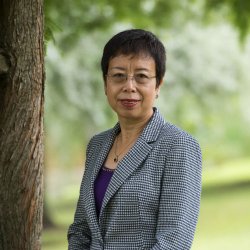
Dr Lian Liu
About
Biography
Dr. Lian Liu joined the University of Surrey in May 2016 at the Department of Chemical and Process Engineering. Dr. Liu obtained her PhD from the University of Queensland in Australia in 1991 and worked in Carrier Transicold in Singapore for three years after her PhD. She then moved back to the University of Queensland and spent most of her academic career in the same University before moving to the University of Surrey.
Dr. Liu's research expertise is in particle technology and formulations for health applications. Her expertise in particle technology ranging from comminution (particle breakage process) to granulation process (particle size enlargement process) as well as bulk powder flow and compaction and crystallisation. Her expertise on formulations includes novel topical formulations for anti-ageing and wounds healing. Dr. Liu also has a keen interest in advanced materials including fire retardant composite materials. She has worked with a wide range of industries such as minerals, agricultural and pharmaceutical and biotech companies.
Affiliations and memberships
ResearchResearch interests
- Milling and grinding - Characterization and modeling
- Powder flow and compaction in pharmaceutical formulation engineering
- Granulation and crystallization process modelling
- Topical formulations for anti-ageing and wounds healing
- Flame retardant epoxy composites
Research projects
Novel formulations for effective and stable skin delivery of anti-aging nutrientsThis project will look at the new formulations for effective delivery of anti-aging nutrient to the skin
A novel nanoemulsion for optimised wound recovery: A topical antibiotic-free approachThis project looks into novel formulations in nano emulsion form for topical application for enhanced wounds healing with antibiotics-free approach. This project is sponsored through Innovate UK's young scholar secondment program with host company Phytoceuticals Ltd.
Research collaborations
Phytoceutical limited
University of Queensland
Nanjing Tech University
Research interests
- Milling and grinding - Characterization and modeling
- Powder flow and compaction in pharmaceutical formulation engineering
- Granulation and crystallization process modelling
- Topical formulations for anti-ageing and wounds healing
- Flame retardant epoxy composites
Research projects
This project will look at the new formulations for effective delivery of anti-aging nutrient to the skin
This project looks into novel formulations in nano emulsion form for topical application for enhanced wounds healing with antibiotics-free approach. This project is sponsored through Innovate UK's young scholar secondment program with host company Phytoceuticals Ltd.
Research collaborations
Phytoceutical limited
University of Queensland
Nanjing Tech University
Publications
A comprehensive understanding of the dynamic processes in sonochemical reactions is essential for providing theoretical support and practical guidance in ultrasonic industrial applications. The influence of acoustic factors (frequency and pressure amplitude) and external parameters (liquid height) on sonochemical activity were researched. The phenomenon of sonoluminescence (SL), sonochemiluminescence (SCL) and potassium iodide (KI) dosimetry were investigated at 114 different settings. The settings included electrical loading-power of 10, 20, 30, and 40 W, 10 frequencies ranging from 22 to 2000 kHz, and reactor volumes of 200, 300, and 400 ml. A new area selection image processing technique was used to conduct a systematically quantitative analysis of SL and SCL across a broader frequency range. The sonochemical activity could be categorised into three zones based on the ultrasonic frequency (22 to 2000 kHz): f < 200 kHz, 200 kHz ≤ f ≤ 1000, and 1000 kHz ≤ f ≤ 2000 kHz. The Pearson and Spearman correlation coefficients were used to discuss the correlation between SL, SCL, reactive oxidant species (ROS) and hydrogen peroxide yields. The findings indicate that the influence of liquid height on cavitation activity within the reactor is mostly manifested in the power density. The ultrasonic oxidation capacity (as indicated by the yield of ROS) exhibits a strong positive relationship with SL intensity. A divergence of correlation between SL and I3- yield was observed. There was a lack of correlation between sonochemical activities (e.g. SCL and ROS yield). The poor correlation highlighted the importance of consideration of chemical mechanisms and reaction locations with respect to the collapsing bubble.
A systematic study on the batch cooling sonocrystallization of p-aminobenzoic acid (pABA) in ethanol was investigated under different ultrasound frequencies (22 kHz to 1 MHz), powers (1-40 W), and sonication times (1.73-31.85 min), with the crystal length, width, aspect ratio (AR), and induction time recorded for each experiment. These measured variables were related to sonoluminescence (SL) values to quantify the cavitation activity. For the first time, the crystal length, aspect ratio, and induction time were observed to decrease with the logarithm of integrated SL intensity per acoustic cycle, irrespective of frequency. No such correlations were observed with power. 200 kHz ultrasound produced crystals with the lowest mean aspect ratio of 5.17, a 68% reduction from the silent case. However, 22 kHz was the most efficient frequency at reducing the induction time (by 95%), crystal length (by 76%), width (by 67%), and aspect ratio (by 26%) at the lowest applied power of 1 W, while increasing the power had no further significant impact. Applying 22 kHz ultrasound bursts (1-10 min duration) before nucleation reduced the induction time by up to 75%, with burst duration and power (5 and 10 W) having no observable effect on the crystal shapes. When applying ultrasound to crystals in a slurry, fragmentation was observed with only 22 kHz ultrasound. It is hypothesized that the mechanism behind sonication under 22 kHz is related to both crystal nucleation and fragmentation caused by unstable, transient cavitation. This differs from the mechanism for 200 kHz and 1 MHz where the cavitation is mainly stable and produces a weaker physical force that does not cause severe crystal fragmentation but enhances crystal nucleation.
In this study, the bed temperature profile of a conical/plasma fluidized bed without a distributor was studied. The same reactor was also used for growing diamond by chemical vapour deposition. It was found that the fluidized bed quenches the plasma gas quite significantly. The bed temperature increases with both the plasma gas flow rate and the plasma input power. A lateral temperature difference from the centre of the bed to the wall exists due to heat loss through the wall. The temperature profiles obtained are suitable for controlling of bed quenching conditions in particle processing and synthesis. The conical/plasma fluidized bed with a distributor on top of the plasma was then applied to diamond synthesis from a gas phase using a distribution between the bed and the plasma. The deposition mainly occurred in the plasma tail fame. Both the scanning electron micrographs and Raman spectra show the existence of diamond on seed particle surfaces, but with a rather low nucleation density. The limitations of the d.c. plasma fluidized bed system are discussed and modifications to the reactor are recommended.
