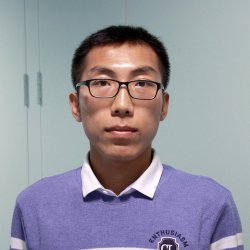
Dr Jianbing Gao
Publications
Gao Jianbing, Ma Chaochen, Tian Guohong, Chen Junyan, Xing Shikai, Huang Liyong (2018) Oxidation activity restoration of diesel particulate matter by aging in air,Energy & Fuels32(2)pp. 2450-2457 American Chemical Society
Diesel particulate matter (PM) was collected at different tailpipe positions where the sampling temperature was different. The PM samples were pre-treated in air at high temperature until 40% mass loss. Then, the partially oxidized PM samples were aged in air for 40 days, and the physicochemical properties of partially oxidized PM before and after aging in air were tested. The results showed that the oxidation activity of partially oxidized PM was appreciably restored by aging in air. The morphology, diameter distribution of primary particles and nanostructures of partially oxidized PM changed slightly after aging in air. The amorphous carbon adsorbing on PM surface were faintly observed through high resolution transmission electron microscope (HRTEM) images. The adsorption of oxygen-containing functional groups (carbonyl and hydroxy) and organic compounds were evidenced through Fourier transform infrared spectroscopy (FTIR) and Raman parameter AD3/AG. The crystallite size calculated using Raman parameter decreased slightly after aging in air.
Gao Jianbing, Tian Guohong, Ma Chaochen, Chen Junyan, Huang Liyong (2018) Physicochemical property changes during oxidation process for diesel PM sampled at different tailpipe positions,Fuel219pp. 62-68 Elsevier
Diesel particulate matter (PM) samples were collected at different tailpipe positions where sampling
temperature differed greatly. All the samples were pre-heated in air at high temperature until 40%
mass was burnt out. Physicochemical properties of diesel PM both before and after partial oxidation
were analyzed, and to further figure out the reasons of oxidation activity changes in the oxidation
process. The results showed that ignition temperature of PM whose sampling temperature was
higher than 208 °C differed greatly from PM sampled below that temperature. After partial
oxidation, sample 3 presented the hugest oxidation activity decreasing with burn out temperature
increasing by 14.7 °C. Primary particle size distribution shifted to smaller diameter direction after
partial oxidation, and particle stacking degree decreased evidently. Nanostructures of diesel PM
transferred from onion like structures with randomly arranged crystallite to core-shell like structures
with void inner cores. Oxygen-containing functional groups (carbonyl and hydroxy) decreased
evidently after PM partial oxidation that was obtained from Fourier transform infrared spectroscopy
(FTIR) spectra, it was consistent with the results of Raman parameter ID3/IG.
Yang Yuxin, Zhang Hongguang, Tian Guohong, Xu Yonghong, Wang Chongyao, Gao Jianbing (2018) Performance analysis of a multistage centrifugal pump used in an ORC system,Journal of Thermal Science Springer Verlag
In an Organic Rankine cycle (ORC) system, the working fluid pump plays an important role in the system performance. This paper focused on the operating characteristics of a multistage centrifugal pump at various speed and condensation conditions. The experimental investigation was carried out to assess the influence of the performance of the pump by the ORC system with special attention to actual net power output, thermal efficiency as well as back work ratio (BWR). The results showed that an increase in the pump speed led to an increase in the mass flow rate and expand in the operating range of the outlet pressure. The mass flow rate decreased nonlinearly with the increase of the outlet pressure from 0.22 to 2.41 MPa; the electric power consumption changed between 151.54 and 2409.34 W and the mechanical efficiency of the pump changed from 7.90% to 61.88% when the pump speed varied from 1160 to 2900 RPM. Furthermore, at lower pump specific speed the ORC system achieved higher thermal efficiency, which suggested that an ultra-low specific speed pump was a promising candidate for an ORC system. The results also suggested that the effects of condensation conditions on the pump performance decreased with the pump speed increasing and BWR was relatively sensitive to the condensation conditions, especially at low pump speed.
