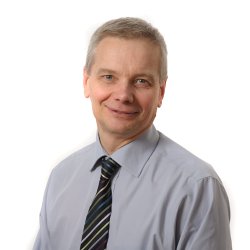
Professor John Chew
About
Research interests
- Fluid Dynamics, Heat Transfer and Aero-elasticity
- Methods for and Application of Computational and Theoretical Fluid Dynamics and Heat Transfer.
- Turbo-machinery internal flow systems and seals
Departmental duties
Professor of Mechanical Engineering
Editor of the Journal of Mechanical Engineering Science (Proc. IMechE Part C).
Technical Programme Chair for ASME Turbo Expo 2016.
Member of the Aerodynamics National Technical Committee.
Member of the Engineering and Physical Sciences Research Council College Peer Review College.
Current Research Programmes
- Large Eddy Simulation (LES) methods for flow and heat transfer prediction in rotating disc cavities
- Unsteady Simulation of Rim Sealing in Turbine Cavities
- Pre-Swirl Systems for Cooling Air Delivery
- Fluid-Solid Aero-Thermo-Mechanical Coupling for Industrial Flows
- Brush Seal Modelling
- Modelling Techniques for Buoyancy-affected Flow in Turbomachinery Disc Cavities
- Thermal Contact Resistance
Publications
Brush seals offer a superior sealing effectiveness compared to labyrinth seals. However, widespread use of brush seals is constrained by deleterious behaviors such as pressure-stiffening and hysteresis. For the latter, the bristles bend during the shaft incursion process and do not fully recover during the shaft retraction process. An opening gap is created, which increases seal leakage unless the pressure load drops to a certain level. In the present work, analytical and numerical models based on a single bristle are proposed to capture the seal’s response to shaft displacement with and without pressure loading. The models are validated using static stiffness tests at an unpressurized condition from literature. The main results show that modeling of the backing ring friction is essential to capture the bristle hang-up behavior. Shaft friction dominates at unpressurized conditions, while backing ring friction dominates at high pressure loading. An expression for shaft hang-up displacement has been derived. A sensitivity study shows that seals with shallow lay angle, short bristle length, and large bristle diameter are less prone to hang-up problems. The models developed in the present framework have been shown to qualitatively capture the pressure stiffening, hysteresis, bristle hang-up, and shaft rotation effects.
Code_Saturne, an open-source computational fluid dynamics (CFD) code, has been applied to a range of problems related to turbomachinery internal air systems. These include a closed rotor-stator disc cavity, a co-rotating disc cavity with radial outflow and a co-rotating disc cavity with axial throughflow. Unsteady Reynolds-averaged Navier-Stokes (RANS) simulations and large eddy simulations (LES) are compared with experimental data and previous direct numerical simulation (DNS) and LES results. The results demonstrate Code_Saturne's capabilities for predicting flow and heat transfer inside rotating disc cavities. The Boussinesq approximation was implemented into the code for modelling centrifugally buoyant flow and heat transfer in the rotating cavity with axial throughflow. This is validated using recent experimental data and CFD results. Good agreement is found between LES and RANS modelling in some cases, but for the axial throughflow cases, advantages of LES compared to URANS are significant for a high Reynolds number condition. The wall-modelled large eddy simulation (WMLES) method is recommended for balancing computational accuracy and cost in engineering applications.
Brush seals are plausible replacements for conventional labyrinth seals in gas turbine internal air systems. They can offer superior leakage performance due to their compliant nature and reduced effective clearance during operation. However, highly swirling flow and aerodynamic forces on the upstream bristles could lead to bristle back aero-elastic instability at high-shaft speed locations. Previous research has shown that the bristles in an idealized pack are displaced from their equilibrium position at swirl velocities of 150 m.s−1 and above for a bristle diameter of 0.1 mm. This study investigates grooves as a means of improving brush seal robustness in these locations by reducing inlet swirl incident on the bristle pack. A parametric study of a simple groove geometry was conducted using computational fluid dynamics (CFD) and a porous medium representation of the bristle pack to achieve representative seal leakages. Groove length, width, angle, and pitch were identified as important parameters for swirl reduction. The performance of ribs from previous research can be replicated and improved upon. A design of experiments (DOE) approach was implemented to investigate a novel groove design geometry. Combining a horizontal channel with an inclined groove enables a higher spacing to achieve the same swirl reduction due to drag and flow channeling/mixing effects at the inner radius. The resulting trends indicate that the novel design performs as intended for the selected boundary conditions in substantially reducing inlet swirl, thus helping to mitigate the above risk of premature seal deterioration and failure.
This paper addresses limitations of widely used Reynolds-averaged turbulence models (RANS) for prediction of gas turbine internal air systems. Results from direct numerical simulation (DNS), wall-resolved large-eddy simulation (LES), wall-modelled large-eddy simulation (WMLES), and RANS for benchmark test cases are compared. For rotor-stator disc cavity flows results for mean velocities, velocity fluctuations, rotor torque and laminar-turbulent transition are considered and compared with published data. For cavities between co-rotating discs attention is focused on buoyancy-driven convection in the centrifugal force field. It is concluded that WMLES is suitable for application in engine conditions, offering better accuracy than RANS in some critical applications. This confirms recently published results for turbine rim sealing and is further illustrated by application to convection in a sealed cavity at higher Rayleigh number than is practical with DNS or wall-resolved LES. The results show that the approximate near-wall treatment gives reasonable results for complex flows and extend previous studies to higher speed rig conditions where Eckert number effects become significant.
Flow and heat transfer in an aero-engine compressor disk cavity with radial inflow has been studied using computational fluid dynamics (CFD), large eddy simulation (LES), and coupled fluid/ solid modeling. Standalone CFD investigations were conducted using a set of popular turbulence models along with 0.2 deg axisymmetric and a 22.5 deg discrete sector CFD models. The overall agreement between the CFD predictions is good, and solutions are comparable to an established integral method solution in the major part of the cavity. The LES simulation demonstrates that flow unsteadiness in the cavity due to the unstable thermal stratification is largely suppressed by the radial inflow. Steady flow CFD modeling using the axisymmetric sector model and the Spalart-Allmaras turbulence model was coupled with a finite element (FE) thermal model of the rotating cavity. Good agreement was obtained between the coupled solution and rig test data in terms of metal temperature. Analysis confirms that using a small radial bleed flow in compressor cavities is effective in reducing thermal response times for the compressor disks and that this could be applied in management of compressor blade clearance.
This research paper presents a CFD analysis of small scale ORC scroll expanders using variable and constant wall thicknesses by providing back-to-back aerodynamic performance comparisons. The evaluation of the three-dimensional and transient CFD results shows that the shorter scroll profile length of the variable wall thickness design (VWD) generated lower average radial and axial gas forces. In addition, higher pressure gradients in between individual working chambers contributed to a higher peak of the tangential gas moment despite higher transient gas force and tangential gas moment variations. Moreover, the pressure trace analysis reveals that the expansion process was finished at a crank angle of 816° in VWD, compared to 996° in the constant wall thickness design (CWD). The studies of the static pressure distributions along the surface of the fixed scroll of the two geometries indicate that static pressure drops through local radial clearances were higher in VWD. However, a higher number of static pressure drops occurred in CWD. The expansion process of CWD was driven by lower pressure gradients resulting in a complete dissipation of the large-scale vortices in the expansion chambers of CWD at the crank angle of 672°, in contrast to 600° in the expansion chambers of VWD.
This study investigates turbine rim seal geometry effects within the rotationally-driven ingestion regime. Computations were performed with a wall-resolved unsteady Reynolds-averaged Navier-Stokes (URANS) model and a large-eddy simulation (LES) model including near-wall boundary layer modelling , that is wall-modelled LES (WMLES). Use of simplified rim sealing models is proposed as an efficient method of ranking seal designs and investigating sensitivity to seal geometry. Four rim seal configurations, two chute seals, an axial seal and a radial seal which are representative of those used in gas turbines and in previous research were investigated. Furthermore, hybrid seals combining geometric characteristics from both the chute and radial seal were considered. Significant sensitivities of sealing performance to turbulence modelling are identified, but URANS and WMLES show similar trends in ranking of seal performance, and these are consistent with previous experimental work. The addition of an outer radial clearance section to a chute seal is effective in reducing ingestion levels.
Brush seals are plausible replacements for conventional labyrinth seals in gas turbines for managing internal air system flows and leakages. They can offer superior leakage performance compared to labyrinth seals due to their compliant nature, and a reduced effective clearance during operation. Despite their improved sealing performance, highly swirling flow and aerodynamic forces on the upstream bristles could lead to aero-elastic instability within the bristle pack. This study investigates grooves as a means of improving brush seal robustness in high-shaft speed locations by reducing the inlet swirl that is incident on the bristle pack. The material removed and implied manufacturing effort and cost are considered. A parametric study of a simple groove geometry was conducted using CFD and a porous medium representation of the bristle pack whose resistance coefficients were calibrated to Bayley and Long’s data to achieve representative seal leakages. This identified groove length, width, angle and pitch as the important groove parameters for swirl reduction and demonstrated that the performance of ribs from previous research can be replicated and improved upon. A Design of Experiments (DOE) approach was adopted to investigate a novel groove design geometry. Combining a horizontal channel with an inclined groove enables a higher pitch to achieve the same swirl reduction by increasing drag and exploiting fluidic effects. The results indicate that the novel groove design performs as intended in substantially reducing the swirl incident on the bristle pack. Adding these features to the traditional front plate may improve brush seal robustness by reducing the effect of aerodynamic forces which could drive bristle pack instabilities, thus having the potential to aid their deployment in high-radius or high-shaft speed engine locations.
CFD-FEA Simulation of Leaf Seal Dynamics * Ramesh Kumar, * Michael J. Pekris, * John W. Chew, * Dario Amirante and * Nicholas J. Hills AIAA 2018-4897 AVS-03: High-Speed Simulation and Drag Reduction Testing • Wednesday, 11 July 2018 • 1600 hrs https://doi.org/10.2514/6.2018-4897
For many gas turbine architectures a failure modes and effects analysis identifies a potential mode in which failure of an oil transfer pipe could result in oil leakage into the secondary air system. Such an event would result in a complex two-phase interacting flow The atomisation and transport of the oil within the air system is of interest, but is difficult to predict. Available data for the droplet size resulting from jet breakup in cropflow are limited. A dimensional analysis shows jet breakup in a crossflow to involve many factors. The atomisation process has been shown experimentally to include many physical processes and is still not completely understood. Current v, the most practical method of modelling these breakup processes in sprays is by using a CFD package with a set of sub-models within an Euler-Lagrangian (discrete-droplet) approach, The strengths and weaknesses of each of these sub-models cannot reasonably, he tested when used in combination with other approximations to model a spray in crossflow. The purpose of this study was to assess various submodels for liquid breakup with a series of simple test cases.
The leakage and transport of oil within secondary air system cavities is of interest in oil and air system design, for which CFD can be used as a predictive tool. This paper focuses on the leakage of oil from cracks into a high speed crossflow, idealised as round nozzles at Weber numbers and momentum flux ratios relevant to those in an aero-engine. Simulations were performed using the Euler-Lagrangian approach implemented in a commercial CFD code (FLUENT), including sub-models for breakup, deforming droplet drag, collisions/coalescence and turbulent dispersion. CFD predictions were compared with experimental data from two independent studies. The calculated position of the centre-of-mass of the spray plume agreed well with experiment in all cases, but the penetration was found to be under-estimated. Differences in droplet sizes between experiments could not be explained by variations in the the gas Weber number alone, and a review of the literature has highlighted the importance of the liquid to gas viscosity ratio in determining droplet size trends. Experimental trends in droplet size with changing viscosity ratios were captured by CFD simulations, and droplet SMD was predicted within 20% of experiment. It is concluded that the sub-models used within an Euler-Lagrangian approach can be useful tools for the prediction of droplet size, although further improvements in breakup and coalescence modelling will be necessary if greater accuracy is required.
Copyright © 1994 by ASME.Sealing of the cavity formed between a rotating disc and a stator with an asymmetric external flow is considered. In these circumstances circumferential pressure variations in the external flow and the pumping action of the disc may draw fluid into the cavity. Gas concentration measurements, showing this effect, have been obtained from a model experiment with a simple axial clearance seal. In the experiment, guide vanes, fitted upstream of the rim seal, generate an asymmetric external flow. The measurements are shown to be in reasonable agreement with three-dimensional computational fluid dynamics (CFD) calculations and are also compared with more elementary models. The CFD results give further insight into the effects of ingestion within the cavity.
Abstract A chute rim seal cavity has been instrumented with time resolved and time-averaged pressure transducers as well as a gas concentration measurement system at the Oxford Rotor Facility. The unsteady pressure transducers were unevenly distributed along the circumference generating 15 combinations of angular spacing to conduct a phase analysis. The test operating conditions were modified through different configurations of mainstream flow, a range of rotational speeds and purge flows to obtain test data in the regimes of rotationally-driven, pressure-driven and combined ingestion. The rotating unsteady flow structures within the rim seal cavity were studied through a combination of phase analysis of dynamic pressure signals and inspection of the frequency domain. The introduction of mainstream flow (axial and swirled) increased the overall unsteadiness exciting an additional band of lower frequencies. The phase analysis revealed these were associated with acoustic waves, providing the first experimental evidence of the presence and coexistence of inertial and acoustic waves in the rim seal cavity. The interaction of the inertial and acoustic waves strongly depends on the operating conditions, and may be linked to changes in sealing effectiveness.
