DECRON: Development of eco-friendly ironmaking processes based on GPU-enhanced DEM modelling
Start date
November 2017End date
October 2019Overview
DECRON aims to identify critical material and process attributes such as process conditions, materials properties and system designs, that dominate the burden distribution and to develop process strategies to achieve controlled burden distribution in blast furnaces.
The following research objectives will be explored:
- Experimental and numerical investigation of size-induced segregation during charging of coke and sinter into a blast furnace.
- The effect of the gas flow on the formation and microstructure of the burden, which mimics the real process condition with blast being continuously injected from the lower part of the furnace during the burden formation.
Funding amount
$195,454
Funders
DECRON is an EC H2020 project funded through the Marie Curie Intra-European Fellowship (IEF) in partnership with the University of Surrey.
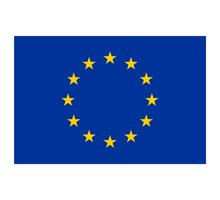
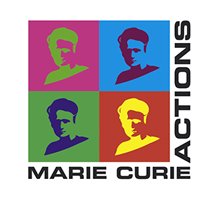
Blast furnace operation
Blast furnaces are widely used in the iron-making industry to produce iron and other base metals. Using blast furnaces, raw feed materials such as fuel, ore, and limestone are continuously charged onto the top of a blast furnace, while air is blown into the lower section of the furnace through the tuyere, so that the chemical reactions take place throughout the furnace as the feed materials move downward.
The process
This process produces molten metal and slag phases that are extracted from the bottom of the blast furnace. It is a typical multi-phase counter-current exchange process involving the downward flow of the solid feed materials and melted metals in the liquid phase, and an up flow of hot, carbon monoxide-rich combustion gases.
Energy consumption
The running of blast furnaces consumes 60 per cent energy of the whole steel industry and is responsible for 90 per cent CO2 emission to the environment from a typical steel plant. In order to reduce the energy consumption and CO2 emissions, the development of a thorough scientific understanding of the operation of blast furnaces and of science-based predictive tools for optimizing the operation of blast furnaces are urgently needed. Since blast furnaces are operated at elevated temperatures (1100 Celsius) and at large scales (4000m3, up to 400 tonnes per hour), conventional visualisation and monitoring techniques are incapable for such a challenging process. In particular, it is difficult, even impossible, to experimentally explore what is happening inside. Due to the complex physical process obtaining empirical solutions is also a non-trivial task.
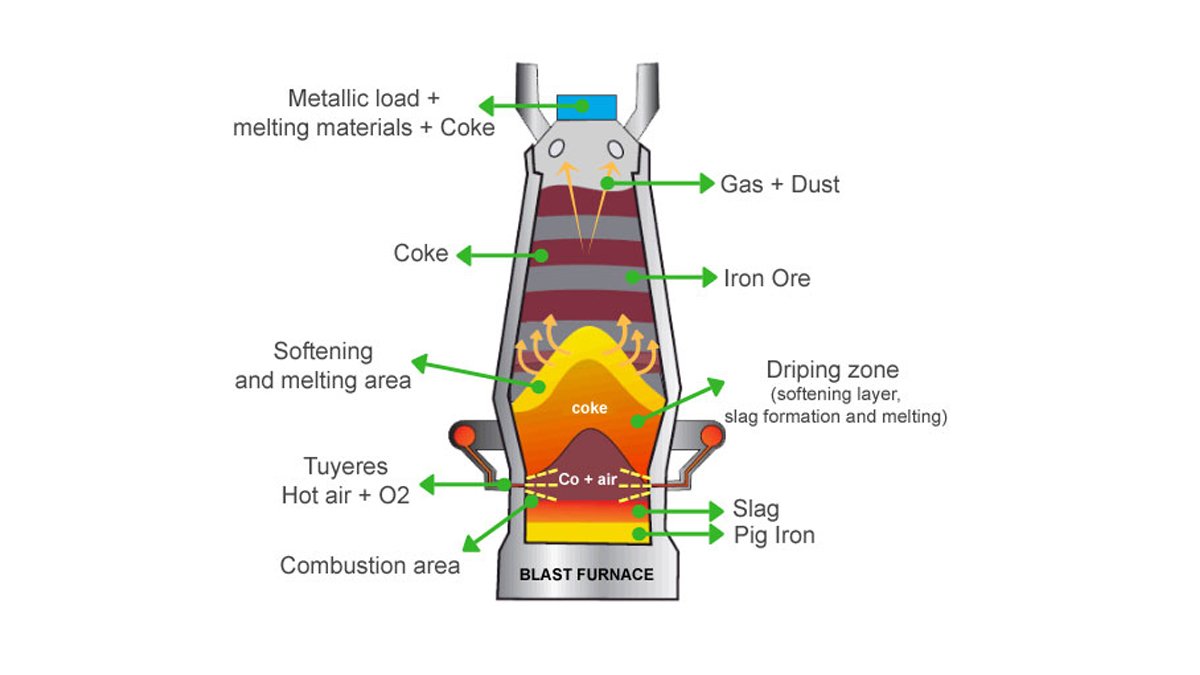
