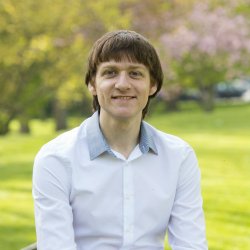
Dr Colin Hare
About
Biography
My expertise are in particle technology, where I aim to relate particle properties and process conditions to product performance, with particular focus on powder flow and particle breakage. I obtained MEng (2006) and PhD (2010) degrees in Chemical Engineering from the University of Leeds. I was awarded the Young Researcher of the Year Award at the UK Particle Technology Forum in 2012, and the IChemE 2015 Nicklin Medal for promising young engineering researchers at ChemEngDayUK 2016. I am also a member of the EPSRC Early Career Forum in Manufacturing Research.
During my PhD I developed a method to predict particle breakage during agitated drying of crystallised solids. As a research fellow at the Institute of Particle Science & Engineering at The University of Leeds (2010 – 2016), I co-developed the method of ball indentation for powder flowability measurement. I carried out a knowledge transfer secondment to Procter & Gamble during 2014-15, exploring “Advanced Manufacturing Based on the Discrete Element Method”, where I developed an approach to predict size reduction in ribbon milling operations.
In 2014 I was awarded a research grant by the International Fine Particle Research Institute (IFPRI) to carry out a “Flowability Assessment of Weakly Consolidated Powders”, receiving further funding from IFPRI in 2017 to continue this work. I have also received funding from Corning Inc. for “Characterising Powder Flow in Dynamic Processes”, and am a co-investigator on the Marie-Curie ITN “Mathegram”.
Areas of specialism
My qualifications
ResearchResearch interests
- Powder flowability, particularly at low stresses and/or high strain rates
- Predicting and optimising particle breakage/attrition mitigation
- Mechanical property characterisation
- The Discrete Element Method (DEM)
- Particle coating by powders or liquids
Research projects
Flowability assessment of weakly consolidated powdersReliable powder flow measurement methods for quasi-static flow under moderate to high stress levels are established, with shear cells being readily utilised for hopper design and powder flowability ranking. However when measuring under low stresses, the reliability of shear cells, and other test methods, deteriorate. This project investigates how best to operate a shear cell in order to improve the flow measurement, as well as exploring alternative flow measurement techniques, such as ball indentation and uniaxial compression. Furthermore, a wide range of powders are explored to determine the influence of individual particle properties on powder flowability. This project is funded by the International Fine Particle Research Institute (IFPRI).
Indicators of esteem
EPSRC Associate College Member
Secretary of the IChemE Particle Technology Special Interest Group (PTSIG) (2021-present)
Treasurer of the IChemE Particle Technology Special Interest Group (PTSIG) (2018 - 2021)
Member of EPSRC Early Career Forum in Manufacturing Research (2016 - present)
Research interests
- Powder flowability, particularly at low stresses and/or high strain rates
- Predicting and optimising particle breakage/attrition mitigation
- Mechanical property characterisation
- The Discrete Element Method (DEM)
- Particle coating by powders or liquids
Research projects
Reliable powder flow measurement methods for quasi-static flow under moderate to high stress levels are established, with shear cells being readily utilised for hopper design and powder flowability ranking. However when measuring under low stresses, the reliability of shear cells, and other test methods, deteriorate. This project investigates how best to operate a shear cell in order to improve the flow measurement, as well as exploring alternative flow measurement techniques, such as ball indentation and uniaxial compression. Furthermore, a wide range of powders are explored to determine the influence of individual particle properties on powder flowability. This project is funded by the International Fine Particle Research Institute (IFPRI).
