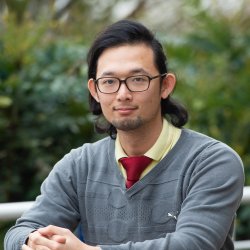
Dr Weeliam Khor
Academic and research departments
School of Mechanical Engineering Sciences, School of Sustainability, Civil and Environmental Engineering.About
Biography
WeeLiam is a Charted Engineer (CEng) and has a PhD in Mechanical Engineering, funded by TWI and Brunel University. His research focuses primarily on fracture mechanics and mechanical testing. Some research findings contributed to the improvement of fracture toughness standards ISO 12135 and ISO 15653. He's currently a member of the BSI's toughness testing group and IOP's Applied Mechanics Group.
WeeLiam have been working on:
- Thermographic image analysis using ML approaches.
- Material enabled NDE.
- Mechanical characterization of composite structures.
- Assessment of fracture toughness of metal matrix composites.
- Fracture, fatigue, corrosion and integrity assessment of cast iron structures.
Areas of specialism
My qualifications
Study of Crack Tip Opening Displacement (CTOD) in Single Edge Notched Bend (SENB) specimens.
Affiliations and memberships
ResearchResearch interests
- Fracture mechanics
- Mechanical testing
- Fracture toughness testing
- Finite element modelling of cracked components
- Image analysis
- Application of machine learning techniques.
Research collaborations
Atkins TISICS Thames Water Mott MacDonald DSTL QinetiQ RMIT
Cambridge Image Analysis Group (CIA) in DAMTP, University of Cambridge
Indicators of esteem
Engineering module lead for the 100 Scientists of Malaysia
https://www.facebook.com/100Scientists/
https://www.instagram.com/100.scientistsofmalaysia/
https://www.thestar.com.my/news/education/2020/02/02/magnifying-malaysi…
Invited peer-reviewer:
EPSRC standard award
EPSRC new investigator award
Fatigue & Fracture of Engineering Materials & Structures
International Journal of Pressure Vessels and Piping
Journal of Pipeline Science and Engineering
Journal of Composite Materials
Composites Communications
Proceedings of the Institution of Civil Engineers: Structures and Buildings
Research interests
- Fracture mechanics
- Mechanical testing
- Fracture toughness testing
- Finite element modelling of cracked components
- Image analysis
- Application of machine learning techniques.
Research collaborations
Atkins TISICS Thames Water Mott MacDonald DSTL QinetiQ RMIT
Cambridge Image Analysis Group (CIA) in DAMTP, University of Cambridge
Indicators of esteem
Engineering module lead for the 100 Scientists of Malaysia
https://www.facebook.com/100Scientists/
https://www.instagram.com/100.scientistsofmalaysia/
https://www.thestar.com.my/news/education/2020/02/02/magnifying-malaysi…
Invited peer-reviewer:
EPSRC standard award
EPSRC new investigator award
Fatigue & Fracture of Engineering Materials & Structures
International Journal of Pressure Vessels and Piping
Journal of Pipeline Science and Engineering
Journal of Composite Materials
Composites Communications
Proceedings of the Institution of Civil Engineers: Structures and Buildings
Publications
The through-the-thickness reinforcement of carbon-epoxy composite joints with shape memory alloy (SMA) tufts has shown significant improvement of the mechanical strength, fracture toughness, and delamination resistance. This study explores the thermal-electric properties of SMA filaments tufted in composite T-joints to exhibit multiple functionalities including material-enabled thermographic inspection and structural health monitoring via in-situ strain sensing. Infrared thermography image analysis was performed on both pristine and damaged T-joint specimens subject to pull-off testing. Experimental results showed that the heat generated by SMA tuftsmeasured by an infrared camera provided accurate indication of delamination perpendicular to the tuft direction. SMA tufts were also used as strain sensors embedded within the T-joint. Local changes of the electrical resistance in SMA filaments, both separately and within the joint, were observed during pulling loads. Digital Image Correlation measurements exhibited good correlation between electrical resistance variations and the opening of delamination. These results pave the way for the development of multifunctional composite joining systems combining enhanced through-the-thickness damage tolerance and self-sensing capabilities.