Wet granule breakage can occur in the granulation process, particularly in granulators with high agitation forces, such as high-shear mixers. In this paper, the granule breakage is studied in a breakage only high-shear mixer. Granule pellets made from different formulations with precisely controlled porosity and binder saturation were placed in a high-shear mixer in which the bulk medium is a non-granulating cohesive sand mixture. After subjecting the pellets to different mixing time in the granulator, the numbers of whole pellets without breakage are counted and taken as a measure of granule breakage. The experimental results showed that binder saturation, binder viscosity and surface tension as well as the primary powder size have significant influence on granule breakage behaviour. It is postulated that granule breakage is closely related to the granule yield strength, which can be calculated from a simple equation which includes both the capillary and viscous force of the liquid bridges in the granule. The Stokes deformation number calculated from the impact velocity and the granule dynamic strength gives a good prediction of whether the granule of certain formulation will break or not The model is completely based on the physical properties of the formulations such as binder viscosity, surface tension, binder saturation, granule porosity and particle size as well as particle shape. (C) 2008 Elsevier B.V. All rights reserved.
[Display omitted] ► Nickel laterite pellets with controlled mass, porosity and binder were made. ► The mechanical strength of the pellets was measured and leaching test was conducted. ► Water-bound pellets are stronger than sulphuric acid solution bound pellets. ► The time to disintegration during leaching test increases with pellet strength. ► More than 70% of Ni is recovered during leaching for air-dried water-bound pellets. Nickel laterite pellets with controlled mass, porosity and binder were made by using a pellet press. Both water and sulphuric acid solution were used as binders. The wet pellets were then dried at different conditions and their mechanical strength was measured. Leaching tests were also conducted on single pellet with irrigation of sulphuric acid solution from the top of the pellet. The leached out solutions were collected and nickel recoveries were analysed. The time taken for the pellets to disintegrate during leaching test was also recorded. It was found that the mechanical strength of the pellets was directly related to their dryness, with completely dried pellets having much higher strength. The dry pellet strength was found to increase with increasing binder content and decreasing pellet porosity. The time taken for the pellets to disintegrate during leaching test increased with increasing pellet strength. In comparison to sulphuric acid solution-bound pellets at the same condition, water-bound pellets exhibited higher mechanical strength. Although the nickel leaching rate for water-bound pellets was low at the beginning of the leaching test, the pellets lasted for more than 200h without disintegration, with 70% of nickel recovered.
Powder flowability is one of the key parameters in the pharmaceutical tabletting process. The flowability is affected by both the particles' properties and the tabletting equipment characteristics. Although it is generally accepted that powder flowability increases with an increase in particle size, quantitative studies and comprehensive theoretical insights into the particle property effects are still lacking. In this paper, ibuprofen, a non-steroidal drug widely used as an anti-inflammatory analgesic was chosen as a model material to assess the effect of particle properties on its flowability. Ibuprofen typically has a needle shaped morphology. The flowability of ibuprofen size fractions was studied in detail using two flow measurement methods. The separated fractions were also compared to magnesium stearate lubricated ibuprofen and its size fractions. The experimental results showed that powder flowability is significantly affected by both the particle size and size distribution. The finest size fraction that is separated from the bulk ibuprofen powder flows better than the bulk powder. For powders with narrow size distributions, the flowability increases significantly with the increase in particle size. In addition, admixing magnesium stearate to ibuprofen not only increases the flow function of the powder, but also reduces the internal friction angle. A theoretical analysis based on the limiting tensile strength of the powder bed was carried out and the flow conditions for particles of different size and shape were developed. (C) 2008 Elsevier B.V. All rights reserved.
Wet granulation is a complex process with several competing physical phenomena occurring in the granulator, which ultimately leads to the formation of the granules. These phenomena are divided into three groups of rate processes: (1) wetting, nucleation, and binder distribution, (2) consolidation and growth, and (3) attrition and breakage. The physical phenomena that control these processes are the same, independent of the type of granulation used. Granule size, size distribution, and porosity, as well as many other key product attributes are controlled by the balance of the rate processes that occur in the granulator. This chapter examines the underlying physics behind each rate process, defines the controlling formulation properties and process parameters for each rate process, uses regime maps to establish the operating regime for the granulator; and provides quantitative relationships to predict the effect of changing operating parameters and formulation properties. This chapter focuses on developments in the past decade where substantial advances in quantitative understanding of granulation rate processes have been made with an emphasis on work done by our group at The University of Queensland and The University of Newcastle. The philosophy of this chapter is to characterize process parameters in generic terms that are equipment independent (collision velocity, powder surface flux, etc.).
Two steps are usually involved in producing high impact polypropylene copolymer in a continuous process. The first is to polymerize propylene using Ziegler–Natta type or more recently metallocene catalyst, and the second is to add ethylene–propylene rubber (EPR). A narrow residence time distribution (RTD) of polymer particles is an important process design and operational target in this process. The broadening of RTD will lead to a widening of copolymer composition distribution in which results in inferior product properties. There are several techniques to obtain a narrower RTD, including by controlling size of particles leaving a well-mixed reactor. In this paper, a dynamic population balance model to track polymer particle age and size is presented. The model is applied to a well-mixed slurry reactor linked to a classifier. Polymer particle growth kinetics including catalyst deactivation with particle age are incorporated. The model agrees well with steady-state analytical solutions and process data for particle age and catalyst efficiency. The classifier acts to significantly narrow particle age distribution. However, the system is very sensitive to small change in feed catalyst size, catalyst deactivation can cause build up of small polymer particles trapped in the system if the feed catalyst size is too low. As a ‘soft sensor’, the RTD information from the validated model provides valuable insight for operational support. Further applications include strategies of reactor control design and optimization of grade transition policy.
This study investigates the flow properties of binary mixtures of both commercial ibuprofen and reprocessed ibuprofen through high shear milling with lactose powders. Ibuprofen is recrystallized in a 30% water-ethanol mixture before high shear wet milling (HSWM). In-situ Process Analytical Techniques (PAT) (Labmax (R)) is used to study the HSWM process dynamics, with particle size measured by a Lasentec Focused Beam Reflectance Measurement, FBRM (R). The flow properties of the binary mixtures of the different ibuprofen particles and its binary mixtures with lactose were measured using a Schulze (R) RST-XS ring shear tester. Results show that the morphology of ibuprofen was changed from needle to hexagonal like crystals during recrystallization and crystal size was reduced dramatically by HSWM for 1 h. The flowability of milled ibuprofen powders is reduced significantly due to its reduced size and change of surface morphology. Mixing the HSWM ibuprofen powders with lactose enhanced its flow properties. However, the increase of the mixture flowability for HSWM ibuprofen is less significant in comparison to the binary mixtures of lactose with commercial ibuprofen. (C) 2012 Published by Elsevier B.V. on behalf of The Society of Powder Technology Japan. All rights reserved.