Indicators of esteem
EPSRC Associate College Member
Secretary of the IChemE Particle Technology Special Interest Group (PTSIG) (2021-present)
Treasurer of the IChemE Particle Technology Special Interest Group (PTSIG) (2018 - 2021)
Member of EPSRC Early Career Forum in Manufacturing Research (2016 - present)
Supervision
Postgraduate research supervision
Principal supervisor:
Azza Mahmoud - Powder Flowability at low stresses
Co-supervisor:
Domenica Braile - Heat generation due to biological activity of biological granular material
Omar Ismail - A combined experimental and numerical study of powder flow through forced feeders in tableting systems
Francisco Kisuka - Modelling of heat generation induced by friction
Aman Rastogi - CFD-DEM modelling of heat generation and transfer in reactive granular materials
Publications
The inability of cohesive powders to flow consistently and reliably is a major cause of process downtime and reduced efficiency across a wide range of powder processing industries. Most methods to assess powder flowability fail at low consolidation pressures (
Roller compaction followed by milling of the generated ribbons is a typical dry granulation route. It is desirable to be able to predict the size distribution of the granules exiting the mill based on the ribbon properties and mill operational conditions. Two DEM-PBM approaches for predicting this size distribution are compared; a direct approach where the size distribution is experimentally determined, and an indirect approach where the successive change in size distribution due to each stressing event is determined mathematically by the PBM. The experimental component of the direct approach assumes shear deformation to be the dominant breakage mechanism. This approach provides a reasonable agreement to experimental data, though the influence of mill parameters is not experimentally tested. When considering breakage to be driven by impact, the indirect approach predicts the correct magnitude of fines generation, though incorrectly predicts the fine fraction to increase with impeller speed. When abrasion is assumed to be the dominant breakage mechanism, the indirect approach suggests the same trend, though with a less pronounced effect of impeller speed and a closer agreement to experimental data. Prediction accuracy is expected to improve by considering distributions of stressing conditions and material strength, the latter being explicitly captured in the experimental component of the direct method. Furthermore, the direct method accounts for the variable loading conditions of the fragments in the mill.
The rheological behaviour of a dense granular bed under dynamic conditions is investigated by simulating granular flow in the FT4 powder rheometer using the Discrete Element Method. The distribution of the prevailing stresses and strain rates in the granular bed, and their dependence on material properties and blade operational conditions, are analysed. The shear stress was found to be approximately constant in the radial direction along the blade but dissipates in the circumferential direction away from the blade. Analogously, the strain rate decreases with increasing angular distance away from the blade as the bed becomes less dynamic. An increase in the blade tip speed, particle aspect ratio and interfacial energy results in an increase in the average shear stress in the granular bed. A predictive model is proposed to compute the average shear stress in the granular bed based on the blade torque by considering the effects of blade tip speed, particle aspect ratio and interfacial energy. [Display omitted] •Rheological response of granular materials in the FT4 rheometer is analysed.•Shear stress and strain rate dissipates away from the blade.•Shear stress is approximately constant radially along the blade.•Increasing tip speed, aspect ratio and interfacial energy increases the shear stress.•A predictive model is proposed to calculate the shear stress from the blade torque.
Ball indentation is a technique capable of assessing powder flowability down to very low consolidation stresses (≤1 kPa). With this method, powder flowability is determined by measuring the hardness of a powder bed, which allows the unconfined yield strength to be inferred via the constraint factor. The latter is well established for continuum materials, whereas for particulate systems its dependency on stress level and powder properties is not well defined. This work investigates these factors by simulating the ball indentation method using DEM. The constraint factor is shown to be independent of pre-consolidation stress. Constraint factor generally increases with interface energy for relatively cohesion-less powders, though not for cohesive powders. An increase in plastic yield stress leads to a decrease in the constraint factor. Increasing the coefficient of interparticle static friction reduces the constraint factor, while increasing the coefficient of inter-particle rolling friction significantly increases the constraint factor.
Friction is a critical factor in shear flow of granular materials. Therefore, understanding and quantification of frictional behaviour of granular materials is necessary for accurate predictive models of shear flow behaviour. In this study, the effect of sliding velocity and normal load on the sliding friction coefficient is experimentally determined by shearing two layers of dry spherical glass particles over one another for a range of sliding velocities from 10 to 300 mm/s, and normal loads of 1.2 to 4.8 N. The friction between the glass surfaces shows a strong velocity-dependent effect, however, the effect of normal load is less significant. Based on the experimental results, a velocity-dependent sliding friction is implemented into DEM to simulate the shear response of spherical particles in the FT4 Powder Rheometer for a range of strain rates; spanning the transition from quasi-static to intermediate flow regimes. The accuracy of the variable friction model and the conventional constant friction model to predict shear flow behaviour in the FT4 Powder Rheometer over a wide range of strain rates is examined. It is demonstrated that the constant friction model only provides accurate prediction of the flow energy over a narrow range of strain rates, whereas the velocity-dependent friction model gives a better prediction of the experimental flow energy over a relatively wider range of strain rates. [Display omitted] •Sliding friction dependency on force and velocity was tested for glass beads•Shearing tests revealed velocity-strengthening behaviour•The normal force effect on sliding friction was found to be less significant•FT4 flow energy was evaluated in DEM with/without velocity-dependent friction•Velocity-dependent model is more accurate over a wide strain rate range
Granular flows are characterised by particle interactions that involve sliding and collisions. In such events, heat is generated from friction and plastic deformation. Despite the importance of such self-heating mechanisms, our understanding of the fundamental principles of heat generation from friction and plastic dissipation is still limited. This work explores this problem at the particle level for oblique impacts between a spherical particle and a rigid substrate. In the first part, theoretical models and a finite element method (FEM) model are used to predict the amount of heat generated and contact temperatures at various impact angles. The theoretical and the FEM models are in good agreement for all impact cases considered. A parametric study of the influence on heat generation and temperature distributions is also carried out. It is shown that the temperature profiles are dependent not only on the amount of the generated heat but also on the material's thermal properties, such as thermal conductivity and specific head capacity. Apart from a good insight into heat generation during oblique impacts, this study also identifies simple theoretical solutions that can be used in other numerical tools, such as discrete element methods, for studying heat generation problems in bulk granular flows.