In this article, we demonstrated the physical application of a portable infrared (IR) security scanning system for the non-contact and stand-off detection of target objects concealed underneath clothing. Such a system combines IR imaging and transfer learning with convolutional neural network (CNN) to enhance the detection of weak thermal signals and automate the classification of IR images. A mid-wavelength IR detector was used to record the real-time heat emitted from the clothing surface by human subjects. Concealed objects reduce transmissivity of IR radiation from the body to the clothing surface, generally showing lower IR intensity compared to regions without objects. Due to limited resource for training data, the transfer learning approach was applied by fine tuning a pre-trained CNN ResNet-50 model using the ImageNet database. Two image types were here investigated, i.e., raw thermal and Fuzzy-c clustered images. Receiver operating characteristic curves were built using a holdout set, showing an area-under-the-curve of 0.8934 and 0.9681 for the raw and Fuzzy-c clustered image models, respectively. The Gradient-weighted Class Activation Mapping (Grad-CAM) visualisation method was used to improve the target identification, showing accurate prediction of the object area. It was also found that complex clothing, such as those composed of materials of different transmissivity, could mislead the model in classification. The proposed IR-based detector has shown potentials as a non-contact, stand-off security scanning system that can be deployed in diverse locations and ensure higher safety of civilians.
Multifunctional fibre reinforced polymer (FRP) composites combine multiple properties that can include mass efficiency, damage resistance, damage tolerance, self-repair, in-service health monitoring and ease of inspection. This paper describes a new type of multifunctional FRP composite material that enables large improvements to the interlaminar fracture toughness and damage tolerance whilst also allowing rapid self-sensing and material-enabled thermography capabilities. The composite material is reinforced in the through-thickness direction using shape memory alloy (SMA) wires inserted by tufting.Tufting is a cost-effective manufacturing process that uses commercially available automated systems to insert yarns in the through-the-thickness direction of dry fabric preforms [1]. Tufting uses a single needle to penetrate the fabric stack, and requires access only from a single side of the preform. As shown in Fig. 1, thin and flexible SMA filaments made of nitrol (Ni-Ti alloy) were tufted into six layers of 0˚/90˚ non-crimp carbon fabric using a KSL RS 522 tufting machine mounted on a KUKA KR240–2 robotic arm. The tufted fabric was infused with epoxy resin using the resin transfer moulding (RTM) process. The final cured composite panel was cut into double cantilever beam (DCB) coupons to perform mode I interlaminar fracture toughness tests according to the ASTM D5528-01 specification.
Variation of Crack Tip Opening Displacement (CTOD) test values can have a significant effect on the Engineering Critical Assessment of a structure. This paper examines the development of CTOD with increasing load in an austenitic stainless steel. The silicone replication method giving variation of CTOD across the specimen thickness, and Digital Image Correlation (DIC) are compared to each other, and in turn to clip gauge measurements from tests. Results from Finite Element models are also presented. Estimations of CTOD from BS 7448‐1, ISO 12135 and ASTM E1820, and a proposed modification from JWES are compared to the experimental data from the crack cast in silicone compound – assumed to be the actual CTOD. The DIC measurement showed consistency with crack replicas, and a formula is given to estimate CTOD using DIC. For high strain hardening austenitic stainless steel, both the JWES and ASTM E1820 estimations provide adequate accuracy for CTOD.