Wet granule breakage is a significant mechanism, particularly in high shear mixer granulation. This paper presents a study of the wet breakage mechanism using a Breakage Only Granulator. Granules with varying powder and liquid binder properties were created using single drop nucleation. These granules were inserted in a Breakage Only Granulator, a high shear mixer granulator with non-granulating cohesive sand as the bulk medium. Two different impellers were used at impeller speeds of 500 and 750 rpm. An 11 degrees beveled edge impeller was used to create both impact and shear in the granulator, and a flat plate impeller was used to minimize impact and maximize shear in the granulator. The fraction of granules which broke during the granulation process was used as a measure of granule breakage using mean dynamic peak flow stresses measured in unconfined uni-axial compression tests. Results for the beveled edge impeller blade show increasing breakage with increasing Stokes deformation number. Significant breakage was observed at high Stokes deformation number. Increasing impeller speed increased the magnitude of breakage. The Stokes deformations number appears to be a reasonable predictor for granule breakage within the granulator. Results for the flat plate impeller show very little breakage at 500 rpm, and significant breakage for only one formulation at 750 rpm. This suggests that either impact is dominant over shear for breakage within the granulator, or that the two impeller designs give substantially different collision velocities in the granulator. The impeller speed type and shape have a profound effect on granule breakage in high shear mixer granulators. (C) 2010 Published by Elsevier Ltd.
The mechanical properties of a range of agglomerates and particulate coatings have been measured using a nanoindenter. The effect of formulation properties such as powder and binder properties on coating hardness is described. An attempt is also made to measure the fracture hardness with the nanoindenter. The use of indentation technology to measure fundamental agglomerate properties is critically analysed. Based on the indentation measurements and standard attrition test results, the coating hardness is found closely related to the attrition rate under standard conditions and can be used to screen different powder/binder formulations. Les propriétés mécaniques d'une gamme d'agglomérats et de revêtements particulaires ont été mesurées à l'aide d'un 'nanoindenteur'. L'effet des propriétés de formulation telles que les propriétés de la poudre et du liant sur la dureté du revêtement est décrit. Des tentatives de mesure de la dureté de la fracture avec le 'nanoindenteur' ont été effectuées. L'utilisation de cette technique de pénétration pour mesurer l'aptitude fondamentale à l'agglomération est débattue. Des mesures de pénétration et les résultats des tests standards d'attrition ont montré que la dureté du revêtement est étroitement liée au taux d'attrition sous les conditions standards. Celle-ci peut aussi être utilisée pour sélectionner différentes formulation poudre/liant.
In this work, a nucleation model that includes nuclei breakage/fragmentation is proposed. The model is based on the nucleation model of Hapgood and the Stokes deformation number calculated from the granule dynamic yield strength from the previously reported granule breakage work. It is proposed that breakage or fragmentation of primary nuclei from binder spray will occur if the Stokes deformation number exceeds a certain critical number. In the case where breakage occurs the model for secondary nuclei size distribution is proposed. To validate the model, the characteristics of the primary nuclei formed from nickel laterite ores with diluted sulphuric solutions as a binder were investigated. The nuclei were produced by dropping the binder solution onto a stationary powder bed. The mechanical integrity of the primary nuclei formed, the relationship between the nuclei diameter and binder drop diameter were studied. The Stokes deformation numbers for nickel laterite powders with different particle size in a lab scale drum granulator were calculated and the nuclei size distributions with different nickel laterite feed powders are predicted.
Dry granulation is commonly used in the pharmaceutical industry for compressing heat and moisture sensitive feed materials into compacts, subsequently followed by milling. Population balance models (PBMs) are often used to explore the effects of milling conditions on the granule size distribution (GSD) but limited studies have investigated the effects of the feed material and ribbon properties on the resulting GSD. In this work, a variety of feed materials and ribbons with different mechanical properties were used to validate a mass-based bi-modal breakage function developed in a previous study (Olaleye et al., 2019). Ribbon like tablets (referred to as ribblets) with a range of precisely controlled porosities were produced using an Instron machine and pharmaceutical excipients including the microcrystalline cellulose MCC 101, MCC DG and a DCPA/MCC mixture. Roll compacted ribbons were also produced using MCC 102 and MCC DG excipients. The ribblets and ribbons were milled in an impact-dominated cutting mill and PBM parameters were obtained from the ribblet milling data. Mechanistic models related to the feed ribbon property were then developed. It was found that the PBM with the mass-based bi-modal breakage function can accurately predict the GSDs of both the milled ribblets and roll compacted ribbons. The model developed was successfully linked to ribbon properties such as porosity for the first time and the model parameter a that reflects the fines mode in the bi-modal breakage function increased linearly with ribblet porosity. This work demonstrates the versatility of the developed PBM and provides a systematic approach for describing the ribbon milling process.
A mill model structure based on the population mass balance framework incorporating breakage characteristics, slurry and solids transport, product classification and discharge and energy consumption was reported in XXVII IMPC and named the Generic Tumbling Mill Model Structure Version I (GTMMS I). In this work, a new 4D (four dimensional) appearance function sub-model based on the experimental results of the JK Rotary Breakage Tester (JK RBT) was developed to describe the breakage characteristics and was applied to this new model structure. The newly developed 4D appearance function model has fewer fitting parameters and is more generic in nature. Most importantly, it is applicable to both high and low energy impact breakage. It is therefore much more versatile in comparison to the existing JKMRC t10-tn appearance function and the size-dependant JK M-p-q t10-tn appearance function. In addition, the Discrete Element Method (DEM) energy distribution model was integrated into the new model structure. With DEM results providing energy distribution information inside the mill directly, the selection function and the back-calculation method used in the existing JKSimMet modelling method are not needed in this model structure. With the above two revolutionary innovations, the previous model structure was upgraded to the Generic Tumbling Mill Model Structure Version II (GTMMS II). Furthermore, the new model structure is dynamic in nature with time-stepping technique for non-steady-state simulation. A case of the dynamic grinding of a SAG mill was studied to validate the GTMMS II. The model simulation results agreed well with the plant data. With the newly developed 4D appearance function model, the incorporation of DEM energy distribution and transport function, the Generic Tumbling Mill Model Structure Version II (GTMMS II) is an important step forward towards mechanistic modelling of tumbling mills.