Large and flexible wind turbine blades may be susceptible to severe blade deformations coupled with dynamic stall. To advance prediction capability for this problem a general deforming mesh computational fluid dynamics (CFD) method has been developed for calculating flows with moving or deforming boundaries using an elastic spring analogy. The method has been evaluated against experimental data for flow around a pitching NACA0012 airfoil in the deep dynamic stall regime where flow is highly separated, and compared with other authors0 CFD simulations for pitching airfoil. The effects of varying the reduced frequency are also investigated. During the upstroke the present results are in generally good agreement with experiment and other CFD studies. During the downstroke some differences with experiment and other CFD models are apparent. This may be due to the sensitivity of the separated flow to modelling assumptions and experimental conditions. Overall, the degree of agreement between CFD and experiment is considered encouraging.
A systematic study of sealing performance for a chute style turbine rim seal using URANS methods is reported. This extends previous studies from a configuration without external flow in the main annulus to cases with a circumferentially uniform axial flow and vane generated swirling annulus flow (but without rotor blades). The study includes variation of the mean seal-to-rotor velocity ratio, main annulus-to-rotor velocity ratio, and seal clearance. The effects on the unsteady flow structures and the degree of main annulus flow ingestion into the rim seal cavity are examined. Sealing effectiveness is quantified by modeling a passive scalar, and the timescales for the convergence of this solution are considered. It has been found that intrinsic flow unsteadiness occurs in most cases, with the presence of vanes and external flow modifying, the associated flow structures and frequencies. Some sensitivities to the annulus flow conditions are identified. The circumferential pressure asymmetry generated by the vanes has a clear influence on the flow structure but does not lead to higher ingestion rates than the other conditions studied.
Code_Saturne, an open-source computational fluid dynamics (CFD) code, has been applied to a range of problems related to turbomachinery internal air systems. These include a closed rotor-stator disc cavity, a co-rotating disc cavity with radial outflow and a co-rotating disc cavity with axial throughflow. Unsteady Reynolds-averaged Navier–Stokes (RANS) simulations and large eddy simulations (LES) are compared with experimental data and previous direct numerical simulation and LES results. The results demonstrate Code_Saturne's capabilities for predicting flow and heat transfer inside rotating disc cavities. The Boussinesq approximation was implemented for modelling centrifugally buoyant flow and heat transfer in the rotating cavity with axial throughflow. This is validated using recent experimental data and CFD results. Good agreement is found between LES and RANS modelling in some cases, but for the axial throughflow cases, advantages of LES compared to URANS are significant for a high Reynolds number condition. The wall-modelled large eddy simulation (WMLES) method is recommended for balancing computational accuracy and cost in engineering applications.
This experimental study considered the performance of a chute rim seal downstream of turbine inlet guide vanes (but without rotor blades). The experimental set up reproduced rotationally-driven ingestion without vanes and conditions of pressure-driven ingestion with vanes. The maximum rotor speed was 9000 rpm corresponding to a rotational Reynolds number of 3x106 with a flow coefficient of 0.48. Measurements of mean pressures in the annulus and the disc rim cavity as well as values of sealing effectiveness deduced from gas concentration data are presented. At high values of flow coefficient (low rotational speeds), the circumferential pressure variation generated by the vanes drove relatively high levels of ingestion into the disc rim cavity. For a given purge flow rate, increasing the disc rotation speed led to a reduction in ingestion shown by higher values of sealing effectiveness despite the presence of upstream vanes. At 𝑈𝑎𝑥(Ω𝑏)⁄=0.48, the sealing effectiveness approached that associated with purely rotationally-driven ingestion. A map of sealing effectiveness against non-dimensional purge flow summarises the results and illustrates the combined rotational and pressure-driven effects on the ingestion mechanism. The results imply that flow coefficient is an important parameter in rim sealing and that rotational effects are important in many applications, especially turbines with low flow coefficient.
This paper presents a numerical investigation of buoyancy-driven flow in a closed rapidly rotating disc cavity. Pseudo two-dimensional models are considered, with periodic boundary conditions on a thin axial domain. An incompressible model, in which density variation is considered with the Boussinesq approximation, is evaluated through comparisons with a full compressible model. Effects of property (viscosity) variation and dependency on buoyancy parameter (ß∆T) and rotational Reynolds number for a given Rayleigh number, are investigated with the full compressible model. The mean centrifugal and radial Coriolis forces are analysed. Heat transfer predictions from the Boussinesq and compressible models agree to within 10%, for ß∆T ≤ 0.2.
This study focuses on the sealing capability of a turbine rim seal subject to hot gas ingestion driven purely by the rotor disc pumping effect rather than that induced by mainstream features such as vane and rotor blade passing. The aim is to provide useful data for conditions in which rotation dominates, and to clarify the flow physics involved in rim sealing. Experimental measurements of sealing effectiveness for a chute seal are presented for the first time without and with an axial, axisymmetric mainstream flow external to the seal. The test matrix covers a range of rotational Reynolds number, Re , from 1.5x106 to 3x106, and nondimensional flow rate, C , from 0 to 4x104 with the mainstream flow (when present) scaled to match engine representative conditions of axial Reynolds number, Re . Results from steady pressure and gas concentration measurements within the rotor-stator disc cavity and the rim seal gap are presented and compared to published data for other seal designs. Sealing performance of the chute seal is somewhat similar to that of axial clearance seals with the same minimum clearance.
Natural convection in differentially heated enclosures is a benchmark problem used to investigate the physics of buoyant flows and to validate numerical methods. Such configurations are also of interest in engineering applications such as cooling of electronic components and air flow around buildings. In this work a spectral element method is used to carry out direct numerical simulations of natural convection in a tall enclosure of aspect ratio 4 with isothermal vertical walls and adiabatic horizontal walls. Spectral element methods combine the flexibility of classical finite element methods with the high accuracy and efficiency of single-domain spectral methods. The flow is solved in a three-dimensional domain with periodic boundary conditions imposed in the third direction. The numerical results are compared with solutions available in the literature and with numerical results obtained using a commercial software that employs a low-order finite volume method. Good agreement with previous work is obtained for the value of the Rayleigh number investigated, Ra = 2E9, which is greater than the critical value of Ra where transition to an unsteady, chaotic state is known to occur. The results are presented in terms of the time-averaged flow structure, Reynolds stresses and modal energies. Although the time-averaged velocity and temperature fields obtained with a commercial finite volume code are in general good agreement with the results obtained with the spectral element code, it does not give accurate predictions of second-order statistics.
In axial gas turbines, hot air from the main annulus path tends to be ingested into the turbine disc cavities. This leads to overheating which will reduce the disc’s life time or lead to serious damage. Often, to overcome this problem, some air is extracted from the compressor to cool the rotor discs. This also helps seal the rim seals and to protect the disc from the hot annulus gas. However, this will deteriorate the overall efficiency. A detailed knowledge of the flow interaction between the main gas path and the disc cavities is necessary in order to optimise thermal effectiveness against overall efficiency due to losses of the cooling air from the main gas path. The aim of this study is to provide better understanding of the flow in a turbine stator-well, and evaluate the use of different CFD methods for this complex, 3-dimensional unsteady flow. This study presents CFD results for a 2-stage turbine. The stator-well cavity for the second row of stationary vanes is included in the calculation and results for both turbine performance and stator-well sealing efficiency are presented.
Sealing of the cavity formed between a rotating disc and a stator with an asymmetric external flow is considered. In these circumstances circumferential pressure variations in the external flow and the pumping action of the disc may draw fluid into the cavity. Gas concentration measurements, showing this effect, have been obtained from a model experiment with a simple axial clearance seal. In the experiment, guide vanes, fitted upstream of the rim seal, generate an asymmetric external flow. The measurements are shown to be in reasonable agreement with three-dimensional computational fluid dynamics (CFD) calculations and are also compared with more elementary models. The CFD results give further insight into the effects of ingestion within the cavity.
Buoyancy-induced flows occur in the rotating cavities of gas turbine internal air systems, and are particularly challenging to model due to the inherently unsteadiness of these flows. While the global features of such flows are well documented, detailed analyses of the unsteady structure and turbulent quantities have not been reported. In this work we use a high-order numerical method to perform large-eddy simulation (LES) of buoyancyinduced flow in a sealed rotating cavity with either adiabatic or heated disks. New insight is given into long-standing questions regarding the flow characteristics and nature of the boundary layers. The analyses focus on showing time-averaged quantities, including temperature and velocity fluctuations, as well as on the effect of the centrifugal Rayleigh number on the flow structure. Using velocity and temperature data collected over several revolutions of the system, the shroud and disk boundary layers are analysed in detail. The instantaneous flow structure contains pairs of large, counter-rotating convection rolls, and it is shown that unsteady laminar Ekman boundary layers near the disks are driven by the interior flow structure. The shroud thermal boundary layer scales as approximately Ra−1/3 , in agreement with observations for natural convection under gravity.
Brush seals can be used in the secondary air systems of gas and steam turbines to reduce parasitic leakages and engine specific fuel consumption. Application of these seal types in highly pressurised and highly swirling environments is limited due to the inherent risk of aerodynamic instability and seal failure. This paper considers coupled 3D CFD and structural modelling of brush seals, and applies the technique to investigate the effects of inlet swirl on the bristle pack. The model applies aerodynamic forces generated by CFD to a bristle pack model that includes interaction between bristles. Iteration between CFD and structural models is used to ensure consistency between the fluid and structural solutions. Inlet swirl is shown to increase bristle circumferential aerodynamic forces. At a critical value of inlet swirl, the aerodynamic force on the upstream bristles is sufficient to cause circumferential slip of the upstream bristle row, despite axial compression of the bristle pack under its operating differential pressure. In practice this may lead to instability of the bristle pack and is consistent with anecdotal reports of seal behavior. The critical swirl velocity was reduced when the downstream pressure level was raised, keeping the same upstream total to downstream static pressure difference. This is caused by the increased dynamic head associated with the inlet swirl. Inclusion of a front plate in the seal design does not offer the intended protection to the bristle pack in highly swirling environments, and in fact further lowers the critical swirl velocity where bristle slip occurs. This is associated with highly swirling flow impinging on the bristle tips. Increasing the bristle diameter and bristle stiffness does not necessarily prevent slip at higher inlet swirl velocities, but reduces the magnitude of slip of the upstream bristles.
A combined computational fluid dynamics (CFD) and experimental study of interaction of main gas path and rim sealing flow is reported. The experiments were conducted on a two stage axial turbine and included pressure measurements for the cavity formed between the stage 2 rotor disc and the upstream diaphragm for two values of the diaphragm-to-rotor axial clearance. The pressure measurements indicate that ingestion of the highly swirling annulus flow leads to increased vortex strength within the cavity. This effect is particularly strong for the larger axial clearance. Results from a number of steady and unsteady CFD models have been compared to the measured results. Good agreement between measurement and calculation for time-averaged pressures was obtained using unsteady CFD models, which predicted previously unknown unsteady flow features. This led to fest response pressure transducer measurements being made on the rig, and these confirmed the CED prediction.
Considerable progress in development and application of computational fluid dynamics (CFD) for aeroengine internal flow systems has been made in recent years. CFD is regularly used in industry for assessment of air systems, and the performance of CFD for basic axisymmetric rotor/rotor and stator/rotor disc cavities with radial throughflow is largely understood and documented. Incorporation of three-dimensional geometrical features and calculation of unsteady flows are becoming commonplace. Automation of CFD, coupling with thermal models of the solid components, and extension of CFD models to include both air system and main gas path flows are current areas of development. CFD is also being used as a research tool to investigate a number of flow phenomena that are not yet fully understood. These include buoyancy-affected flows in rotating cavities, rim seal flows and mixed air/oil flows. Large eddy simulation has shown considerable promise for the buoyancy-driven flows and its use for air system flows is expected to expand in the future.
Thermal analysis of a turbine disc through a transient test cycle is demonstrated using 3D computational fluid dynamics (CFD) modeling for the cooling flow and 3D finite element analysis (FEA) for the disc. The test case is a 3D angular sector of the high pressure (HP) turbine assembly of a civil jet engine and includes details of the coolant flow around the blade roots. Proprietary FEA and CFD solvers are used to simulate the metal and fluid domains, respectively. Coupling is achieved through an iterative loop with smooth exchange of information between the FEA and CFD simulations at each time step, ensuring consistency of temperature and heat flux on the coupled interfaces between the metal and fluid domains. The coupled simulation can be completed within a few weeks using a PC cluster with multiple parallel CFD executions. The FEA/CFD coupled result agrees well with corresponding rig test data and the baseline 3D and 2D FEA solutions, which have been calibrated using test data. Provision of upstream boundary conditions and modeling of rapid transients are identified as areas of uncertainty. Averaging of CFD solutions and relaxation is used to overcome difficulties caused by CFD oscillations associated with flow unsteadiness. The present work supports the continued use and development of the FEA/CFD coupling method for industrial applications. Copyright © 2012 by ASME.