Die filling is a critical process step in pharmaceutical tablet manufacturing. Mass and content uniformity of the tablets as well as production throughput depend upon the die filling performance of the formulations. The efficiency of the die filling process is influenced by powder properties, such as flowability, cohesion, particle size and morphology, as well as the process conditions. It is hence important to understand the influence of powder properties on the die filling performance. The purpose of the present study is to identify the critical material attributes that determine the efficiency of die filling. For this purpose, a model rotary die filling system was developed to mimic the die filling process in a typical rotary tablet press. The system consists of a round die table of 500 mm diameter, equipped with a rectangular die. The die table can rotate at an equivalent translational velocity of up to 1.5 m/s. The filling occurs when the die passes through a stationary shoe positioned above the die table. Using this system, die filling behaviours of 7 commonly used pharmaceutical excipients with various material characteristics (e.g. particle size distribution, sphericity and morphology) and flow properties were examined. The efficiency of die filling is evaluated using the concept of critical filling velocity. It was found that the critical filling velocity is strongly dependent on such properties as cohesion, flowability, average particle size and air sensitivity index. In particular, the critical filling velocity increases proportionally as the mean particle size, flow function, air permeability and air sensitivity index increase, while it decreases with the increase of specific energy and cohesion.
Segregation of granular materials is often induced by differences in size, density, shape and surface properties. Density and size-induced mixing and segregation of binary mixtures of glass beads and/or resin particles in the FT4 powder rheometer are investigated experimentally using a new FT4 methodology. The proposed methodology allows for quantification of mixing and segregation of components based on a mixing index. It is observed that the mixing index increases with increasing density and size ratio. Variation of flow energy and torque is related to the mixing and segregation of the mixture components, thus demonstrating that the FT4 powder rheometer may be used as a predictive tool for the tendency of mixture components to segregate under various stress conditions. Numerical analysis by DEM shows that for non-cohesive systems mixing and segregation occur by sifting of fines through interstitial gaps formed between coarse particles in the dilated region. For the non-cohesive system, higher blade tip speeds reduce the rate of mixing and minimise the segregation of different-sized components. Increasing the interfacial energy reduces the rate of mixing and alleviates the segregation of particles. For the cohesive systems, mixing occurs by rupture of cohesive fine clusters with the mixing index increasing with increasing blade tip speed owing to the higher shear stresses that break the agglomerates. [Display omitted] •Mixing and segregation of binary mixtures in the FT4 were investigated.•A new FT4 methodology was developed to quantify mixing and segregation.•Effects of size and density ratios and surface energy were investigated.•Mechanisms governing mixing and segregation were evaluated.•Mixing and segregation rates were related to FT4 flow energy.
Many granular materials change their volume as they absorb fluids. This phenomenon is called swelling and can be observed in a variety of solids, such as soils, wood, absorbent hygiene products (AHPs) and pharmaceutical excipients. Therefore, an in-depth understanding of grain swelling is of great importance. Since experimental investigations can often provide only limited information, while great insight could be gained from numerical modelling, rigorous numerical models for predicting particle swelling are required. Hence, the objective of this research is to develop and validate a Discrete Element Method (DEM) for swelling of particles. A first order kinetic model was employed to predict the volume expansion of a single grain and subsequently implemented in DEM. The validation of the model was accomplished by comparing the expansion with time of a packed bed made of super absorbent polymer (SAP) particles obtained numerically and experimentally. It was shown that the DEM model can accurately predict the bed expansion. The model was then employed to simulate the swelling of three different materials: superabsorbent polymer (SAP), rice and microcrystalline cellulose (MCC Avicel PH102). As expected, it is demonstrated that the material properties play a significant role on the swelling; the fastest to reach its maximum expansion is the granular bed made of MCC PH102, followed by SAP and rice. However, the highest swelling capacity is achieved with SAP. Moreover, a preliminary DEM analysis of the segregation in a swelling binary mixture is presented in this work. Results suggest that systems which contain a small number of particles, and thus are looser, are more prone to segregation. Future study could advance the developed model to analyse consequences of swelling phenomena in granular materials, such as segregation and heat generation.
