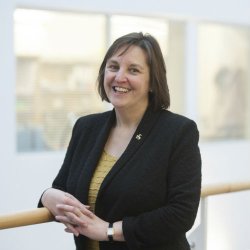
Professor Julie Yeomans
About
Biography
Professor Julie Yeomans was the Associate Dean, Research and Innovation, for the Faculty of Engineering and Physical Sciences. Previously, she undertook a two-year secondment as the first academic Director of Equality, Diversity and Inclusion (EDI), having been Head of the School of Mechanical Engineering Sciences and Director of the Engineering and Physical Sciences Research Council (EPSRC) Centre for Doctoral Training in Micro- and NanoMaterials and Technologies.
She is a materials engineer specialising in ceramics and for the last forty years she has worked on a wide variety of ceramic and ceramic matrix composite systems, always with an interest in the microstructural characterisation of materials before and after fracture as a result of exposure to demanding environments such as those experienced in wear, thermal shock, joining and most recently ballistic and nuclear applications. In 2008, in recognition of her contribution to ceramics, she was awarded the Veralum Medal and Prize from the Institute of Materials, Minerals and Mining. She is also a William Penney Fellow.
Julie was a member of the EPSRC Strategic Advisory Network and the Strategic Facilities Advisory Board of the Henry Royce Institute, which is the result of a £235 million investment in materials research. Previously, she was the academic leader of the Materials and Manufacturing theme within the Advanced Materials Leadership Council, which ran from 2014-2016, to provide strategic advice to the Minister of State for Universities and Science. She has also served as an elected member of the Council of the Institute of Materials and an editor of the Journal of Materials Science.
ResearchResearch interests
- Localised fracture in ceramics and ceramic matrix composites resulting from indentation, impact, wear and/or thermal shock
- Metal - ceramic interactions
Research projects
- Microstructure - property relationships in ceramics for high strain rate applications.
- Thermal shock of ceramic materials.
- Ceramics for civil nuclear applications.
Research interests
- Localised fracture in ceramics and ceramic matrix composites resulting from indentation, impact, wear and/or thermal shock
- Metal - ceramic interactions
Research projects
- Microstructure - property relationships in ceramics for high strain rate applications.
- Thermal shock of ceramic materials.
- Ceramics for civil nuclear applications.
Publications
The master sintering curve approach represents densification data in terms of a master variable that combines sintering time and temperature. Recently, a finite-element scheme to predict sintering deformation that requires only the master sintering curve instead of a full constitutive law as the input data has been developed. Here, a modification to the original master sintering curve approach, so that it is more suitable for finite-element analysis, is presented. Finite-element shape functions are used to represent the densification data as well as the master sintering curve. This approach confers extra flexibility to the master sintering curve approach, even when it is not used with finite-element analysis. For example, by using shape functions, a varying activation energy can be used to obtain a master sintering curve for a set of densification data that cannot be fitted using a constant activation energy.
Authors test an Al#72O#73-based and two Si#73N#74-based ceramics in three common workpieces. The molten metals consist of Fe-Ni alloys and two Ni-based superalloys. Results show Al#72O#73 is resistant to all three metals, but the other two are attacked. The suggested mechanism is diffusion into the metal via the grain boundary phase with subsequent dissolution of Si#73N#74 grains.
The purpose of the study is to accelerate the development of ceramic materials for armour applications, by substantially increasing the information obtained from a high-energy projectile impact event. This has been achieved by modifying an existing test configuration to incorporate a block of ballistic gel, attached to the strike face of a ceramic armour system, to capture fragments generated during the ballistic event such that their final positions are maintained. Three different materials, representative of the major classes of ceramics for armour applications, alumina, silicon carbide and boron carbide, have been tested using this system. Ring-on-ring biaxial disc testing has also been carried out on the same materials. Qualitative analysis of the fracture surfaces using scanning electron microscopy and surface roughness quantification, via stereoimaging, has shown that the fracture surfaces of biaxial fragments and ballistic fragments recovered from the edges of the tile are indistinguishable. Although the alumina and boron carbide fragments generated from areas closer to the point of impact were also similar, the silicon carbide fragments showed an increase in porosity with respect to the fragments from further away and from biaxial testing. This porosity was found to result from the loss of a boron-rich second phase, which was widespread elsewhere in the material, although the relevance of this to ballistic performance needs further investigation. The technique developed in this work will help facilitate such studies.