The proposed study aims to evaluate the feasibility of a range extender scroll engine by means of an analytical heat release rate analysis. This novel engine technology is comprising an upstream compressor and a downstream scroll expander which is mechanically connected and drives the compressor. Hence, the compression and expansion processes of the air-fuel mixture are decoupled which enables the possibility to apply higher expansion than compression ratios resulting in a scroll engine combustion process being similar to the Miller or Aktinson cycle. The scroll engine performance in terms of power output and thermal efficiency was accordingly evaluated for two compression ratios of 8.2:1 and 10.1:1 and six corresponding expansion ratios in the range of 8.2:1 to 17.8:1. It has been proven that high compression ratios are beneficial for the power output as more fuel can be introduced into the expander part. At a constant compression ratio, the power output increased for a rising expansion ratio but at the expense of a reduced power density. The evaluation revealed a peak value of 44.48kW at a compression ratio of 10.1:1 and an expansion ratio of 17.8:1. A more thorough expansion process due to the implementation of a Miller/Aktinson cycle resulted in a significantly increasing thermal efficiency for a rising ratio of expansion to compression ratio reaching a peak value
This paper presents WMLES simulations of a chute type turbine rim seal. Configurations with an axisymmetric annulus flow and with nozzle guide vanes fitted (but without rotor blades) are considered. The passive scalar concentration solution and WMLES are validated against available data in the literature for uniform convection and a rotor-stator cavity flow. The WMLES approach is shown to be effective, giving significant improvements over an eddy viscosity turbulence model, in prediction of rim seal effectiveness compared to research rig measurements. WMLES requires considerably less computational time than wall-resolved LES, and has the potential for extension to engine conditions. All WMLES solutions show rotating inertial waves in the chute seal. Good agreement between WMLES and measurements for sealing effectiveness in the configuration without vanes is found. For cases with vanes fitted the WMLES simulation shows less ingestion than the measurements, and possible reasons are discussed.
Copyright © 1989 by ASME.Sealing of the cavity formed between a stationary disc and a rotating disc under axisymmetric conditions is considered. A mathematical model of the flow in the cavity based on momentum integral methods is described and this is coupled to a simple model of the seal for the case when no ingress occurs. Predictions of the minimum imposed flow required to prevent ingress are obtained and shown to be in reasonable agreement with the data of Bayley and Owen (1970), Owen and Phadke (1982), Phadke (1982), and Phadke and Owen (1982, 1983, 1988). With an empirical constant in the model chosen to match this data predictions for the minimum sealing flow are shown to be in good agreement with Graber et al's (1987) measurements. The analysis of Phadke's data also indicates the measurements for small seal clearances must be viewed with caution due to errors in setting the seal clearance. These errors are estimated to be twice the minimum clearance considered. Seal behaviour when ingress occurs is also considered and estimates of the amount of ingress are made from the available data.
The effects of surface roughness on air-riding seals are investigated here using the Rayleigh-pad as an example. Both incompressible and compressible flows are considered using both CFD analysis and analytical/numerical solutions of the Reynolds equation for various 2D or 3D roughness patterns on the stationary wall. A 'unit-based' approach for incompressible flows has also been employed and is shown to be computationally much less expensive than the full-geometry solution. Results are presented showing the effect of surface roughness on the net lift force. The effects of varying the Reynolds number are demonstrated, as well as comparative results for static stiffness.
Copyright © 1988 by ASME.Finite difference solutions are presented for turbulent flow in the cavity formed between a rotating and a stationary disc, with and without a net radial outflow of fluid. The mean flow is assumed steady and axisymmetric and a mixing length model of turbulence is used. Grid dependency of the solutions is shown to be acceptably small and results are compared with other workers' experimental data. Theoretical and measured disc moment coefficients are in good agreement, while theoretical and measured velocities are in reasonable agreement. It is concluded that the mixing-length model is sufficiently accurate for many engineering calculations of boundary layer dominated flows in rotating disc systems.
This paper describes Large-Eddy Simulations (LES) of the flow in a rotating cavity with narrow inter-disc spacing and a radial inflow introduced from the shroud. Simulations have been conducted using a compressible, unstructured, finite-volume solver, and testing different subgrid scale models. These include the standard Smagorinsky model with Van Driest damping function near the wall, the WALE model and the implicit LES procedure. Reynolds averaged Navier-Stokes (RANS) results, based on the Spalart-Allmaras and SST k − ω models, are also presented. LES solutions reveal a turbulent source region, a laminar oscillating core with almost zero axial and radial velocity and turbulent Ekman type boundary layers along the discs. Validations are carried out against the experimental data available from the study of Firouzian et al. [1]. It is shown that the tangential velocity and the pressure drop across the cavity are very well predicted by both RANS and LES, although significant differences are observed in the velocity profiles within the boundary layers.
This paper considers 3D CFD and structural modelling of brush seals, and investigates the effects of inlet swirl on the bristle pack. The model couples aerodynamic forces generated by CFD to a structural model that includes interaction between bristles. At a critical value of inlet swirl, aerodynamic forces cause circumferential slip of the upstream bristle row. In practice this may lead to instability of the bristle pack and is consistent with anecdotal reports of seal behavior. The critical swirl velocity was reduced when the downstream pressure level was raised, keeping the same upstream total to downstream static pressure difference. This is caused by the increased dynamic head associated with the inlet swirl. Inclusion of a front plate in the seal design does not offer the intended protection to the bristle pack in highly swirling environments. This is associated with highly swirling flow impinging on the bristle tips. Fitting of roughness elements on the upstream face of the front plate could improve stability by reducing swirl of the flow impacting on the bristles. Increasing the bristle diameter and bristle stiffness does not necessarily prevent slip at higher inlet swirl velocities, but reduces the magnitude of slip of the upstream bristles.
To achieve enhanced cooling of hot components in the high pressure (HP) section of an aeroengine, application of cooled cooling air (CCA) has been proposed. Here a “two row preswirl feed” arrangement is considered to accommodate the CCA, together with the uncooled cooling air (UCA) in high pressure turbine (HPT) preswirl cavity. The CCA and UCA inflows are introduced into the preswirl cavity at two different radii. Most of the cooling air leaves the preswirl cavity from the receiver holes. To assess the CCA behavior in the preswirl cavity, a definition of feeding effectiveness is introduced based on the relative total temperature at the exit of the receiver hole. The CFD investigation for the preswirl cavity was conducted in a systematic way by altering both the radial position of the receiver hole and inflows of the CCA and UCA, while keeping other conditions unchanged. It was found that the feeding effectiveness increases as the radial position of the receiver hole decreases. An optimal feeding effectiveness close to a minimum mixing condition was achieved by adjusting the CCA and UCA inflows. Unsteady CFD investigations gave a similar prediction for the overall performance of the CCA in the preswirl cavity, but with a lower feeding effectiveness compared with its steady CFD counterpart. The reduction in the feeding effectiveness was attributed to an enhanced mixing from the discrete CCA and UCA inflows and associated unsteady effects.
In this paper large-eddy simulation is used to study buoyancy-induced flow in a rotating cavity with an axial throughflow of cooling air. This configuration is relevant in the context of secondary air systems of modern gas turbines, where cooling air is used to extract heat from compressor disks. Although global flow features of these flows are well understood, other aspects such as flow statistics, especially in terms of the disk and shroud boundary layers, have not been studied. Here, previous work for a sealed rotating cavity is extended to investigate the effect of an axial throughflow on flow statistics and heat transfer. Time- and circumferentially-averaged results reveal that the thickness of the boundary layers forming near the upstream and downstream disks is consistent with that of a laminar Ekman layer, although it is shown that the boundary layer thickness distribution along the radial direction presents greater variations than in the sealed cavity case. Instantaneous profiles of the radial and azimuthal velocities near the disks show good qualitative agreement with an Ekman-type analytical solution, especially in terms of the boundary layer thickness. The shroud heat transfer is shown to be governed by the local centrifugal acceleration and by a core temperature, which has a weak dependence on the value of the axial Reynolds number. Spectral analyses of time signals obtained at selected locations indicate that, even though the disk boundary layers behave as unsteady laminar Ekman layers, the flow inside the cavity is turbulent and highly intermittent. In comparison with a sealed cavity, cases with an axial throughflow are characterised by a broader range of frequencies, which arise from the interaction between the laminar jet and the buoyant flow inside the cavity.
This paper presents buoyancy-induced flow for a sealed rotating cavity with rotational Rayleigh number Ra in the range 10⁷ to 10⁹. DNS for an incompressible model with the Boussinesq approximation is compared with LES for a compressible gas flow model. The compressible solver's solutions show the shroud Nusselt number scales with Ra0.286, in close agreement with the corrected experimental correlation and the Ra2/7 scaling for gravitational heat convection between horizontal plates, but differs from the N u ∝ Ra1/3 scaling given by the incompressible solver. The shroud thermal boundary layer thickness, based on the root mean square of the temperature fluctuation, can be estimated with λ* = 0:5N u-1 Velocities scale approximately with Ωa√β∆T. Disc laminar Ekman layer behaviour is confirmed up to Ra = 109. An Ekman layer scrubbing effect, associated with the viscous energy dissipation, is considered to be mainly responsible for the difference in N u between the two solvers at Ra = 109, in spite of rather small Eckert number. The analysis of the turbulent kinetic energy budget shows a dominant constant buoyancy production in the core. The use of the incompressible formulation for the considered problem is restricted by the applicable range of the Boussinesq approximation characterised by the buoyancy parameter β∆T and neglect of viscous heating and compressibility effects characterised by the Eckert number Ec = Ω2r2m =(Cp∆T).
This paper presents wall-modeled large-eddy simulations (WMLES) simulations of a chute type turbine rim seal. Configurations with an axisymmetric annulus flow and with nozzle guide vanes fitted (but without rotor blades) are considered. The passive scalar concentration solution and WMLES are validated against available data in the literature for uniform convection and a rotor-stator cavity flow. The WMLES approach is shown to be effective, giving significant improvements over an eddy viscosity turbulence model, in prediction of rim seal effectiveness compared to research rig measurements. WMLES requires considerably less computational time than wall-resolved LES, and has the potential for extension to engine conditions. All WMLES solutions show rotating inertial waves in the chute seal. Good agreement between WMLES and measurements for sealing effectiveness in the configuration without vanes is found. For cases with vanes fitted the WMLES simulation shows less ingestion than the measurements, and possible reasons are discussed.
Rotating fluids are well-known to be susceptible to waves. This has received much attention from the geophysics, oceanographic and atmospheric research communities. Inertial waves, which are driven by restoring forces, for example the Coriolis force, have been detected in the research fields mentioned above. This paper investigates inertial waves in turbine rim seal flows in turbomachinery. These are associated with the large-scale unsteady ow structures having distinct frequencies, unrelated to the main annulus blading, identified in many experimental and numerical studies. These unsteady flow structures have been shown in some cases to reduce sealing effectiveness and are difficult to predict with conventional steady Reynolds-averaged Navier-Stokes (RANS) approaches. Improved understanding of the underlying ow mechanisms and how these could be controlled is needed to improve the efficiency and stability of gas turbines. This study presents large-eddy simulations for three rim seal configurations { chute, axial and radial rim seals { representative of those used in gas turbines. Evidence of inertial waves is shown in the axial and chute seals, with characteristic wave frequencies limited within the threshold for inertial waves given by classic linear theory (i.e. jf=frelj 2), and instantaneous flow fields showing helical characteristics. The radial seal, which limits the radial fluid motion with the seal geometry, restricts the Coriolis force and suppresses the inertial wave.
A new experimental facility for the investigation of rim sealing is described and measurements are presented for two representative radial clearance seals with a nominally axisymmetric external flow. One radial seal has an upward rotor lip and is upstream of the rotor while the other has an upward stator lip and is downstream of the rotor. Measurements include surface pressures, tangential velocities in the core region of the disc cavity flow, and traverses of gas concentration in the cavity showing the distribution of mainstream ingestion. Tests were conducted at rotational Reynolds numbers up to 3 × 106 with nominal seal clearance to radius ratios in the range 0.002 to 0.01. For the radial seals a differential pressure criterion is found to overestimate the minimum sealing flow. Tangential velocity measurements in the wheelspace are in excellent agreement with other workers measurements and with theoretical predictions.
This paper presents large-eddy and direct numerical simulations of buoyancy-driven convection in sealed and open rapidly rotating cavities for Rayleigh numbers in the range 107-109, and axial throughflow Reynolds numbers 2000 and 5600. Viscous heating due to the Ekman layer scrubbing effect, which has previously been found responsible for the difference in sealed cavity shroud Nusselt number predictions between a compressible N-S solver and an incompressible counterpart using the Boussinesq approximation, is discussed and scaled up to engine conditions. For the open cavity with an axial throughflow, laminar Ekman layer behaviour of the mean flow statistics is confirmed up to the highest condition in this paper. The Buoyancy number Bo is found useful to indicate the influence of an axial throughflow. For the conditions studied the mean velocities are subject to Ra, while the velocity fluctuations are affected by Bo. A correlation, Nu0 = 0:169(Ra0)0:318, obtained with both the sealed and open cavity shroud heat transfer solutions, agrees with that for free gravitational convection between horizontal plates within 16% for the range of Ra0 considered.
