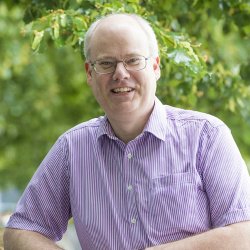
Professor Mark J. Whiting
Academic and research departments
School of Mechanical Engineering Sciences, Institute for Sustainability.About
Biography
The broad area I research is materials ageing and performance. This includes materials for the energy, defence, aerospace, and transport sectors. Many of the materials and systems I research are made by additive manufacture which pose new challenges. I use a variety of materials characterisation tools to explore materials ageing and performance, especially advanced microscopy and diffraction techniques.
University roles and responsibilities
- Director of the MicroStructural Studies Unit (MSSU) - the University's electron microscopy facility
Affiliations and memberships
ResearchResearch interests
- Ageing and Performance of Engineering Materials
- Additive Manufacture of Materials and Systems
- Physical and chemical processes that occur at metal/metal and metal/ceramic interfaces
- The role of interfaces in phase transformations
- Electron microscopy and diffraction as a tool for studying microstructure
Research collaborations
Recent and current industrial partners and sponsors include:
- Dyson
- EPSRC
- Lockheed Martin UK
- NPL
- Rolls-Royce
- ThermoFisher
- TISICS
Research interests
- Ageing and Performance of Engineering Materials
- Additive Manufacture of Materials and Systems
- Physical and chemical processes that occur at metal/metal and metal/ceramic interfaces
- The role of interfaces in phase transformations
- Electron microscopy and diffraction as a tool for studying microstructure
Research collaborations
Recent and current industrial partners and sponsors include:
- Dyson
- EPSRC
- Lockheed Martin UK
- NPL
- Rolls-Royce
- ThermoFisher
- TISICS
Supervision
Completed postgraduate research projects I have supervised
Teaching
Year 1 Materials and Statics; Year 3 Engineering Materials; Year 3 Materials Selection in Mechanical Design; Years 3 and M Individual Research Projects
Sustainable development goals
My research interests are related to the following:
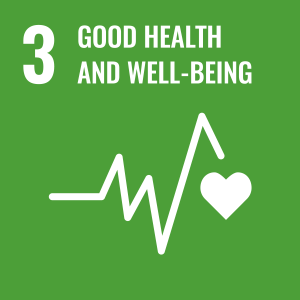
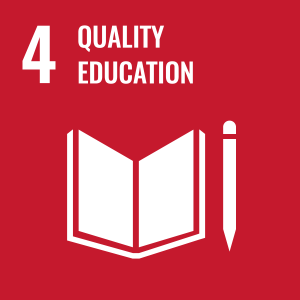
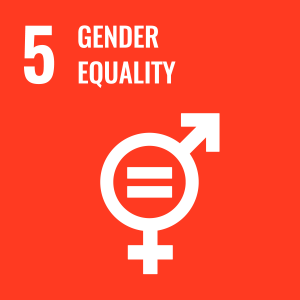
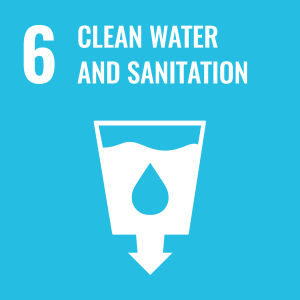
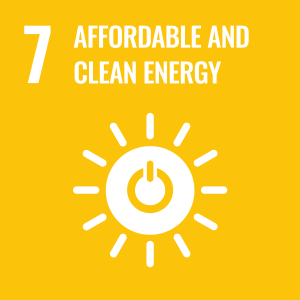
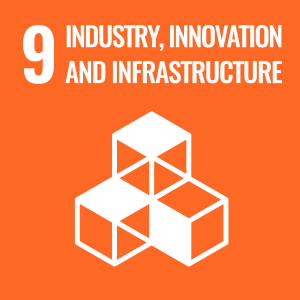
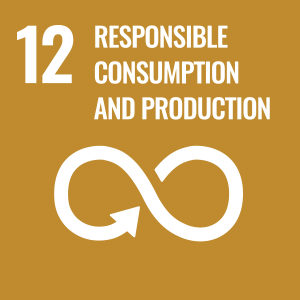
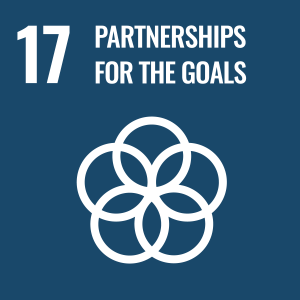
Publications
Residual stress poses significant risks to the life management of key engineering components in nuclear fusion reactors. It is often induced within the narrow heat-affected zone (HAZ) during remote laser welding, essential for maintaining and assembling in-vessel components. Residual stress interacts with high temperatures, degrading mechanical properties and altering fracture mechanisms. Establishing a correlative methodology with microstructures to investigate these stresses and understand their effects on mechanical properties within the narrow HAZ is crucial for extending the reactor's lifetime. In this study, advanced residual stress measurements, including plasma-focused ion beam and digital image correlation, were employed to reveal heterogeneous stress distribution, discovering the peak tensile residual stress of 150 MPa at the interface of the fusion zone (FZ) and HAZ, and peak compressive residual stress of 550 MPa within HAZ. The residual stress effects on micro-hardness are quantitatively evaluated, showing a 25% hardening effect at HAZ/BM interface and a 10% softening effects at fusion line. The deformation mechanism is further analysed using tensile testing, where the residual stress effects were prominent in the low-stress field, reducing 6.5% strain evolution, while microstructures reinforced the material in the high-stress field. At elevated temperatures, the joint exhibited a significant reduction from 532 MPa to 345 MPa for yield strength and from 12 % to 8 % for elongation, with distinct fracture mechanisms observed through fractography compared to its behaviour at room temperature. These findings provide critical insights into enhancing laser welding processing and maintaining the structural integrity of in-service nuclear fusion reactor components.