Dry granulation through roll compaction followed by milling is a widely used pharmaceutical process. The material properties of powders and the roll compaction process conditions affect the strength of ribbons, and subsequently the granule size distribution (GSD). Accurate prediction of the granule size distribution from milling of ribbons with different properties is essential for ensuring tablet quality in the final compaction stage. In this study, MCC, PH-102 ribbons with precisely controlled porosities were produced and milled in a cutting mill and granule size distribution was analysed using QicPic. A population balance model with a new breakage function based on the Weibull function was developed to model the ribbon milling process. Eight model parameters were initially obtained for each ribbon porosity and very good agreement between the model and experimental results was obtained. Sensitivity analysis was then performed and thus reduced the number of model parameters that changed with ribbon porosity to two in the breakage function. The refined model was able to predict the granule size distribution both within and outside the experimental boundaries. It was shown that the model developed in this study has a great potential for predicting granule properties and therefore the optimisation of the dry granulation process.
•Breakup regime of superheated liquid jet under depressurized release is examined.•Both thermal nonequilibrium and mechanical forces are involved as driving effects.•The coupling regime of the two driving effects during depressurization is explored.•Non-flashing, partially flashing, and fully flashing breakup modes are identified.•The interaction of the two driving effects is quantified by dimensionless analysis. Superheated liquid jets disintegrate into numerous droplets when released into the ambient with lower saturated pressure, driven by thermal nonequilibrium induced flashing and the accompanying mechanical forces. Such a phenomenon facilitates fuel atomization in energy utilization while posing a serious threat during accidental releases. In this work, the breakup and droplet formation of superheated liquid jets under depressurized releases were investigated with an experimental 20 L tank. A high-speed camera was utilized to characterize breakup behaviors. The interaction between thermodynamic and mechanical effects during depressurization was discussed based on linear stability analysis and bubble dynamics. Furthermore, the quantitative relationship between the two driving effects under different conditions was established using dimensionless and multiple regression analyses. Results show that the thermodynamic effect increases with the decreased mechanical effect during depressurization because of the increased energy of bubble burst, regardless of the external or internal flashing regime. Non-flashing, partially flashing, and fully flashing breakup modes are identified. The dimensionless and multiple regression analyses show that in addition to thermodynamic (Ja, ρv/ρl, Rp, and ηp) and mechanical (Wev and Oh) effects, the inhibition induced by the cooling effect (Pr and Ec) should not be overlooked. The quantitative expression among them agrees well with experimental data with R2=0.976.
Pursuing efficient and low-cost catalysts for the sluggish oxygen evolution reaction (OER) is imperative for the large-scale deployment of promising electrochemical technologies such as water splitting and CO₂ electrochemical reduction. The earth-abundant perovskite catalysts based on LaNiO₃-δ show promise in OER catalysis because of their relatively low cost and their optimal electronic structure but suffer from low electrode-area normalized activity. In this work, we partially substituted La with Sr and Ni with Fe to enable a remarkably high OER activity with an ultra-low overpotential of 374 ± 3 mV vs RHE at a current density of 10 mA cm−2 normalized by electrode geometric area. This performance even surpasses the performance of benchmark RuO2. Our results show that Sr could promote OER-active sites including Ni(III), O2−₂/O−, and optimal Ni/Fe ratios, which significantly improve the surface intrinsic activity at the perovskite surface. Therefore, this work not only developed a highly efficient earth-abundant catalyst towards OER, but also demonstrated the effective modulation of catalyst surface interactions through A-site doping for perovskite oxides for key applications such as water splitting, CO₂ electrochemical reduction and N₂ electrochemical fixations.
Possessing the advantages of both polymeric membranes and the specific inorganic nanoparticles or nanotubes, mixed matrix membranes (MMMs) have captured the imagination of researchers for a possible technological breakthrough for efficient gas separation. However, it is still very challenging to achieve defect-free interface between fillers and polymer matrix. In this study, the naturally abundant and low cost halloysite nanotubes (HNTs) were applied as fillers for MMMs synthesis. To improve the filler dispersion and filler-matrix interface affinity, the raw HNTs were modified by either alkali etching or (3-Aminopropyl) triethoxysilane grafting. After surface etching, the defect holes were formed on the surfaces of etched-HNTs, resulting in the rougher HNT walls and significant increment of surface area and CO2 adsorption capacity. The filler/polymer interfacial voids and filler dispersion were quantitatively assessed by tomographic focused ion beam scanning electron microscopy. HNTs surface etching significantly improved the HNTs/polymer interfacial affinity (void% = 0.06% for Raw-HNTs MMM, 0.02% for Etched HNTs MMMs) and filler dispersion, while grafted-HNTs mainly contribute to the filler dispersion. Compared to the pure polymer membrane and MMMs with untreated HNTs, MMMs containing 10 wt.% etched HNTs filler exhibited both increased CO2 permeability (807.7 Barrer) and higher CO2 selectivity (CO2/CH4 selectivity of 27.8) on the well-known limit of Robeson upper bound. In contrast, grafting HNTs only increased the membrane permeability without enhancing CO2 selectivity. The results suggest that surface etching can be an effective route in filler modification to improve interfacial morphology and membrane separation performance.
Impairment of the skin’s structural integrity initially results in acute wounds which can become chronic if timely wound closure is not achieved. Chronic wounds (CWs) affect more than 1% of the global population with increasing cases of this condition due to the ageing population. Current wound management relies on debridement, hyperbaric oxygen, antibiotics, and wound dressings, which lack early intervention and specificity. Herein, antibiotics-free retinol-based micellar formulations (RMF) were made and their wound healing efficacy were investigated in vitro. Five different formulations with retinol contents of 0.3% and 1% against a placebo were topically applied to an organotypic full-thickness skin wound model (FT-SWM, MatTek®) with a 3 mm punch wound, and maintained in an incubator for 6 days. The histological analysis of the FT-SWM was conducted at depths of 60 µm and 80 µm. It was found that all the micellar retinol formulations accelerated wound bed contraction, with 0.3% RMF demonstrating the highest efficacy. At the depths of 60 µm and 80 µm, the 0.3% RMF exhibited inner wound diameter contraction of 58% and 77%, respectively, in comparison to the placebo showing 15% and 8%. The RMF significantly accelerated wound healing and can thus be a potential early intervention for speedy wound recovery. It should be pointed out that these results were obtained based on a small sample size and a large sample size will be explored to further validate the results.