Large-Eddy Simulations (LES) were carried out for a turbine rim seal and the sensitivity of the results to changes in grid resolution and the size of the computational domain are investigated. Ingestion of hot annulus gas into the rotor-stator cavity is compared between LES results and against experiments and Unsteady Reynolds-Averaged Navier–Stokes (URANS) calculations. The LES calculations show greater ingestion than the URANS calculation and show better agreement with experiments. Increased grid resolution shows a small improvement in ingestion predictions whereas increasing the sector model size has little effect on the results. The contrast between the different CFD models is most stark in the inner cavity, where the URANS shows almost no ingestion. Particular attention is also paid to the presence of low frequency oscillations in the disc cavity. URANS calculations show such low frequency oscillations at different frequencies than the LES. The oscillations also take a very long time to develop in the LES. The results show that the difficult problem of estimating ingestion through rim seals could be overcome by using LES but that the computational requirements were still restrictive.
The prediction of the pre-swirl cooling air delivery and disc metal temperature are important for the cooling system performance and the rotor disc thermal stresses and life assessment. In this paper, standalone 3D steady and unsteady CFD, and coupled FE-CFD calculations are presented for prediction of these temperatures. CFD results are compared with previous measurements from a direct transfer pre-swirl test rig. The predicted cooling air temperatures agree well with the measurement, but the nozzle discharge coefficients are under predicted. Results from the coupled FE-CFD analyses are compared directly with thermocouple temperature measurements and with heat transfer coefficients on the rotor disc previously obtained from a rotor disc heat conduction solution. Considering the modelling limitations, the coupled approach predicted the solid metal temperatures well. Heat transfer coefficients on the rotor disc from CFD show some effect of the temperature variations on the heat transfer coefficients. Reasonable agreement is obtained with values deduced from the previous heat conduction solution. Copyright © 2012 by ASME.
A high-order numerical method is employed to investigate flow in a rotor/stator cavity without heat transfer and buoyant flow in a rotor/rotor cavity. The numerical tool used employs a spectral element discretisation in two dimensions and a Fourier expansion in the remaining direction, which is periodic and corresponds to the azimuthal coordinate in cylindrical coordinates. The spectral element approximation uses a Galerkin method to discretise the governing equations, similarly to a finite element method, but employs high-order polynomials within each element to obtain spectral accuracy. A second-order, semi-implicit, stiffly stable algorithm is used for the time discretisation, and no subgrid modelling is included in the governing equations. Numerical results obtained for the rotor/stator cavity compare favourably with experimental results for Reynolds numbers up to Re1 = 106 in terms of velocities and Reynolds stresses. For the buoyancy-driven flow, the energy equation is coupled to the momentum equations via the Boussinesq approximation, which has been implemented in the code considering two different formulations. Numerical predictions of the Nusselt number obtained using the traditional Boussinesq approximation are considerably higher than available experimental data. Much better agreement is obtained when the extended Boussinesq approximation is em-ployed. It is concluded that the numerical method employed has considerable potential for further investigations of rotating cavity flows.
This paper presents a systematic study of flow and heat transfer mechanisms in a compressor disc cavity with an axial throughflow under centrifugal buoyancy-driven convection, comparing with previously published experimental data. Wall-modelled large-eddy simulations are conducted for six operating conditions, covering a range of rotational Reynolds number (3.2 × 105 – 2.2 × 106), buoyancy parameter (0.11 – 0.26) and Rossby number (0.4 – 0.8). Numerical accuracy and computational efficiency of the simulations are considered. Wall heat transfer predictions are compared with measured data with a good level of agreement. A constant rothalpy core occurs at high Eckert number, appearing to reduce the driving buoyancy force. The flow in the cavity is turbulent with unsteady laminar Ekman layers observed on both discs except in the bore flow affected region on the downstream disc cob. The shroud heat transfer Nusselt number-Rayleigh number scaling agrees with that of natural convection under gravity for high Rayleigh numbers. Disc heat transfer is dominated by conduction across unsteady Ekman layers, except on the downstream disc cob. The disc bore heat transfer is close to a pipe flow forced convection correlation. The unsteady flow structure is investigated showing strong unsteadiness in the cavity that extends into the axial throughflow.
Experimental measurements from a new single stage turbine are presented. The turbine has 26 vanes and 59 rotating blades with a design point stage expansion ratio of 2.5 and vane exit Mach number of 0.96. A variable sealing flow is supplied to the disc cavity upstream of the rotor and then enters the annulus through a simple axial clearance seal situated on the hub between the stator and rotor. Measurements at the annulus hub wall just downstream of the vanes show the degree of circumferential pressure variation. Further pressure measurements in the disc cavity indicate the strength of the swirling flow in the cavity, and show the effects of mainstream gas ingestion at low sealing flows. Ingestion is further quantified through seeding of the sealing air with nitrous oxide or carbon dioxide and measurement of gas concentrations in the cavity. Interpretation of the measurements is aided by steady and unsteady computational fluid dynamics solutions, and comparison with an elementary model of ingestion.
Previous studies have indicated some differences between steady CFD predictions of flow in a rotor-stator disc cavity with rotating bolts compared to measurements. Recently time-dependent CFD simulations have revealed the unsteadiness present in the flow and have given improved agreement with measurements. In this paper unsteady Reynolds averaged Navier-Stokes (URANS) 3600 model CFD calculations of a rotor-stator cavity with rotor bolts were performed in order to better understand the flow and heat transfer within a disc cavity previously studied experimentally by other workers. It is shown that the rotating bolts generate unsteadiness due to wake shedding which creates time-dependent flow patterns within the cavity. At low throughflow conditions, the unsteady flow significantly increases the average disc temperature. A systematic parametric study is presented giving insight into the influence of number of bolts, mass flow rate, cavity gap ratio and the bolts-to-shroud gap ratio on the time depended flow within the cavity.
Measurements and analysis for a pre-swirl cooling air delivery system are reported here. The experimental rig used is representative of aero-engine conditions, having 18 pre-swirl nozzles, 72 receiver holes, capable of speeds up to 11 000 rpm, and giving differences between total temperature upstream of the pre-swirl nozzles and relative total temperature measured in the receiver holes of up to 26K. Pressure and temperature measurements are reported. An elementary model is developed for calculation of the cooling air delivery temperature. This accounts for the pre-swirl nozzle velocity coefficient, moments on the stationary and rotating surfaces in the pre-swirl chamber, and flows through the inner and outer seals to the chamber. The model is shown to correlate the measurements well for a range of disc speeds and pre-swirl velocity to disc speed ratios.
Design and optimization of an efficient internal air system of a gas turbine requires thorough understanding of the flow and heat transfer in rotating disc cavities. The present study is devoted to numerical modelling of flow and heat transfer in a cylindrical cavity with radial inflow and comparison with the available experimental data. The simulations are carried out with axi-symmetric and 3-D sector models for various inlet swirl and rotational Reynolds numbers upto 2.1×106. The pressure coefficients and Nusselt numbers are compared with the available experimental data and integral method solutions. Two popular eddy viscosity models, the Spalart-Allmaras and the k-e , and a Reynolds stress model have been used . For cases with particularly strong vortex behaviour the eddy viscosity models show some shortcomings with the Spalart-Allmaras model giving slightly better results than the k-e model. Use of the Reynolds stress model improved the agreement with measurements for such cases. The integral method results are also found to agree well with the measurements. Copyright © 2012 by ASME.
While turbine rim sealing flows are an important aspect of turbomachinery design, affecting turbine aerodynamic performance and turbine disc temperatures, the present understanding and predictive capability for such flows is limited. The aim of the present study is to clarify the flow physics involved in rim sealing flows and to provide high quality experimental data for use in evaluation of CFD models. The seal considered is similar to a chute seal previously investigated by other workers, and the study focuses on the inherent unsteadiness of rim seal flows, rather than unsteadiness imposed by the rotating blades. Unsteady pressure measurements from radially and circumferentially distributed transducers are presented for flow in a rotor-stator disc cavity and the rim seal without imposed external flow. The test matrix covered ranges in rotational Reynolds number, Re∅, and non-dimensional flow rate, , of 2.2 –3.0x106 and 0 – 3.5x103 respectively. Distinct frequencies are identified in the cavity flow and detailed analysis of the pressure data associates these with large scale flow structures rotating about the axis. This confirms the occurrence of such structures as predicted in previously published CFD studies and provides new data for detailed assessment of CFD models.
Swimming pools provide an excellent facility for exercise and leisure but are also prone to contamination from microbial pathogens. The study modelled a 50-m x 20-m swimming pool using both a small scale physical model and computational fluid dynamics to investigate how water and pathogens move around a pool in order to identify potential risk spots. Our study revealed a number of lessons for pool operators, designers and policy makers: disinfection reaches the majority of a full scale pool in approximately 16 minutes operating at the maximum permissible inlet velocity of 0.5m/s. This suggests that where a pool is designed to have 15 paired inlets it is capable of distributing disinfectant throughout the water body within an acceptable time frame. However, the study also showed that the exchange rate of water is not uniform across the pool tank and that there is potential for areas of the pool tank to retain contaminated water for significant periods of time. ‘Dead spots’ exist at either end of the pool where pathogens could remain. This is particularly significant if there is a faecal release into the pool by bathers infected with Cryptosporidium parvum, increasing the potential for waterborne disease transmission.
Better understanding and more accurate prediction of heat transfer and cooling flows in aero engine components in steady and transient operating regimes are essential to modern engine designs aiming at reduced cooling air consumption and improved engine efficiencies. This paper presents a simplified coupled transient analysis methodology that allows assessment of the aerothermal and thermomechanical responses of engine components together with cooling air mass flow, pressure and temperature distributions in an automatic fully integrated way. This is achieved by assembling a fluid network with contribution of components of different geometrical dimensions coupled to each other through dimensionally heterogeneous interfaces. More accurate local flow conditions, heat transfer and structural displacement are resolved on a smaller area of interest with multidimensional surface coupled computational fluid dynamics (CFD)/FE codes. Contributions of the whole engine air-system are predicted with a faster monodimensional flow network code. Matching conditions at the common interfaces are enforced at each time-step exactly by employing an efficient iterative scheme. The coupled simulation is performed on an industrial high pressure turbine (HPT) disk component run through a square cycle. Predictions are compared against the available experimental data. The paper proves the reliability and performance of the multidimensional coupling technique in a realistic industrial setting. The results underline the importance of including more physical details into transient thermal modeling of turbine engine components.
This paper considers the coupling of a finite element thermal conduction solver with a steady, finite volume fluid flow solver. Two methods were considered for passing boundary conditions between the two codes - transfer of metal temperatures and either convective heat fluxes or heat transfer coefficients and air temperatures. These methods have been tested on two simple rotating cavity test cases and also on a more complex real engine example. Convergence rates of the two coupling methods were compared. Passing heat transfer coefficients and air temperatures was found to give the quickest convergence. The coupled method gave agreement with the analytic solution and a conjugate solution of the simple free disc problem. The predicted heat transfer results for the real engine example showed some encouraging agreement, although some modelling issues are identified. Copyright © 2001 by ASME.
An investigation of hot gas ingestion driven by the disc pumping effect in a chute seal was conducted at the Oxford Rotor Facility. Measurements of mean pressure, unsteady pressure and gas concentration have been logged and analysed under different operating conditions. The sensitivity of mean cavity pressure coefficient, frequency spectra of the unsteady pressures and sealing effectiveness to changing conditions of purge flow, annulus flow, rotor disc speed and seal clearance has been studied. The steady pressures revealed the development of two vortices in the cavity, induced by the sharp change in geometry of the stator wall. The increased shear at the interface between these two vortices strengthened the unsteady activity at this location. The addition of mainstream flow improved the sealing capability of the chute seal under certain operating conditions. The excitation of further frequencies when an axisymmetric annulus flow was introduced suggested a complex interaction between annulus and purge flows. INTRODUCTION Decades of research in the topic of hot gas ingestion pointed towards disc pumping, circumferential annulus pressure asymmetries and, more recently, unstable rim seal flows as the main drivers for hot gas ingestion. These three mechanisms are depicted in Figure 1. Ingress of high temperature flow from the main gas path is undesired. Rotor discs are not thermally insulated and ingestion of hot gas from the mainstream can significantly reduce the operating life and damage the mechanical integrity of these highly stressed components. To prevent this from occurring, cool air is injected between the stator and rotor discs to purge and pressurise the cavity, however, this comes at the detriment of engine efficiency. The intrinsically convoluted flow field in the turbine rim region creates a complex environment in which fundamental understanding of the basic flow physics becomes paramount to comprehend the synergetic effect of each of the mechanisms mentioned above. This investigation focuses on the performance of a chute rim seal with no blades and vanes in the annulus, such that ingestion is expected to be driven by the effects of rotation. Bru Revert et al. (2021) showed that this scenario is relevant for high pressure turbines at low flow coefficients.
This paper reports large-eddy simulations (LES) and unsteady Reynolds-averaged Navier-Stokes (URANS) calculations of a turbine rim seal configuration previously investigated experimentally. The configuration does not include any vanes, blades or external flows, but investigates inherent unsteady flow features and limitations of CFD modelling identified in engine representative studies. Compared to RANS and URANS CFD models, a sector LES model showed closer agreement with mean pressure measurements. LES models also showed agreement with measured pressure frequency spectra, but discrepancies were found between the LES and experiment in the speed and the circumferential lobe number of the unsteady flow structures. Sensitivity of predictions to modelling assumptions and differences with experimental data are investigated through CFD calculations considering sector size, interaction between the rim cavity and the inner cavity, outer annulus boundary conditions, and the coolant mass flow. Significant sensitivity to external flow conditions, which could contribute to differences with measurements, is shown, although some discrepancies remain. Further detailed analysis of the CFD solutions is given illustrating the complex flow physics. Possible improvement of a steady RANS model using a priori analysis of LES was investigated, but showed a rather small improvement in mean pressure prediction.