Die filling is an important process step in manufacturing of tablets. An important mechanism in the die filling process is suction that is developed with the downward motion of the bottom punch once the die is covered by powder. However, the contribution of suction to the die filling performance is still poorly understood. Hence, the present study aimed to experimentally investigate the flow behaviour of powders during suction filling. Four different types of pharmaceutical powders were used and a model suction filling system was developed. Effects of filling and suction velocities, as well as powder properties, on the efficiency of die filling were systematically investigated. Cohesive and free-flowing powders behaved differently at various filling-to-suction velocity ratios. The filling behaviour of cohesive powders was improved at high filling-to-suction ratios due to acceleration-induced densification. Free-flowing powders performed better at low filling-to suction ratios.
The present study investigated particle size-induced segregation during die filling of binary pharmaceutical blends, consisting of fine and coarse particles in various fractions. Coarse fraction was made of milled and sieved acetylsalicylic acid, whereas the fine fraction was mannitol. The die filling process was carried out in gravity filling and suction filling. The segregation was assessed through determination of the coarse component concentration using UV–Visible spectrophotometry. The obtained values of concentration, determined for ten units of identical volume inside the die, were used to calculate the segregation index (SI), which was an indicator of uniformity of the powder blend deposited into the die. It was found that high segregation tendency was generally observed during gravity filling at a low velocity, due to the effect of air drag, and during gravity filling at a high velocity, as it was carried out through three consecutive filling steps. The lowest segregation tendency was generally observed during suction filling at a low velocity. The horizontal segregation was mostly observed in the top layers of the die, due to mainly two mechanisms: coarse particles cascading down the heap formed by the powder in the final steps of die filling, which produces higher coarse concentration at the near side of the die, observed at low coarse concentration; or coarse particle cascading down the top surface of the flowing powder stream into the die, which increases the coarse concentration at the far end of the die.
In industrial processing and manufacturing, characterizing the flowability of particulate solids is of particular importance both for reliable powder flow and for a consistent production rate. Shear testing is the most widely used method for powders subjected to moderate or high stresses, and under quasi-static conditions. However, this method is not suitable for measuring the powder flow properties occurring in dynamic systems, such as powder mixers and screw conveyors. In this study, the rheological behaviour of powders at high shear rates has been evaluated by the ball indentation method. The technique, which simply consists of dropping a ball onto a cylindrical bed of previously consolidated powder, directly measures the material hardness, which is related to the unconfined yield stress by the constraint factor. The impact of the ball on the bed is recorded with a high-speed camera to determine velocity and penetration depth. The hardness against the strain rate is considered for four different materials. Because of their difference in particle size, and by using a range of drop heights and a range of indenter densities, the intermediate regime of flow has been fully analyzed. Although hardness is constant in the quasi-static condition, it results to be strain rate dependent in the intermediate regime of flow. Finally, a predictive correlation that allows the operator to choose the best operating conditions for achieving the desired flow regime is proposed, and the unconfined yield strength of the materials is inferred.
Poor and inconsistent flow of cohesive powders is a major issue in powder processing. A common solution is to coat the surfaces of the cohesive particles with finer particles, referred to as flow-aids. Such particles adhere to sticky surfaces and act as spacers preventing them from contacting each other and thus reducing the inter-particle forces and bulk powder cohesion. A question which naturally arises is how much flow-aid is needed to enhance the flowability to an optimum level. This work aims to establish a relationship between the degree of Surface Area Coverage (SAC) of flow-aids and the flowability, the latter as determined by a quasi-static shear cell method, as well as the angle of repose test and the FT4 powder rheometer. Glass beads of 90-150 μm sieve cut are made cohesive by silanising their surfaces with a commercial chemical reagent, Sigmacote® and are used as host particles. Two types of zeolite particles are used as flow aids. The mass fraction of the flow aids required to achieve a theoretical SAC of 1, 5, 10, 20, 50 and 100% is first estimated and then the host particles are coated in a pan mixer. The SAC is measured by Scanning Electron Microscopy, coupled with image analysis, and found to correlate well with the estimated value. The optimum surface coverage is found to be when SAC is 10-20%, as this provides the greatest flowability. An increase in SAC beyond this range leads to a gradual reduction in flowability.