Fusion In-vessel components, assembled and maintained using laser welding, one of the most promising techniques, exhibit complex distributions of residual stress, microstructures, and material properties. These residual stresses can compromise structural integrity and lifespan of critical components. Although using advanced experimental measurements can evaluate the residual stress for individual case, extending the measurements to massive number of components are costly and time-consuming. Traditional machine learning (ML) models struggle to account for the heterogeneity and anisotropy of these stress distributions. Here, we develop a novel ML framework based on the Eurofer97 steel, the structural material for in-vessel components. The ML framework is trained on high-resolution residual stress data derived from recently-developed evaluation techniques. Combining with microstructures, the model enables prediction of heterogenous and anisotropic residual stress distribution. It successfully predicts the compressive residual stress in fusion zone (∼−200 MPa) balanced by tensile residual stress in heat affected zone (∼300 MPa), aligning closely with experimental results with the R-squared value of 0.989 and the mean square error of 10−4. Unlike experiments that take hours, the ML model provides predictions within seconds. It offers valuable insights into residual stress prediction for various joints, enhancing the reliability and lifetime prediction of in-vessel components.
Hard chromium plate (HCP) has been the wear resistant coating of choice in the nuclear industry for decades, but new protective coatings are required as a result of the hazardous nature of Cr(VI) compounds used in electroplating. This study compares the wear performance of candidate replacements materials, Cr2O3 and Cr3C2–NiCr. These two coatings are also compared with HCP and a WC-(W,Cr)2C–Ni coating assessed in an earlier publication. The Cr2O3 and Cr3C2–NiCr coatings were supplied having been applied to Inconel 625 substrates using high velocity oxy fuel (HVOF) and thermal detonation gun spray techniques, respectively. A ball-on-flat sliding wear configuration was used with three environments: dry, deionised water, and borated water to partially simulate nuclear reactor water chemistry. Wear rates were measured using both volume and mass standard metrics. The wear surface samples were characterised using scanning electron microscopy (SEM) and X-ray photoelectron spectroscopy (XPS) in order to establish the operative wear mechanisms. All three candidate coating materials exhibited similar wear performance to HCP in the three test environments. There was, however, enough of a difference between performance in deionised and borated water, to merit the use of borated water in future testing. The data gathered using SEM and XPS provided insight into the wear mechanisms. These include both particle pull-out and tribolayer formation. The XPS data revealed that Cr3C2 is preferentially removed from the Cr3C2–NiCr coating during wear testing in a borated water environment. •Three ceramic and cermet coatings wear tested in reactor coolant water.•Cr2O3 is the best hard chromium plate alternative in the wear system investigated.•Deionised water is not a suitable analogue for borated water during wear testing.•Wear mechanisms include tribolayer formation and particle/material pull-out.•XPS can elucidate further information on tribolayer formation and wear mechanisms.
This work provides new insight and evidence that challenges and extends the accepted view of the oxidation of Kovar (ASTM-15). Specimens of 2 mm diameter Kovar wire were oxidised in air at 700 °C or 800 °C for 10 minutes. The resulting oxide layers were analysed by X-ray diffraction, X-ray photoelectron spectroscopy, scanning electron microscopy with energy dispersive X-ray spectroscopy, scanning transmission electron microscopy and Raman spectroscopy. Oxide layers of approximately 2 μm and 4 μm thick were formed at 700 °C and 800 °C, respectively. These were found to contain iron, cobalt and traces of nickel. The combination of analysis techniques revealed that the oxide contains Fe2O3 in addition to (Fe,Co,Ni)3O4, a spinel oxide, in contrast to the combinations of Fe3O4, Fe2O3 and FeO that are typically reported. The oxide layer was found to be complex, consisting of multiple layers with different compositions which is overlooked in the existing literature.
Glass-ceramics are widely utilized in the electronics industry to provide electrical insulation and to form leak tight joints with a range of metals. The coefficient of thermal expansion (CTE) of the glass-ceramic can be controlled by the extent of crystallization to reduce detrimental tensile stresses in the joint. In recent years there has been interest in using titanium alloys, in place of stainless steels, due to their lower density and superior specific strength. In this study, the heat treatment of a strontium boroaluminate glass has been tailored to create glass-ceramics with mean CTEs ranging from 5.7 ± 0.1 × 10-6 K-1 to 9.7 ± 0.1 × 10-6 K-1 over the temperature range 303 K to 693 K. The resultant glass-ceramic consists of three crystalline phases and residual glass. A glass-ceramic with a mean CTE of 6.9 ± 0.1 × 10-6 K-1 was subsequently fabricated to form a compression seal with a Ti-6Al-4V housing and a pre-oxidized Kovar pin. Single pin assemblies were shown to be reproducible in terms of microstructure and all passed a standard helium leak test, indicating that a successful seal had been produced.
