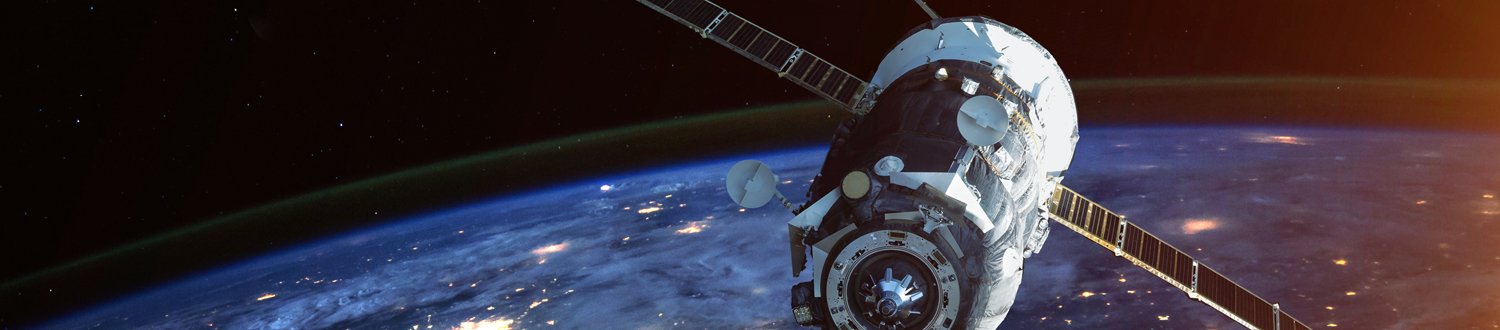
Propulsion Group
The principal aim of our small satellite propulsion research is to produce low-cost, moderate-to-high performance propulsion systems capable of moving microsatellites from low to high earth orbit and beyond, and to maintain microsatellites in their orbits for innovative, demanding mission schemes, such as those required for formation flying.
Overview
The conventional small satellite tends to remain where it's placed, due to a combination of issues:
- Small satellites are often hitchhikers on larger space missions, and combustible propellants potentially represent a possible risk to the primary spacecraft.
- Small satellites are extremely limited in terms of both available mass and volume, and propulsion systems must live within these constraints.
These factors have given rise to promising lines of research into environmentally friendly, "green" propellants, volume-efficient engine designs utilising high density propellants and new transfer strategies suitable for increasing a small satellite's orbital range. These novel systems provide small satellites with many of the advantages that previously were the preserve of large, expensive satellites.
Missions
Surrey continues to expand on its research into novel propulsive systems following the successful launch of its first minisatellite, UoSAT-12. This spacecraft carried both a nitrous oxide (NO2) resistojet and cold gas (N2) propulsion system. The resistojet was a design developed within the Centre, and which is especially suited for our low-cost satellite strategy. Both these propulsion systems are continuing to function extremely well, nearly three years after launch.
In June 2000, we launched a novel butane propulsion system on the SNAP-1 nanosatellite, the world's first nanosatellite to have 3-axis control and a propulsive capability. The butane system was designed to allow for experimentation with satellite formation flying, exploiting a launch opportunity with a sister Surrey satellite Tsinghua-1.
Experimentation on various types of propulsion systems, and plans for their adaptation for small satellite platforms, continues with a variety of options being considered. These projects intend to increase the performance of systems already flown and add an extra dimension of functionality currently absent in many of today's small satellites.
Meet the team
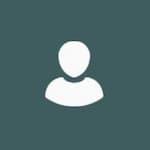
Dr Andrea Lucca Fabris
Head of the Group
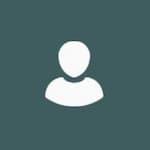
Dr Burak Karadag
Research Fellow
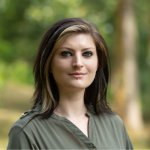
Dr Rachel Moloney
Research Fellow
Postgraduate research students
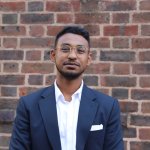
Moe Ahmed
Electrode and electrode-less technologies for plasma propulsion
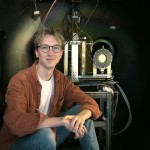
Dr Oliver Hitchens
Ceramic 3D printed Electron Cyclotron Resonance (ECR) thruster
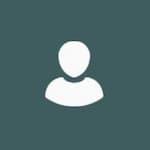
Silvia Masillo
Postgraduate Research Student
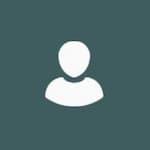
Phillip Thomas
Postgraduate Research Student
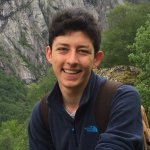
Mansur Tisaev
Air-breathing electric propulsion