Gao Jianbing, Tian Guohong, Sorniotti Aldo, Karci Ahu Ece, Di Palo Raffaele (2019) Review of thermal management of catalytic converters to decrease engine emissions during cold start and warm up,Applied Thermal Engineering147pp. 177-187 Elsevier
Catalytic converters mitigate carbon monoxide, hydrocarbon, nitrogen oxides and particulate matter emissions from internal combustion engines, and allow meeting the increasingly stringent emission regulations. However, catalytic converters experience light-off issues during cold start and warm up. This paper reviews the literature on the thermal management of catalysts, which aims to significantly reduce the light-off time and emission concentrations through appropriate heating methods. In particular, methods based on the control of engine parameters are easily implementable, as they do not require extra heating devices. They present good performance in terms of catalyst light-off time reduction, but bring high fuel penalties, caused by the heat loss and unburnt fuel. Other thermal management methods, such as those based on burners, reformers and electrically heated catalysts, involve the installation of additional devices, but allow flexibility in the location and intensity of the heat injection, which can effectively reduce the heat loss in the tailpipe. Heat storage materials decrease catalyst light-off time, emission concentrations and fuel consumption, but they are not effective if the engine remains switched off for long periods of time. The main recommendation of this survey is that integrated and more advanced thermal management control strategies should be developed to reduce light-off time without significant energy penalty.
Gao Jianbing, Chen Haibo, Chen Junyan, Ma Chaochen, Tian Guohong, Li Ying (2019) Explorations on the continuous oxidation kinetics of diesel PM from heavy-duty vehicles using a single ramp rate method,Fuel248pp. 254-257 Elsevier
Particulate matter (PM) emitted by internal combustion engines has brought about serious environmental problems. Investigations of the PM oxidation behaviors and kinetics make the foundations of decreasing PM emission and working out the regeneration problems of PM capture devices. In this paper, the oxidation kinetics and microstructure evolutions of diesel PM in the oxidation process were researched. The results showed that thermogravimetric analysis (TGA) temperature history had a limited influence on the tendency of the oxidation kinetics. The volatilization of the organic compounds dominated the mass loss without any heat release at the initial stage of PM oxidation. The abnormal phenomenon (negative apparent activation energy) was observed in the oxidation process when the oxidation temperature was in the range of 200/°C?340/°C, which was ubiquitous during PM oxidation. However, the abnormal phenomenon disappeared if the PM sample was pre-treated to remove the volatile organic compounds (VOC), with the result that the phenomenon was caused by the VOC. The hydrogen bonding complex was formed in that temperature range, where the energy of the hydrogen bonding complex was lower than the value of the reactants, which caused the negative apparent activation energy. The apparent activation energy increased gradually when the temperature was higher than 340/°C.
Gao Jianbing, Chen Haibo, Tian Guohong, Ma Chaochen, Zhu Fei (2019) An analysis of energy flow in a turbocharged diesel engine of a heavy truck and potentials of improving fuel economy and reducing exhaust emissions,Energy Conversion and Management184pp. 456-465 Elsevier
The impetus of the internal combustion engine developments is the reductions of the fuel consumptions and exhaust emissions. Thermal management is an efficient method to decrease the exhaust emissions and enhance fuel economy. In order to further optimize the thermal management of internal combustion engines, a detailed analysis of the energy flow in each component of internal combustion engines is indispensable. In this paper, the test bench of a heavy duty diesel engine was established to obtain the target parameters. The energy distributions in each component of the diesel engine, including compressor, intercooler, shaft power, turbine, coolant and exhaust, were calculated using tested parameters. The lubricating oil consumption was also taken into consideration. In addition, the potential influences of different turbochargers on the total thermal efficiency were analyzed. The results showed that the thermal efficiency of the diesel engine was more than 38% when the engine operated at 50%?100% engine load and 1000/rpm?1700/rpm conditions. The energy loss by coolant was more than 50% of the total fuel energy consumption in the low power output conditions. However, it was lower than 30% in high power output conditions, and the thermal loss was more than 150/kW around rated power conditions. The maximum proportion of the energy being consumed by turbine was <10% of the fuel energy; additionally, the exhaust energy distributions changed significantly after the turbine expansion. 1%?3% of the fuel energy was recycled by the turbocharger, then, flowed into the cylinders. The energy loss through the intercooler accounted for <6% of the fuel energy. Significant reductions of exhaust emissions and fuel consumptions can be achieved by optimizing the coolant and lubricating oil thermal conditions. Turbochargers presented a huge effect on exhaust temperature distributions at high power output conditions, and the total thermal efficiency changed significantly if all kinds of energy recovery approaches were applied.