Heat transfer between contacting surfaces is a key factor in the thermal behaviour of engineering components in turbomachinery and various other areas of technology. Thermal contact conductance (TCC) is a parameter that quantifies this heat flow. An ongoing challenge in measuring and modelling TCC is the different length scales of surface topography exhibited on real components. Manufacturing techniques such as turning and fly cutting introduce repeatable surface deviations of medium wavelength which are the focus of this study. An instrumented split tube with in-line washers, loaded under carefully controlled conditions, was used to measure the TCC of washers made of PE16. Fly cutting was used in this study to introduce a repeatable lay typifying a range of manufacturing techniques. Experimental determination of TCC for (i) flat contacting washers and (ii) contact between flat washers and fly cut washers with repeatable lay is reported. As expected the latter case gives rise to significantly lower TCC than the former. A 2D finite element model is described which models the elastic-plastic deformation of a representative machining induced contact line. Using the TCC data for flat contacting surfaces, FEA is used to calculate the reduced TCC for the machined case. Predicted values of TCC assuming plane stress and plane strain are compared with experimental data.
Unsteady flow phenomena unrelated to the main gas-path blading have been identified in a number of turbine rim seal investigations. This unsteadiness has significant influence on the sealing effectiveness predicted by the conventional steady RANS (Reynolds-averaged Navier–Stokes) method, thus it is important for turbine stage design and optimisation. This paper presents CFD (computational fluid dynamics) modelling of a chute type rim seal that has been previously experimentally investigated. The study focuses on inherent large-scale unsteadiness rather than that imposed by vanes and blades or external flow. A large-eddy simulation (LES) solver is validated for a pipe flow test case and then applied to the chute rim seal rotor/stator cavity. LES, RANS and unsteady RANS (URANS) models all showed reasonable agreement with steady measurements within the disc cavity, but only the LES shows unsteadiness at a similar distinct peak frequency to that found in the experiment, at 23 times the rotational frequency. The boundary layer profile within the chute rim seal clearance has been scrutinised, which may explain the improvement of LES over RANS predictions for the pressure drop across the seal. LES results show a clockwise mean flow vortex. A more detailed sketch of the rim sealing flow unsteady flow structures is established with the help of the LES results. However, there are some significant differences between unsteadiness predicted and the measurements, and possible causes of these are discussed.
This paper presents a review of research on turbine rim sealing with emphasis placed on the underlying flow physics and modelling capability. Rim seal flows play a crucial role in controlling engine disc temperatures but represent a loss from the main engine power cycle and are associated with spoiling losses in the turbine. Elementary models that rely on empirical validation and are currently used in design do not account for some of the known flow mechanisms, and prediction of sealing performance with computational fluid dynamics (CFD) has proved challenging. CFD and experimental studies have indicated important unsteady flow effects that explain some of the differences identified in comparing predicted and measure sealing effectiveness. This review reveals some consistency of investigations across a range of configurations, with inertial waves in the rotating flow apparently interacting with other flow mechanisms which include vane, blade and seal flow interactions, disc pumping and cavity flows, shear layer and other instabilities, and turbulent mixing.
The cooling air in a rotating machine is subject to windage as it passes over the rotor surface, particularly for cases where non-axisymmetric features such as boltheads are encountered. The ability to accurately predict windage can help reduce the quantity of cooling air required, resulting in increased efficiency. Previous work has shown that steady CFD solutions can give reasonable predictions for the effects of bolts on disc moment for a rotor-stator cavity with throughflow but flow velocities and disc temperature are not well predicted. Large fluctuations in velocities have been observed experimentally in some cases. Time-dependent CFD simulations reported here bring to light the unsteady nature of the flow. Unsteady Reynolds averaged Navier-Stokes (URANS) calculations for 1200 and 3600 models of the rotor-stator cavity with 9 and 18 bolts were performed in order to better understand the flow physics. Although the rotor-stator cavity with bolts is geometrically steady in the rotating frame of reference, it was found that the bolts generate unsteadiness which creates time-dependent rotating flow features within the cavity. At low throughflow conditions, the unsteady flow significantly increases the average disc temperature.
Unsteady flow dynamics in turbine rim seals are known to be complex and attempts accurately to predict the interaction of the mainstream flow with the secondary air system cooling flows using computational fluid dynamics (CFD) with Reynolds-averaged Navier–Stokes (RANS) turbulence models have proved difficult. In particular, published results from RANS models have over-predicted the sealing effectiveness of the rim seal, although their use in this context continues to be common. Previous studies have ascribed this discrepancy to the failure to model flow structures with a scale greater than the one which can be captured in the small-sector models typically used. This article presents results from a series of Large-Eddy Simulations (LES) of a turbine stage including a rim seal and rim cavity for, it is believed by the authors, the first time. The simulations were run at a rotational Reynolds number Re ¼ 2.2 106 and a main annulus axial Reynolds number Rex ¼ 1.3 106 and with varying levels of coolant mass flow. Comparison is made with previously published experimental data and with unsteady RANS simulations. The LES models are shown to be in closer agreement with the experimental sealing effectiveness than the unsteady RANS simulations. The result indicates that the previous failure to predict rim seal effectiveness was due to turbulence model limitations in the turbine rim seal flow. Consideration is given to the flow structure in this region. K
The built-in volume ratio of variable wall thickness scroll expanders can be increased without increasing the number of scroll turns and the expander size in contrast to constant wall thickness expanders. CFD models for these novel scroll-type designs are presented in this research paper. The validation, verification and the findings have proven consistency with the theory of small scale ORC scroll expanders. The performance analysis indicates that the optimum performance point was reached at a pressure ratio of 3.5. The decrease of radial clearance from 200μm to 75μm had a significant effect on the isentropic efficiency and the specific power output, with the isentropic efficiency significantly increasing from 31.9% up to 53.9%. Based on the second-law analysis, it is found that exergy of 336.5W (75μm) and 864.2W (200μm) were destroyed during the expansion processes. Furthermore, characteristic pressure imbalances were observed in the expansion chambers. The studies also reveal that the large-scale vortices, generated during the suction process, were completely dissipated in the expansion chambers at a crank angle of 600°. Analysis of the pressure-volume diagram shows that variable wall thickness scroll expanders with built-in volume ratios above 4.5 could fully expand the working fluid to the defined outlet pressure.
A chute rim seal cavity has been instrumented with time resolved and time-averaged pressure transducers as well as a gas concentration measurement system at the Oxford Rotor Facility. The unsteady pressure transducers were unevenly distributed along the circumference generating 15 combinations of angular spacing to conduct a phase analysis. The test operating conditions were modified through different configurations of mainstream flow, a range of rotational speeds and purge flows to obtain test data in the regimes of rotationally-driven, pressure-driven and combined ingestion. The rotating unsteady flow structures within the rim seal cavity were studied through a combination of phase analysis of dynamic pressure signals and inspection of the frequency domain. The introduction of mainstream flow (axial and swirled) increased the overall unsteadiness exciting an additional band of lower frequencies. The phase analysis revealed these were associated with acoustic waves, providing the first experimental evidence of 1 Corresponding author for paper number GTP-22-1603: anna.brurevert@rolls-royce.com ASME Journal of Gas Turbines and Power GTP-22-1603 Bru Revert Copyright © 2022 by Rolls-Royce plc 2 the presence and coexistence of inertial and acoustic waves in the rim seal cavity. The interaction of the inertial and acoustic waves strongly depends on the operating conditions, and may be linked to changes in sealing effectiveness.
Copyright © 1989 by ASME.A combined theoretical and experimental study is described in which de-swirl nozzles were used to reduce the radial pressure drop in a rotating cavity with a radial inflow of air. The nozzles, which were attached to the outer part of the cavity, were angled such that the angular speed of the air at inlet could be in the opposite direction to that of the cavity. Solutions of the momentum-integral equations were used to predict the resulting radial distributions of pressure throughout the cavity. Flow visualization was used to confirm the flow structure, and transducers attached to one of the rotating discs in the cavity were used to measure the radial pressure distributions. Results are presented for 'swirl fractions' (that is, the ratio of the angular speed of the air leaving the nozzles to that of the cavity) in the range -0.4 to + 0.9, and for 0.01 < | Cw | Reφ-0-8 < 0.5, where Cw and Reφ are the nondimensional flow rate and rotational Reynolds number, respectively. The measured pressures are in good agreement with the predicted values, and the pressure drop across the cavity can be significantly less than that associated with solid-body rotation. The flow rate produced by the pressure drop across the cavity is not unique: there are up to three possible values of flow rate for any given value of pressure drop.
Scroll expanders are currently attracting interest for integration in small scale organic Rankine cycle (ORC) waste heat recovery applications and have been subject to significant research over the last two decades. The most common geometrical design uses a scroll profile generated by the involute of a circle with a constant wall thickness. A major disadvantage of this approach is that the increase of the geometric expansion ratio is constrained, since it is accompanied with a large increase in the scroll profile length and is associated with a decreased efficiency. In this paper, the published literature related to scroll expander geometry is reviewed. Investigations regarding the influence of varying scroll geometrical parameters on the performance of scroll expanders with a constant wall thickness are first examined. The use of variable wall thicknesses and their effects on the performance are then considered. Finally, the impact of scroll expander geometries using unconventional scroll profiles and scroll tip shape variations on the performance is discussed and summarised. The major conclusion to be drawn from this review is that scroll expanders with variable wall thickness scrolls should be further designed and developed. It is possible to increase the geometric expansion ratio without increasing the length of the scroll profiles. CFD simulations are a promising tool to illustrate and understand the non-uniform and asymmetric inner flow and temperature fields. The related benefits could lead to scroll devices with variable wall thickness not only improving the performance of organic Rankine cycle (ORC) systems but also opening a broad new field of applications such as refrigeration cycles and other power cycles where a high pressure ratio is preferred.
A combined theoretical and experimental study is described in which de-swirl nozzles were used to reduce the radial pressure drop in a rotating cavity with a radial inflow of air. The nozzles, which were attached to the outer part of the cavity, were angled such that the angular speed of the air at inlet could be in the opposite direction to that of the cavity. Solutions of the momentum-integral equations were used to predict the resulting radial distributions of pressure throughout the cavity. Flow visualization was used to confirm the flow structure, and transducers attached to one of the rotating disks in the cavity were used to measure the radial pressure distributions. The measured pressures are in good agreement with the predicted values, and the pressure drop across the cavity can be significantly less than that associated with solid-body rotation.
Understanding and modelling of main annulus gas ingestion through turbine rim seals is considered and advanced in this paper. Unsteady 3-dimensional computational fluid dynamics (CFD) calculations and results from a more elementary model are presented and compared with experimental data previously published by Hills et al (1997). The most complete CFD model presented includes both stator and rotor in the main annulus and the inter-disc cavity. The k-ε model of turbulence with standard wall function approximations is assumed in the model which was constructed in a commercial CFD code employing a pressure correction solution algorithm. It is shown that considerable care is needed to ensure convergence of the CFD model to a periodic solution. Compared to previous models, results from the CFD model show encouraging agreement with pressure and gas concentration measurements. The annulus gas ingestion is shown to result from a combination of the stationary and rotating circumferential pressure asymmetries in the annulus. Inertial effects associated with the circumferential velocity component of the flow have an important effect on the degree of ingestion. The elementary model used is an extension of earlier models based on orifice theory applied locally around the rim seal circumference. The new model includes a term accounting for inertial effects. Some good qualitative and fair quantitative agreement with data is shown. Copyright © 2001 by ASME.
Computational fluid dynamics solutions are presented for unsteady flow and heat transfer in model fluid couplings. Factors studied include the effects of coupling size, cooling throughflow, vane numbers, and angled vanes. Predictions of torque characteristics are consistent with previously published experimental data and an elementary analysis. In this initial study, only single-phase solutions are presented, although these results do confirm that cavitation and/or air entrapment can be significant in practice. Angling of the vanes at 20 degrees to the axial direction is found to give a large increase in torque at low slip running conditions. However, pressure variations within the coupling are also increased and so the angled vane geometry will be more susceptible to cavitation.
The paper describes a Large Eddy Simulation (LES) conducted for a non adiabatic rotating cavity with a radial inflow introduced from the shroud. The dimensionless mass flow rate of the radial inflow is Cw = 3500 and the rotational Reynolds number, based on the cavity outer radius, is equal to Reθ = 1.2 x 10⁶. The time averaged local Nusselt number on the heated wall is compared with the experimental data available from the literature, and with those derived from the solution of two Unsteady Reynolds Averaged Navier-Stokes (URANS) eddy viscosity models, namely the Spalart-Allmaras and the k - ω SST model. It is shown that the Nusselt number is under-predicted in the lower part of the disc and over-predicted in the outer region by both URANS models, whereas the LES provides a much better agreement with the measurements. The behaviour results primarily from a different flow structure in the source region, which, in the LES, is found to be considerably more extended and show localized buoyancy phenomena that the URANS models investigated do not capture.
