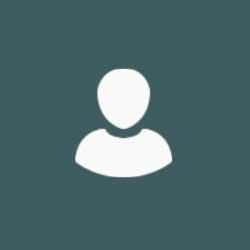
Dr Shumaila Babar
Academic and research departments
Centre for Engineering Materials, School of Mechanical Engineering Sciences.Publications
The operation of a lithium-sulfur (Li-S) battery involves the transport of Li + ions and soluble sulfides mostly in the form of solvated ions. Key challenges in the development of Li-S battery technology are the diffusion of Li + in micropores filled with sulfur and eliminating the “shuttling” of polysulfides. Ion dimensions in solvated and desolvated forms are key parameters determining the diffusion coefficient and the rate of transport of such ions, while constrictivity effects due to the effect of pore size compared to ion size control both transport and filling of the pores. We present molecular simulations to determine the solvation parameters of electrolyte ions and sulfides S 2 2− , S 4 2− , S 6 2− , and S 8 2− in two different electrolyte systems: LiTFSI in DOL/DME and LiPF 6 in EC/DMC. The calculated parameters include the coordination number and the geometrically optimized model and dimensions, using the van der Waals surface approach, of the solvated and desolvated ions. The desolvation energy of the electrolyte ions is also calculated. Such data is useful for the modeling and design of the pore sizes of cathode host materials to be able to accommodate the different sulfides while minimizing their “shuttling” between cathode and anode.
The performance of single crystal CdZnTe radiation detectors is dependent on both the bulk and the surface properties of the material. After single crystal fabrication and mechanical polishing, modification of the surface to remove damage and reduce the surface leakage current is generally achieved through chemical etching followed by a passivation treatment. In this work, CdZnTe single crystals have been chemically etched using a bromine in methanol (BM) treatment. The BM concentrations employed were 0.2 and 2.0 (v/v) % and exposure times varied between 5 and 120 s. Angle resolved XPS and sputter depth profiling has been employed to characterize the surfaces for the different exposure conditions. A Te rich surface layer was formed for all exposures and the layer thickness was found to be independent of exposure time. The enriched Te layer thickness was accurately determined by calibrating the sputter rate against a CdTe layer of known thickness. For BM concentrations of 0.2 (v/v) % and 2 (v/v) %, the Te layer thickness was determined to be 1.3 ± 0.2 and 1.8 ± 0.2 nm, respectively. The BM etched surfaces have subsequently been passivated in a 30 wt.% HO solution employing exposure time of 15 s. The oxide layer thickness has been calculated using two standard XPS methodologies, based on the Beer-Lambert expression. The TeO thickness calculated from ARXPS data are slightly higher than the thickness obtained by the simplified Beer-Lambert expression. For BM exposures of 30-120 s followed by a passivation treatment of 30 wt. % HO solution employing an exposure time 15 s, the ARXPS method gave an average TeO thickness value of 1.20 nm and the simplified Beer-Lambert expression gave an average thickness value of 0.99 nm. © 2012 Elsevier B.V. All rights reserved.
Ultra-thin CdTe:As/Cd1-xZnxS photovoltaic solar cells with an absorber thickness of 0.5 µm were deposited by metal-organic chemical vapour deposition on indium tin oxide coated boro-aluminosilicate substrates. The Zn precursor concentration was varied to compensate for Zn leaching effects after CdCl2 activation treatment. Analysis of the solar cell composition and structure by X-ray photoelectron spectroscopy depth profiling and X-ray diffraction showed that higher concentrations of Zn in the Cd1-xZnxS window layer resulted in suppression of S diffusion across the CdTe/Cd1-xZnxS interface after CdCl2 activation treatment. Excessive Zn content in the Cd1-xZnxS alloy preserved the spectral response in the blue region of the solar spectrum, but increased series resistance for the solar cells. A modest increase in the Zn content of the Cd1-xZnxS alloy together with a post-deposition air anneal resulted in an improved blue response and an enhanced open circuit voltage and fill factor. This device yielded a mean efficiency of 8.3% over 8 cells (0.25 cm2 cell area) and best cell efficiency of 8.8%.
Graphene electrodes are investigated for electrochemical double layer capacitors (EDLCs) with lithium ion electrolyte, the focus being the effect of the pore size distribution (PSD) of electrode with respect to the solvated and desolvated electrolyte ions. Two graphene electrode coatings are examined: a low specific surface area (SSA) xGNP-750 coating and a high SSA coating based on a-MWGO (activated microwave expanded graphene oxide). The study comprises an experimental and a computer modeling part. The experimental part includes fabrication, material characterization and electrochemical testing of an EDLC with xGNP-750 coating electrodes and electrolyte 1M LiPF6 in EC:DMC. The computational part includes simulations of the galvanostatic charge-discharge of each EDLC type, based on a continuum ion transport model taking into account the PSD of electrodes, as well as molecular modeling to determine the parameters of the solvated and desolvated electrolyte ions and their adsorption energies with each type of electrode pore surface material. Predictions, in agreement with the experimental data, yield a specific electrode capacitance of 110 F g(-1) for xGNP-750 coating electrodes in electrolyte 1M LiPF6 in EC:DMC, which is three times higher than that of the high SSA a-MWGO coating electrodes in the same lithium ion electrolyte.
A major challenge in the simulation of Li-S batteries is that the electrochemical reaction parameters supplied from the fitting of 0-d or 1-d models depend on the cathode and separator microstructure, so these parameters cannot be used in the design and optimization of material microstructure. The present investigation fits the electrochemical reaction kinetics employing a continuum model taking into account the pore size distribution and tortuosity of cathode and separator in the transport of sulfur molecules and ion species (Li+ ion, electrolyte and sulfide anions) in solvated or desolvated form depending on pore size. Hence, the specified reaction kinetics parameters are independent from the material microstructure. The Li-S redox reaction model includes six redox reactions in the cathode and the lithium redox reaction at the anode. Reactions are assumed to take place in the electrolyte solution rather than in the solid phase of sulfur or lithium sulfide precipitates, where dissolution/precipitation kinetics is modeled especially for the low solubility compounds: sulfur, Li2S and Li2S2. The fitting exercise is conducted based on experimental data of a cyclic voltammetry cycle accompanied by in operando UV-vis spectroscopy. The investigated battery has electrolyte LiTFSI in DOL/DME and no electrocatalysts in any part of the cell.