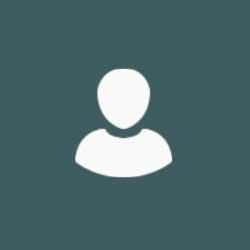
Ling Zhang
Publications
The tensile strength is an important material attribute of granular products, and diametrical compression is one of the most common methods to determine the tensile strength of the agglomerate. In this study, three-dimensional diametrical compression tests of annular agglomerates with various bonding strengths, i.e. interfacial energies and internal holes, are for the first time modelled by the Discrete Element Method (DEM) with the JKR theory. The fracture patterns and tensile strengths of annular specimens are analysed and compared with those of disc specimens. It is found that annular specimens show complete tension failures with progressive fractures along the loading diameter towards the central hole, while the disc specimens show wedge-shaped shear fractures near the platens. The results also show that the tensile strengths of annular specimens are linear with the surface energy, whereas increase with the size of internal hole and then decrease with the size of internal hole. A dimensionless parameter is introduced to analyse the failure mechanism of the agglomerate. This parameter quantifies the ratio between the external force exerted by the platens and the cohesive force among bonded particles. The proposed parameter emphasises the crucial influence of the internal hole size of an annular agglomerate and bonding capacity on its tensile strength.
[Display omitted] •Friction-induced heat generation and heat transfer models are developed.•Thermal behaviours of particles and walls are experimentally and numerically analysed.•Effects of rotation speed on temperature rises on both particles and walls are examined. In many granular material handling processes, heat generation, and subsequent temperature rise, due to contacts between particles and surfaces is common. Aiming to explore this phenomenon, friction-induced heat generation and heat transfer models are developed and implemented into a Discrete Element Method (DEM) in this paper. The DEM models are validated qualitatively for the temperature distribution pattern and quantitatively for the evolution of particle temperature rise using data obtained experimentally. Moreover, the temperature distribution of the drum end plates obtained in the simulations shows the same annulus pattern observed in experiments. It is also found that increasing the rotation speed of the drum leads to an increase in the annular heated region of drum and in the net heat that particles obtain. In addition, a higher rotation speed leads to higher absolute fluctuations and lower relative variability of particle temperature.
Triboelectrification due to frictional contacts between particles and surfaces is prevalent in many powder handling processes. Aiming to explore the friction-induced electrostatic charging behavior, a discrete element method (DEM) is developed for the first time in the current article, in which a frictional charging model and electrostatic interaction models are implemented. The charge accumulation on both the particles and the surface in a rotational container is then analyzed numerically and experimentally to evaluate the developed DEM. The numerical results for the frictional electrification between insulant particles and an insulant wall agree well with the experimental measurement. It is also shown that both the net charge on the particles and the degree of the particle dispersion are a function of the charging time. Moreover, it is revealed that the friction-induced particle charge enhances particle dispersion, and increases the granular temperature due to the electrostatic interactions.
Diffusion-induced swelling or shrinkage of particles is ubiquitous in many industrial processes and nature. Aiming to rigorously model these deformable particles, a microscopic model that considers the microstructural evolution of individual particles is developed for the first time and implemented into the discrete element method (DEM), which is experimentally validated. The robustness of this model is also evaluated by comparing its performance with a macroscopic diffusion-induced swelling model and a phenomenological swelling model. The swelling behaviours of a single particle and particle beds of various configurations in water are then analysed. It is shown that the microscopic swelling model and the phenomenological swelling model can better describe the swellings of single particle and particle beds than the macroscopic swelling model. Moreover, the microscopic swelling model can not only reproduce the phenomena of volume expansion of particles but also well predict the microstructural evolution of individual particles, as observed experimentally. Furthermore, the microscopic swelling model is capable of describing the shrinkage processes and the particle-particle diffusions of swellable particles. It is hence demonstrated that DEM with the microscopic swelling model, which captures the microscopic physical mechanisms of particle swelling and the microstructural change of swelling particles, could be a useful tool for modelling swellable granular materials in various industrial processes.