Single particle breakage characterisation at fine sizes for use in mill modelling has been addressed by only a few researchers and is not utilised in engineering design. This is mainly due to the challenge of accurately imparting a range of impact energies to sub-millimetre particles and then measuring the progeny size distribution for the tiny resultant mass. In order to fill this gap, a dispersed monolayer multi-particle breakage method was applied with a mini JK Drop weight tester in this work to extend the single particle breakage test from 16 mm down to 425 μm, covering a specific energy (Ecs) range of 0.1 - 2.5 kWh/t to provide a wide range of test conditions. A challenge that had to be addressed was switching from single particle to dispersed mono-layer due to the physical constraints of drop-height and drop mass in maintaining accuracy in input energy over the orders of magnitude required to apply the required specific range of energy input. As only a limited size range could be subjected to both single particle and mono-layer bed breakage, it was necessary to establish if the two testing techniques provide the same breakage results. A novel application of the Fréchet distance was successfully applied to quantitatively evaluate the discrepancy of progeny size distribution between single particle breakage and monolayer multiple particle breakage. Extrapolation of an empirical Fréchet distance model indicated that the application of dispersed mono-layer breakage below 2 mm provides an acceptable comparison with the single particle breakage applied to coarser sizes, thus facilitating the fitting of a single appearance function across this wide range of sizes and applied breakage energies.
The stability of agglomerated/pelletized ores is one of the key properties for successful heap leaching of complex, low-grade nickel laterite minerals. In this paper, single pellets of saprolitic and goethitic nickel laterite with controlled binder type (tap water and 44 wt.% H2SO4), binder content and pre-set porosity were made by a pellet press and subjected to mechanical strength and rewetting stability tests. The effect of fine/coarse particles ratio on the mechanical strength was also investigated using siliceous goethitic ore. The failure strength of the pellets under different drying conditions was measured and the time taken for the pellets to disintegrate under saturated (soaking) and leaching conditions was recorded. The results showed that, with the same type of nickel laterite, the time taken to disintegration during leaching test is proportional to the pellets tensile strength. Pellets with water as binder are more stable under soak conditions. Furthermore, failure strength for oven dried pellets is greater than that of air dried. With saprolitic nickel laterite (SAP) pellets, their mechanical strength and re-wetting stability can be enhanced by drying the wet pellets or by increasing the binder content in the pellets. The pellets mechanical strength was found to be a good indication of their stability under leaching conditions as well. However, no relationship between the two was observed for goethitic nickel laterite pellets.
Heap leaching is a widely used extraction method for low-grade minerals including nickel and cobalt. Agglomeration of fine mineral particles as a precursor to heap leaching is an important means of enhancing leaching rates and metal recoveries. Single pellet leaching behaviour of three nickel laterite ores, namely siliceous goethitic (SG), goethitic (G) and saprolitic (SAP) was investigated to assess the effect of pellet properties (binder type, binder content, porosity and dryness) on its stability, initial leaching rate and maximum Ni recovery. The column leaching performance of agglomerates of the same ores was also investigated. Both single pellet and column leaching tests showed that the ore mineralogy played a major role in the Ni extraction rate, with G-type of ore the lowest. The Ni extraction rate was also found to be directly related to the pellet/agglomerate dryness and the highest rate was obtained at an intermediate degree of dryness due to the better wetting and diffusion of acidic lixiviant into the pores in between the particles. However, no significant effect of drying on the stability of the agglomerates (measured by agglomerate slump in the column) was found in column leaching. For G type of ore, mixing it with high clay ores during agglomeration is recommended to enhance its robustness during leaching process.
Milling is commonly used for controlling the size distribution of granules in the pharmaceutical dry granulation process. A thorough understanding of the breakage of single compacts is crucial in unravelling the complex interactions that exist between different pharmaceutical feed materials and the mill process conditions. However, limited studies in the literature have examined the impact breakage of single pharmaceutical compacts. In this study, pharmaceutical powders including the microcrystalline MCC 101, MCC 102 and MCC DG were compressed at different pressures and tablets with different porosities and thicknesses were produced. Impact breakage tests were conducted in an air gun and the tablet impact velocities and breakage patterns were analysed using a Phantom ultrahigh-speed camera. It was observed that the tablet breakage rate and the amount of fines reduced as the tablet porosity decreased. In addition, thin tablets with low porosity exhibited semi-brittle fracture and less intense crack propagation while thick tablets with high porosity primarily disintegrated into fine fragments. Thus, this study provides a better understanding of the breakage behaviour of different pharmaceutical materials and can potentially be used to describe the breakage modes of compacts in the ribbon milling processes.
[Display omitted] •A model has been proposed for the prediction of breakage in a high-shear mixer.•The capillary number and the pore saturation appear to be the key parameters.•Data fitted to the model is well-predicted.•The model does currently not extend to different powder-binder systems. Granule breakage is an important rate process in wet granulation that promotes product uniformity and controls product size and strength. In this work, a model to predict granule breakage is proposed and experimentally validated. The model assumes exponential of the surviving granules, dependent on a probability of breakage; a function of powder and binder properties, as well as operating parameters. Validation experiments were performed with a breakage-only granulator, filled with cohesive, non-granulating sand. Premade pellets made from lactose monohydrate and silicone oils were granulated at several impeller speeds, and the number of survivors was observed over time. The results revealed that the number of granules did indeed decay exponentially. It was found that the overall probability of breakage was inversely proportional to the capillary number. Moreover, the pore saturation played an important role in determining the probability of breakage, with higher pore saturations reducing breakage overall. A comparison with experimental data from literature revealed that the developed models agrees qualitatively with the experimental data, but is unable to fully capture the effect of powder properties and powder-binder interaction.
