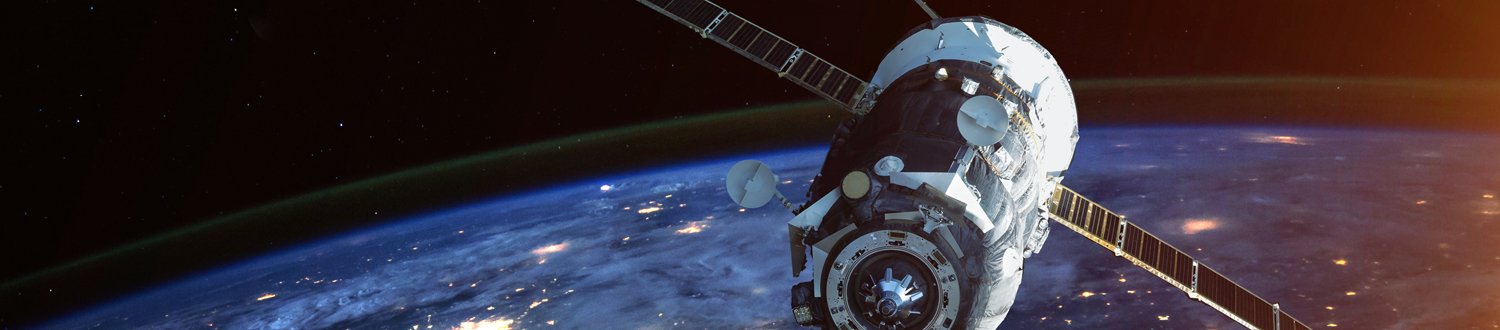
SME-SAT
Fueled by mass market demand, terrestrial consumer electronics continue to drive technology advancement in the field of microelectronics devices. Many of these technologies are spearheaded by the contributions of small and medium enterprises (SME).
Overview
There is a clear opportunity to revolutionise space technologies by leveraging advancement in the commercial electronics market. However, despite the benefits to the space industry, it remains difficult for SMEs to get involved due to the significant cost, effort, time, and paper work to qualify parts for space applications.
The primary purpose of this spacecraft is as a technology demonstrator. Each SME in the consortium will be responsible for contributing a particular spacecraft subsystem. These systems/subsystems will be integrated into a nanosatellite forming SME-SAT and allow Small to Medium Enterprises to space qualify and characterise their technologies in the environment of space.
The SME-SAT will be implemented using a 3U commercially available off the shelf (COTS) structure. This standard consists of a structure that has an external envelope of 100mm x 100mm x 340.5mm, internal envelope of 98.4mm x 98.4mm x 295.2mm (L x W x H). On the outside of this structure will be mounted a number of solar arrays that will provide power to the bespoke power system. Inside the structure are a number of PC-104 standard boards that provide the functionality discussed in the following subsections.
The sensor payloads are all connected to a common PC-104 board that interfaces to the rest of the satellite bus. Many of the sensor payloads are internal to the satellite, however the accelerometers and gyros are placed on a deployable boom that will move them approximately 300mm away from the spacecraft.
Funding
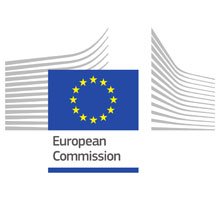
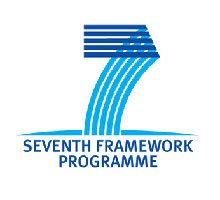
Objectives
The primary objective of this project is to involve SMEs from the terrestrial sector on a space project and allow them to space qualify their technology. SME-SAT brings together one of the largest SME based consortiums ever to develop advanced space technologies based on terrestrial applications, which enables them to fully space qualify their technologies within three years of the project start date.
This project represents a unique, unprecedented space mission, fostering a new alliance between SME’s, universities and a large scale space prime/integrator in which high risk technologies will be developed and fully tested in space using cubesats.
The particular payloads that will be demonstrated in this project include:
- High precision ADCS (Surrey)
- Nano-Control Moment Gyros for agility (Surrey)
- Gyros (Sensonor)
- Accelerometers (Sensonor/Theon)
- Star sensor (ISIS)
- Failure Detection, Isolation and Recovery (HSS)
- Power system (SystematIC design, NL)
- Structures (MPB)
- Magnetometer (LEMI)
- GPS (SSBV).
SME-SAT CubeSat
SME-SAT is a 3U CubeSat that incorporates 60 per cent of sensors and systems developed by the SME partners. These systems act on top of a heritage backbone to de-risk the satellite bus. The core elements of the satellite are constructed from higher technology readiness level (TRL) components in the form of:
- Dipole deployable antenna system and electronics for VHF/UHF communications
- ADCS "bundle" that comprises the CubeSense system, CubeComputer, a reaction wheel, Magnetometer, 3-axis gyros and 3 axis Magnetorquer control.
These systems are adequate in order to control and actuate the satellite from deployment. Once the satellite has de-tumbled and is in a known control mode the experimental systems can be activated for evaluation.
For this operation to be completed, a series of complex operations was required and was a major milestone. The sequence broadly checks the key platform subsystems, power switches, and payloads together with telecommanding, telemetry request handling, and 50 kB experiment data collection (50 kB). At this point, the team was satisfied with the software interfaces and the project entered project extension whilst awaiting launch with flight software and ground operations plans to be developed and completed.
The main results of this work are the soft-stack integration, functional testing, and limited qualification of the SME-SAT platform and payload subsystems. Due to an uncertain launch window, and outstanding deliverables from integration and development delays, the project was closed.
Despite this, the project has achieved many key milestones for the platform and payload providers including the advancements of new payloads that have CubeSat compliant mechanical, electrical, and software interfaces – and an initial qualification and characterisation of their technologies towards the environment of space.
As the satellite has a small amount of remedial work left to complete – it is the Surrey plan to submit to the EC or H2020 for future funding to complete final environmental tests, launch, and operate this largely complete satellite.