Adhesively bonded joints are susceptible to contamination of surfaces during manufacture and environmental deterioration in real operating conditions. These may cause the generation of so-called “kissing bonds” that can dramatically alter the strength of the joint leading to premature failure. Nonlinear acousto-ultrasonic (AU) techniques have shown great potential for monitoring kissing bonds with piezoelectric sensors permanently installed on the structural joint, thus enabling online and in-situ inspection. This paper investigated the combined contact acoustic nonlinearity (CAN) and local damage resonance (LDR) effects in the presence of kissing bonds in adhesive joints. Experimental nonlinear AU tests showed the formation of LDR frequency down-shifts and “jumps” of the fundamental damage resonance in adhesively bonded aluminium joints, with the kissing bond located internally to the overlapping region between the two adherends. These results were supported by a theoretical model based on the solution of the nonlinear Duffing's equation, under the assumption that the debonded region is a damped nonlinear harmonic oscillator subject to harmonic forcing. The Harmonic Balance Method was used to solve the nonlinear differential problem, showing the generation of frequency down-shifts via the dependence of the ratio between the excitation and LDR frequencies with the amplitude of the fundamental damage resonance. Additionally, two-dimensional finite element simulations using a reduced order model based on the Craig-Bampton technique were carried out to support experimental AU tests for the the identification of the LDR frequency and the generation of nonlinear resonance effects. Good agreement between analytical, numerical, and experimental results revealed that a monitoring approach combining CAN and LDR is an extremely efficient and sensitive tool for ensuring integrity and safety of structural adhesive joints.
Non-invasive scanning techniques are vital for threat detection in areas of heavy human traffic to ensure civilian safety. Longer waves in the electromagnetic spectrum, such as millimetre waves and terahertz, have been successfully deployed in commercial personnel scanning systems. However, these waves suffer from lower image resolution due to their longer wavelengths.Infrared has a shorter wavelength compared to millimetre waves and terahertz. Infrared has a lower penetration potential compared to its counterparts but boosts higher image resolution due to its shorter wavelength. Machine learning techniques, i.e., principal component analysis, active contour, and Fuzzy-c, were applied to the infrared images to improve the visualization of concealed objects.Convolutional neural networks, i.e., ResNet-50, were explored as an automatic classifier for the presence of concealed objects. A transfer learning approach was applied to an ImageNet pre-trained ResNet-50 model. After preprocessing the IR images using Fuzzy-c, two models were trained, using 900 and 3082 images, respectively. Evaluating the models using a confusion matrix and receiver operating characteristic curve, an area-under-curve of 0.869 and 0.922 was obtained. An optimization procedure was used to determine the model threshold, resulting in a prediction error of 19.9% and 14.9%, respectively.
This paper presents a novel approach to improve the structural properties and damage tolerance of fibre-reinforced polymer composite joints via tufting using shape memory alloy (SMA) filaments. T-shaped joints made of carbon-epoxy composite material were reinforced with thin SMA (Ni-Ti nitinol) tufts. Experimental testing and finite element (FE) modelling reveal that the ultimate load, ultimate displacement and absorbed energy capacity of the T-joint increase with the areal density of SMA tufts. Improvements of over 110% in strength and 450% in absorbed energy capacity were achieved by SMA tufting. Under certain conditions, the shape memory effect of the tufts can be activated via electrical resistance heating to partially or completely close cracks in the T-joint caused by over-loading. The novel use of SMA tufts both to improve the resistance against cracking and to close cracks when they occur is a unique approach to improving the damage tolerance of composite structural joints.
This paper presents a study on the effectiveness of a convolutional neural network (CNN) in classifying infrared images for security scanning. Infrared thermography was explored as a non-invasive security scanner for stand-off and walk-through concealed object detection. Heat generated by human subjects radiates off the clothing surface, allowing detection by an infrared camera. However, infrared lacks in penetration capability compared to longer electromagnetic waves, leading to less obvious visuals on the clothing surface. ResNet-50 was used as the CNN model to automate the classification process of thermal images. The ImageNet database was used to pre-train the model, which was further fine-tuned using infrared images obtained from experiments. Four image pre-processing approaches were explored, i.e., raw infrared image, subject cropped region-of-interest (ROI) image, K-means, and Fuzzy-c clustered images. All these approaches were evaluated using the receiver operating characteristic curve on an internal holdout set, with an area-under-the-curve of 0.8923, 0.9256, 0.9485, and 0.9669 for the raw image, ROI cropped, K-means, and Fuzzy-c models, respectively. The CNN models trained using various image pre-processing approaches suggest that the prediction performance can be improved by the removal of non-decision relevant information and the visual highlighting of features.