The nuclear industry has used hard chromium plate for many years but is seeking alternatives, due to the adverse health effects of Cr(VI) employed in electroplating. In this study, testing and analysis regimes for the comparison of the sliding wear performance of candidate materials have been established and the performance of WC-(W,Cr)2C-Ni has been compared with that of hard chromium plate. WC-(W,Cr)2C-Ni was applied to Inconel 625 substrates using a detonation gun thermal spray technique. Sliding wear testing was performed using a ball-on-flat configuration reciprocating tribometer at 20 °C in three environments: dry, deionised water and simulated nuclear reactor water chemistry. Wear rates have been evaluated, using both mass and volume loss, and the worn samples were analysed using scanning electron microscopy (SEM) and X-ray photoelectron spectroscopy (XPS). The WC-(W,Cr)2C-Ni coating had a broadly comparable wear performance to hard chromium plate in all three environments. There were differences between deionised and borated water, such that the latter needs to be used in further evaluation. SEM and XPS analyses enabled the wear mechanisms for WC-(W,Cr)2C-Ni and HCP to be elucidated, including pull-out and tribolayer formation. XPS has shown that the tribolayer on WC-(W,Cr)2C-Ni is stratified and undergoes chemical changes as a result of wear.
Pressed WC-Co hardmetal compacts of two different compositions, 6 and 10 wt.% Co, were heat treated under flowing atmospheres of nitrogen, hydrogen and methane at temperatures from 500 to 900 °C prior to sintering under argon. Microstructural examination showed excessive carburisation up to 2.5 mm into the compacts with regions most exposed to heat treatment atmospheres showing greatest carburisation. η-phase was present in the 6 wt.% Co samples heat treated at low temperatures without methane but was not present with heat treatment temperatures of 700 °C or above with methane present. The hardness of both materials was significantly lower in highly carburised regions, highlighting the need for careful control of heat treatment parameters.
Delamination in the interlayers of multi-layer systems can cause a degradation in functionality, stability and life span of that system. This is even more pertinent for systems at high temperature. Laser flash analysis (LFA) has long been used for thermophysical properties measurements at high temperatures. Multi-layer reference artefacts, with and without, debonded regions are required for validating the thermal characterization of such systems using LFA. To aid in the design of these reference artifacts a numerical model was developed to simulate LFA of multi-layer systems, with and without, defects. This paper discusses a sensitivity study that was conducted to determine if a defect in the interlayer can be detected and if so what are the most sensitive parameters. It was found that the area and thermal conductance of the defect had the greatest effect on the simulated half-rise time of the system, with shape and radial location having a significant but lesser effect in comparison. To be able to observe a change of 10% in the half-rise time, a circular defect equivalent to 5 μm air gap with an area of 25% of the measurement area in the radial centre of the sample would have to be present.
Psalms 1 and 2 are considered unimportant in many interpretative paradigms. It is argued that this is due, in part, to the canonisation of the presupposition that there is no coherent determinable literary structure in the Psalter. This presupposition is challenged by noting the evidence that exists of literary intentionality at the micro-, meso- and macro-structural levels within the Psalter. The content of Psalms 1 and 2 is identified and the use of these themes and motifs within the Psalter is explored. A unifying overarching concern with Zion Theology is tentatively considered. The hermeneutical and theological potential of Psalms 1 and 2 as an intentional introduction are explored. Such an editorial agenda indicates that the collected Psalter is a deliberate rereading of its individual compositions. We conclude with the suggestion that this rereading might usefully be seen as a step in the direction of the more radical rereading demanded by NT faith.
A method of collecting composition data and examining structural features of pearlite lamellae and the parent austenite at the growth interface in a 13wt. % manganese steel has been demonstrated with the use of Scanning Transmission Electron Microscopy (STEM). The combination of composition data and the structural features observed at the growth interface show that available theories of pearlite growth cannot explain all the observations.
Performing EBSD with a horizontal sample and a parallel EBSD detector sensor, enables safer specimen movements for data collection of large specimen areas and improves the longitudinal spatial resolution. The collection of electron backscattering patterns (EBSPs) at normal incidence to the electron beam has been revisited via the use of a direct electron detection (DED) sensor. In this article we present a fully operational DED EBSD detection system in this geometry, referred to as the tilt-free geometry. A well-defined Σ=3[101]{121} twin boundary in a Molybdenum bicrystal was used to measure the physical spatial resolution of the EBSD detector in this tilt-free geometry. In this study, two separate methods for estimating the spatial resolution of EBSD, one based on a pattern quality metric and the other on a normalised cross correlation coefficient were used. The spatial resolution was determined at accelerating voltages of 8 kV, 10 kV, 12 kV, 15 kV and 20 kV ranging from ∼22−38 nm using the pattern quality method and ∼31−46 nm using the normalised cross correlation method.