Rotary tabletting presses are widely used to produce tablets in the pharmaceutical industry. In the tabletting process using a rotary press, rotary die filling is one of critical process steps, as powder behaviour during die filling dictates the quality of final products, such as dosage and weight variations. It is hence of importance to understand powder flow behaviour during rotary die filling. The purpose of this study is to identify the critical process parameters and material attributes that determine the die filling performance. For this purpose, a model rotary die filling system with a paddle feeder was constructed to mimic the powder feeding process in a typical rotary press. Using this model system, the effects of turret speed and paddle speed on die filling behaviour were investigated. Three grades of microcrystalline cellulose powders were considered. It was found that the turret speed has a more pivotal role in controlling the die filling performance than the paddle speed. In addition, it is demonstrated that powder flowability has a great impact on the fill weight variation, and a higher weight variation is induced for the powders with poorer flowability.
[Display omitted] •The GPU-based DEM approach is used to study the lab-scale die filling system.•The numerical model is calibrated and validated well with experimental data.•The stirrer occupying a specific space and reducing the effective discharge area.•Flow patterns of the free-flowing powder during die filling process is analyzed. Understanding die filling behaviour of powders is critical in developing optimal formulation and processes in various industries, such as pharmaceuticals and fine chemicals. In this paper, forced die filling is analysed using a graphics processing unit (GPU) based discrete element method (DEM), for which a powder feeder equipped with a wired stirrer is considered. The influences of operating parameters, such as the initial powder bed height, the filling speed, and the stirrer speed, on the die filling performance are systematically explored. It is shown that a larger initial powder bed height leads to a higher filling ratio, which can be attributed to a higher filling intensity; while the deposited particle mass in the die is almost independent of the powder bed height, when the initial fill level is larger than a critical bed height. Additionally, the filling ratio slightly increases with the increase of stirrer speed for cases with a stirrer, while the filling ratios are lower than that without a stirrer, which is attributed to the stirrer occupying some space above the die and reducing the effective discharge area. The obtained results can provide useful information for optimising the feeder system design and the operating condition.
As one of critical process steps during pharmaceutical tabletting, rotary die filling is still not well understood. To address this issue, a model rotary die filling system with a paddle feeder was developed to closely mimic the industrial process. Using this model system, the performance of various pharmaceutical powders at different turret and paddle speeds was evaluated, and the dependence of fill variation on process conditions and material properties was examined. A comprehensive dataset was created and reported here to show the effects of material and process parameters on the die filling performance and the filling consistency. It is believed that the data can also be used for data-driven process modelling and for developing robust machine learning models for pharmaceutical manufacturing.
Twin screw granulation (TSG) is increasingly used to produce granules in various industries, such as food, pharmaceutical, and fine chemicals. However, there is a large parametric space in terms of screw designs, formulation properties and operating conditions, so how to maximise the production throughput while maintaining consistent product quality is not a trivial task and still needs further investigation. In this study, the TSG process was systematically analysed using a discrete element method (DEM) based on the graphics processor unit (GPU) architectures that can provide not only macroscopic information but also microscopic insights into the complicated TSG process. In particular, the particle flow profiles and residence time distributions were obtained from the simulations and analysed in details. The effects of particle size and screw speed on flow behaviour of particles in TSG were also explored. It was shown that the mean residence time and its variance in the granulator decreased with increasing particle size and screw speed. The E-curves of the residence time with larger particle size at higher screw speed had a narrower spread, implying that particles with a larger size had similar residence time in the twin screw granulator. In addition, the cumulative distribution function, the F-curves, showed a higher increasing rate for larger particles and higher screw speeds, indicating a faster conveying efficiency. (C) 2020 Elsevier B.V. All rights reserved.