Methods for determining crack tip opening displacement (CTOD) given in national and international standards are compared for steels with a range of strain hardening characteristics. Crack tip opening displacement measurements were made from single‐edge notched bend notches using a silicone rubber casting method. The finite element model produced good agreements with predictions of these CTOD measurements. The versatility of the finite element model enabled CTOD from the original crack tip and the 45° intercept method to be compared. The 45° CTOD generally underestimates the origi nal crack tip CTOD, and is less useful for conditions with stable crack extension. Apart from the high strain hardening material, CTOD calculated using BS 7448‐1, WES 1108 (JWES), and ASTM E1820 was slightly lower than the values determined from silicone measurements and modelling, which is conservative. ASTM E1820 gave the largest underestimation of CTOD, whilst BS 7448‐1 may be unsuitable for higher strain hardening steels, where the standard predicts higher CTOD than measured from the replica. JWES gives the most consistent estimation of CTOD for steels with a wide range of strain hardening values.
Crack tip opening displacement (CTOD) from national and international standards was shown to give different values. This paper investigates the feasibility of CTOD determined based on the concept of rigid rotational factor in single‐edge notched bend (SENB) specimens. Based on validated modelling methods, finite element (FE) models were simulated for crack ratios 0.3 ≤ a0/W ≤ 0.7 and yield‐to‐tensile ratio 0.44 ≤ σys/σuts ≤ 0.98. This covers cases of shallow to deeply cracked specimens and a wide range of strain hardening properties. CTOD obtained from the FE models was used as the basis of a newly implemented strain hardening corrected rotational factor, which considers the effects of crack tip blunting due to strain hardening, rp sh. An improved equation considering strain hardening was implemented based on the rp sh. The equation gives accurate estimation of CTOD from the FE models compared with the equation from BS 7448‐1, ASTM E1820, and WES 1180.
Penstocks have been used in the water industry for flow control since the Victorian expansion and consolidation of clean and waste water networks. However, the Victorians were the first to use grey cast iron (GCI) castings to manufacture large scale penstocks. Most of these ageing assets are still in operation, however engineering assessments are necessary to determine a structure’s fitness-for-service. Even today, penstocks in the sewer system tend to be made from GCI, due to ease of manufacturing, resistance to corrosion and cost. One characteristic property of grey cast iron is the graphite flake structure in the material, contributing to its low toughness, inconsistency in material strength and brittle behaviour, despite exhibiting slight hardening properties. Finite element analysis (FEA), is a numerical method which allows the analysis of complex structures by splitting it into finite parts and solving them with a computer processor. Despite the versatility of FEA, appropriate considerations and assumptions are necessary due to the difficulty to obtain data from inspection and unique material behaviour of GCI. The article shows concerns for an analysis of GCI penstocks using FEA, which extends into the application of fracture mechanics approaches for defect assessments.
Shape memory alloy (SMA) tufted composites have shown a significant improvement of the mechanical strength, fracture toughness, and delamination resistance of structural joints. This paper investigated the self-sensing functionality of SMA tufted carbon/epoxy composite T-joints to enable in-situ strain monitoring for the detection of low-velocity impacts. Indeed, large deformations in the tufted composite due to impacts caused abrupt changes in electrical resistance of SMA filaments, which were used to trigger the detection system. An Arduino Mega controller was programmed to simultaneously extract and process real-time electrical resistance recordings from SMA tufts during impact tests conducted at 5 J and 10 J. Experimental results showed that the proposed SMA-enabled detection system can capture accurately the time of the impact and localise the delamination onset, thus demonstrating the truly multifunctional capabilities of proposed SMA tufted composites.