This paper explores the processing of an alumina matrix composite with a percolating network of graphene oxide (GPO), which exhibits a moderate electric resistivity and a near zero temperature coefficient of resistance. Different formulations of GPO–alumina composites were processed using a water–base blending, and, the pellets were densified by pressureless sintering under Argon flow. Electrical conduction at room temperature was achieved in the 2 wt % GPO–alumina composite sintered at 1400 °C, and, the 3 wt % GPO–alumina composites sintered at 1400, 1550 and 1700 °C. An investigation of the degradation of electrical conductivity was used to identify potential stable operating regimes in which these materials could be used as heaters. Thermogravimetric analysis using the Ozawa–Flynn–Wall method, was used to determine the kinetic parameters of a 3 wt % GPO composite sintered at 1400 °C which, had an activation energy for GPO degradation of 195 ± 68 kJ/mol and, an estimated thermal lifetime of 8.7 ± 0.8 years for a conversion of 0.5 wt % (failure criterion) at an application temperature of 340 °C.
Stir casting and powder metallurgy are the mainstream technologies for manufacturing particle-reinforced aluminum matrix composites. However, particle agglomeration and extensive interfacial reaction in stir casting, as well as residual porosity in powder metallurgy, make it challenging to obtain the due performance. In this study, a semi-solid metal direct writing process based on mixed powder remelting was proposed to manufacture SiCp/Al composites. The mixed powder consisting of AlSi10Mg alloy powder, pure Al powder, and SiCp is heated to a temperature slightly exceeding the melting point of the alloy powder and then sheared to produce a paste-like semi-solid aluminum slurry with suspended SiCp. The microstructures of SiCp/Al composites were experimentally investigated and modeled, demonstrating the uniformity of SiCp and the designability of microstructural characteristics (i.e., the volume fraction and shape factor of the solid phases). The SiCp-matrix interface was also characterized to illustrate the reliable interfacial bonding due to the relatively low processing temperature. Compared with the mentioned processes, this novel approach shows superiorities in particle dispersion and interfacial reaction control.
Laser flash analysis (LFA) has long been used for thermophysical properties measurements at high temperatures for both monolayer and multi-layer materials. Although some high-temperature bulk candidate reference materials were developed and studied, e.g., in the European Metrology Research Programme (EMRP) funded Joint Research Project (JRP) ENG08 Metrofission, they were not able to meet the requirements for validating thermal measurements of multi-layer systems using LFA. In the European Metrology Programme for Innovation and Research (EMPIR) funded JRP 17IND11 Hi-TRACE project, the National Physical Laboratory (NPL) is developing multi-layer reference artifacts, including both fully bonded and partially debonded systems for validating thermal characterization of multi-layer systems at temperatures from room temperature to above 1000 degrees C using LFA. This paper details the methodology of production, measurement and validation of silicon carbide and molybdenum foil-based multi-layer systems with, and without, partial debonding. Reproducibility and thermal stability of the artifacts will be discussed, with recommendation on the usage criteria as LFA multi-layer reference artifacts. The multi-layer system was found to be thermally stable for at least ten thermal cycles between room temperature and 1200 degrees C. The interface thermal conductance of both the bonded and debonded region of the artifacts was calculated using an inverse model and was shown to remain stable with varying temperatures and over five thermal cycles.
Indium tin oxide (ITO) thin films with a specific resistivity of 3.5 × 10− 4 Ω cm and average visible light transmission (VLT) of 90% have been reactively sputtered onto A4 Polyethylene terephthalate (PET), glass and silicon substrates using a remote plasma sputtering system. This system offers independent control of the plasma density and the target power enabling the effect of the plasma on ITO properties to be studied. Characterization of ITO on glass and silicon has shown that increasing the plasma density gives rise to a decrease in the specific resistivity and an increase in the optical band gap of the ITO films. Samples deposited at plasma powers of 1.5 kW, 2.0 kW and 2.5 kW and optimized oxygen flow rates exhibited specific resistivity values of 3.8 × 10− 4 Ω cm, 3.7 × 10− 4 Ω cm and 3.5 × 10− 4 Ω cm and optical gaps of 3.48 eV, 3.51 eV and 3.78 eV respectively. The increase in plasma density also influenced the crystalline texture and the VLT increased from 70 to 95%, indicating that more oxygen is being incorporated into the growing film. It has been shown that the remote plasma sputter technique can be used in an in-line process to produce uniform ITO coatings on PET with specific resistivities of between 3.5 × 10− 4 and 4.5 × 10− 4 Ω cm and optical transmission of greater than 85% over substrate widths of up to 30 cm.
The thermal dissolution and decarburization of WC-based powders that occur in various spray processes are a widely studied phenomenon, and mechanisms that describe its development have been proposed. However, the exact formation mechanism of decarburization products such as metallic W is not yet established. A WC-17Co coating is sprayed intentionally at an exceedingly long spray distance to exaggerate the decarburization effects. Progressive xenon plasma ion milling of the examined surface has revealed microstructural features that would have been smeared away by conventional polishing. Serial sectioning provided insights on the three-dimensional structure of the decarburization products. Metallic W has been found to form a shell around small splats that did not deform significantly upon impact, suggesting that its crystallization occurs during the in-flight stage of the particles. W2C crystals are more prominent on WC faces that are in close proximity with splat boundaries indicating an accelerated decarburization in such sites. Porosity can be clearly categorized in imperfect intersplat contact and oxidation-generated gases via its shape.
