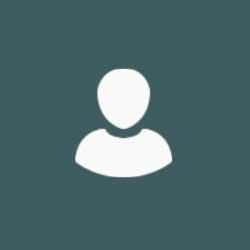
Dr Vladislav Ganine
Publications
Accurate prediction of metal temperatures, blade tip and seal clearances in high pressure compressor and turbine air systems leads to dramatic improvements in overall aero-engine efficiency and component life. Fast transients during an engine flight profile may introduce large changes in geometry between adjacent rotor and stator components. The changing dynamics in a few critical seals and interfaces can change the dynamics of the entire engine, compromising efficiency, integrity and long service life. In this paper we present results of a coupled aero-thermo-mechanical transient simulation of a high pressure turbine assembly throughout an engine flight cycle. The fluid and solid model geometry is approximated as 2D axisymmetric. The problem, formulated as a four field coupled multiphysics system of equations, is simplified using a quasi-steady state assumption: the transient thermal solid problem is coupled to a sequence of steady fluid problems and static structural problems. The predicted results compare well with the experimental measurements over the entire fluid-solid interface. We show improvement in transient predictions isolating the effects of the solid domain deformation. The remaining transient error is linked to temporal uncertainties in the fluid model inlet boundary conditions which were taken as a spatial average of the main annulus flow conditions.
Better understanding and more accurate prediction of heat transfer and cooling flows in aero engine components in steady and transient operating regimes are essential to modern engine designs aiming at reduced cooling air consumption and improved engine efficiencies. This paper presents a simplified coupled transient analysis methodology that allows assessment of the aerothermal and thermomechanical responses of engine components together with cooling air mass flow, pressure and temperature distributions in an automatic fully integrated way. This is achieved by assembling a fluid network with contribution of components of different geometrical dimensions coupled to each other through dimensionally heterogeneous interfaces. More accurate local flow conditions, heat transfer and structural displacement are resolved on a smaller area of interest with multidimensional surface coupled computational fluid dynamics (CFD)/FE codes. Contributions of the whole engine air-system are predicted with a faster monodimensional flow network code. Matching conditions at the common interfaces are enforced at each time-step exactly by employing an efficient iterative scheme. The coupled simulation is performed on an industrial high pressure turbine (HPT) disk component run through a square cycle. Predictions are compared against the available experimental data. The paper proves the reliability and performance of the multidimensional coupling technique in a realistic industrial setting. The results underline the importance of including more physical details into transient thermal modeling of turbine engine components.
Conjugate heat-transfer problems are typically solved using partitioned methods where fluid and solid subdomains are evaluated separately by dedicated solvers coupled through a common boundary. Strongly coupled schemes for transient analysis require fluid and solid problems to be solved many times each time step until convergence to a steady state. In many practical situations, a fairly simple and frequently employed fixed-point iteration process is rather ineffective; it leads to a large number of iterations per time step and consequently to long simulation times. In this article, Anderson mixing is proposed as a fixed-point convergence acceleration technique to reduce computational cost of thermal coupled fluid–solid problems. A number of other recently published methods with applications to similar fluid–structure interaction problems are also reviewed and analyzed. Numerical experiments are presented to illustrate relative performance of these methods on a test problem of rotating pre-swirl cavity air flow interacting with a turbine disk. It is observed that performance of Anderson mixing method is superior to that of other algorithms in terms of total iteration counts. Additional computational savings are demonstrated by reusing information from previously solved time steps.
The paper presents a computational procedure for heterogeneous coupled analysis of 1D flow network models of air engine secondary air systems and 2D/3D solid thermo-mechanical finite element models of engine components. We solve an unsteady heat transfer problem over solid domain coupled to a sequence of structural static and steady flow problems using a quasi-steady state approximation. Strong coupling is achieved at each time step by a fixed-point iteration, based on the successive solution of the fluid and the solid sub-problems. The procedure is applied to a 2D axisymmetric finite element model of an intermediate pressure turbine assembly coupled to a flow network model of whole engine secondary air system simulated through a square cycle. The simulation results are compared to reference stand-alone predictions showing important non-negligible coupled effects and component interactions of a multidisciplinary multi-physical nature resolved in an efficient and automatic fashion.
Better understanding and more accurate prediction of heat transfer and cooling flows in aero engine components in steady and transient operating regimes are essential to modern engine designs aiming at reduced cooling air consumption and improved engine efficiencies. This paper presents a simplified coupled transient analysis methodology that allows assessment of the aerothermal and thermomechanical responses of engine components together with cooling air mass flow, pressure and temperature distributions in an automatic fully integrated way. This is achieved by assembling a fluid network with contribution of components of different geometrical dimensions coupled to each other through dimensionally heterogeneous interfaces. More accurate local flow conditions, heat transfer and structural displacement are resolved on a smaller area of interest with multidimensional surface coupled CFD/FE codes. Contributions of the whole engine air-system are predicted with a faster mono dimensional flow network code. Matching conditions at the common interfaces are enforced at each time step exactly by employing an efficient iterative scheme. The coupled simulation is performed on an industrial high pressure turbine disk component run through a square cycle. Predictions are compared against the available experimental data. The paper proves the reliability and performance of the multidimensional coupling technique in a realistic industrial setting. The results underline the importance of including more physical details into transient thermal modelling of turbine engine components.
This paper presents the transient aero-thermal analysis of a gas turbine internal air system through an engine flight cycle featuring multiple fluid cavities that surround a HP turbine disk and the adjacent structures. Strongly coupled fluid-structure thermal interaction problems require significant computational effort to resolve nonlinearities on the interface for each time step. Simulation times may grow impractical if multiple fluid domains are included in the analysis. A new strategy is employed to decrease the cost of coupled aero-thermal analysis. Significantly lower fluid domain solver invocation counts are demonstrated as opposed to the traditional coupling approach formulated on the estimates of heat transfer coefficient. Numerical results are presented using 2D FE conduction model combined with 2D flow calculation in five separate cavities interconnected through the inlet and outlet boundaries. The coupled solutions are discussed and validated against a nominal stand-alone model. Relative performance of both coupling techniques is evaluated.
This paper describes a coupling framework for parallel execution of different solvers for multi-physics and multi-domain simulations with an arbitrary number of adjacent zones connected by different physical or overlapping interfaces. The coupling architecture is based on the execution of several instances of the same coupling code and relies on the use of smart edges (i.e., separate processes) dedicated to managing the exchange of information between two adjacent regions. The collection of solvers and coupling sessions forms a flexible and modular system, where the data exchange is handled by independent servers that are dedicated to a single interface connecting two solvers’ sessions. Accuracy and performance of the strategy is considered for turbomachinery applications involving Conjugate Heat Transfer (CHT) analysis and Sliding Plane (SP) interfaces.
This paper presents the transient aerothermal analysis of a gas turbine internal air system through an engine flight cycle featuring multiple fluid cavities that surround a HP turbine disk and the adjacent structures. Strongly coupled fluid-structure thermal interaction problems require significant computational effort to resolve nonlinearities on the interface for each time step. Simulation times may grow impractical if multiple fluid domains are included in the analysis. A new strategy is employed to decrease the cost of coupled aerothermal analysis. Significantly lower fluid domain solver invocation counts are demonstrated as opposed to the traditional coupling approach formulated on the estimates of heat transfer coefficient. Numerical results are presented using 2D finite element conduction model combined with 2D flow calculation in five separate cavities interconnected through the inlet and outlet boundaries. The coupled solutions are discussed and validated against a nominal stand-alone model. Relative performance of both coupling techniques is evaluated.