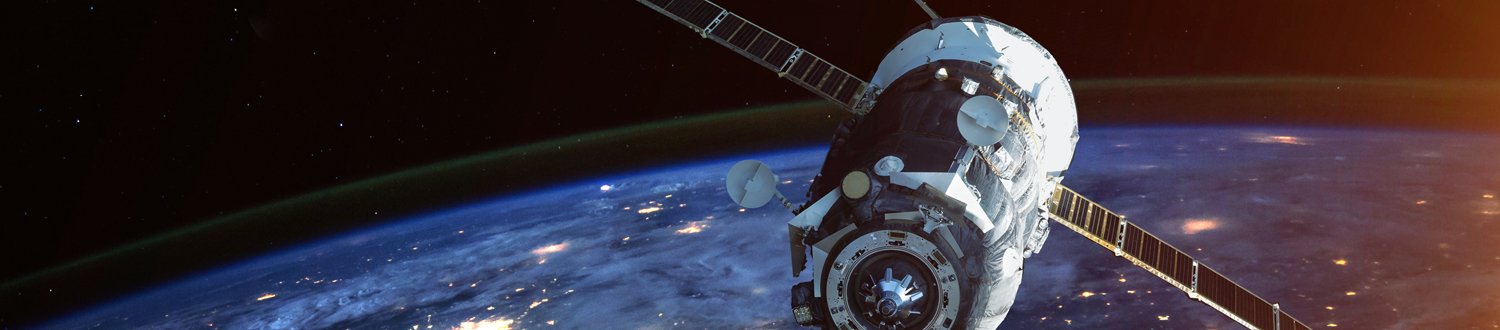
People
Take a look at the staff and PhD students who work in our Space Centre.
Our staff and students
Find out more about our staff and students and get in contact.
Take a look at the staff and PhD students who work in our Space Centre.
Find out more about our staff and students and get in contact.