Delamination of the interlayers of multi-layer systems can cause a degradation in functionality, stability and life span of that system. This is even more pertinent for systems at high temperature. Laser flash analysis (LFA) has long been used for thermophysical properties measurements at high temperatures. Multi-layer reference artefacts, with and without, debonded regions are required for validating the thermal characterisation of such systems using LFA. Although some high-temperature bulk candidate reference materials were developed and studied, e.g. in the European Metrology Research Programme (EMRP) funded Joint Research Project (JRP) ENG08 Metrofission, they were not able to meet the requirements for validating thermal measurements of multi-layer systems using LFA. In the European Metrology Programme for Innovation and Research (EMPIR) funded JRP 17IND11 Hi-TRACE project, the National Physical Laboratory is developing multi-layer reference artefacts, including both fully bonded and partially de-bonded systems for validating thermal characterisation of multi-layer systems at temperatures from room temperature to above 1000 degrees C using LFA. This paper details the methodology of production, measurement and validation of isotropic graphite and hafnium based multi-layer systems with, and without, partial debonding. Reproducibility, thermal stability and sensitive parameters concerning the thermal response of the artefacts will be discussed, with recommendation on the usage criteria as LFA multi-layer reference artefacts.
[Display omitted] •Alternating magnetic field treatment improved cavitation erosion resistance of alloys via a non-thermal effect regardless of the alloy magnetic nature.•The treatment increased hardness by precipitation of Guinier-Preston zones and Θ’’ in alloy AA2014 and κIV in nickel-aluminium bronze.•Dislocation movement from grain boundaries led to more compressive residual stresses at the surface of EN8 steel, 70/30 brass, nickel-aluminium bronze and AA2014. Results of cavitation erosion tests for EN8 steel, nickel-aluminium bronze (NAB), 70/30 brass and aluminium alloy AA2014-T6 following alternating magnetic field (AMF) treatment are presented. These alloys were selected because of their magnetic nature; EN8 steel is ferromagnetic, NAB and 70/30 brass are diamagnetic and AA2014 alloy is paramagnetic. The indirect cavitation erosion tests (ASTM G32–10 standard) were fulfilled at a frequency of 20 kHz in deionized water which was maintained at room temperature and ambient pressure for a predetermined time. The results show significant decrease in the mass loss for all samples that had underg1 AMF treatment. The eroded samples were characterised by means of scanning electron microscopy, while microhardness measurements showed an increase in the surface hardness as a result of the AFM treatment. The results of X-ray diffraction indicated formation of more compressive residual stresses following treatment, while examination by transmission electron microscopy showed evidence of dislocation movement away from grain boundaries. In the case of the NAB and 20014-T6 alloys, there was evidence of new precipitation. By considering the deformed state and the magnetic nature of each alloy, mechanisms explaining the increase in the cavitation erosion resistance due to the treatment are proposed and discussed.
•Bulk inspection reveals residual strain distribution of laser-welded Eurofer97 joints.•Residual strain tomography was reconstructed using neutron Bragg edge imaging projections.•Tomographic reconstructions were achieved using a small number of projections. Nuclear fusion is a potential source of electricity which can address the environmental problems posed by fossil fuels. Eurofer97 steel is a primary structural material for breeding blanket and divertor components in fusion Tokamaks. Assembling and maintaining the structural integrity of these in-vessel components requires remote joint techniques, such as laser welding, although it induces immersive residual stress. The interaction of the residual strain and the heterogeneous microstructure degrades the mechanical performance of fusion components. However, an inspection of bulk residual strain distribution is still challenging. This study presents the residual strain distribution in the bulk of the weldment using volumetric tomographic reconstruction. A neutron Bragg edge imaging technique is used to obtain 2D angular projections. The 3D volumetric strain map is reconstructed from 2D residual strain projections using the filtered back projection technique. It is found that the laser welding technique generates a uniform residual strain field in the through-thickness direction. The results also demonstrate the potential of reconstructing volumetric residual strain distribution in bulk materials using fewer projections to reduce data redundancy and acquisition time for the neutron Bragg edge imaging technique.
Heat transfer between contacting surfaces is a key factor in the thermal behaviour of engineering components in turbomachinery and various other areas of technology. Thermal contact conductance (TCC) is a parameter that quantifies this heat flow. An ongoing challenge in measuring and modelling TCC is the different length scales of surface topography exhibited on real components. Manufacturing techniques such as turning and fly cutting introduce repeatable surface deviations of medium wavelength which are the focus of this study. An instrumented split tube with in-line washers, loaded under carefully controlled conditions, was used to measure the TCC of washers made of PE16. Fly cutting was used in this study to introduce a repeatable lay typifying a range of manufacturing techniques. Experimental determination of TCC for (i) flat contacting washers and (ii) contact between flat washers and fly cut washers with repeatable lay is reported. As expected the latter case gives rise to significantly lower TCC than the former. A 2D finite element model is described which models the elastic-plastic deformation of a representative machining induced contact line. Using the TCC data for flat contacting surfaces, FEA is used to calculate the reduced TCC for the machined case. Predicted values of TCC assuming plane stress and plane strain are compared with experimental data.
