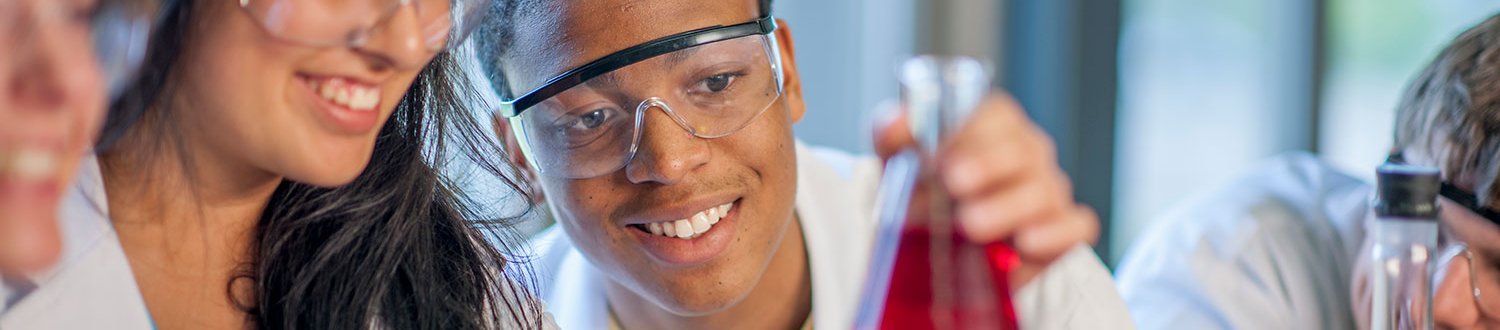
Chemistry and chemical engineering research
Our research is strongly interdisciplinary and ranges from fundamental science to commercialisation of technological innovations. We have successful research collaborations across the School, the University and with other academic institutions and industry in the UK and worldwide.
Research excellence
In the latest UK Research Excellence Framework (REF 2021), we ranked 15th in the UK for ‘*research power’ in engineering.
Overall, Surrey has risen 12 places in the rankings since 2014 to 33rd in the UK for our research quality.
* Research power is the overall quality of submissions, calculated by grade point average and multiplied by the full-time equivalent number of staff submitted.