The laser treatment of ceramics can lead to increased concentrations of hydroxyl ions on the surface, resulting in improved adhesive bond strength in quasi-static tests. Whether the improvement can be translated to armor applications is investigated here. The ballistic testing of composite-backed, surface treated and non-treated ‘control’ alumina and silicon carbide panels was undertaken. The failure locus of the ceramic to adhesive/composite joint and the qualitative degree of damage were assessed. Laser surface treated samples performed better than control samples, with silicon carbide moving from single shot to multi-shot capability, thus giving significant advantages for the deployment of these materials.
The Knoop and Vickers indentation behaviour of spark plasma sintered SiC–5 wt.% B4 C, B4 C and SiC–2.5 wt.% AlN–3 wt.% C armour ceramics have been investigated and observations correlated with ballistic performance. Surface and sub-surface indentation-induced damage has been characterised via cross-sectioning and serial ceramographic polishing techniques. The nature of the damage appears to be less influential than hardness in relation to ballistic performance, but variability in indentation behaviour appears to correlate with variability in ballistic performance. Examination of the indentation size effect curves shows that both Knoop hardness and predicted transition velocities correlate with V50 ballistic performance against an armour-piercing threat, further supporting the importance of hardness and the potential for indentation to be used as a screening method for armour materials.
The advent of engineering-designed polymer matrix composites in the late 1940s has provided an impetus for the emergence of sophisticated ceramic matrix composites. The development of CMCs is a promising means of achieving lightweight, structural materials combining high temperature strength with improved fracture toughness, damage tolerance and thermal shock resistance. Considerable research effort is being expended in the optimisation of ceramic matrix composite systems, with particular emphasis being placed on the establishment of reliable and cost-effective fabrication procedures. Ceramic matrix composites consists of a collection of chapters reviewing and describing the latest advances, challenges and future trends in the microstructure and property relationship of five areas of CMCs. Part one focuses on fibre, whisker and particulate-reinforced ceramic matrix composites, part two explores graded and layered ceramics, while the five chapters in part three cover nanostructured CMCs in some detail. Refractory and speciality ceramic composites are looked at in part four, with chapters on magnesia-spinel composite refractory materials, thermal shock of CMCs and superplastic CMCs. Finally, part four is dedicated to non-oxide ceramic composites. Ceramic matrix composites is a comprehensive evaluation of all aspects of the interdependence of processing, microstructure, properties and performance of each of the five categories of CMC, with chapters from experienced and established researchers. It will be essential for researchers and engineers in the field of ceramics and more widely, in the field of inorganic materials. Looks at the latest advances, challenges and future trendsCompiled by experienced and established researchers in the fieldEssential for researchers and engineers.
Hard chromium plate (HCP) has been the wear resistant coating of choice in the nuclear industry for decades, but new protective coatings are required as a result of the hazardous nature of Cr(VI) compounds used in electroplating. This study compares the wear performance of candidate replacements materials, Cr2O3 and Cr3C2–NiCr. These two coatings are also compared with HCP and a WC-(W,Cr)2C–Ni coating assessed in an earlier publication. The Cr2O3 and Cr3C2–NiCr coatings were supplied having been applied to Inconel 625 substrates using high velocity oxy fuel (HVOF) and thermal detonation gun spray techniques, respectively. A ball-on-flat sliding wear configuration was used with three environments: dry, deionised water, and borated water to partially simulate nuclear reactor water chemistry. Wear rates were measured using both volume and mass standard metrics. The wear surface samples were characterised using scanning electron microscopy (SEM) and X-ray photoelectron spectroscopy (XPS) in order to establish the operative wear mechanisms. All three candidate coating materials exhibited similar wear performance to HCP in the three test environments. There was, however, enough of a difference between performance in deionised and borated water, to merit the use of borated water in future testing. The data gathered using SEM and XPS provided insight into the wear mechanisms. These include both particle pull-out and tribolayer formation. The XPS data revealed that Cr3C2 is preferentially removed from the Cr3C2–NiCr coating during wear testing in a borated water environment. •Three ceramic and cermet coatings wear tested in reactor coolant water.•Cr2O3 is the best hard chromium plate alternative in the wear system investigated.•Deionised water is not a suitable analogue for borated water during wear testing.•Wear mechanisms include tribolayer formation and particle/material pull-out.•XPS can elucidate further information on tribolayer formation and wear mechanisms.