Delamination in the interlayers of multi-layer systems can cause a degradation in functionality, stability and life span of such systems. This is even more pertinent for systems at high temperatures. Laser flash analysis (LFA) has long been used for thermophysical properties measurements at high temperatures. In the European Metrology Programme for Innovation and Research (EMPIR) funded JRP 17IND11 Hi-TRACE project, the National Physical Laboratory (NPL) is developing multi-layer reference artefacts, including both fully bonded and partially de-bonded systems for validating thermal characterisation of multi-layer systems at temperatures from room temperature to above 1000 degrees C using LFA. The sensitivity studies carried out before creating the partially debonded artefacts have shown that the measurement area of the detector is one the important parameters that affect the accuracy of the thermal characterisation using LFA. However, this parameter is unknown to users of the early version of the Netzsch LFA 427, as it has negligible effect on radially homogenous samples which LFA is typically used for. This paper details the effect of measurement area on thermal characterisation of artefacts with partial debonding in the interface using LFA. For a bi-layer IG-210 grade graphite-hafnium foil system with a 6 mm diameter defect at the centre of the foil interface, variation in the measurement area can change the heat pulse transmission half-rise time by up to similar to 40%. Three methods to determine the system measurement area are discussed. The physical measurement diameter for the LFA 427 at NPL was estimated to be 7.7 mm +/- 0.3 mm, independent of temperature. Within the uncertainty range of the measurement diameter, the thermal conductance of the defect region and the average heat transfer coefficient (HTC) can vary by +/- 36% and +/- 3.5% respectively. It is important to remember that this change is for a defect of 6 mm diameter which is a significant portion of the measurement area. For much smaller defects a much smaller change can be expected.
Extrusion-based metal direct writing is a promising metal additive manufacturing technology due to its high efficiency and low cost. However, fabricating parts with high integrity and complex geometry remains challenging. The most critical factor is the unavailable of semi-solid slurries with uniform and nearly spherical solid particles, resulting in uncontrollable extrusion and printing. Currently, mixed powder remelting (MPR) is reported to preset the features of the solid phases, including volume fraction, morphology, and size distribution. Specifically, the semi-solid slurries of hypoeutectic AlSi alloys were obtained by preheating and shearing the mixed powder composed of eutectic AlSi alloy powder and pure aluminum powder. Their microstructural characteristics and rheological behavior were investigated, demonstrating the microstructure tailoring (controllable solid fraction and size distribution, high shape factor of about 0.9) and the reduced viscosity fluctuation by a factor of 7 compared with traditional processes. MPR shows unparalleled advantages for further engineering applications of metal direct writing.
A fusion power plant requires not only the control of high energy plasma but also advanced techniques for maintenance and assembly to generate electricity consistently and safely. Laser welding is a promising technique for cutting and joining pipes and in-vessel components made of Eurofer97, a European baseline structural material. However, the substantial residual strain induced during post-weld cooling degrades the mechanical properties and reduces the lifespan of engineering components. Establishing the underpinning mechanistic connection between residual strain, microstructure, and tensile behaviour is critical to lifetime assessments of engineering components. Here, the heterogeneous strain evolution in laser-welded Eurofer97 joint is quantitatively evaluated using in situ neutron diffraction at the lattice-scale, nanoindentation at the microscale, and digital image correlation (DIC) at a macroscale. The residual strain in the loading direction is characterised via neutron diffraction and validated using a plasma-focused ion beam (PFIB-DIC) ring-core method. Superimposing the microstructural strengthening, the highest residual tensile strain (0.6×10−3με) accelerates the accumulation of tensile deformation around the fusion line (FZ/HAZ interface), whereas residual compressive strain (−1×10−3με) hinders the tensile strain evolution around the heat-affected zone and the base material interfaces, increasing the localised yield strength to 506 MPa. Residual strain is the primary strengthening mechanism during the initial deformation stage, although the microstructural strengthening then dominates as deformation increases. This work reveals the critical role of residual strain, and the results provide insight into managing structural integrity and developing predictive tools for lifetime assessment.
As part of ongoing research in the UK, TISICS have developed an improved 140 µm carbon coated silicon carbide monofilament for the reinforcement of metal matrix composites. The monofilament is fabricated in a single reactor using a high speed chemical vapor deposition process at a rate of 8 m/min (26 ft/min). Statistical analysis of monofilament properties over two years of production has demonstrated excellent reproducibility of the process. The monofilaments have an average tensile strength of 4.0 ± 0.2 GPa with a Weibull modulus of 50 ± 10. Composites incorporating the monofilaments show similar low variability in yield and tensile strength with the latter exhibiting a mean value above 90% of the maximum theoretical strength predicted by the rule of mixtures. By varying the volume fraction and orientation of the monofilament reinforcement, composite properties can be tailored to fit design requirements. Examples are given of demonstrator components made for the European aerospace sector.