Fine cohesive powders are often dry granulated to improve their flowability. Roller compaction is commonly used to produce dense ribbons which are then milled. The material properties of the powder and the conditions in the roller compactor affect the strength of the ribbons, however there is no method in the literature to predict the size distribution of the product of ribbon milling. Here we introduce a method, by using the Distinct Element Method (DEM) to determine the prevailing impact velocities and stresses in the mill, with bonded spheres representing the ribbons. The bond strength is calibrated by matching experimental results of three point bend measurements and predictions from numerical simulations. The ribbons are then exposed to the dynamic conditions predicted by the DEM, by dropping them from a controlled height to cause fragmentation, and subsequently stressing them in a shear cell under the conditions again predicted by the DEM. The fragments are sheared under these conditions to represent repeated passage of bars over the fragments at the mill base. Sieve analysis is used here to determine the particle size distribution under given mill conditions. The predicted size distribution of the mill product compares well with the plant data. It is found that the mill speed and length of ribbons fed to the mill have no significant influence on the product size distribution for the range tested.
During agitated drying and mixing processes, particle beds are exposed to shear deformation. This leads to particle attrition, the extent of which is dependent on the prevailing stresses and strains in the bed. The distributions of shear stresses and strain rates within the bed are highly non-uniform, requiring attention to localised conditions. Therefore a narrow angular sector of the bed is divided radially and vertically into a number of measurement cells, within which the stresses and strain rates are calculated throughout one rotation by the Distinct Element Method. These are then used in an empirical relationship of material breakage to predict the extent of attrition due to agitation. Here we investigate the influence of the measurement cell size on the estimated stresses and strain rates, and the subsequent effect on the predicted attrition. The measurement cell size is altered by varying the measurement sector size and the number of radial and vertical divisions within it. The median particle size is also varied to establish its influence on the predicted attrition. An increase in the average number of particles in a given cell, by varying the particle size or measurement cell dimensions, leads to a reduction in the estimated stresses and strain rates, and therefore a reduction in the predicted attrition. Comparison of the predicted attrition with the experimental breakage in the agitated vessel shows that the prediction method is accurate when the cell dimensions are comparable to the width of a naturally occurring shear band.
The characterisation of bulk behaviour of cohesive powders is very important in processing of particulate solids, e.g. for reliable powder flow out of storage vessels. For filling and dosing of small quantities of powders in capsules and for dispersion in dry powder inhalers, the interest is on the behaviour of loosely-compacted powders in small quantities and under very low applied loads. Furthermore at the early stages of drug development, the quantity of the powder available is often very small and the traditional bulk testing methods are neither possible nor applicable. In this work we evaluate a method to infer powder flowability by ball indentation. This technique provides a measure of flow resistance which can be related to the unconfined yield stress. It can be applied at very low loads and requires only a small sample quantity, typically a few mm3 . The operational window in the ball indentation method in terms of minimum sample size, penetration depth and indenter properties (such as size, shape, friction and Young’s modulus) has been analysed and reported here.
Particles are frequently exposed to shear stresses during manufacturing, which leads to breakage. This is particularly relevant to weak active pharmaceutical ingredients and is prevalent in pharmaceutical and food industries. The attrition of Paracetamol and Aspirin caused by shear deformation at very low stresses is investigated here. The extent of breakage of these particles is related to the prevailing shear stresses and strains. In contrast to the expected trend, smaller particles exhibited increased breakage rates. At the onset of shearing at low stresses Aspirin particles experienced slightly more breakage than the Paracetamol, however prolonged shearing resulted in greater breakage of Paracetamol. Breakage occurred initially through chipping with some fragmentation, particularly more noticeable for Aspirin, with an increase in abrasion after extensive shear strain for Paracetamol. Empirical breakage relationships are proposed and when combined with process stresses and strain analyses the extent of breakage occurring in process equipment can be estimated.
Auto-granulation is the growth of particle clusters within a dry, fine powder bed due to the bulk powder cohesion. This clustering occurs without the addition of any binder to the system due to simple agitation of a powder, such as during storage or handling. For this reason, it is important in powder processing to be able to characterize this behavior. In this study, a sub-micron titania powder is mechanically vibrated under controlled conditions to induce clustering and promote auto-granulation. The amplitude and frequency of the vibration is varied to view the effect on the equilibrium granule size. A statistical model of the effect is also developed to determine that the granule size increases linearly with vibrational energy. Furthermore, imaging of cross-sections of the granules is conducted to provide insight into to the internal microstructure and measure the packing fraction of the constituent particles. It is found that under all vibrational conditions investigated the particles exhibit a core-rim microstructure.