Accidental superheated liquid emissions into the atmosphere yield two-phase releases. The resulting flashing jet, driven by thermal nonequilibrium and mechanical forces, breaks up into massive droplets, fostering beneficial conditions for fire, explosion, and toxic diffusion. In this work, a 20 L tank was built to examine two-phase flow behaviors during depressurized releases of superheated liquids via a high-speed camera and phase Doppler anemometry. Different breakup regimes of flashing jet and dimensionless groups that effectively represent thermodynamic (RpJa) and mechanical (WevOh) driving effects were determined. Based on the interaction between the two effects, quantitative criteria to distinguish different regimes were developed. The accompanying jet characteristics, including jet angle (θ), area fraction (fA), droplet diameter (dSMD), and droplet velocity (ud), and their relationship with jet breakup were revealed. Results show that non-flashing (NFB), partially flashing (PFB), and fully flashing (FFB) breakups coincide with RpJa(WevOh)1/7
This work aims to build a generic dynamic model structure, which can accommodate interchangeable sub-models of each sub-process, making it amenable to continuous upgrade without the need for redevelopment, for multicomponent tumbling grinding mills. The Generic Tumbling Mill Model Structure (GTMMS) is based on a population mass balance framework which incorporates breakage characteristics, transport, classification along the mill, a discharge function, and energy consumption incorporated in a dynamic mill model structure. Version III builds on two earlier versions by incorporating energy distributions derived from discrete element modelling, an updated version of the 4D breakage appearance function which applies to a broader size range, and addresses multi-component ore breakage via the probability distribution of energy split based on material stiffness. The model has been tested against multi-component plant survey data. GTMMS III suggests a mechanistic insight into mixture prediction through component analysis and is a step forward towards the unified comminution model (UCM) with its mechanistic, generic, and dynamic prediction capability.
A two-dimensional, along-the-channel, two-phase flow, non-isothermal model is developed which represents a low temperature proton exchange membrane (PEM) fuel cell. The model describes the liquid water profiles and heat distributions inside the membrane electrode assembly (MEA) and gas flow channels as well as effectiveness factors of the catalyst layers. All the major transport and electrochemical processes are taken into account except for reactant species crossover through the membrane. The catalyst layers are treated as spherical agglomerates with inter-void spaces, which are in turn covered by ionomer and liquid water films. Liquid water formation and transport at the anode is included while water phase-transfer between vapour, dissolved water and liquid water associated with membrane/ionomer water uptake, desorption and condensation/evaporation are considered. The model is validated by experimental data and used to numerically study the effects of electrode properties (contact angel, porosity, thickness and platinum loading) and channel geometries (length and depth) on liquid water profiles and cell performance. Results reveal low liquid water saturation with large contact angle, low electrode porosity and platinum loading, and short and deep channel. An optimal channel length of 1 cm was found to maximise the current densities at low cell voltages. A novel channel design featured with multi-outlets and inlets along the channel was proposed to mitigate the effect of water flooding and improve the cell performance.
The t10 relationship developed by Narayanan and Whiten has underpinned a number of the JKMRC models and the characterisation of ore competence through impact testing with the drop weight tester. This usefulness is based on a consistent relationship between the t10 value and the overall size distribution that was noted for brittle rocks. However, like all characterisation tests this should be used only when the controlling conditions apply, which in this case is single impact breakage between two metal platens and within the range of sizes in which fragment sizes are normalizable. For any other mode of breakage the relationship should be confirmed before being applied. Soft ores or bimodal ores with widely different competence between dominant components have non-typical breakage signatures. Breakage via single point impact abrasion, compressed-bed breakage, low-energy surface breakage and incremental breakage, to name some of the other breakage modes, do not obey the general t10 relationship, so their outcomes cannot be used to provide a direct comparison. Inappropriate use of the t10 parameter can result in misleading conclusions about efficiency of energy use. These issues and alternative comparison techniques are presented and discussed in terms of choosing appropriate measures of efficiency of breakage, ore competence and energy required for comminution.
In this paper, ibuprofen from a commercial source and its fractioned samples with narrower size distribution were characterized to assess the effect of particle properties on compaction characteristics. The compaction behavior of binary mixtures of ibuprofen with spray-dried lactose was also studied. The tablet in-die densification rate and tablet out-of-die porosity and tensile strength were measured for all samples. It was found that the particle size of ibuprofen does not affect the yield stress as derived from a Heckel plot, however the yield stress increases with the increase of ibuprofen particle size in the binary mixtures. Particle size also affects the tablet out-of-die properties, with tablet porosity and tensile strength increasing with the decrease in particle size. The effect of adding a weak compacting powder such as lactose on the tablet tensile strength is very much dependent on the ibuprofen particle size and mass ratio of the binary mixtures. Mixing lactose with ibuprofen of similar size in equal mass has no effect on the tensile strength of the tablet whereas mixing it with ibuprofen of larger size reduces the strength compared to ibuprofen alone. Adding a smaller amount of lactose can lead to an increase in tablet strength, even though the particle size of ibuprofen and lactose is quite different. Theoretical analysis on the tablet strength based on particle–particle bond strength was also carried out to explain the experimental results.
The addition of organic phosphorus-containing flame retardants (OPFRs) has greatly improved the fire resistance of epoxy resins (EPs). Developing the relationship of the fire resistance with the structure of OPFRs and their addition amount will help discover high-performance EP composites, which was achieved in this work by machine learning (ML). By combining descriptors encoded from OPFR molecules and the addition amount as features, an ML model with the limiting oxygen index (LOI) as the target was developed with a coefficient of determination (R2) of the ML model on the test set of 0.642. The trained ML model indicated that fire retardants containing conjugated systems with penta-substituted phosphorus containing a P=O bond and the nitrogen element can significantly increase the LOI of EPs, which led to the synthesis of a 9,10-dihydro-9-oxa-10-phosphaphenanthrene-10-oxide derivative (BDOPO) in this work. Furthermore, the accuracy of the ML model was validated through experiments. The predicted LOI values of the EP/BDOPO composites followed the same trend as the experimental values, with an average error of 5.1%. The model can also illustrate the molecular structure required for synthesizing an OPFR and predict the amount of this OPFR to be added into EPs for enhanced LOI of the EPs.
Dry granulation through roll compaction is a technology commonly used in the pharmaceutical industry for producing roll compacted ribbons. The significance of the feed screw speed and roll speed during ribbon production was highlighted in recent publications. However, previous studies focused primarily on the individual effects of either the feed screw speed or roll speed on ribbon porosity, and the synergetic effect of these parameters was rarely examined. The aim of this study therefore was to investigate the effects of the screw-to-roll speed ratio on the porosity of roll compacted ribbons, produced at different roll compaction conditions using the microcrystalline cellulose MCC, Avicel PH-102 feed material. It was observed that ribbon porosity decreased linearly with increasing screw-to-roll speed ratio. Furthermore, an increase in the speed ratio led to an increase in the roll gap and mass throughput while a decrease in the screw constant was observed. Thus, this study demonstrates that the screw-to-roll speed ratio can be treated as one of the critical process parameters for controlling ribbon porosity and can also be used to determine the optimum operating regimes during roll compaction.