Gao Jianbing, Tian Guohong, Jenner Phil, Burgess Max, Emhardt Simon (2019) Preliminary explorations of the performance of a novel small scale opposed rotary piston engine,Energy116402 Elsevier Ltd
With the increasing pressure of fossil fuel consumption and pollutions from vehicles powered by internal combustion engines, much attention has been attracted for hybrid and electric vehicles. With this background, an increasing demand for compact and high power density engines is being developed for the purpose of hybrid vehicles. In this paper, the design of a novel opposed rotary piston engine was investigated. In comparison with conventional reciprocating engines, this design has no crank connecting rods and intake/exhaust valves, and the operation cycle takes 360° crank angle to complete but similar to a four stroke cycle. 3D and 1D simulations were conducted to analyse the in-cylinder flow and evaluate the engine performance. The simulation results indicated the air velocity was very high at the end of intake stroke due to the lack of intake valves. The opposed rotary piston engine had a higher fraction of constant volumetric combustion that yielded to less heat loss, which contributed to a higher power output per combustion cycle than a reciprocating engine at low engine speed. The estimated minimum brake specific fuel consumption and maximum power density were 240 g/(kW·h) and approximately 80 kW/L, respectively.
Xing Shikai, Gao Jianbing, Tian Guohong, Zhao Meng, Ma Chaochen (2020) Preliminary Investigations of an Opposed Rotary Piston Compressor for the Air Feeding of a Polymer Electrolyte Membrane Fuel Cell System,ACS Omega5(38)pp. 24733-24745 American Chemical Society
Automotive polymer electrolyte membrane fuel cell systems are attracting much attention, driven by the requirements of low automotive exhaust emissions and energy consumption. A polymer electrolyte membrane fuel cell system provides opportunities for the developments in different types of air compressors. This paper proposed an opposed rotary piston compressor, which had the merits of more compact structures, less movement components, and a high pressure ratio, meeting the requirements of polymer electrolyte membrane fuel cell systems. Preliminary performance evaluations of the opposed rotary piston compressor were conducted under various scenarios. This will make a foundation for optimizations of outlet pipe layouts of the compressor. A three-dimensional numerical simulation approach was used; further, in-cylinder pressure evolutions, fluid mass flow rates, and P?V diagrams were analyzed. It indicated that the cyclic period of the opposed rotary piston compressor was half of reciprocating piston compressors. The specific mass flow rate of the compressor is in the range of 0.094?0.113 kg·(s·L)?1 for the given scenarios. Outlet ports 1 and 2 dominated the mass flow in the discharge process under scenarios 1, 3, and 4. In-cylinder pressure profiles show multipeaks for all of these scenarios. In-cylinder pressure increased rapidly in the compression process and part of the discharge process, which led to high energy consumption and low adiabatic efficiency. The maximum adiabatic efficiency is approximately 43.96% among the given scenarios.
Gao Jianbing, Xing Shikai, Tian Guohong, Ma Chaochen, Zhao Meng, Jenner Phil (2021) Numerical simulation on the combustion and NOX emission characteristics of a turbocharged opposed rotary piston engine fuelled with hydrogen under wide open throttle conditions,Fuel285119210 Elsevier
Under the stress of environmental pollutions and fossil fuel consumption caused by on-road transport, hybrid vehicles are attracting much attention. Opposed rotary piston (ORP) engines are a promising power source for hybrid vehicles, due to their compact designs and high power density. In this paper, combustion and emission characteristics of a turbocharged ORP engine fuelled with hydrogen were investigated to evaluate the overall performance of this engine. The results indicated that volumetric efficiency of this ORP engine was higher than 89.0% for all the given cases. Peak in-cylinder pressure was in the range of 51.0 ~ 69.0 bar; and 4000 RPM scenario had the maximum value, being benefitted from high intake temperature and pressure, and high volumetric efficiency. Combustion duration of this engine ranged 27 ~ 43° crank angle (CA), and combustion phase happened at 7.5 ~ 13°CA after top dead centre (TDC). Peak nitrogen monoxide (NO) formation rates were corresponding to 5 ~ 13°CA after TDC; accumulated NO decreased slightly after reaching the peak value for low engine speed conditions. Discharge pressure at the start of the exhaust stroke was higher than 6.0 bar, especially for 5000 RPM case whose value was approximately 11.0 bar. This ORP engine presented excellent torque characteristics, and the maximum indicated power density was approximately 104.0 kW·L?1 which was much higher than turbocharged four-stroke reciprocating engines fuelled with gasoline.