Multiscale Topology Optimisation (MTO), by definition, operates over multiple length scales to achieve an optimised structural solution. Consequentially MTO can be computationally very expensive. Machine learning provides the opportunity to accelerate the process utilising surrogate models that approximate the behaviour of the system, allowing for faster evaluation and optimisation. This is particularly advantageous in scenarios where direct simulations at all scales are impractical or prohibitively time-consuming. In this study we demonstrate the effectiveness of a convolutional neural network (CNN) to map topologies of 2D micro-architectures to their corresponding stiffness property matrices. We utilise the topological dataset presented by Jiang et al [1] and generate the stiffness properties using 2D homogenisation [2] for micro-architectures made of a combination of printable polymeric materials (i.e. from a multi-material 3D printer such as an Object 260). We present a successful mapping, achieving results of R 2 greater than 99% and a mean average error of 0.012. Additionally, we examine the transferability of the initial learning of the above trained network. The trained mapping was used on the same topological dataset but with a different material combination. R 2 reduced to 34% and mean average error rose to 0.436. Mappings trained on one material combination will therefore be valid for only a small section of the total design space. To further explore the transferability of CNN, two architectures are proposed and evaluated. One network architecture employs transfer learning and the other incorporates branched connections which account for different printable material combinations. These models are assessed in terms of both the reduction in the computational cost, by leveraging the already trained CNN, and accuracy.
The industrial scale production of silicon carbide monofilaments by chemical vapour deposition (CVD) can be disrupted by growth anomalies that initiate filament fracture during its manufacture. The anomalies take the form of growth warts on the surface of the silicon carbide fibre. Complementary 3D imaging techniques, micro X-ray computed topography (XCT) and plasma focused ion beam scanning electron microscopy (PFIB-SEM), in combination with other materials characterisation techniques (Raman spectroscopy, X-ray photoelectron spectroscopy (XPS), scanning electron microscopy (SEM), electron backscatter diffraction (EBSD) and X-ray diffraction (XRD) analysis) have been used to investigate the nature and cause of the anomalies. Metallic tungsten particulates with an unusual dendritic morphology attached to the tungsten core were found to be the origin of the anomalies. Further investigation of the CVD system led to the observation of process-induced W oxide particulate agglomerates accumulating at the cleaning stage inlet to the reactor. These particulates became attached to tungsten wire in the cleaning stage of the CVD reactor and were rapidly reduced to elemental tungsten prior to entering the silicon carbide deposition chamber. Silicon carbide growth on the tungsten particulates results in the development of a wart-like morphology on the fibre surface. An understanding of this mechanism enabled minor modifications to reactor conditions, which prevented W oxide particulate formation and greatly reduced the occurrence of such growth anomalies. [Display omitted]
The present work has used an alternating magnetic field treatment at ambient temperature to improve the wear resistance of nickel-aluminium bronze and aluminium alloy 2014-T6. Pin-on-disc wear tests under lubricating conditions using a AISI52100 steel ball bearing as the counter face material have shown reduction in the width and depth of wear scars as well as lower values of the coefficient of friction following the treatment. The improved wear properties have been attributed to increased precipitation of κIV in the case of the nickel-aluminium bronze and of GP zones as well as θ’’ for AA2014-T6. Transmission electron microscopy also revealed changes in the dislocation distribution, while X-ray diffraction showed changes in the residual stress for both alloys. The mechanism leading to these changes is discussed by consideration of the soft ferromagnetic properties of the nickel-aluminium bronze and the paramagnetic nature of AA2014. •Improvement of the wear resistance of nickel-aluminium bronze and AA2014-T6 by application of magnetic field was recorded.•Increased dislocation mobility and precipitation were recorded, leading to redistribution of RS and increase in hardness.•Mechanisms responsible for the increased dislocation mobility and precipitation leading to the improvement were suggested.
In the present paper, the tribological properties of untreated and magnetically treated EN8 medium-carbon steel were studied. Tribological tests were performed using a pin-on-disc friction and wear tester. The alternating magnetic field treatment has led to a reduction in the coefficient of friction by 18% and of the wear rate by 41% and to decreases in the surface roughness and the wear scar width by 30% and 12% respectively. Examination by means of transmission electron microscopy attributed these results to increased dislocation mobility and migration to the surface as a result of alternating magnetic field treatment leading to an increase in the Vickers microhardness and to an increase in compressive residual stresses at the surface. •The application of an alternating magnetic field led to improved wear resistance of EN8 steel.•TEM showed increased dislocation mobility resulting in higher compressive residual stresses and in increase in hardness.•Mechanisms leading to the increased dislocation mobility and to the improved WR are proposed and discussed.
The European DEMOnstration power plant (EU DEMO) project is currently leading the research endeavours within the fusion field with the goal of developing a next generation fusion reactor. Given the challenging nature of the application, it is essential to establish methodologies that can provide convenient and reliable characterisation of the chosen materials within DEMO. In this paper, the recently developed Time-of-Flight Neutron Bragg Edge Imaging (TOF-NBEI) was used on Tungsten (W)/ Copper (Cu) dissimilar joints sample mock-ups of the cooling system design used in the critical divertor component with the goal of mapping the residual stresses across the sample. Residual strain mapping was performed on the W phase with considerable tensile residual strains identified close to the W-Cu interface. The large-grain microstructure of the Cu phase was analysed using the energy-resolved neutron radiographs. The results will be used as a basis for future TOF-NBEI experiments of tungsten monoblocks related to DEMO.