While it is known that the occurrence of flutter is dominated by aerodynamics, it also depends on such parameters as inlet distortion and acoustics, aerodynamic and mechanical mistuning, and structural damping. It is shown in this paper that recent developments in predictive methods are showing considerable promise and leading to an improved understanding of the controlling parameters. A non-linear coupled structural-fluid approach is described and applied at engine representative conditions. This involves 3D unsteady CFD calculations of the fan and intake flows. Particular emphasis is placed on the influence of intake acoustics. Earlier work on flutter prediction has focused on either the fan assembly without a proper representation of the intake, or the calculation of the acoustic properties of the intake without properly representing the interaction with the fan. The present study includes a combined fan plus intake calculation, the latter being represented via an axisymmetric approximation. With an initial prescribed velocity disturbance of the blades in a 2 nodal diameter mode, the calculations showed a strong response in a 4 nodal diameter mode. Considerable acoustic activity within the duct was also noted. This result was compared with CFD calculations for the full 3D intake geometry. It was concluded that a realistic representation of intake acoustics is required for a full description of the problem.
Large-eddy simulations (LES) of centrifugal convection in a closed rotating cavity with different thermal boundary conditions are presented for Rayleigh numbers (Ra) 107∼109. Previous results for radial convection with a positive radial temperature gradient and for axial convection with low Ra are confirmed. For axial convection, turbulence develops in the core flow at Ra=109, but is considerably weaker than the turbulence for the radial and mixed convection. In mixed convection, the mean core temperature shows little radial variation as in radial convection, but has a significant axial temperature gradient as in axial convection. Compared to the radial and axial convection cases, both shroud and disc heat transfer are increased in mixed convection. Changes in disc heat transfer from the axial convection case are particularly strong. In all the conditions, laminar kinematic Ekman layers occur on the discs, but the disc thermal boundary layers for axial and mixed convection are considerably thicker. •Open-source CFD code is applied to the pure centrifugal buoyant driven flow in a rotating disc cavity, with results comparing well to the published data. The calculations are then extended to axial convection and mixed convection with Rayleigh numbers up to 109.•Under axial convection and mixed convection, temperature gradient and mean flow circulation along the axial direction are developed. In the mixed convection, turbulence level in the cavity and heat transfer on the shroud are both increased.
An efficient finite element analysis/computational fluid dynamics (FEA/CFD) thermal coupling technique has been developed and demonstrated. The thermal coupling is achieved by an iterative procedure between FEA and CFD calculations. Communication between FEA and CFD calculations ensures continuity of temperature and heat flux. In the procedure, the FEA simulation is treated as unsteady for a given transient cycle. To speed up the thermal coupling, steady CFD calculations are employed, considering that fluid flow time scales are much shorter than those for the solid heat conduction and therefore the influence of unsteadiness in fluid regions is negligible. To facilitate the thermal coupling, the procedure is designed to allow a set of CFD models to be defined at key time points/intervals in the transient cycle and to be invoked during the coupling process at specified time points. To further enhance computational efficiency, a “frozen flow” or “energy equation only” coupling option was also developed, where only the energy equation is solved, while the flow is frozen in CFD simulation during the thermal coupling process for specified time intervals. This option has proven very useful in practice, as the flow is found to be unaffected by the thermal boundary conditions over certain time intervals. The FEA solver employed is an in-house code, and the coupling has been implemented for two different CFD solvers: a commercial code and an in-house code. Test cases include an industrial low pressure (LP) turbine and a high pressure (HP) compressor, with CFD modeling of the LP turbine disk cavity and the HP compressor drive cone cavity flows, respectively. Good agreement of wall temperatures with the industrial rig test data was observed. It is shown that the coupled solutions can be obtained in sufficiently short turn-around times (typically within a week) for use in design.
A combined theoretical and experimental study is decribed in which de-swirl nozzles were attached to the outer part of a rotating cavity and angled so that the angular speed of the air at inlet could be in the opposite direction to that of the cavity. Solutions of the momentum-integral equations are used to predict the resulting radial distributions of pressure throughout the cavity. Flow visualization is used to confirm the flow structure, and transducers attached to one of the rotating discs are used to measure the radial pressure distributions. Theoretical values are compared with measurements made inside a rig in which de-swirl nozzles were used to reduce the swirl fraction of the incoming air. It is concluded that there is good agreement between the theoretical and experimental values of pressure distribution. (R.E.P.)
The Internal Cooling Air Systems for Gas Turbines (ICAS-GT) research programme, sponsored by the European Commission, ran from January 1998 to December 2000, and was undertaken by a consortium of ten gas turbine manufacturing companies and four universities. Research was concentrated in five discrete but related areas of the air system including turbine rim seals, rotating cavity flow and heat transfer, and turbine pre-swirl system effectiveness. In each case, experiments were conducted to extend the database of pressure, temperature, flow and heat transfer measurements to engine representative non-dimensional conditions. The data was used to develop correlations, and to validate CFD and FE calculation methods, for internal fluid flow and heat transfer. This paper summarises the outcome of the project by presenting a sample of experimental results from each technical work package. Examples of the associated CFD calculations are included to illustrate the progress made in developing validated tools for predicting rotating cavity flow and heat transfer over an engine representative range of flow conditions.
This paper presents large-eddy and direct numerical simulations of buoyancy-driven convection in sealed and open rapidly rotating cavities for Rayleigh numbers in the range 107–109, and axial throughflow Reynolds numbers 2000 and 5600. Viscous heating due to the Ekman layer scrubbing effect, which has previously been found responsible for the difference in sealed cavity shroud Nusselt number predictions between a compressible N-S solver and an incompressible counterpart using the Boussinesq approximation, is discussed and scaled up to engine conditions. For the open cavity with an axial throughflow, laminar Ekman layer behaviour of the mean flow statistics is confirmed up to the highest condition in this paper. The Buoyancy number Bo is found useful to indicate the influence of an axial throughflow. For the conditions studied the mean velocities are subject to Ra, while the velocity fluctuations are affected by Bo. A correlation, Nu' = 0.169(Ra')0.318, obtained with both the sealed and open cavity shroud heat transfer solutions, agrees with that for free gravitational convection between horizontal plates within 16% for the range of Ra' considered.
This study investigates turbine rim seal geometry effects within the rotationally-driven ingestion regime. Computations were performed with a wall-resolved unsteady Reynolds-averaged Navier-Stokes (URANS) model and a large-eddy simulation (LES) model including near-wall boundary layer modelling, that is wall-modelled LES (WMLES). Use of simplified rim sealing models is proposed as an efficient method of ranking seal designs and investigating sensitivity to seal geometry. Four rim seal configurations, two chute seals, an axial seal and a radial seal which are representative of those used in gas turbines and in previous research were investigated. Furthermore, hybrid seals combining geometric characteristics from both the chute and radial seal were considered. Significant sensitivities of sealing performance to turbulence modelling are identified, but URANS and WMLES show similar trends in ranking of seal performance, and these are consistent with previous experimental work. The addition of an outer radial clearance section to a chute seal is effective in reducing ingestion levels.
Better understanding and more accurate prediction of heat transfer and cooling flows in aero engine components in steady and transient operating regimes are essential to modern engine designs aiming at reduced cooling air consumption and improved engine efficiencies. This paper presents a simplified coupled transient analysis methodology that allows assessment of the aerothermal and thermomechanical responses of engine components together with cooling air mass flow, pressure and temperature distributions in an automatic fully integrated way. This is achieved by assembling a fluid network with contribution of components of different geometrical dimensions coupled to each other through dimensionally heterogeneous interfaces. More accurate local flow conditions, heat transfer and structural displacement are resolved on a smaller area of interest with multidimensional surface coupled CFD/FE codes. Contributions of the whole engine air-system are predicted with a faster mono dimensional flow network code. Matching conditions at the common interfaces are enforced at each time step exactly by employing an efficient iterative scheme. The coupled simulation is performed on an industrial high pressure turbine disk component run through a square cycle. Predictions are compared against the available experimental data. The paper proves the reliability and performance of the multidimensional coupling technique in a realistic industrial setting. The results underline the importance of including more physical details into transient thermal modelling of turbine engine components.
Flows induced by centrifugal buoyancy occur in rotating systems in which the centrifugal force is large when compared to other body forces and are of interest for geophysicists and also in engineering problems involving rapid rotation and unstable temperature gradients. In this numerical study we analyse the onset of centrifugal buoyancy in a rotating cylindrical cavity bounded by two plane, insulated disks, adopting a geometrical configuration relevant to fundamental studies of buoyancy-induced flows occurring in gas turbine’s internal air systems. Using linear stability analysis, we obtain critical values of the centrifugal Rayleigh number and corresponding critical azimuthal wavenumbers for the onset of convection for different radius ratios. Using direct numerical simulation, we integrate the solutions starting from a motionless state to which small sinusoidal perturbations are added, and show that nonlinear triadic interactions occur before energy saturation takes place. At the lowest Rayleigh number considered, the final state is a limit-cycle oscillation affected by the presence of the disks, having a spectrum dominated by a certain mode and its harmonics. We show that, for this case, the limit-cycle oscillations only develop when no-slip end walls are present. For the largest considered chaotic motion occurs, but the critical wavenumber obtained from the linear analysis eventually becomes the most energetic even in the turbulent regime.
In compressor inter-disc cavities with a central axial throughflow it is known that the flow and heat transfer is strongly affected by buoyancy in the centrifugal force field. As a step towards developing CFD methods for such flows, buoyancy-driven flows under gravity in a closed cube and under centrifugal force in a sealed rotating annulus have been studied. Numerical simulations are compared with the experimental results of Kirkpatrick and Bohn (1986) and Bohn et al (1993). Two different CFD codes have been used and are shown to agree for the stationary cube problem. Unsteady simulations for the stationary cube show good agreement with measurements of heat transfer, temperature fluctuations, and velocity fluctuations for Rayleigh numbers up to 2 × 10 . Similar simulations for the rotating annulus also show good agreement with measured heat transfer rates. The CFD results confirm Bohn et al's results, showing reduced heat transfer and a different Rayleigh number dependency compared to gravity-driven flow. Large scale flow structures are found to occur, at all Rayleigh numbers considered.
This paper presents wall-modeled large-eddy simulations (WMLES) of a chute-type turbine rim seal. Configurations with an axisymmetric annulus flow and with nozzle guide vanes fitted (but without rotor blades) are considered. The passive scalar concentration solution and WMLES are validated against available data in the literature for uniform convection and a rotor-stator cavity flow. The WMLES approach is shown to be effective, giving significant improvements over an eddy viscosity turbulence model, in prediction of rim seal effectiveness compared to research rig measurements. WMLES requires considerably less computational tune than wall-resolved LES, and has the potential for extension to engine conditions. All WMLES solutions show rotating inertial waves in the chute seal. Good agreement between WMLES and measurements for sealing effectiveness in the configuration without vanes is found. For cases with vanes fitted, the WMLES simulation shows less ingestion than the measurements, and possible reasons are discussed.
Numerical solutions of the Reynolds-averaged Navier-Stokes equations have been used to model the influence of cobs and a bolt cover on the flow and heat transfer in a rotating cavity with an imposed radial outflow of air. Axisymmetric turbulent flow is assumed using a mixing length turbulence model. Calculations for the non-plane discs are compared with plane disc calculations and also with the available experimental data. The calculated flow structures show good agreement with the experimentally observed trends. For the cobbed and plane discs, Nusselt numbers are calculated for a combination of flow rates and rotational speeds; these show some discrepancies with the experiments, although the calculations exhibit the more consistent trend.
This paper presents transient aero-thermal analysis for a gas turbine disk and the surrounding air flows through a transient slam acceleration/deceleration “square cycle” engine test, and compares predictions with engine measurements. The transient solid-fluid interaction calculations were performed with an innovative coupled finite element (FE) and computational fluid dynamics (CFD) approach. The computer model includes an aero-engine high pressure turbine (HPT) disk, adjacent structure, and the surrounding internal air system cavities. The model was validated through comparison with the engine temperature measurements and is also compared with industry standard standalone FE modelling. Numerical calculations using a 2D FE model with axisymmetric and 3D CFD solutions are presented and compared. Strong coupling between CFD solutions for different air system cavities and the FE solid model led to some numerical difficulties. These were addressed through improvement to the coupling algorithm. Overall performance of the coupled approach is very encouraging giving temperature predictions as good as a traditional model that had been calibrated against engine measurements.
This paper presents the transient aero-thermal analysis of a gas turbine internal air system through an engine flight cycle featuring multiple fluid cavities that surround a HP turbine disk and the adjacent structures. Strongly coupled fluid-structure thermal interaction problems require significant computational effort to resolve nonlinearities on the interface for each time step. Simulation times may grow impractical if multiple fluid domains are included in the analysis. A new strategy is employed to decrease the cost of coupled aero-thermal analysis. Significantly lower fluid domain solver invocation counts are demonstrated as opposed to the traditional coupling approach formulated on the estimates of heat transfer coefficient. Numerical results are presented using 2D FE conduction model combined with 2D flow calculation in five separate cavities interconnected through the inlet and outlet boundaries. The coupled solutions are discussed and validated against a nominal stand-alone model. Relative performance of both coupling techniques is evaluated.