In the shear deformation of powder beds beyond the quasi-static regime the shear stress is dependent on the strain rate. Extensive work has been reported on the rapid chute flow of large granules but the intermediate regime has not been widely addressed particularly in the case of cohesive powders. However in industrial powder processes the powder flow is often in the intermediate regime. In the present work an attempt is made to investigate the sensitivity of the stresses in an assembly of cohesive spherical particles to the strain rate in ball indentation using the Distinct Element Method. This technique has recently been proposed as a quick and easy way to assess the flowability of cohesive powders. It is shown that the hardness, deviatoric and hydrostatic stresses within a bed, subjected to ball indentation on its free surface, are dependent on the indentation strain rate. These stresses are almost constant up to a dimensionless strain rate of unity, consistent with trends from traditional methods of shear cell testing, though fluctuations begin to increase from a dimensionless strain rate of 0.5. For dimensionless strain rates greater than unity, these stresses increase, with the increase in hardness being the most substantial. These trends correlate well with those established in the literature for the Couette device. However quantitative value of the strain rate boundaries of the regimes differ, due to differences in the geometry of shear deformation band. Nevertheless, this shows the capability of the indentation technique in capturing the dynamics of cohesive powder flow.
Measurement of the adhesive force is of great interest in a large number of applications, such as powder coating and processing of cohesive powders. Established measurement methods such as Atomic Force Microscopy (AFM) and the centrifugal method are costly and time consuming. For engineering applications there is a need to develop a quick test method. The drop test method has been designed and developed for this purpose. In this test method particles that are adhered to a substrate are mounted on and are subjected to a tensile force by impacting the stub against a stopper ring by dropping it from a set height. From the balance of the detachment force and adhesive force for a critical particles size, above which particles are detached and below which they remain on the substrate, the interfacial specific energy is calculated. A model of adhesion is required to estimate the adhesive force between the particles and the surface, and in this work we use the JKR theory. The detachment force is estimated by Newton’s second law of motion, using an estimated particle mass, based on its size and density and calculated particle acceleration. A number of materials such as silanised glass beads, Avicel, α-lactose monohydrate and starch have been tested and the adhesive force and energy between the particle and the substrate surface have been quantified. Consistent values of the interface energy with a narrow error band are obtained, independent of the impact velocity. As the latter is varied, different particle sizes detach; nevertheless similar values of the interface energy are obtained, an indication that the technique is robust, as it is in fact based on microscopic observations of many particles. The trends of the results obtained with the drop test method are similar to those shown in studies by other researchers using established methods like the AFM and the centrifuge method.
Coating of particulate solids by a thin film layer is of interest in many industrial applications such as seed and tablet coating. In seed processing, seeds are commonly coated with a protective coating layer consisting of fertilisers and disease control agents, such as pesticides and fungicides. Batch coaters are commonly used for this purpose. A typical coater consists of a vertical axis cylindrical vessel with a rotating base and a spray disc in the centre, onto which the coating liquid is fed to atomise and spray-coat the seeds. The seeds are driven around the vessel by its rotating base, and are mixed by two baffles; one on either side of the vessel. In the present study, Distinct Element Method (DEM) simulations are used to model the seed coating process. Corn seed are used as a model material and their shape is captured using X-Ray Tomography (XRT), which is approximated in the DEM by clumped spheres. The coating uniformity of the seeds is predicted by implementing a coating model in the DEM, whereby the coating droplets are simulated as very fine spheres projecting tangentially from a ring at the edge of the spinning disk. The size and velocity of droplets leaving the spray disk are measured using high speed video imaging and implemented into DEM simulations. The coating mechanism is represented in the DEM by considering that once a droplet contacts a corn seed, it is removed from the simulation and its mass is attributed to the coating of the corn seed. The distribution of mass of sprayed spheres on the corn seeds and their coefficient of variation are evaluated for a range of process conditions, such as the base rotational speed, atomiser disc position relative to the base and baffle arrangement and designs. It is found that the atomiser disc vertical position, baffle angle and clearance to the wall are most influential, whilst the base rotational speed and baffle width and curvature have only minimal effect.