Figure one: The blast furnace is powered by hot air and oxygen that enters the blast furnace through the tuyeres to form a combustion zone that heats the layers of coke and iron ore. The heated iron ore softens, melts and drips under gravity to collect at the bottom of the blast furnace for further processing. The blast furnace is continuously charged with coke and iron ore by a hopper at the top of the blast furnace.
Blast furnace charging
The permeability of burden distribution is influenced by the charging process and the geometric properties of the feed particles. Therefore, a thorough understanding of the behaviors of burden formation and descent is critical in developing appropriate strategies for energy-efficient blast furnace operations.
The furnace should be charged in such a way that the coarse and fine particles are distributed appropriately on the burden surface to control the burden distribution, so that the gas utilisation of the furnace can reach the optimal and the furnace can be operated in a more energy-efficient manner. Ideally, in order to increase gas utilisation, the sinter of small sizes should be discharged in the periphery area for protecting the lining and preventing excessive heat losses, and particles of large sizes in the central area to form a strong central gas flow.
In addition, the mean size of the sinter should gradually increase from the periphery to the center in order to attain an increasing gas distribution from the periphery area to the central area (a weak gas flow at the wall area and a strong gas flow in the central line of furnace). Creating a thin iron-bearing material layer at the periphery with a small quantity of small size sinters leads to a thin cohesive zone at the lower part of furnace and a reduced pressure drop of whole furnace.
Although the benefit of the controlled burden distribution (i.e. burden of a controlled microstructure achieved with an optimal distribution of feed materials) has been anticipated, it is a challenging task to realise it in practice. Hence, only the height of the burden layer is currently controlled in the blast furnace through the control of the mass flow rate in the discharging system. Therefore, it is of great scientific and commercial interest to study the burden distributions and packing structure accurately.
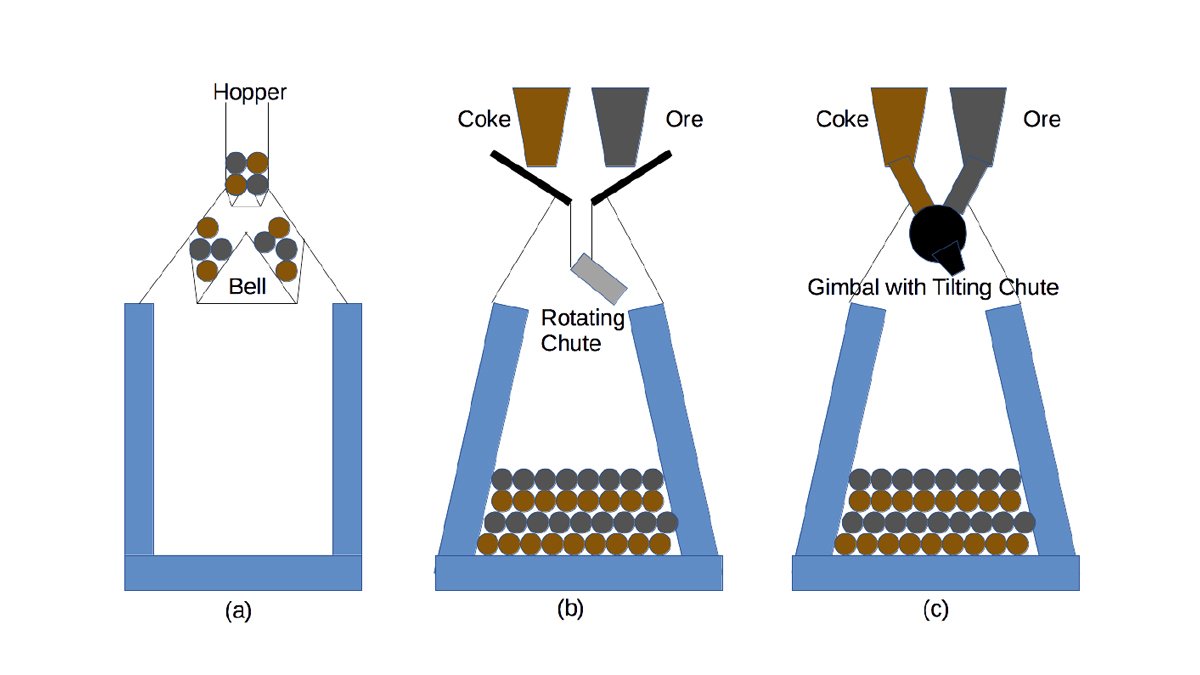
Figure two: Depicting the various charging systems for blast furnaces, we are considering in this project. Of the first charging systems developed was the single bell systems that later developed into the double bell systems as depicted in figure two (a). This was followed by the bell-less top charging systems with parallel hoppers as depicted in figure two (b). This allows for near continuous blast furnace charging that was lately further refined into gimbal charging systems by Siemens-VAI as depicted in figure two (c).
Team
Project lead
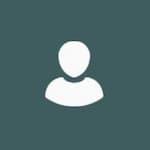
Dr Nicolin Govender