Porosity was measured for 21 AA2319 wire and arc additive manufacture (WAAM) panels built using different wire batches, cold metal transfer (CMT) modes, wire feed speed (WFS) and travel speed (TS). Image analysis software was used to measure the porosity across two different planes, totalling an area of 84 mm2 approximately 20 layers in height. Porosity was not strongly dependent on CMT mode, WFS and WFS to TS ratio within the ranges tested but batch-to-batch variability in feedstock wire had a significant influence on area of porosity and size distribution. Wire characterisation showed that porosity did not appear to depend on bulk composition but was influenced by surface finish. Surface finish could affect hydrogen content on the wire surface and arc stability which would affect porosity. Further investigation of the relationships between surface finish and surface hydrogen content, and surface finish and arc stability is required to understand porosity formation in aluminium WAAM components.
Most current analysis of nano-indentation test data assumes the sample to behave as an isotropic, homogeneous body. In practice, engineering materials such as structural steels, titanium alloys and high strength aluminium alloys are multi-phase metals with microstructural length scales that can be the same order of magnitude as the maximum achievable nano-indentation depth. This heterogeneity results in considerable scatter in the indentation load-displacement traces and complicates inverse analysis of this data. To address this problem, an improved and optimised inverse analysis procedure to estimate bulk tensile properties of heterogeneous materials using a new ‘multi-objective’ function has been developed which considers nano-indentation data obtained from several indentation sites. The technique was applied to S355 structural steel bulk samples as well as an autogenously electron beam welded sample where there is a local variation of material properties. Using the new inverse analysis approach on the S355 bulk material resulted in an error within 3% of the experimental yield strength and strain hardening exponent data, which compares to an approximate 9% error in the yield strength and an 8% error in the strain hardening exponent using a more conventional approach to the inverse analysis method. Applying the new method to indentation data from different regions of an S355 steel weld and using this data as an input into an FE model of the cross-weld, tensile data from the FE model resulted matching the experimentally measured properties to within 5%, confirming the efficacy of the new inverse analysis approach.
A method of collecting composition data and examining structural features of pearlite lamellae and the parent austenite at the growth interface in a 13wt. % manganese steel has been demonstrated with the use of Scanning Transmission Electron Microscopy (STEM). The combination of composition data and the structural features observed at the growth interface show that available theories of pearlite growth cannot explain all the observations.
The plasma-facing components of future fusion reactors, where the Eurofer97 is the primary structural material, will be assembled by laser-welding techniques. The heterogeneous residual stress induced by welding can interact with the microstructure, resulting in a degradation of mechanical properties and a reduction in joint lifetime. Here, a Xe+ plasma focused ion beam with digital image correlation (PFIB-DIC) and nanoindentation is used to reveal the mechanistic connection between residual stress, microstructure, and microhardness. This study is the first to use the PFIB-DIC to evaluate the time-resolved multiscale residual stress at a length scale of tens of micrometers for laser-welded Eurofer97. A nonequilibrium microscale residual stress is observed, which contributes to the macroscale residual stress. The microhardness is similar for the fusion zone and heat-affected zone (HAZ), although the HAZ exhibits around ~30% tensile residual stress softening. The results provide insight into maintaining structural integrity for this critical engineering challenge.
•Through-thickness residual stress distribution in three dimensions is evaluated.•High-resolution residual strain is mapped by neutron Bragg edge imaging.•Location-dependent reference lattice spacing is first applied on neutron imaging.•Correlation between microstructure, residual stress and micro-hardness is studied. Eurofer97 steel is a primary structural material for applications in fusion reactors. Laser welding is a promising technique to join Eurofer97 plasma-facing components and overcome remote handling and maintenance challenges. The interaction of the induced residual stress and the heterogeneous microstructure degrades the mechanical performance of such fusion components. The present study investigates the distribution of residual stresses of as-welded and post-heat treated Eurofer97 joints. The mechanistic connections between microstructure, material properties, and residual stress are also studied. The neutron diffraction is used to study the through-thickness residual stress distribution in three directions, and neutron Bragg edge imaging (NBEI) is applied to study the residual strain in high spatial resolution. The microstructures and micro-hardness are characterised by electron backscatter diffraction and nanoindentation, respectively. The M-shaped residual stress distribution through the thickness of the as-welded weldment is observed by neutron diffraction line scans over a region of 1.41 × 10 mm2. These profiles are cross-validated over a larger area (∼56 × 40 mm2) with the higher spatial resolution by NBEI. The micro-hardness value in the fusion zone of the as-welded sample almost doubles from 2.75 ± 0.09 GPa to 5.06 ± 0.29 GPa due to a combination of residual stress and cooling-induced martensite. Conventional post weld heat treatment (PWHT) is shown to release ∼ 90% of the residual stress but not fully restore the microstructure. By comparing its hardness with that of stress-free samples, it is found that the microstructure is the primary contribution to the hardening. This study provides insight into the prediction of structural integrity for critical structural components of fusion reactors.