In ductile materials the fracture toughness is usually characterised by a tearing resistance curve, or R-curve, plotting the fracture toughness in terms of J or CTOD against crack extension. Recent research has evaluated the methods to determine CTOD in engineering alloys with a wide range of yield to tensile (Y/T) ratios for single point CTOD. This work develops the investigation into R-curves, and reviews the assumptions about SENB specimens deforming under rigid rotation, the evaluation of CTOD from J for R-curves, and the nature of tearing initiation in low Y/T ratio stainless steel, from comparisons against a series of silicone replicas cast from the SENB specimen notch during fracture toughness tests. For CTOD R-curves, the methods based on CTOD from J in ISO 12135 and ASTM E1820 gave lower and less accurate R-curves than the rigid rotation methods in BS 7448-4 and WES 1108. However, the accuracy of the BS 7448-4 formula varied for the different strain hardening materials, and overestimated the R-curves in the low tensile ratio stainless steel. Investigations into the effect of the assumption about rigid rotation in different strain hardening materials led to a rotational factor function of tensile ratio, rp sh, to be developed from numerical modelling. When this function was substituted into standard equations in place of the fixed value of rp an improvement in the accuracy of BS 7448-4 R-curves compared to replica measurements was seen for the range of strain hardening investigated, but it did not significantly improve the accuracy of the WES 1108 formula, which accounts for strain hardening in other parameters. A combination of the elastic CTOD part of the WES 1108 formula, with the plastic CTOD incorporating the modified rotational factor, was concluded to offer the optimum method to determine CTOD R-curves for a range of strain hardening materials.
Whilst superseded by other materials, there are many instances of engineering structures in use today that are formed of grey cast iron. These aging assets need to be assessed for their abilities to continue to function, and to predict performance in the event of engineering works being carried out on the asset, or nearby. Grey cast iron does not exhibit an obvious elastic regime when loaded in tension and is often classified in terms of minimum guaranteed tensile strength. Grey cast irons typically fail in brittle cleavage with a strain limit of
According to some standards, fracture toughness tests loaded under bending are assumed to deform around a fixed plastic hinge point within the ligament ahead of the notch tip. The rotation factor,rp, defines the proportion of the ligament ahead of the crack tip to where this hinge point is located. In this paper, the concept of an SENB specimen bending about a fixed rotational point under loading was investigated. Experimental SENB tests were carried out on three different strain hardening steels, and the geometrical point of rotation was determined experimentally throughout the tests using a double clip gauge and the similar triangles principle. The experimental results were then used to develop and validate a series of different strain hardening property numerical models. By extracting the rotational factor from the different strain hardening property models, a relationship between strain hardening and a strain hardening corrected rotational factor, rp sh was established. This corrected rotational factor function was used to propose an improved equation for the calculation of CTOD and CTOD R-curves, which gave good estimations of CTOD when compared to values measured experimentally from sections through silicone replicas of the specimen crack-tip. The improved R-curve equation will be proposed for future amendments to the ISO 12135 standard.
Additional publications
Khor W, Moore PL, Pisarski HG, Brown CJ (2018) A modified approach to the rigid rotation plastic hinge point in SENB specimens in different strain hardening alloys and crack depth. In: BSI, ed. ISE/101/04 Toughness testing annual meeting.
Khor W, Moore PL, Pisarski HG, Brown CJ (2018) Determination of the rigid rotation plastic hinge point in SENB specimens in different strain hardening steels. In: Physics Io, ed. Modern Practice in Stress and Vibration Analysis. Institute of Physics, Clare College, Cambridge, UK.
Khor W (2018) Crack tip opening displacement (CTOD) in single edge notched bend (SEN(B)). Dept of Mechanical Aerospace and Civil Engineering Brunel University London, Brunel University London, http://bura.brunel.ac.uk/handle/2438/16198
Khor, W. (2016) Measurement and prediction of CTOD in austenitic stainless steel. In National Structural Integrity Research Centre Conference 2016. Cambridge.
Khor, W. (2015) Validation of Standardized CTOD Equations. In National Structural Integrity Research Centre Conference 2015. Cambridge.
Khor, W. & Pisarski, H. (2015) Comparison of CTOD estimation procedures with physical measurements. In International Institute of Welding Annual Assembly.