The latest state of the art on Discrete Element Method (DEM) and the increased computational power are capable of incorporating and resolving complex physics in comminution devices such as tumbling mills. A full 3D simulation providing a comprehensive prediction of bulk particle dynamics in a grinding mill is now possible using the latest DEM software tools.This paper explores the breakage environment in mills using DEM techniques, and how these techniques may be expanded to provide more useful data for mill and comminution device modelling. A campaign of DEM simulations were performed by varying the mill size and charge particle size distribution to explore and understand the breakage environment in mills using DEM techniques. Analysis of each mill was conducted through consideration of the total energy dissipation and the nature of the collision environment that leads to comminution.The DEM simulations show that the mill charge particle size distribution has a strong influence on the mill input power and on the way the energy is distributed across the charge. The smaller particles experience higher energies while the larger experience less, but this variation is strongly dependent on the mill size. The results also showed that the average particle collision energy increases with increasing mill size, whereas its distribution over particle size is strongly influenced by the mill content particle size distribution. The simulations also captured the energy distribution within different regions of the tumbling charge, with the toe impact region having higher impact energies and the bulk shear region having higher tangential energies. Regardless of the mill size most of the energy is consumed by the particles in the mid-size range, which has the highest percentage mass of the total charge distribution.
We conduct Observing System Simulation Experiments (OSSEs) with Lagrangian data assimilation (LaDA) in two-layer point-vortex systems, where the trajectories of passive tracers (drifters or floats) are observed on one layer that is coupled to another layer with different dynamics. Depending on the initial position of the observed tracers, the model studied here can exhibit nonlinear features that cause the standard Kalman filter and its variants to fail. For this reason, we adopt a Monte Carlo approach known as particle filtering, which takes the nonlinear dynamics into account. The main objective of this paper is to understand the effects of drifter placement and layer coupling on the precision skill of assimilating Lagrangian data into multi-layered models. Therefore, we analyze the quality of the assimilated vortex estimates by assimilating path data from passive tracers launched at different locations, on different layers and in systems with various coupling strengths between layers. We consider two cases: vortices placed on different layers (heton) and on the same layer (non-heton). In both cases we find that launch location, launch layer and coupling strength all play a significant role in assimilation precision skill. However, the specifics of the interplay of these three factors are quite different for the heton case versus the non-heton case. © 2014.
In order to develop a common mathematical and simulation platform for tumbling mills, a review of existing mechanistic models was made identifying the key aspects of grinding and slurry transport which are common to all tumbling mills. A mill model structure has been developed for all types of tumbling mills based on the population balance framework by incorporating breakage characteristics, slurry and solids transport, product classification and discharge, and energy consumption. A size-dependant breakage model developed by the JKMRC is applied. Transport is separated from breakage events and treated as a main sub-model in the new model structure. The model structure is based on dynamic time-stepping technique to enable dynamic simulation capability for non-steady-state simulation and control modelling. It is envisaged that the new model will cover a full range of milling conditions. It should enable a smooth transition between different mill types, such as from AG (Autogenous Grinding) to SAG to ball mill. The dynamic mill model structure developed here is the first step towards mechanistic modelling of grinding mills and provides great potential for the optimization of the comminution process
Chronic wounds and their treatment present a significant burden to patients and healthcare systems alike, with their management further complicated by bacterial infection. Historically, antibiotics have been deployed to prevent and treat infections, but the emergence of bacterial antimicrobial resistance and the frequent development of biofilms within the wound area necessitates the identification of novel treatment strategies for use within infected chronic wounds. Here, several non-antibiotic compounds, polyhexamethylene biguanide (PHMB), curcumin, retinol, polysorbate 40, ethanol, and D-& alpha;-tocopheryl polyethylene glycol succinate 1000 (TPGS) were screened for their antibacterial and antibiofilm capabilities. The minimum inhibitory concentration (MIC) and crystal violet (CV) biofilm clearance against two bacteria frequently associated with infected chronic wounds, Staphylococcus aureus and Pseudomonas aeruginosa, were determined. PHMB was observed to have highly effective antibacterial activity against both bacteria, but its ability to disperse biofilms at MIC levels was variable. Meanwhile, TPGS had limited inhibitory activity but demonstrated potent antibiofilm properties. The subsequent combination of these two compounds in a formulation resulted in a synergistic enhancement of their capability to kill both S. aureus and P. aeruginosa and disperse their biofilms. Collectively, this work highlights the utility of combinatory approaches to the treatment of infected chronic wounds where bacterial colonization and biofilm formation remains significant issues.
The breakage characteristics of a two-component ore in a confined bed was studied in this work in order to predict the breakage behaviour of a multi-component ore from the properties of individual components. Bed compression tests with each single component and blended components at different bulk volumetric ratios were carried out at different volume based specific energies and the bed particle size distributions of each component in the mixtures were measured (through magnetic separation). The experimental results show that the breakage product size measured by t10 – the cumulative mass percentage of particles less than 1/10th of the feed size, is linearly proportional to the relative bed porosity reduction, for both single component and multi-component ore. There is a minimum bed porosity reduction to be reached before any breakage occurs and the less competent the ore, the lower the minimum porosity reduction value. Theoretical analysis on bed compression breakage shows that the relationship between product size measured in t10 and the specific comminution energy (Ecs) is not unique and is dependent on the testing conditions. The analysis shows the importance of testing bed breakage at conditions that are independent of bed configurations. Furthermore, models for predicting the product t10 and specific comminution energy of multi-component ore from single component compression data are developed. By compressing the particle bed at the set porosity reduction for each component and few multi-component tests, one can predict the mixture product and mixture energy consumption at any mixture ratios without the needs to physically separate the products in the mixture test.