Principal investigator
Project supervisor
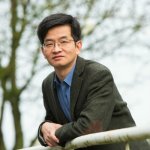
Outputs
Numerical investigation into the effect of angular particle shape on blast furnace burden topography and percolation using a GPU solved discrete element model.
The reduction of ore bearing granular materials to molten state using a blast furnace is an energy and cost intensive task. The obvious correlation between energy usage and the furnace operation is in:
- Ease of uniform percolation of the packed-bed with interstitial gas flow which speeds up heat and mass transfer
- Provision of greater surface area per unit bed volume for combustion due to more uniform gas percolation.
The burden topography and packing density affects the stability of the burden, permeability of gas flow as well as the efficiency of the heat transfer. Therefore a fundamental understanding on the influence and interaction of coke and ore particles on the burden topography and packing density is essential.
In this paper we analyse the effect of particle shape with and without angularity on the charge distribution of the coke and ore inside a bell-less blast furnace using discrete element method (DEM). Computing the DEM on graphical processor units (GPU) allows us to model polyhedral particle shapes with volume overlap contact models, instead of conventional approaches to accommodate shape effects that includes modifying the rolling resistance when modelling with spherical particles.
Burden topography
We found that shape polydispersity mainly influenced the topography of the burden, i.e. macroscopic particle transport of particles within the BF, whereas the size polydispersity mainly influenced the inter-layer percolation, i.e. localized particle diffusion. Particle shape therefore has a macroscopic effect on the spatial packing density due to particle transport, whereas size polydispersity influences a more local spatial packing density. We found that spherical particles resulted in a burden topography that had a wave like pattern with a thin coke center. In addition, the iron ore layers tend to be semi-circle shaped slanting downwards towards the center of the BF, with little additional variations in the axial direction.
The burden topography for the polyhedral shaped particle system resulted in more moderate wave like patterns, with one particle set that ended with a definite coke core pushing through the burden surface. The polyhedral ore layers are more crescent shaped due to their sinking into the coke layers result in semi-circle shaped layers, while a central coke push distorts the semi-circle shaped layers into crescent shaped layers. This evidently resulted in a larger concentration of coke at the center and walls in the radial direction, with thin uniformly distributed coke layers along the radial direction away from the wall and middle.