This work provides new insight and evidence that challenges and extends the accepted view of the oxidation of Kovar (ASTM-15). Specimens of 2 mm diameter Kovar wire were oxidised in air at 700 °C or 800 °C for 10 minutes. The resulting oxide layers were analysed by X-ray diffraction, X-ray photoelectron spectroscopy, scanning electron microscopy with energy dispersive X-ray spectroscopy, scanning transmission electron microscopy and Raman spectroscopy. Oxide layers of approximately 2 μm and 4 μm thick were formed at 700 °C and 800 °C, respectively. These were found to contain iron, cobalt and traces of nickel. The combination of analysis techniques revealed that the oxide contains Fe2O3 in addition to (Fe,Co,Ni)3O4, a spinel oxide, in contrast to the combinations of Fe3O4, Fe2O3 and FeO that are typically reported. The oxide layer was found to be complex, consisting of multiple layers with different compositions which is overlooked in the existing literature.
Quasistatic indentation has been used to study the hardness and fracture toughness of advanced ceramic materials and has been used as the starting point for the modelling of many wear situations. A lack of data on the nature of subsurface cracks in ceramics has resulted in limited evidence to indicate that crack systems generated by indentation bear any relationship to complex wear situations. In the current study, the technique of confocal scanning laser microscopy (CSLM) has been used to obtain subsurface information on a fine-grained alumina ceramic. The alumina has been indented and CSLM has been used to obtain a substantial amount of data on both surface and subsurface cracking. The data have been compared with predictions from existing theories and it has been shown that the subsurface lateral cracking can be predicted by measuring the more easily observable radial cracks. Radial cracking and subsurface damage due to indentation have proved to be similar to that produced by single particle ballistic impact; hence it may be possible to predict erosive wear rates by conducting simple indentation studies.
The use of manufacturing methods commonly used for polymer matrix composites (PMCs) in the production of ceramic matrix composites (CMCs), as opposed to more traditional ceramic manufacturing methods, has the potential to reduce the cost of components. This work focuses on three typical PMC manufacturing methods and assesses their suitability for the production of an oxide-oxide porous matrix ceramic composite, starting from a commercially available pre-impregnated Nextel 610®/aluminium oxide material. While all the techniques can be used to produce CMCs, results showed that compared with vacuum bagging and warm pressing, autoclave processing produced the best outcome. It resulted in the most uniform thickness laminates and the lowest macro-porosity, as well as the highest flexural strength.
The techniques of confocal scanning laser microscopy (CSLM) and reflected-light microscopy (RLM) have been combined in a study of the subsurface damage in continuous-fibre reinforced ceramic-matrix composites (CMCs). The damage was induced by subjecting a composite to Vickers hardness indentation tests and single-particle impacts. The subsurface damage was viewed conventionally by RLM at specific depths, following material removal by standard metallographic techniques. Mechanical sectioning, however, is time-consuming and may introduce artefacts in the crack patterns. Consequently CSLM was employed to provide a rapid, non-destructive analysis of the subsurface damage. In the classic description of elastic-plastic indentation of monolithic ceramics, there are two major types of crack: radial cracks, which grow out from the elastic-plastic boundary perpendicular to the surface, and lateral cracks, which are on planes approximately parallel to the surface. In CMCs radial cracks were found to be restricted to the near-surface region. Lateral cracks, however, were located a few micrometres from the free surface. Preliminary analysis of damage about impact sites by mechanical sectioning and CSLM has shown that the crack patterns are similar to those observed in indentation fracture. The topographical-mapping facility of the CSLM has been used to detail the radius of damage about an impact site, which has been found to increase with increasing impact velocity.
Composites consisting of an alumina matrix and 20 vol.% transition metal (Ni or Fe) particles, prepared by hot pressing powder blends, have been studied using spatially resolved transmission electron energy-loss spectroscopy (EELS), and, to a lesser extent, by high-resolution electron microscopy (HREM). Particular attention was paid to the elucidation of the chemical bonding mechanisms at the metal-ceramic interface; EELS spectra from interfacial regions being obtained via a spatial difference technique. From both qualitative and quantitative interpretation of EELS near-edge structures, as well as observed HREM images, the data appear to be consistent with the presence of an Al-terminated alumina at the interface and the formation of direct transition metal - aluminium bonds in Al(O3M) (M = Ni or Fe) tetrahedral units, possibly as a result of the dissolution and interfacial reprecipitation of Al during processing. These results correlate well with similar model studies on diffusion-bonded Nb/Al2O3 interfaces and may, in the light of recent theoretical electronic structure calculations, have implications for the resultant interfacial bond strength in such materials.