At moderate stresses, shear cells are the preferred method of powder flow measurement. However, several industrial processes operate at low stresses, where the determination of unconfined yield strength by the shear cell technique may be inconsistent, or found not to correlate with observed behaviour. Alternatively, ball indentation can be used, which directly measures hardness; related to unconfined yield strength by the constraint factor. However, it is not known how constraint factor is influenced by particle properties. Here, ball indentation and shear cell methods are applied for glass beads of various size distributions, and the influence of particle size distribution on the constraint factor is explored. The constraint factor is shown to be independent of the pre-consolidation stress, though reduces as the d10, d50 or d90 are increased. Unconfined yield strength inferred from indentation measurements suggest that extrapolation of shear cell data to low stresses overestimates the unconfined yield strength
Discrete Element Method (DEM) simulations coupled with shear cell experimental results have been used to investigate the flow behaviour of a dry particle assembly of glass beads in the quasi-static regime. 10 Experimental studies have been undertaken using an FT4 powder shear cell apparatus, in parallel with extensive DEM simulations of both homogeneous simple shear and the FT4 shear cell itself. The findings show that it is not possible to accurately predict the bulk friction coefficient with homogeneous simple shear simulations unless both rolling and sliding friction are considered. There are, however, multiple pairs of sliding and rolling friction coefficients which can reproduce the experimental bulk friction coefficient. Sliding 15 test experiments were conducted to yield the coefficient of sliding friction, and hence minimise the set of potentially correct pairs. Simulations of the full FT4 shear cell with two different calibration pairs, along with a pair without rolling friction, were then undertaken to understand the effect of their selection on realistic wall-bounded shearing conditions. Discrepancies were mainly found in the obtained radial contact number and velocity profiles, with increasing friction coefficients - particularly sliding friction - found to in20 hibit packing and particle velocity in the shear deformation zone. Comparison between homogeneous simple shear and shear cell simulation results showed a significant effect of the wall on the obtained force network, with almost a complete absence of the weakest structures which were seen supporting the strong structures in the simple shear scenario.
As the size of individual particles is reduced below several microns, the interparticle cohesive forces begin to play a major role in the bulk powder behavior. Fine powders generally exhibit poor flowability as well as an affinity to agglomerate and form clusters due to this cohesion. This clustering behavior of dry, binderless particles is known as auto-granulation and can often cause difficulties in processing and handling of powders. In this study, a titania powder is vibrated under controlled conditions to induce clustering and promote agglomerate growth. The amplitude and frequency of the mechanical vibration is varied to view the effect of the input energy on the equilibrium agglomerate size. Furthermore, the densities of the formed agglomerates are measured to investigate the role of consolidation as a mechanism of auto-granulation. Given that the size of the agglomerates formed by this auto-granulation process is affected by the balance between the cohesive energy of the particles and the disruptive energy of vibration, this work provides insight into the mechanism controlling the growth of these agglomerates to an equilibrium size.
In the seed processing industry, rotary batch seed coaters are widely used for providing a protective coating layer (consisting of various ingredients including fertilisers and crop protection chemicals) on the seeds. Seed motion and mixing are important in ensuring uniform coating. In the batch seed coater, the base of a cylindrical vessel rotates, whilst the cylindrical wall is stationary and two baffles turn the bed over for mixing. In the present study, the Discrete Element Method (DEM) is used to simulate the effect of particle shape on motion and mixing in this device. Corn seed is used as a model material and the effect of its shape on motion is analysed by considering two approaches: (1) manipulation of rolling friction to account for shape as it is commonly used in the field; (2) approximation of the actual shape by a number of overlapping spheres of various sizes. The geometry of corn seeds is captured using X-Ray micro tomography and then the ASG2013 software (Cogency, South Africa) is used to generate and optimise the arrangement of the overlapping spheres. A comparison is made of the predicted tangential and radial velocity distributions of the particles from DEM and those measured experimentally. It is concluded that for rapid shearing systems with short collisional contacts a small number of clumped spheres suffices to provide a reasonable agreement with experimental results. Equally well, manipulating the rolling friction coefficient can provide results that match experiments but its most suitable value is unknown a priori, hence the approach is empirical rather than predictive.
The paper entitled “Analysis of the Dynamics of the FT4 Powder Rheometer” contains calculation errors that lead to an underestimate of deviatoric stresses by a factor of ten and average compressive stresses by a factor of approximately three. The trends remain unchanged from those shown in the paper, with compressive stress and deviatoric stress both increasing approximately linearly with blade penetration depth. Here, the corrected values of compressive and deviatoric stress are given.