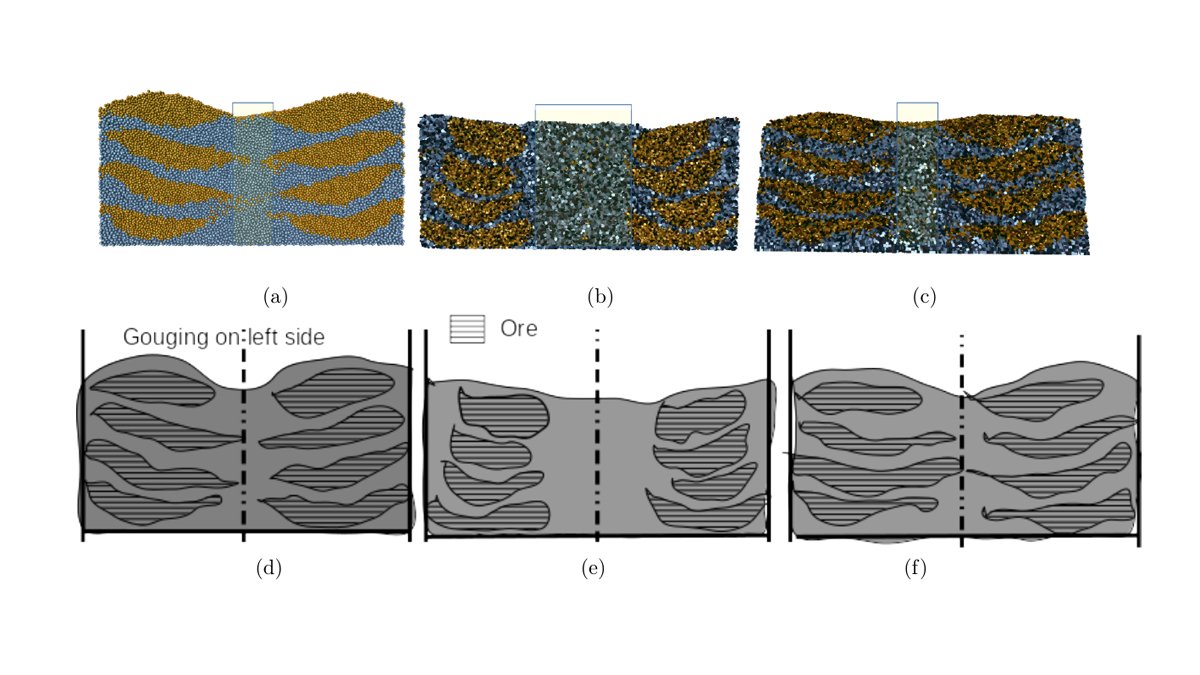
Figure eight: Depicting the burden topography obtained from our simulation software after eight layers of charging, for the three particle sets. Figure eight (a) depicts the spherical particles and figure eight (b) and (c) respectively set one polyhedral and set two polyhedral particle systems. The topography is coloured by material and figure eight (d) - (f) is a sketch of the ore distribution.
Findings
The findings from the first year of this project is that the common approach of modelling spheres with rolling friction to account for the shape may be insufficient to account for particle shape complexity in a blast furnace, which is significant as it seems particle shape has a noteworthy influence on the burden characteristics.
Conferences
- Invited talk, GTC 2018 San Jose, USA
- Comminution 2018, Cape Town, South Africa
- ESCO 2018, Pilzen, Czech Republic.
Papers
- Hopper flow of irregularly shaped particles (non-convex polyhedra): GPU-based DEM simulation and experimental validation Chemical Engineering Science Volume 188, 2018, Pages 34-51
- Large-scale GPU based DEM modeling of mixing using irregularly shaped particles, Advanced Powder Technology Volume 29, Issue 10, 2018, Pages 2476-2490
- Effect of particle shape in grinding mills using a GPU based DEM code, Minerals Engineering Volume 129, 2018, Pages 71-84.
Training
University of Surrey: Introduction to GPU computing
9 November 2018
The course covers the basics of scientific computing and how to write code which gives the best possible performance. An introduction to computer hardware. How to program for the GPU and identify algorithms that can be sped up on the GPU using C++ and Linux.
Training on blaze-DEM software
13 November 2018
This course introduces the software used and developed within DECRON to the university. Attendees will learn how to use the software to do DEMs simulations and how the input parameters affect GPU performance. The skills obtained in the training will help in understanding the structure of the code.