Glass-ceramics are widely utilized in the electronics industry to provide electrical insulation and to form leak tight joints with a range of metals. The coefficient of thermal expansion (CTE) of the glass-ceramic can be controlled by the extent of crystallization to reduce detrimental tensile stresses in the joint. In recent years there has been interest in using titanium alloys, in place of stainless steels, due to their lower density and superior specific strength. In this study, the heat treatment of a strontium boroaluminate glass has been tailored to create glass-ceramics with mean CTEs ranging from 5.7 ± 0.1 × 10-6 K-1 to 9.7 ± 0.1 × 10-6 K-1 over the temperature range 303 K to 693 K. The resultant glass-ceramic consists of three crystalline phases and residual glass. A glass-ceramic with a mean CTE of 6.9 ± 0.1 × 10-6 K-1 was subsequently fabricated to form a compression seal with a Ti-6Al-4V housing and a pre-oxidized Kovar pin. Single pin assemblies were shown to be reproducible in terms of microstructure and all passed a standard helium leak test, indicating that a successful seal had been produced.
The nuclear industry has used hard chromium plate for many years but is seeking alternatives, due to the adverse health effects of Cr(VI) employed in electroplating. In this study, testing and analysis regimes for the comparison of the sliding wear performance of candidate materials have been established and the performance of WC-(W,Cr)2C-Ni has been compared with that of hard chromium plate. WC-(W,Cr)2C-Ni was applied to Inconel 625 substrates using a detonation gun thermal spray technique. Sliding wear testing was performed using a ball-on-flat configuration reciprocating tribometer at 20 °C in three environments: dry, deionised water and simulated nuclear reactor water chemistry. Wear rates have been evaluated, using both mass and volume loss, and the worn samples were analysed using scanning electron microscopy (SEM) and X-ray photoelectron spectroscopy (XPS). The WC-(W,Cr)2C-Ni coating had a broadly comparable wear performance to hard chromium plate in all three environments. There were differences between deionised and borated water, such that the latter needs to be used in further evaluation. SEM and XPS analyses enabled the wear mechanisms for WC-(W,Cr)2C-Ni and HCP to be elucidated, including pull-out and tribolayer formation. XPS has shown that the tribolayer on WC-(W,Cr)2C-Ni is stratified and undergoes chemical changes as a result of wear.
This review is concerned with ductile particle ceramic matrix composites, which are a group of materials comprising micro- or nano-scale metallic particles in a ceramic matrix. The most studied materials have an alumina matrix; nickel, iron, molybdenum, copper, and silver are some of the more frequently used metals. In contrast to conventional cermets and composites containing an interconnected metallic phase, the particles are discrete. The larger particles provide a toughening increment by deforming plastically and bridging an advancing crack. For the nanoscale composites significant improvements in strength have been reported. Improvements in strength and toughness, coupled with changes to elastic properties and thermal conductivity, have led to improved thermal shock resistance and a consideration of these materials for wear applications.
As a precursor to a study of erosive near behaviour of ceramic matrix composites fracture by indentation and single particle impact has been studied in two glass-ceramic/silicon carbide fibre composite systems. The damage has been characterised and quantified using a combination of confocal scanning laser microscopy and scanning electron microscopy. Lateral cracks which form approximately parallel to the surface, have been found to be the predominant damage event. In the calcium alumino-silicate (CAS)/Nicalon system, lateral cracks tend, to form in regions of the matrix which have a high local fibre volume fraction, whilst in the barium magnesium alumino silicate (BMAS)/Tyranno system they tend to avoid fibre-rich regions. These results are consistent with an analysis of residual thermal stresses in the two systems. In CAS/Nicalon the coefficient of thermal expansion of the matrix is greater than that of the fibre. This puts the matrix into axial tension at room temperature with the stress increasing with local fibre volume fraction. In BMAS/Tyranno the reverse in the case. Thus in both systems, the observed damage is a consequence of the residual stress as well as the stress due to the contact event.