Tablets are the most common solid dosage form of pharmaceutical active ingredients due to their ease of use. Their dissolution behaviour depends on the particle size distribution and physicochemical properties of the formulation, and the compression process, which need to be optimised for producing consistently robust tablets, as weaker tablets are often prone to breakage during production, transport and end use. Tablet strength is typically determined by diametric compression and friability tests. The former gives rise to propagation of a crack on a plane along the compression axis, whilst the latter, carried out in a rotating drum, incurs surface damage and produces chips and debris. These tests produce different measures of strength, neither of which have been correlated with mechanical properties that are accountable for breakage, i.e. hardness, elastic modulus and fracture toughness. We propose a new method based on single tablet impact testing, following the work of Ghadiri and Zhang (2002), who analysed particle damage by propagation of sub-surface lateral cracks and identified the fundamental form accountable for impact surface damage to be a lumped parameter related to hardness and fracture toughness. Microindentation, carried out separately, to determine fracture toughness led to complete failure of the tablets, hence an unreliable measurement of fracture toughness and no correlation with the experimental trend. In addition, by assuming the fracture toughness to be proportional to the square root of Young’s modulus, the indentation measurements do not correlate well with the impact breakage. The discrepancy between the impact and indentation methods is expected to be due to mechanical property variation across the tablet surface, and with strain rate. The impact method is a more suitable test to describe tablet propensity for attrition as it directly represents the failure mode tablets may experience during processing under well-defined conditions. In contrast, the friability test subjects tablets to a similar breakage mechanism but under less well-defined conditions, whilst the compression test represents a different failure mode that is not representative of stresses incurred during processing.
Powders can exhibit different flow behaviour resulting from a combination of physical properties of the material and equipment design. Problems with powder flow are ubiquitous in process industry and become prominent when dealing with fine and cohesive powders. It is therefore of great importance to characterise the flowability of cohesive materials for better process control. Powder flowability is commonly assessed under relatively high preconsolidation loads using shear cell and uniaxial compression methods by which the unconfined yield strength (Y) is evaluated as a function of the applied load. However, these techniques are typically limited to applied stresses greater than 1 kPa and require a relatively large quantity of powder. To overcome these limitations, the recently developed Ball Indentation Method (BIM) is used in this work for assessing powder flow behaviour at low stress levels. The unconfined yield strength (Y) is inferred from the resistance to ball penetration into the surface of a powder bed, based on the method for measurement of hardness (H). This requires the flow resistance, represented by hardness, to be related to the unconfined yield strength by a proportionality factor termed the constraint factor, C, following the analogy with yield stress measurement in continuum solids, i.e. Y=H/C. The constraint factor for silanised glass ballotini, calcium carbonate, α-lactose monohydrate, Avicel and limestone is evaluated and reported here. It is shown that the unconfined yield strength inferred by this method correlates well with those from the uniaxial compression and shear cell measurement. The characterisation of the constraint factor makes it possible to use BIM for powder flowability testing at low stress levels and using a very small powder quantity. This is highly desirable for applications such as capsule filling, tableting and dry powder inhaler devices. [Display omitted] •We evaluate a method to infer powder flowability by ball indentation.•The technique can be applied at very low loads using small sample quantity.•Constraint factor, from unconfined yield strength and hardness measurement is reported.
Spiral jet milling is a size reduction process driven by the fluid energy of high velocity gas jets. Inter-particle and particle-wall interactions are responsible for size reduction. The process is energy intensive, but inefficient. The underlying mechanisms for size reduction in the mill are also not very well understood. The optimum grinding conditions are still currently found by trial and error experimentation. In this work, the Discrete Element Method coupled with Computational Fluid Dynamics is used to investigate the effects of different parameters on the particle collisional behaviour in a spiral jet mill. These include the particle concentration in the grinding chamber, the particle size, and the fluid power input. We report on our work analysing the efficiency of energy transfer and how it can be improved by changing the milling conditions and particle properties.
The Freeman FT4 Powder Rheometer has been reported to describe well the powder flow behaviour in instances where other techniques fail. We use DEM to simulate the FT4 operation for slightly cohesive large glass beads at a range of strain rates. The curved impeller is shown to be beneficial in comparison to a flat blade as the variation of shear stress across the blade is reduced. The shear stress in front of the blade correlates well with flow energy (which the device measures) for a range of tip speeds and is shown to increase approximately linearly with tip speed when operating beyond the quasi-static regime.