyethylene used, the polymer layer thickness and the projectile nose shape. The greatest benefit of bi-layer construction (on an equal mass basis) is seen for blunt projectiles, using a polyethylene that maintains a high degree of strain hardening at high strain rates (i.e. UHMWPE), and a polymer thickness just sufficient to switch the failure mode in the metal layer from discing (failure at the projectile perimeter) to tensile failure at the plate centre.
The use of polymer layers to alter the impact response of metallic plates has emerged recently as an effective and economical means to enhance perforation resistance. However, the function of the polymer in such laminate systems remains unclear. In this investigation we aim to identify, through systematic experiments, the influence of a polymer layer on the perforation mechanisms and energy absorption of laminated plates. In particular, we consider the combination of a polymer with a thin metallic plate in a bi-layer configuration, subjected to either quasi-static or impact loading by a blunt indenter. Bi-layers are investigated which comprise an aluminium alloy layer (6082-T6) and a polyethylene layer (LDPE, HDPE and UHMWPE). It is found that the energy required to perforate the bi-layer plate can significantly exceed that of the bare metallic substrate (showing the potential for polymer coatings as an effective retro-fit solution) when the polymer is on the impacted face. Furthermore, bi-layer configurations are also shown to outperform the equivalent mass of monolithic metal if the correct thickness ratio of polymer and metal is selected. The effectiveness of a polymer layer in enhancing perforation energy is connected to its large ductility, allowing extensive deformation of the polymer under the indenter, which in turn suppresses plugging and diffuses plastic deformation in the metal layer. In this way the energy absorbed by the metal layer can be maximised. The thickness of the polymer layer is found to be a crucial parameter in maximising the effectiveness of the bi-layer target. An optimum polymer thickness is observed which maximises energy absorption per unit mass of bi-layer target (for a fixed substrate thickness). The synergy between metal and polymer layers also depends on the polymer type and the rate of loading. A polymer with high strain hardening performs best under impact conditions. However, under quasi-static loading, the bi-layer performance is less sensitive to the yield strength and strain hardening of the polymer.
The quasi-static flexural and impact performance, up to projectile impact velocities of about 270 m s−1, of fibre metal laminates (FMLs), which consist of relatively thin, alternately stacked, layers of an aluminium alloy and a thermoset glass fibre epoxy composite, have been investigated. The effects of varying (a) the yield strength, tensile strength and ductility of the aluminium alloy layer, (b) the surface treatment used for the aluminium alloy layers and (c) the number of layers present in the FML have been studied. It was found that increasing the strength of the aluminium alloy increases the quasi-static flexural strength of the FML, providing that good adhesion is achieved between the metal and the composite layers. Further, increasing the number of alternating layers of the aluminium alloy and fibre composite also somewhat increases the quasi-static flexural properties of the FML. In contrast, increasing the strength of the aluminium alloy had relatively little effect on the impact perforation resistance of the FML, but increasing the number of alternating layers of aluminium alloy and fibre composite did significantly increase the impact perforation resistance of the FML. The degree of adhesion achieved between the layers had only a negligible influence on the impact perforation resistance.
The choice of the materials used for the core and skin of a sandwich structure plays an extremely important role in the skin-core interfacial behaviour. In this paper, three PMI foams are used as core material and the effect of foam type in the skin-core interfacial response is examined.
Composite sandwich panels are well known for their relatively high stiffness over weight ratio and have been increasing utilized in various applications where the weight of the structure is a key design concern, e.g. in aircraft and aerospace components. However, these structures are vulnerable when subjected to a transverse impact loading. In this paper, the impact performance of composite sandwich structures with foam core is investigated. In particular, the idea of multi-layering the core by foam layers of different density and its effect on the energy absorption under low and high velocity impact is of interest. In this study, composite sandwich panels made of Glass Fibre Reinforced Polymers (GFRP) for skins and PVC foam for the core are used. Two different arrangements of foam core are considered: uniform core (80/80/80 kg/m3 ) and graded core (100/60/100 kg/m3 ). Both of these core arrangements have the same areal density. Low (up to 5 ms-1 ) and high (up to 200ms-1 ) velocity impact tests were performed using a drop tower and a gas gun respectively. In-plane and out-plane properties of composite sandwich samples were measured employing 2-D and 3-D Digital Imaging Correlation (DIC) methods. The results indicate that the composite sandwich structure with graded foam core has a better energy absorption capability compare to the one with uniform foam core.
Owing to their high strength and stiffness to mass ratio, composite sandwich structures have increasing been used for various engineering applications especially where mass has a direct influence on operating cost and performance. In sandwich structures, the core has an important role of separating and stabilising the skins as well as transferring shear and compressive stresses between the skins. Therefore, the core properties have a strong influence on the strength and perforation resistance of sandwich structures. In this study, the aim is to investigate the effect of grading the core on the structural as well as impact performance of sandwich panels made of GFRP skins and PVC foam core. Both low and high velocity impacts are considered. High speed 3D digital image correlation is employed to extract full-field displacement and strain contours during impact. Grading the core is found to result in a more stable failure process under quasi-static loading which can sustain larger deflections before final failure. Under impact loading, grading the core can improve the perforation resistance if a lower density core layer is immediately behind the impacted skin. The efficiency of grading, however, is influenced by the deformability of the impactor.
The choice of the polymer interlayer is a key consideration for laminated aircraft windshields. Such windshields often employ chemically strengthened glasses and are required to withstand impact by birds, hail-stones and other foreign bodies. In the present study, windshields employing three different polymer interlayer materials were investigated under high-velocity impact by a soft projectile: Thermoplastic Polyurethane (TPU), Polyvinyl Butyral (PVB) and Ionoplast interlayer-SentryGlas® Plus (SGP). Parameters such as the polymer interlayer type and thickness, multi-layering the interlayer and the sensitivity of the behaviour of the windshield to the environmental temperature were studied. The performance was assessed through a series of laboratory-scale impact experiments (using a bird-substitute material) and modelled via finite element simulations (using a smoothed particle hydrodynamics approach). The experimental and numerical results were found to be in good agreement for the three polymer interlayers investigated. The polymer interlayer type was found to have the most significant effect on both the deformation and the failure of the laminated glass windows at room temperature, i.e. 25°C. However, the influence of the polymer interlayer type became less pronounced at lower temperatures. The novel modelling that has been developed assists in the choice of the best polymer interlayer, including the multi-layering of interlayers, for complex windshield designs.
The effect of ion-exchange on the fracture behavior and the threshold load is investigated for radial crack initiation resulting from cube-corner indentation. Both tin and air sides of the sodium aluminosilicate float glass are considered. The threshold load and mechanical properties are experimentally measured by nanoindentation. A qualitative explanation of crack initiation is developed by analyzing the stresses at the indentation site. The ion-exchanged glasses show a lower threshold load for radial crack initiation with a cube-corner indenter than the raw glass, and this is due to a higher crack driving stress for ion-exchanged glasses. However, the compressive stress on the surface of the ion-exchanged glasses can inhibit the expanding of the radial cracks. The air side always shows higher values for the threshold load than the tin side before and after ion-exchange, which is in accordance with the calculated crack driving stress results.