The microstructural and stress evolution of thick (25 μm) alumina films on dense alumina substrates sintered at temperatures from 1300 °C to 1600 °C has been investigated. In this study the constraint on sintering was monitored in the absence of significant differences in thermal expansion between the film and the substrate. For comparison purposes unconstrained alumina pellets sintered at 1300 °C-1600 °C were also examined. Overall, the constrained alumina densified less than the free alumina, as expected, although at intermediate temperatures densification rates were comparable. Sintering in the direction perpendicular to the substrate was enhanced with respect to that parallel to the substrate as a means of stress relaxation. Using fluorescence spectroscopy the residual stresses of the films parallel to the substrates were measured; residual tensile stresses as high as 450±40 MPa were exhibited by the films. The considerable stress development resulted in cracking and delamination of the film from the substrate, subsequently film constraint was reduced and densification was not impeded. © 2014 The Authors.
The use of chromium (III) acetylacetonate as a source of nanometre sized chromium particles for the production of Al 2O 3–5 vol.% Cr nanocomposites has been investigated. The details of the processing procedure are crucial in determining the mechanical properties of the composite. The highest strength and fracture toughness, 736±29 MPa and 4.0±0.2 MPa m 1/2, respectively, were obtained for the nanocomposite hot pressed at 1450 °C. It is shown that the strengthening in Al 2O 3–5% Cr nanocomposites mainly results from microstructure refinement in that the mean alumina matrix grain size in the optimum composite was 0.68 μm compared with a grain size of 3.6 μm in the monolithic alumina hot pressed under identical conditions. Crack bridging and crack deflection by the nano-sized Cr particles did not occur to any significant extent. The slight improvement in fracture toughness may result from the observed change in fracture mode from intergranular fracture for monolithic alumina to transgranular failure for the nanocomposites.
Pressed WC-Co hardmetal compacts of two different compositions, 6 and 10 wt.% Co, were heat treated under flowing atmospheres of nitrogen, hydrogen and methane at temperatures from 500 to 900 °C prior to sintering under argon. Microstructural examination showed excessive carburisation up to 2.5 mm into the compacts with regions most exposed to heat treatment atmospheres showing greatest carburisation. η-phase was present in the 6 wt.% Co samples heat treated at low temperatures without methane but was not present with heat treatment temperatures of 700 °C or above with methane present. The hardness of both materials was significantly lower in highly carburised regions, highlighting the need for careful control of heat treatment parameters.
Surface treatments of alumina have been investigated with the aim of increasing the strength of the bond created between the alumina and a toughened epoxy adhesive. Four surface conditions have been assessed: as-fired; grit blasted; and krypton fluoride excimer laser treated under two sets of conditions. Compared with the as-fired surface, the grit blasted surface was rougher with poorer wettability, probably due to surface contamination. It was found that the laser treatments removed some of the sintering additives and caused rounding of the alumina grains, slightly increasing the surface roughness. Further, the laser treatment led to an increased surface energy and wettability, which has been linked tentatively to an observed increase in the hydroxyl groups on the surface. The adhesive bond strength was assessed by testing joints in tension and shear. It was found that the laser treated surfaces demonstrated slight improvements in bond strength, with a cohesive failure of the adhesive in tension for surfaces subjected to one of the two laser treatments, compared with failure at the interface for the as-fired, grit blasted and other laser treated samples in tension and for all samples in shear. Thus, it has been demonstrated that modifications to the surface of alumina can result in mechanical and chemical changes which affect roughness, wettability, bond strength and the locus of failure.
Surface treatments of silicon carbide have been investigated with the aim of improving the strength of the bond between the ceramic and an epoxy adhesive. Three surface conditions have been characterised; as-fired, air re-fired and KrF laser processed. A number of characterisation techniques have been used to determine the morphological and chemical changes that have occurred to the surface. Scanning electron microscopy of the re-fired and laser processed samples showed surfaces that appeared glassy, with the laser processed surface showing a different morphology. X-ray photoelectron spectroscopy indicated both treatments had oxidised the surface and the laser processed surface also had a greater concentration of hydroxyl groups. The wettability of both surfaces had improved and the laser processed surface was found to be highly hydrophilic. Mechanical testing of joints prepared with this technique showed them to have the highest strength in tension, with the locus of failure being cohesive. © 2013 The Authors.