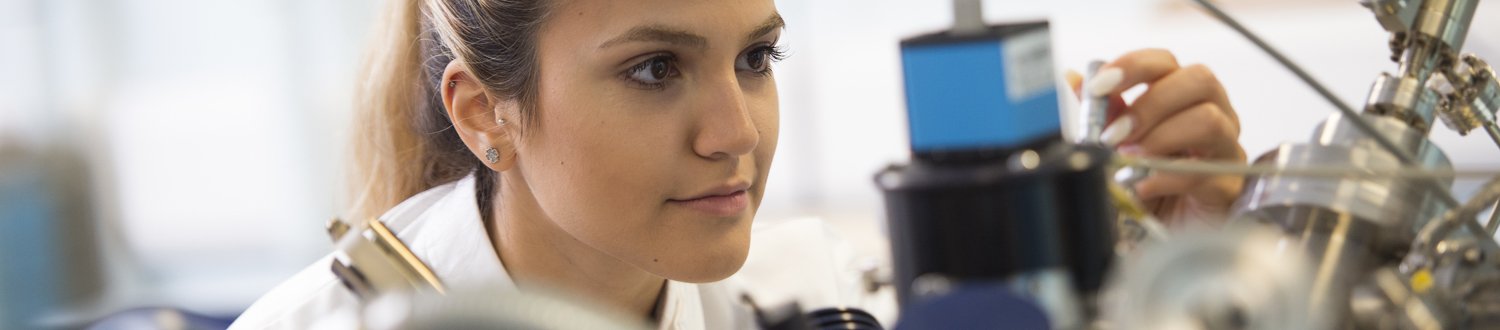
Become a student
Engineering doctorate (EngD) students, or research engineers as they are known, are part of the Centre for Doctoral Training (CDT) in MiNMaT and will spend four years principally with their industrial sponsor, with visits to the University for courses and to use the characterisation facilities.
Key benefits
Some of the key benefits of undertaking an EngD are:
- Experience of tackling a relevant research problem (or problems) within an industrial organisation
- High quality training in technical skills and non-scientific areas such as project management and communication skills, delivered by our Centre
- The support of a supervisory/support team, comprising one or more sponsor-based supervisors, two academic supervisors and a support network, headed by the Centre Director and Centre Manager
- Access to expertise from academics at the forefront of their field, and to state-of-the-art characterisation facilities
- The opportunity to start building your professional network via events such as the Centre’s annual conference.
What our students say
Listen to Jacob describe the differences between a PhD and an EngD, introduce the programme structure, and talk about his project.
Get in contact
If you have any queries or would like to register your interest then please contact the Centre Manager, Noelle Hartley:
- Email: n.hartley@surrey.ac.uk
- Phone: +44 (0)1483 683467
Available projects
If you would like to receive information about projects as they become available, please email our Centre Manager, Noelle Hartley, attaching a copy of your current CV and a covering letter telling us why you are interested in studying for an EngD at Surrey.