This experimental study considered the performance of a chute rim seal downstream of turbine inlet guide vanes (but without rotor blades). The experimental set up reproduced rotationally-driven ingestion without vanes and conditions of pressure-driven ingestion with vanes. The maximum rotor speed was 9000 rpm corresponding to a rotational Reynolds number of 3.3x106 with a flow coefficient of 0.45. Measurements of mean pressures in the annulus and the disc rim cavity as well as values of sealing effectiveness deduced from gas concentration data are presented. At high values of flow coefficient (low rotational speeds), the circumferential pressure variation generated by the vanes drove relatively high levels of ingestion into the disc rim cavity. For a given purge flow rate, increasing the disc rotational speed led to a reduction in ingestion, shown by higher values of sealing effectiveness, despite the presence of upstream vanes. At Uax/(Ωb) = 0.45, the sealing effectiveness approached that associated with purely rotationally-driven ingestion. A map of sealing effectiveness against non-dimensional purge flow summarises the results and illustrates the combined rotational and pressure-driven effects on the ingestion mechanism. The results imply that flow coefficient is an important parameter in rim sealing and that rotational effects are important in many applications, especially turbines with low flow coefficient.
Design of pre-swirl systems is important for the secondary air cooling system of gas turbine engines. In this paper, three pre-swirl nozzles, a cascade vane and two drilled nozzles are analysed and their performances are compared. The two drilled nozzles considered are a straight drilled nozzle and an aerodynamically designed nozzle. CFD analyses are presented for stand-alone and pre-swirl system 3D sector models at engine operating conditions near to engine maximum power condition rotational Reynolds number (Re ?) up to 4.6 ! 10 . Nozzle performance is characterised by the nozzle discharge coefficient (C ), nozzle velocity coefficient (?η) and cooling air delivery temperature. Two commonly used eddy viscosity models are employed for the study, the standard κ-ε and Spalart-Allmaras models with wall functions. Both models give very similar results for C and η and are in reasonable agreement with available experimental data. Effects of nozzle or vane number and sealing flow have been analysed. The cascade vanes perform slightly better than the aerodynamically designed drilled nozzles but the final design choice will depend on other component and manufacturing costs. An elementary model is presented to separate temperature losses due to the nozzle, stator drag and sealing flow. Copyright © 2011 by Rolls-Royce plc.
Although conventional Reynolds-averaged Navier-Stokes (RANS) models of turbulence are generally used for predicting the performance of gas turbine pre-swirl systems, these models are known to have shortcomings. Motivated by the need to predict mixing where cooled-cooling air (CCA) and un-cooled cooling air (UCA) streams are introduced in pre-swirl systems, computational fluid dynamics (CFD) modelling capability is reassessed. An initial study focuses on a normal jet in crossflow (JICF), illustrating some of the shortcomings of a popular Reynolds-averaged Navier-Stokes (RANS) model and the possible advantages and disadvantages of wall-modeled large eddy simulation (WMLES). Pre-swirl system studies focus on a previously investigated low radius feed, direct flow configuration for which measurements and CFD solutions are available, and extend this to consider a mixed feed system. The velocities in the near-jet region of the pre-swirl chamber were predicted differently by unsteady RANS (URANS) and WMLES, however no significant differences were observed closer to the receiver holes. Comparing to measurements shows little overall difference between the models, with similar results to earlier studies. Although no measurements are available for a mixed feed system, comparison of predictions from the two models indicates significant sensitivity and uncertainty involved in these predictions.
The paper describes a Large Eddy Simulation (LES) conducted for a non adiabatic rotating cavity with a radial inflow introduced from the shroud. The dimensionless mass flow rate of the radial inflow is Cw = 3500 and the rotational Reynolds number, based on the cavity outer radius, is equal to Req =1:2 x 106. The time averaged local Nusselt number on the heated wall is compared with the experimental data available from the literature, and with those derived from the solution of two Unsteady Reynolds Averaged Navier-Stokes (URANS) eddy viscosity models, namely the Spalart-Allmaras and the k-w SST model. It is shown that the Nusselt number is underpredicted in the lower part of the disc and over-predicted in the outer region by both URANS models, whereas the LES provides a much better agreement with the measurements. The behaviour results primarily from a different flow structure in the source region, which, in the LES, is found to be considerably more extended and show localized buoyancy phenomena that the URANS models investigated do not capture.
A CFD code for the prediction of flow and heat transfer in rotating turbine disc cavities is described and its capabilities demonstrated through comparison with available experimental data. Application of the method to configurations typically found in aeroengine gas turbine is illustrated and discussed. The code employs boundary-fitted coordinates and uses the κ-ε turbulence model with alternative near-wall treatments. The wall function approach and a one-equation near-wall model are compared and it is shown that there are particular limitations in the use of wall functions at low rotational Reynolds number.
The EMPAS collaborative project covered development and demonstration of an electric motor powered aero-engine simulator in the QinetiQ 5-metre wind-tunnel. As part of the project, the University of Surrey was responsible for background research and development of various flow measurement and system monitoring technologies, for use in the EMPAS windtunnel tests. Development of an integrated digital pressure rake system is presented, which has enabled assessment of duct flow characteristics and derivation of fan pressure ratio for the EMPAS system. A novel approach based on use of miniature, low cost microphones was developed, which successfully provided in-situ fan RPM measurement and highlighted several promising areas for future monitoring of fan/system health. A 7-hole pressure probe was used to great effect for extensive flow-field surveys, to investigate and validate the aerodynamic flow field effects associated with the aero-engine simulator. Wind-tunnel results from use of the microphone and 7-hole probe systems are analyzed and presented in detail.
Hot gas ingestion in a chute seal configuration has been numerically and experimentally investigated. First, the NGVs were included to generate a swirled annulus flow. This staged approach to rig configuration is used to understand the relative contribution of rotation and NGVs induced pressure asymmetries in turbine rim sealing flow ingestion. Computations were performed with a URANS model and a novel LES code including near wall boundary layer modelling, the wall-modelled LES (WMLES). The experimental data was obtained in the Oxford Rotor Facility (ORF). The main focus of this study was the mean cavity flow aerodynamics and the sealing performance of the chute seal under a range of operating conditions. These are studied through measurements of pressure and gas concentration within the rotor-stator disc cavity and the rim seal which are compared to CFD predictions. In addition, experimental and CFD assessments of concentration-based sealing effectiveness in the gas path for the vaned configuration are presented. Measurements were taken at a representative rotor leading edge axial position to focus on the radial diffusion and interaction between the purge flow and annulus flow. Overall the WMLES code better captured the interaction between main annulus and turbine cavity flow positioning it as a powerful tool with potential to be implemented in the design and verification process.
This paper presents a systematic study of flow and heat transfer mechanisms in a compressor disk cavity with an axial throughflow under centrifugal buoyancy-driven convection, comparing with previously published experimental data. Wall-modeled large-eddy simulations (WMLES) are conducted for six operating conditions, covering a range of rotational Reynolds number (3.2 x 10(5) - 2.2 x 10(6)), buoyancy parameter (0.11-0.26), and Rossby number (0.4-0.8). Numerical accuracy and computational efficiency of the simulations are considered. Wall heat transfer predictions are compared with measured data with a good level of agreement. A constant rothalpy core occurs at high Eckert number, appearing to reduce the driving buoyancy force. The flow in the cavity is turbulent with unsteady laminar Ekman layers observed on both disks except in the bore flow affected region on the downstream disk cob. The shroud heat transfer Nusselt number-Rayleigh number scaling agrees with that of natural convection under gravity for high Rayleigh numbers. Disk heat transfer is dominated by conduction across unsteady Ekman layers, except on the downstream disk cob. The disk bore heat transfer is close to a pipe flow forced convection correlation. The unsteady flow structure is investigated showing strong unsteadiness in the cavity that extends into the axial throughflow.
Buoyancy-induced flows occur in the rotating cavities of gas turbine internal air systems, and are particularly challenging to model due to the inherently unsteadiness of these flows. While the global features of such flows are well documented, detailed analyses of the unsteady structure and turbulent quantities have not been reported. In this work we use a high-order numerical method to perform large-eddy simulation (LES) of buoyancyinduced flow in a sealed rotating cavity with either adiabatic or heated disks. New insight is given into long-standing questions regarding the flow characteristics and nature of the boundary layers. The analyses focus on showing time-averaged quantities, including temperature and velocity fluctuations, as well as on the effect of the centrifugal Rayleigh number on the flow structure. Using velocity and temperature data collected over several revolutions of the system, the shroud and disk boundary layers are analysed in detail. The instantaneous flow structure contains pairs of large, counter-rotating convection rolls, and it is shown that unsteady laminar Ekman boundary layers near the disks are driven by the interior flow structure. The shroud thermal boundary layer scales as approximately Ra−1/3, in agreement with observations for natural convection under gravity.
Copyright © 1988 by ASME.The problem of radial inflow between two plane co-rotating discs with the angular velocity of the fluid at inlet equal to that of the discs is considered. An integral solution technique for turbulent flow, based on that of von Karman (1921), is described. Solutions are shown to be in good agreement with most of the available experimental data. For incompressible flow the pressure drop coefficient is a function of just two non-dimensional parameters; the radius ratio for the cavity and a throughflow parameter. For air flows compressibility can be important and an additional non-dimensional parameter is needed. Results for a wide range of conditions are presented graphically. These show the sensitivity of the pressure coefficient to the governing parameters and provide a quick method for estimating the pressure drop.
Reynolds-Averaged Navier-Stokes (RANS) computations have been conducted to investigate the flow and heat trans-fer between two co-rotating discs with an axial throughflow of cooling air and a radial bleed introduced from the shroud. The computational fluid dynamics (CFD) models have been cou-pled with a thermal model of the test rig, and the predicted metal temperature compared with the thermocouple data. CFD solutions are shown to vary from a buoyancy driven regime to a forced convection regime, depending on the radial inflow rate prescribed at the shroud. At a high radial inflow rate, the computations show an excellent agreement with the measured temperatures through a transient rig condition. At a low radial inflow rate, the cavity flow is destabilized by the thermal stratification. Good qualitative agreement with the measurements is shown, although a significant over-prediction of disc temperatures is observed. This is associated with under prediction of the penetration of the axial throughflow into the cavity. The mismatch could be the result of strong sensitivity to the prescribed inlet conditions, in addition to possible shortcomings in the turbulence modeling.
Experimental measurements from a new single stage turbine are presented. The turbine has 26 vanes and 59 rotating blades with a design point stage expansion ratio of 2.5 and vane exit Mach number of 0.96. A variable sealing flow is supplied to the disc cavity upstream of the rotor and then enters the annulus through a simple axial clearance seal situated on the hub between the stator and rotor. Measurements at the annulus hub wall just downstream of the vanes show the degree of circumferential pressure variation. Further pressure measurements in the disc cavity indicate the strength of the swirling flow in the cavity, and show the effects of mainstream gas ingestion at low sealing flows. Ingestion is further quantified through seeding of the sealing air with nitrous oxide or carbon dioxide and measurement of gas concentrations in the cavity. Interpretation of the measurements is aided by steady and unsteady computational fluid dynamics solutions, and comparison with an elementary model of ingestion.
The studies of constant wall thickness scroll expander have pointed out that geometries with large built-in volume ratios are necessary to achieve high performances in small-sized organic Rankine cycle (ORC) units. The variable wall thickness expander design offers the opportunity of increasing the geometric expansion ratio with the number of scroll turns remaining unchanged to avoid sealing and lubricating issues. In this paper, unsteady and three-dimensional computational fluid dynamics (CFD) simulations of scroll expander using variable wall thicknesses were therefore carried out to investigate the effects of the geometry on the internal flow behaviour. The scroll expander was integrated into an ORC unit fed by R123. The dynamic mesh technology of ANSYS Fluent was applied to generate the deforming mesh in the expander working chambers. The aerodynamic performance analysis yielded how over-expansion phenomena occurred at low pressure ratio while under-expansion phenomena were existing at high pressure ratio which are consistent with the thermodynamic theory of scroll expander. The higher pressure ratio was also contributing to higher temperature drops during the expansion process. Moreover, the occurrence of flank leakages through the radial clearances and its effects on the flow field were pointed out further proving the thermodynamic theory of scroll expander.
This paper presents the transient aerothermal analysis of a gas turbine internal air system through an engine flight cycle featuring multiple fluid cavities that surround a HP turbine disk and the adjacent structures. Strongly coupled fluid-structure thermal interaction problems require significant computational effort to resolve nonlinearities on the interface for each time step. Simulation times may grow impractical if multiple fluid domains are included in the analysis. A new strategy is employed to decrease the cost of coupled aerothermal analysis. Significantly lower fluid domain solver invocation counts are demonstrated as opposed to the traditional coupling approach formulated on the estimates of heat transfer coefficient. Numerical results are presented using 2D finite element conduction model combined with 2D flow calculation in five separate cavities interconnected through the inlet and outlet boundaries. The coupled solutions are discussed and validated against a nominal stand-alone model. Relative performance of both coupling techniques is evaluated.
in a rotor/stator cavity without heat transfer and buoyant flow in a rotor/rotor cavity. The numerical tool used employs a spectral element discretisation in two dimensions and a Fourier expansion in the remaining direction, which is periodic and corresponds to the azimuthal coordinate in cylindrical coordinates. The spectral element approximation uses a Galerkin method to discretise the governing equations, but employs high-order polynomials within each element to obtain spectral accuracy. A second-order, semi-implicit, stiffly stable algorithm is used for the time discretisation. Numerical results obtained for the rotor/ stator cavity compare favourably with experimental results for Reynolds numbers up to Re1 = 106 in terms of velocities and Reynolds stresses. The buoyancy-driven flow is simulated using the Boussinesq approximation. Predictions are compared with previous computational and experimental results. Analysis of the present results shows close correspondence to natural convection in a gravitational field and consistency with experimentally observed flow structures in a water-filled rotating annulus. Predicted mean heat transfer levels are higher than the available measurements for an air-filled rotating annulus, but in agreement with correlations for natural convection under gravity.