The Appearance function, also known as breakage distribution function, is used to describe the breakage characteristics of an ore impacted with a certain energy. It is the bedrock of comminution modelling. The range of applicability of the majority of existing appearance functions is limited to coarser sizes above a few millimetres. In the previous work, a 4D (four dimensional) appearance function model was developed based on JKRBT test data, but its applicable range was not sufficiently broad at −24.4 + 7.3 mm. In order to develop a more versatile appearance function model that can be used for a wide range of energy levels and feed particle sizes, drop weight tests for smaller particles with sizes ranging from 425 μm to 16 mm were carried out with the Mini JK drop weight tester. Combined with data up to 63 mm from Standard JK Drop Weight Tests, the outcomes were fitted to two types of 4D appearance functions - the P80-m based 4D model and the P80-m-q based 4D model. The proposed 4D models are more accurate and scalable than existing models. Most importantly, they can be used for a wide range of conditions, with feed particle size ranging from 425 μm to 63 mm and input specific energy from 0.1 to 2.5 kW h/t in the initial test data.
The preparation of effective phosphorus-nitrogen flame retardants (PNFRs) is still limited using organic solvent. In this work, a solvent-free mechanochemical method was introduced to prepare a phosphorus-containing hypercrosslinked aromatic polymer (HCAP) from triphenylphosphine. Subsequently, nitrogen-rich graphitized carbon nitride was introduced to prepare a series of phosphorus and nitrogen-containing heterojunctions named HCN. The formation of the HCAP and HCN was verified by a combination of density functional theory (DFT) calculations and experiments. Afterwards, upon addition of 5 wt% 20HCN to epoxy resin (EP), the limiting oxygen index and vertical combustion test level reached 30.3% and V-0, respectively. The peak heat release rate, total heat release, peak smoke production rate and total smoke production were reduced by 41.2%, 38.4%, 34.9% and 36.0%, respectively, relative to those of the pure EP. The combined scores of multiple flame retardant properties were evaluated through machine learning. The mechanical properties and thermal conductivity remained at the same level as those of EP. These results confirmed the role of HCN in reducing the fire hazard of EP, stemming from its lamellar char and ability to blow out flames. This work provides a new method of preparing PNFRs. [Display omitted] •Solvent-free synthesized of a new phosphorus-nitrogen flame retardant (PNFR).•Combining density functional theory calculation and experiments.•The fire resistance of EP with this new PNFR was improved.•A lamellar char and a “blowing out” phenomenon were formed.•Machine learning was adopted to compare fire resistance.
Solid pharmaceutical tablets can be manufactured via three processing technologies: direct compression, dry granulation and wet granulation before the final compaction process. Dry granulation using roll compaction generally involves production of ribbons, followed by milling to produce granules and the production of tablets. The mechanical properties of ribbons produced during roll compaction can influence breakage behaviour in a mill and hence the performance of a drug formulation. Therefore it is important to explore critical factors that determine the quality of ribbons. In this study, MCC Avicel PH-102 was used as the model powder for roll compaction and the critical operating factors affecting ribbon quality were studied. MCC 102 ribbons were manufactured at a range of process conditions (roll speed, feed screw speed and compaction pressure) using the TF mini roll compactor with a serrated die & punch (DPS), grooved roll surface. The key ribbon properties measured are the powder feed ratio (defined as the ratio of feed screw speed to that of roll speed) and mass throughput ratio (defined as the mass of ribbons produced in a given time to that of fines). The porosity of ribbons was observed to depend significantly on powder feed ratio into the compaction zone. Porosity remained constant at a fixed feed ratio irrespective of the absolute roll speed and the feed screw speed conditions used. Mass throughput ratio is another factor that was introduced to describe process efficiency i.e. to draw comparison between the amount of ribbons and fines. The amount of ribbons and fines generated at a given process condition depends significantly on the feed screw speed and the compaction pressure. In addition, ribbon porosity decreased with increasing pressure but there was negligible effect on ribbon porosity when excessively high pressure (> 60 bar) was used. Ribbon porosity was also observed to decrease with increasing feed screw speed but the converse is true with increasing roll speed. In conclusion, the impact of various roll compaction process parameters were critically investigated and a detailed insight into the main factors (powder feed and mass throughput ratios) that govern the behaviour of roll compacted ribbons was provided. In future, the focus is to relate these process properties (and ribbon porosity) to granule size distribution from a milling process.
The latest state of the art on Discrete Element Method (DEM) and the increased computational power are capable of incorporating and resolving complex physics in comminution devices such as tumbling mills. A full 3D simulation providing a comprehensive prediction of bulk particle dynamics in a grinding mill is now possible using the latest DEM software tools. This paper explores the breakage environment in mills using DEM techniques, and how these techniques may be expanded to provide more useful data for mill and comminution device modelling. A campaign of DEM simulations were performed by varying the mill size and charge particle size distribution to explore and understand the breakage environment in mills using DEM techniques. Analysis of each mill was conducted through consideration of the total energy dissipation and the nature of the collision environment that leads to comminution. The DEM simulations show that the mill charge particle size distribution has a strong influence on the mill input power and on the way the energy is distributed across the charge. The smaller particles experience higher energies while the larger experience less, but this variation is strongly dependent on the mill size. The results also showed that the average particle collision energy increases with increasing mill size, whereas its distribution over particle size is strongly influenced by the mill content particle size distribution. The simulations also captured the energy distribution within different regions of the tumbling charge, with the toe impact region having higher impact energies and the bulk shear region having higher tangential energies. Regardless of the mill size most of the energy is consumed by the particles in the mid-size range, which has the highest percentage mass of the total charge distribution.
Optimisation of grinding circuits is invariably dependent on sound process models together with process simulators that can solve the process models accurately. Most of the process models are solved numerically because analytical solutions are not available, which can lead to errors in the results due to the numerical approximation of mathematical equations. Whiten [1], and Valery Jnr & Morrell [2, 3] have developed a dynamic model with numerical simulation for autogenous and semi-autogenous mills, and validated the model with dynamic response of mills in terms of power draw, grinding charge level, slurry level and product size distribution to changes in feed rate, feed size, feed hardness and water addition [2, 3]. In this work, an analytical solution for their dynamic model of tumbling mills has been developed based on the knowledge of solutions to the first-order nonhomogeneous linear differential equations. Two algorithms, Direct Single Time method (DST) and Direct Multiple Time method (DMT), were applied to obtain the analytical solutions respectively. It was found that analytical solutions are more accurate than the traditional finite difference numerical methods. However, the DST analytical method has a drawback of numerical instability due to the accumulation of round-off errors which are amplified by exponential functions, whilst the DMT method can provide stable solutions. To test the DMT analytical method, two cases of SAG mill dynamic operation were studied with both the traditional numerical method and the newly developed analytical method, further proving the robustness and feasibility of the analytical solutions.