During twin screw granulation (TSG), small particles, which generally have irregular shapes, agglomerate together to form larger granules with improved properties. However, how particle shape impacts the conveying characteristics during TSG is not explored nor well understood. In this study, a graphic processor units (GPUs) enhanced discrete element method (DEM) is adopted to examine the effect of particle shape on the conveying characteristics in a full scale twin screw granulator for the first time. It is found that TSG with spherical particles has the smallest particle retention number, mean residence time, and power consumption; while for TSG with hexagonal prism (Hexp) shaped particles the largest particle retention number is obtained, and TSG with cubic particles requires the highest power consumption. Furthermore, spherical particles exhibit a flow pattern closer to an ideal plug flow, while cubic particles present a flow pattern approaching a perfect mixing. It is demonstrated that the GPU-enhanced DEM is capable of simulating the complex TSG process in a full-scale twin screw granulator with non-spherical particles.
Continuous powder blending is an essential operation during continuous pharmaceutical manufacturing. However, the complex granular dynamics in the blender is still poorly understood. This study employs a graphic processor unit (GPU) enhanced discrete element method (DEM) to analyse the granular dynamics in a continuous blender. Numerical results indicate that only a small fraction of powder distributes in the upper region of the blender, while most of that distributes in the middle and lower regions. Besides, a higher impeller speed leads to a smaller hold-up mass and a shorter mean residence time. Interestingly, the maximum number of blade passes is achieved at an intermediate impeller speed. There are two distinct regimes during continuous blending: i) a shearing regime at low impeller speeds; and ii) a dynamic regime at high impeller speeds. This study demonstrates that the GPU-enhanced DEM can be a robust tool for analysing powder flow during continuous pharmaceutical manufacturing. [Display omitted] •GPU-enhanced DEM analysis on the full-scale continuous blending is performed.•Impeller speed has a significant impact on the powder flow in the inclined blender.•At steady-state, powder mainly distributes in the middle and bottom zones of blender.•Maximum number of blade passes can be achieved at an intermediate impeller speed.
[Display omitted] •Powder characteristics have a significant influence on powder flow behaviour during die filling.•For free-flowing powders, flow behaviours in linear and rotary die filling are similar.•For poor-flowing powders, a higher filling efficiency is achieved during linear die filling than rotary die filling. In the pharmaceutical industry, linear die filling is widely employed in R&D, while rotary die filling is very common in commercial production. It is not clear if powder die filling behaviour in a linear die filling system is representative of the flow performance in a rotary tablet press. In this study, a linear die filling system and a rotary die filling system were used to examine flow behaviours of both poor-flowing and free-flowing powders. It was found that the performance of poor-flowing powder in the linear die filling system is slightly better than that in the rotary die filling system, while the performance of free-flowing powders in the linear die filling system is similar to that in the rotary die filling system. Hence, it is suitable to use the linear die filling system to estimate the flow behaviour during rotary die filling with free-flowing powders, but caution needs to be taken when poor-flowing powders are used.
The presence of liquids in particulate materials can have a significant effect on their bulk behaviour during processing and handling. It is well recognised that the bulk behaviour of particulate materials is dominated by the interactions between particles. Therefore, a thorough understanding of particle-particle interaction with the presence of liquids is critical in unravelling complex mechanics and physics of wet particulate materials. In the current study, a discrete element method for wet particulate systems was developed, in which a contact model for interactions with pendular liquid bridges between particles of different sizes was implemented. In order to evaluate the accuracy and robustness of the developed DEM, normal elastic impacts of wet particles with a wall were systematically analysed. It was shown that the DEM simulations can accurately reproduce the experimental observations reported in the literature. In addition, the DEM analysis was also in good agreement with the elastohydrodynamic model. It was further demonstrated that the rebound behaviour of wet particles is dominated by the Stokes number. There was a critical Stokes number, below which the particle will stick with the wall. For impacts with a Stokes number higher than the critical Stokes number, the coefficient of restitution increases as the stokes number increases for elastic particles. It was also found that the contact angle and surface tension played an insignificant role in the normal impact of wet particles, while the viscosity of the liquid has a dominant effect on the rebound behaviour.