Sealing of the cavity formed between a rotating disc and a stator in the absence of a forced external flow is considered. In this circumstances the pumping action of the rotating disc may draw fluid into the cavity through the rim seal. Minimum cavity throughflow rates required to prevent such ingress are estimated experimentally and from a mathematical model. The results are compared with other worker's measurements. Measurements for three different types of rim seal are reported for a range of seal clearances and for rotational Reynolds numbers up to 3 × 106. The mathematical model is found to correlate the experimental data reasonably well.
Water use is a significant operational cost factor for large swimming pool facilities, however it has been overshadowed by the recent focus on energy consumption and carbon emissions. Currently it is difficult for operators to make decisions in relation to water efficiency due to the lack of information on the relationship between pool operation and water use. This study has started to address this issue by reviewing water use at a fully operational facility. The analysis of the consumption data has led to a proposal for a new water performance indicator, the Water Exchange Deficit. Modifications to the method of predicting water consumption have also been proposed to enable enhanced water management guidance to be developed.
With the rapid progress of computational fluid dynamics (CFD) and computer technology, CFD has been increasingly used for aero-engine component temperature predictions. This paper presents a review of the latest progress in this aspect with emphasis on internal air system applications. The thermal coupling methods discussed include the traditional finite element analysis (FEA), the conjugate heat transfer, FEA/CFD coupling procedure and other thermal coupling techniques. Special attention is made to identify the merits and disadvantages between the various methodologies. Discussion is further extended on the steady and transient thermal coupling applications.
A wall-modelled large-eddy simulation (WMLES) method previously validated against laboratory experiments is applied to a real engine disc cavity geometry with surface and air temperatures representative of maximum power conditions. An appropriate set of independent nondimensional parameters describing the problem is defined and the sensitivities to these parameters are investigated by independently varying each parameter in the WMLES. Effects of a change in disc temperature distribution and a reduction in radius of the downstream disc are also investigated. The flow and heat transfer mechanisms predicted are very similar to those found for the research rig configuration although rotating cavity flow structures with two or more lobes are found for the engine geometry rather than the single-lobed structures shown in (Gao and Chew, ASME J Eng Gas Turbines Power, 2022). The simulations are compared with an elementary model giving further insight into scaling of the flow and heat transfer with operating conditions. The model assumes a well-mixed core flow in the cavity with constant rothalpy, relates shroud heat transfer to that of natural convection under gravity for high Rayleigh number, and relates disc heat transfer to conduction across unsteady Ekman layers. An energy balance for the cavity is used to obtain an effective mass flow exchange rate between the axial throughflow and the disc cavity to the disc and shroud heat transfer and core temperature. The model is considered to give a useful basis for engineering calculations involving correlation and extrapolation of WMLES and experimental results.
Predicting the degree of hot gas ingestion into turbine disc cavities is a challenge for computational fluid dynamics due to the complex unsteady flow dynamics in turbine rim seals and sensitivity to operating condition and seal geometry. This paper reports research aimed at clarifying the effect of operating conditions on seal performance and turbulence modelling requirements. A systematic study of sealing performance for an axial rim seal is reported, comparing an unsteady Reynolds-averaged Navier-Stokes (URANS) model and wall-modelled large-eddy simulation (WMLES). The conditions considered are classed as rotation-driven ingestion, pressure-driven ingestion, and combined mechanism ingestion. WMLES and URANS results showed similar ingestion levels and seal flows within the pressure-driven regime. For the rotationally-driven condition URANS displays larger, more coherent vortical flow structures than the WMLES. The larger vortices in the URANS drive ingress into the wheel-space resulting in higher levels of ingestion than indicated by the WMLES. For the combined ingestion condition, WMLES shows higher levels of ingestion and flow unsteadiness than URANS. The present results give some explanation for the mixed results reported for the performance of URANS models in previous studies.
The buoyancy-affected flow in rotating disk cavities, such as occurs in compressor disk stacks, is known to be complex and difficult to predict. In the present work, large eddy simulation (LES) and unsteady Reynolds-averaged Navier-Stokes (RANS) solutions are compared to other workers’ measurements from an engine representative test rig. The Smagorinsky-Lilly model was employed in the LES simulations, and the RNG k- turbulence model was used in the RANS modeling. Three test cases were investigated in a range of Grashof number Gr=1.87 to 7.41 108 and buoyancy number Bo=1.65 to 11.5. Consistent with experimental observation, strong unsteadiness was clearly observed in the results of both models; however, the LES results exhibited a finer flow structure than the RANS solution. The LES model also achieved significantly better agreement with velocity and heat transfer measurements than the RANS model. Also, temperature contours obtained from the LES results have a finer structure than the tangential velocity contours. Based on the results obtained in this work, further application of LES to flows of industrial complexity is recommended.
This paper presents CFD (computational fluid dynamics) modelling of a chute type rim seal that has been previously experimentally investigated. The study focuses on inherent large-scale unsteadiness rather than that imposed by vanes and blades or external flow. A large-eddy simulation (LES) solver is validated for a pipe flow test case and then applied to the chute rim seal rotor/stator cavity. LES, Reynolds-averaged Navier-Stokes (RANS) and unsteady RANS (URANS) models all showed reasonable agreement with steady measurements within the disc cavity, but only the LES shows unsteadiness at a similar distinct peak frequency to that found in the experiment, at 23 times the rotational frequency. However, there are some significant differences between unsteadiness predicted and the measurements, and possible causes of these are discussed.
Flow and heat transfer in axial compressor disc cavities involve strong interaction of axial throughflow at the disc bores with centrifugal buoyant flow in the cavities. This paper presents large eddy simulation (LES) of flow and heat transfer in rotating cavities with a heated shroud and a relatively weak axial cooling throughflow. The conditions considered for a single cavity configuration correspond to Rossby numbers Ro=0.2 and 0.3, rotational Reynolds numbers Re Ω =3.2×10 5 and 7.7×10 5 , and buoyancy parameters βΔT=0.24 and 0.26. Reasonable agreement of the results with shroud heat transfer measurements was confirmed for the Ro=0.2 condition for which test data were available. A dual cavity configuration for Ro=0.3 and Re Ω =3.2×10 5 is also modelled. The simulations show that, at low Ro conditions, flow reversals occur along the length of the bore flow path, upstream and downstream of the rotating cavities. With the dual cavity strong, unsteady interactions between the flows in the two cavities occur. These flow interactions result in less stable flow structures, higher air temperatures within the cavities and lower shroud and disc heat transfer compared to the single cavity case. FFT analysis reveals a complex phase-locking mechanism between flows in the two cavities.
Previous studies have indicated some differences between steady CFD predictions of flow in a rotor-stator disc cavity with rotating bolts compared to measurements. Recently time-dependent CFD simulations have revealed the unsteadiness present in the flow and have given improved agreement with measurements. In this paper unsteady Reynolds averaged Navier-Stokes (URANS) 3600 model CFD calculations of a rotorstator cavity with rotor bolts were performed in order to better understand the flow and heat transfer within a disc cavity previously studied experimentally by other workers. It is shown that the rotating bolts generate unsteadiness due to wake shedding which creates time-dependent flow patterns within the cavity. At low throughflow conditions, the unsteady flow significantly increases the average disc temperature. A systematic parametric study is presented giving insight into the influence of number of bolts, mass flow rate, cavity gap ratio and the bolts-to-shroud gap ratio on the time depended flow within the cavity.
Research in rotational buoyancy-driven flow has shown that the flow within the compressor inter-disc cavities is highly three-dimensional and time dependent. Two approaches in the numerical modelling of the flow have been considered. One is to use 3D, unsteady CFD to model a single inter-disc cavity with axial throughflow. This is very computationally expensive. A second approach, adopted here, is to break down the complex flow process into separate physical mechanisms and introduce approximate but computationally efficient models for these processes. The aim is to produce a method that can be incorporated into current design practice. Two underlying flow mechanisms may be identified for this complex flow; the first associated with the flow within the inter-disc cavities and the second associated with the axial throughflow under the compressor disc bores. Using CFD, the modelling of these two underlying flow mechanisms has been combined and a steady axisymmetric modelling method has been developed. The technique has been applied to both a research compressor rig and to an actual gas turbine HP compressor rotor, and results have been compared to measured data.
When subject to highly swirling inlet flow, the bristles on the upstream face of a brush seal in gas turbine engines tend to slip circumferentially, which may lead to aeromechanical instability and seal failure. In this article, a new design of the front plate of brush seal, which mitigates this effect, is presented. Angled ribs on the upstream side of the front plate are used to reduce the swirl of the flow impacting on the bristle pack. The effects of the rib geometry, including angle of inclination and height-to-spacing ratio, are investigated using computational fluid dynamics, and a bulk porous medium model of the bristle pack, on a simple seal geometry. Results show that the ribs can effectively regulate the flow upstream of the bristle pack, reducing the swirl and channeling flow radially inward to the sealing section, resulting in decreased circumferential forces on the bristles. Ribs inclined at 20° to the radial direction and with height-to-spacing ratio of 0.4 were selected as the most effective of those investigated for the seal geometry under study. A model of an aeroengine preswirled cooling air chamber was created to give insight into the inlet swirl boundary conditions that a preswirl seal brush seal could be subjected to at a range of leakage flow rates and inlet swirl velocities. The new design and upstream roughness feature substantially reduced inlet swirl velocity incident on the bristle pack. The findings in this work could have a significant impact on brush seal design and, in particular, mitigate a significant operational risk of swirl-induced instability in high-pressure, high-speed shaft seal locations.
Unsteady flow dynamics in turbine rim seals are known to be complex and attempts accurately to predict the interaction of the mainstream flow with the secondary air system cooling flows using CFD with RANS turbulence models have proved difficult. In particular, published results from RANS models have overpredicted the sealing effectiveness of the rim seal, although their use in this context continues to be common. Previous authors have ascribed this discrepancy to the failure to model flow structures with a scale greater than can be captured in the small sector models typically used. This paper presents results from a series of Large-Eddy Simulations (LES) of a turbine stage including a rim seal and rim cavity for, it is believed by the authors, the first time. The simulations were run at a rotational Reynolds number Reθ = 2.2 × 106 and a main annulus axial Reynolds number Rex = 1.3 × 106 and with varying levels of coolant mass flow. Comparison is made with previously published experimental data and with unsteady RANS simulations. The LES models are shown to be in closer agreement with the experimental sealing effectiveness than the unsteady RANS simulations. The result indicates that the previous failure to predict rim seal effectiveness was due to turbulence model limitations in the turbine rim seal flow. Consideration is given to the flow structure in this region.
The internal gear box (IGB) of an aeroengine represents a severe challenge in computational fluid dynamics (CFD). In the present study, an axisymmetric CFD model was assessed to investigate the complex internal air flow in an aeroengine IGB. All the non-axisymmetric components and geometry features inside the gear box, such as bearings, gears, bolts and slots, as well as the radial drive system and vent pipes, were simulated using porous media models. Their flow resistance was estimated either by empirical correlations or by preparatory CFD studies and comparison with measurements. To evaluate the CFD technique adopted in the present investigation, a separate bolt windage study was conducted using a similar axisymmtric CFD model with the porous media approach. Good agreement of the bolt windage with other workers' rig test data was observed. The present application of the porous media approach into a complex gear box flow represents a first attempt to use state of art CFD to assist an industrial design. Both maximum take-off (MTO) and ground idle (GI) running conditions were investigated. The complex flow patterns in the gear box were obtained. The results show a similar dimensionless performance of intermediate pressure (IP) and high pressure (HP) gears between the two operating conditions. For the present gear box arrangement under investigation, the CFD results suggest that the airflows induced by the HP gear and HP bearing are higher than their IP counterparts. A comparison with power absorption rig test data for the similar HP crownwheel in isolation shows that an assumption of pressure loss coefficient of 10 for the porous media of bevel gears may be appropriate, as the HP gear torque coefficient obtained in the CFD prediction is equal to 0.05, very close to its expected value. In addition, the effects of an assumed stationary IP gear and a large seal clearance on the HP gear performance were also investigated. The numerical results show that their impacts are insignificant, probably due to the strong pumping effects of the HP gear. Further discussion on the possible influence of the airflow on the oil motion within the gearbox and assistance to improve the traditional internal airflow models used for bearing chamber sealing analysis was also made. Three dimensional geometry modeling and inclusion of the oil phase are considered feasible. Such further investigations would aid the understanding of the interaction between the induced airflow due to the rotating components and oil motion, and their impact on oil scavenging behaviour and `windage' contribution to heat oil.